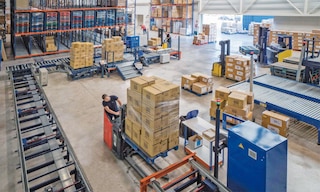
Warehouse machines: which do I need for each operation?
Warehouse machines are essential elements in any logistics facility. They’re charged with moving goods internally, from the loading docks to the storage area, from production to the pick stations, and so on.
Warehouse machines are generally divided into two major categories: manual (pallet jacks, forklifts, order pickers, etc.) and automatic (conveyors, electrified monorails, stacker cranes, etc.).
The different types of machines can also be grouped according to the process or operation they perform:
Warehouse machines for loading and unloading at the docks
To carry out the goods receipt and dispatch processes at the warehouse docking areas, the following warehouse machines are normally employed:
- Pallet jacks and stackers. The pallet jack is the most widely used and versatile type of handling equipment. Available in manual and electric versions, pallet jacks are reserved for transportation operations, as they only work at floor level. Pallet stackers, on the other hand, can raise palletized goods several feet (up to about 19.7'), thus facilitating truck loading and unloading.
- Counterbalanced forklift. Counterbalanced forklifts are excellent for loading and unloading trucks, thanks to their forks that protrude from the front of the machine. The main difference from pallet jacks and stackers is that these machines are faster, they can work inside and outside the warehouse, and their operation is based on the lever principle, incorporating a large counterweight in the rear part.
- ATLS (automatic truck loading systems). Automatic truck loading and unloading systems enable the automatic insertion and removal of pallets into/from a truck with minimal operator intervention.
The loading docks are the access point of any logistics facility, so choosing the right equipment for this area is crucial.
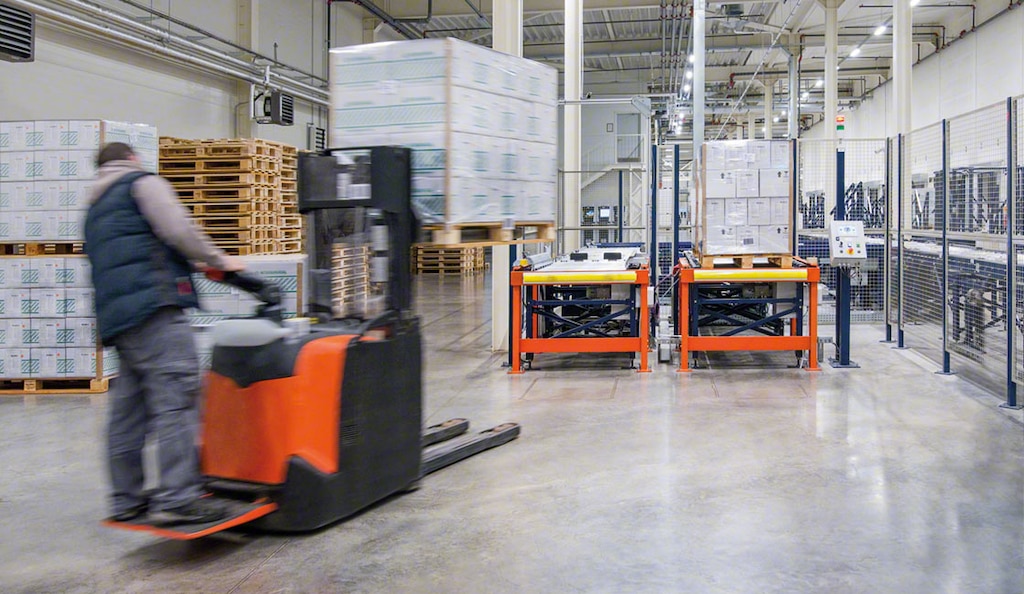
Warehouse machines for depositing and extracting unit loads
Let’s take a look at the most popular warehouse machinery for placing and removing products from racks:
- Forklifts. In addition to counterbalanced forklifts, other types of forklifts can be used to deposit and retrieve goods from the racks. Reach trucks — the most universal warehouse machines — can lift loads more than 30' high. Side-loading reach trucks have a system whereby their wheels can turn 90°. This allows for sideways and forward movements, making them perfect for handling profiles and tubes and working with cantilever racks. Lastly, narrow aisle forklifts (trilateral and bilateral turret trucks) operate in aisles with widths of 59" to 70.9" and can raise loads to heights of over 45.9'.
