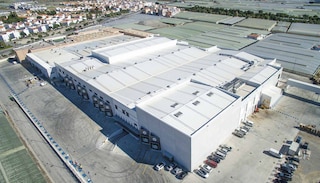
Multistory warehouses: the solution to scarce floor space?
The demand for shipments within 24 hours and even same-day deliveries from e-commerce customers has turned urban installations and consolidation centers into a strategic option for meeting strict delivery times. Consequently, the availability of storage space near large cities has become very limited. To mitigate this situation, a new model of facility construction is emerging: multistory warehouses.
In our article, we’ll analyze the pros and cons of these types of logistics complexes as a means of leveraging storage space in urban areas. We’ll also examine other strategies that, likewise, aim to maximize storage space vertically.
What’s a multistory warehouse? How does it work?
Logistics centers are defined as areas in which various activities related to goods transportation and distribution are carried out nationally and internationally. Users normally have access to common services, such as general installations, freight contracting services and ancillary companies (repair shops, restaurants, administrative agencies, consultants, etc.), among others.
Multistory warehouses are an evolution of the above concept, as, in this case, they are storage installations built on various floors. Each level works as an independent facility, with its own loading docks, accessed by trucks or delivery vehicles via ramps set up for this purpose. Therefore, each level can be operated by a different customer without interference between them.
These new types of logistics installations are usually designed on demand. They are located near major urban hubs where there’s a shortage of available logistics facilities that can meet very tight deadlines. Some examples of these kinds of multistory warehouses are the Amazon facility in Seattle, the Ikea center in Paris, and the complex being built in Barcelona for logistics provider DSV.
The reason for multistory warehouses: urban goods distribution today
The logistics real estate market is one of the most dynamic sectors when it comes to purchase/sales transactions and warehouse rentals. Net US warehouse rents have increased 1.7 percent, to $7.21 per square foot, the highest level since real estate firm CBRE began tracking rents in 1989.
The rapid growth of e-commerce has fueled development of warehouses and distribution centers in the 12 primary US inland-port markets at nearly twice the national rate, according to CBRE. These markets are Southern California’s Inland Empire; Phoenix; Dallas/Ft. Worth; Kansas City; Houston; St. Louis; Chicago; Memphis, Tenn.; Columbus, Ohio; Atlanta; Greenville, SC; and East and Central Pennsylvania. What’s more, logistics facilities that supply online stores require more space than those that serve brick-and-mortar stores. This is due to the intense returns management operations they carry out and the direct access to the goods that they require to meet delivery times.
This trend is well established in the US. The availability of these types of smaller warehouses in urban areas (up to about 400,000 ft2) has dropped by 4% in the last five years, according to CBRE. Consequently, prices rose by 30% between 2014 and 2019. In addition to this, the development of new storage facilities is very limited (having grown by only 1% since 1990) because of the higher profitability achieved from other uses, such as commercial and residential.
In light of this, it’s no wonder several leading companies are choosing to build multistory warehouses as a viable alternative in the face of a lack of traditional installations.
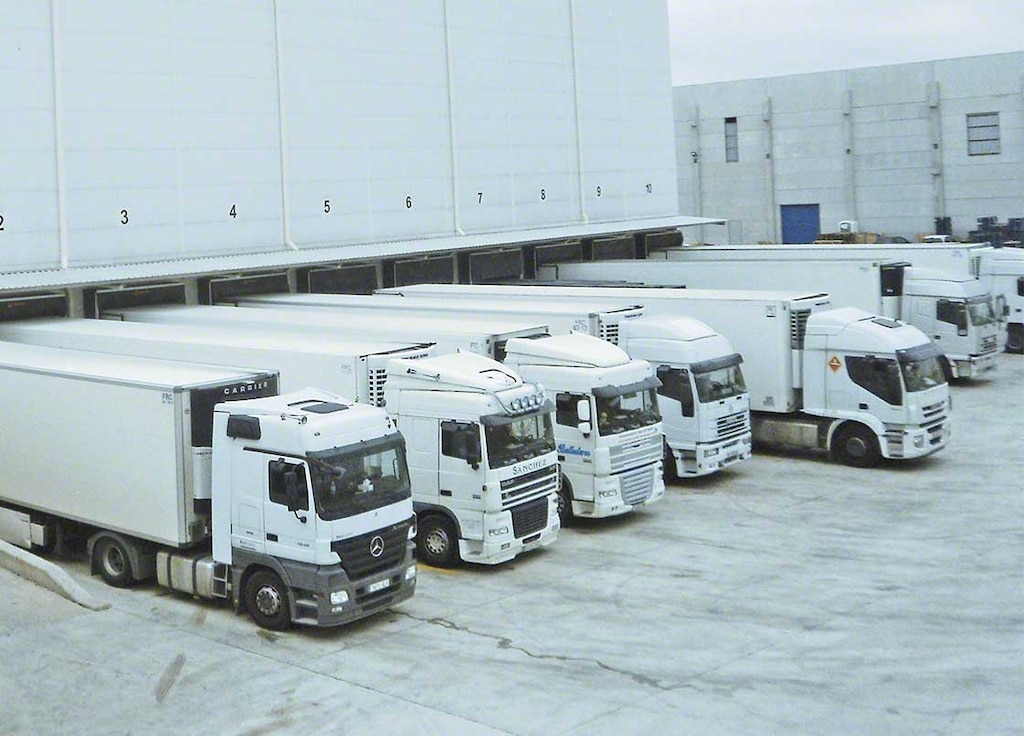
Advantages of multistory warehouses
Multistory facilities offer some real benefits in this sense:
- Multistory warehouses improve the use of the storage space in densely populated areas. This involves having strategic positions for dealing with last-mile transportation efficiently and for containing the costs linked to it.
- The fact that there are loading and unloading docks available on every floor ensures more streamlined stock inflows and outflows in each installation.
- Various companies can occupy the same location, since each level of this type of warehouse works independently. In the case of 3PL logistics, the advantage is that each installation can specialize in a certain type of product or customer, maintaining the same agility in operations.
- Multistory facilities are an innovative and emerging solution in the US. As such, the projects are designed and implemented using the latest construction technologies. This ensures enhanced performance in terms of energy efficiency and increased durability in the operation of the facility.
Drawbacks of multilevel warehouses
Nevertheless, multistory facilities also face certain difficulties that pose challenges to their mass implementation:
- In the US, there’s a lack of supply of multilevel logistics centers already built. Most projects are turnkey installations designed by the customers themselves.
- Red tape may prove to be an obstacle to completing projects quickly. It’s necessary to create specific, standardized regulations for building multistory warehouses (for example, in relation to fire protection systems and the safety of the foundations). Moreover, from an urban planning point of view, the local authorities need to assess whether the area on which the structures will stand is capable of absorbing a higher volume of traffic.
- Multistory warehouses are generally more expensive to build than traditional facilities. The structure needs to be reinforced to safely support the loads of several installations, while the ramps have to withstand the intense road traffic of heavy vehicles. Access to light delivery vehicles is ensured on the top levels, but the frequent traffic of double semi-trailers could pose a challenge.
Height — essential for warehouse design
Currently, building vertically is one of the most common strategies for gaining in storage capacity when faced with limitations to expanding an installation’s surface area. The ideal solution will always depend on the characteristics of the stock stored, the number of SKUs, and the goods flows that take place in the center. In any case, the two most popular options are:
Mezzanines in traditional warehouses
The concept of mezzanine floors is based on the same principle as multistory warehouses, but it’s implemented in a single facility. The main difference is that, in the case of mezzanine floors, one installation is divided into various levels. Therefore, the loading and unloading docks are the same, and the height affects the time dedicated to picking (it takes longer to move the products from the upper levels to the consolidation or dispatch area, for example).
Mezzanine floors are mainly set up in facilities with extensive inventories and a large variety of SKUs requiring direct access.
Rack supported buildings
The racks themselves form the structure of rack supported installations. Generally, these are high-density storage systems paired with automatic stacker cranes and even the Pallet Shuttle. This combination makes it possible to design facilities measuring over 130 feet tall with the assurance that load movements will continue to be agile and safe.
The automation of warehouse processes also provides the added advantage of height, since stacker cranes can operate with taller racks as compared to manual handling equipment.
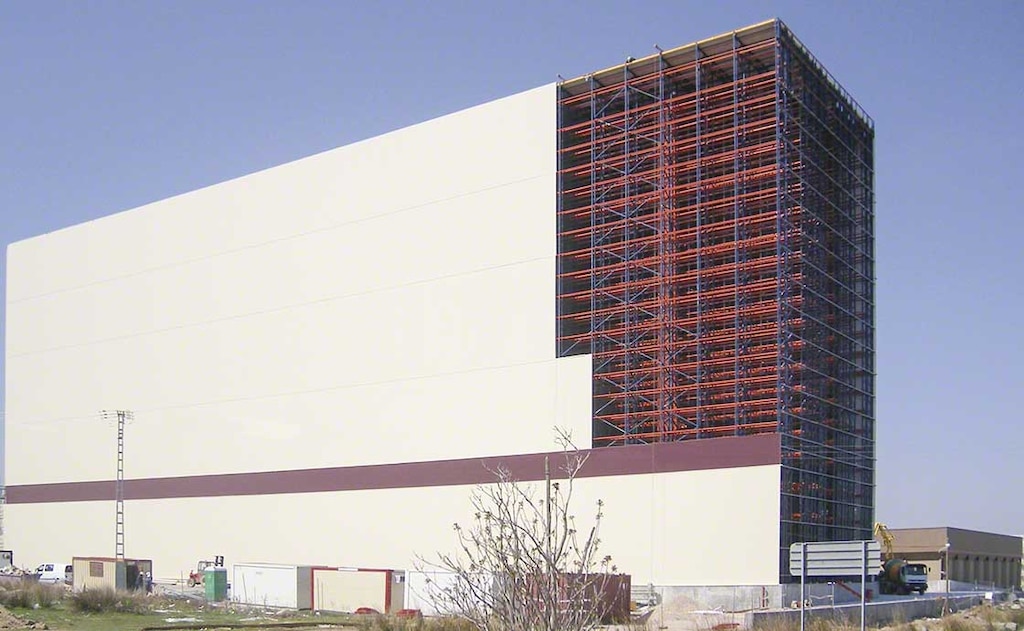
Are multistory warehouses the future of urban logistics?
The saturation of industrial urban space has made multistory warehouses another option for setting up installations and consolidation centers dedicated to e-commerce. However, this alternative is not yet widespread at present,
mainly because planning a multistory warehouse is complex and depends on multiple factors. Not only must it take into account aspects related to the company’s internal logistics systems, but it also has a significant impact on an urban level.
In any event, if space is scarce at your installation, we can analyze it and suggest vertical storage solutions for your particular situation. Contact us and one of our specialists will provide you with detailed advice.