- Stacker cranes and trilateral stacker cranes. Guided by a warehouse control system (WCS), this fully automated handling equipment transports and stores goods in their corresponding locations in the racking. There are several different types of stacker cranes, depending on the masts or forks. Stacker cranes (AS/RS for pallets) can raise loads to heights of over 131'. AS/RS trilateral stacker cranes are capable of picking and depositing pallets on racks from three positions — from the front and either side — due to their rotating head. Moreover, they don’t require an upper guide rail (meaning there’s no fastening device at the top of the stacker crane).
- Pallet Shuttle. This automatic shuttle moves inside the storage channels to store and remove pallets in compact racking units. Capable of operating in channels up to 131' deep, the Pallet Shuttle system has two versions: semi-automated and automated. While the semi-automated variety requires an operator to place the automatic shuttle in the corresponding channels, with the automated Pallet Shuttle, this action is performed by a stacker crane.
- Miniload system. Miniload systems (AS/RS for boxes) are machines that automate the insertion and extraction of boxes in and from the warehouse racking, improving speed and safety in storage tasks. In addition to maximizing space utilization, this system follows the goods-to-person order picking method, whereby products are automatically brought to the operators.
There’s no one ideal forklift or stacker crane for all operations. Generally, for low movement flows, one or more manual machines will suffice. If, instead, you need a higher level of safe, uninterrupted goods activity, it’s best to invest in automatic warehouse machinery.
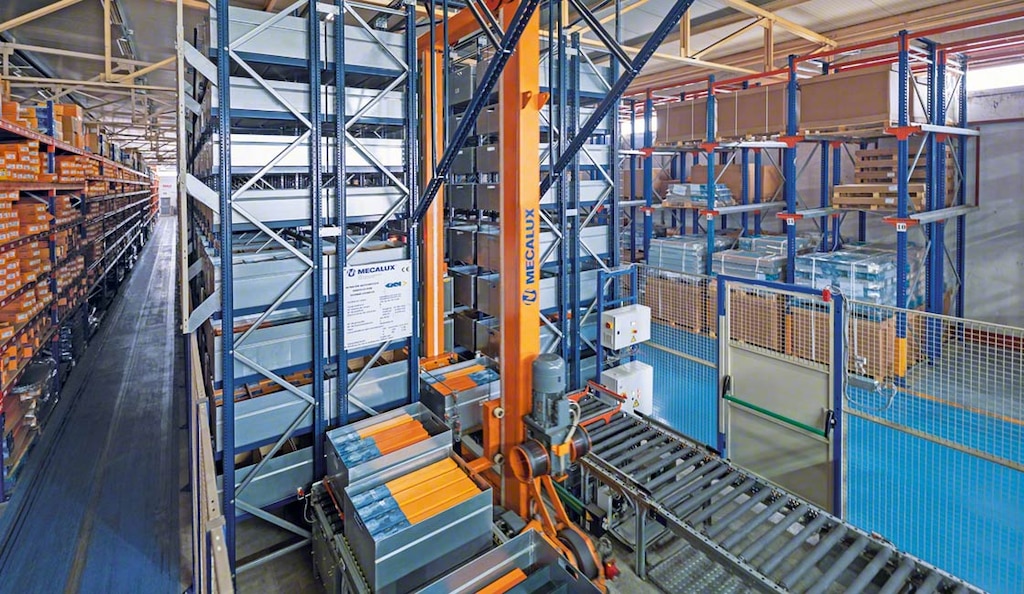
Warehouse machines for transporting goods
The following warehouse machines are charged with the conveyance of loads from one point to another:
- Forklifts. Any type of forklift can temporarily serve to carry goods between two points. The most common tends to be the counterbalanced forklift, since its movements are faster.
- Conveyors. These consist of a set of rollers that carry the load (boxes or pallets) and propel it along a circuit. The system is equipped with electric motors that move the unit loads in a safe, controlled way. Roller conveyors work by means of the WCS, which executes machine movements as per instructions sent by the warehouse management system (WMS).
- Overhead chain conveyors. These are primarily used to transport hanging items. They comprise an aerial circuit with continuously moving chains. Suspended from the chains are various supports that hold a number of different items (boxes, hanging garments, components, etc.).
- Electrified monorails. This discontinuous transportation system consists of automatic trolleys driven by an electric motor. Electrified monorails move along a rail that can be either hung from the ceiling (in the case of overhead electric monorails) or fixed to the warehouse flooring (inverted models).
- Pallet lifts. Also known as vertical conveyors, these warehouse machines are integrated in a conveyor line to raise or lower a pallet several feet (e.g., to another floor). Pallet lifts make it possible to access multiple levels, from a minimum distance of 16.5' to a maximum of 131'.
- Bridge crane. Transportation and lifting system formed by one or two girders fitted with a travel motor. These warehouse machines are suitable for transporting large loads and profiles.
- AGVs/LGVs/AMRs. Automatic guided vehicles (AGVs) are warehouse machines that move autonomously by following a preprogrammed route. They're guided by one of two systems: wire-guided (AGVs) or laser-guided (LGVs). As opposed to AGVs, AMRs (autonomous mobile robots) work and travel without preset routes, adapting their travel according to information they receive from their environment in real time.
The purpose of these machines is to speed up the flow of materials in the warehouse, ensuring at all times the utmost safety in transporting and handling the goods.
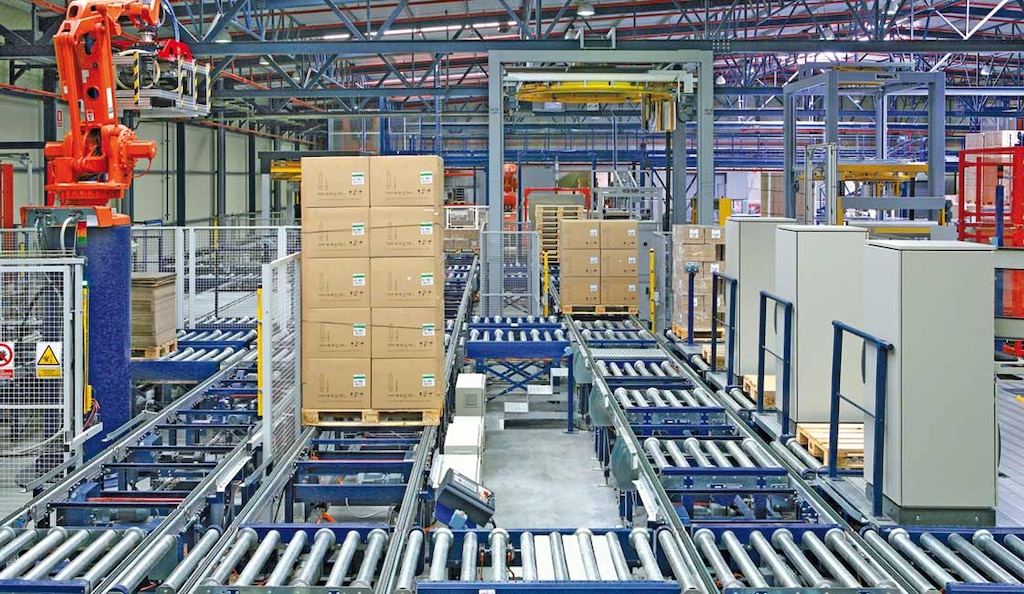
Warehouse machines for picking
Order picking costs account for a high percentage of a logistics facility's total operating costs. Reducing them can be vital to your company’s success, and your choice of warehouse machine has a lot to do with this:
- Order pickers. Order pickers are an evolution of pallet jacks and electric stackers. They’re specially adapted to facilitate picking from manual racks, as operators can access the machine controls on one side and the pallet or load on the other, thus streamlining goods picking maneuvers.
- Manual picking carts. These are used to transport boxes, complement order pickers, or to carry out order prep with the pick-to-cart method. Picking carts are recommended for products that are small and easily transportable.
- Conveyors. Roller conveyors for boxes, totes, and bins and pallet conveyor systems can be used to facilitate goods-to-person order picking because they bring the products to the pick stations. Workers remain at their stations, waiting to receive the items they need. As a result, they’re much faster when completing each order.
- Industrial robotic arms. These help operators in handling heavy loads. These robots are similar to human arms, as they contain components that carry out rotational motion and linear displacement. Industrial robotic arms have enhanced the pick and place order picking technique.
To sum up, warehouse machines speed up order prep operations, aid operators in carrying out their tasks, and reduce errors.
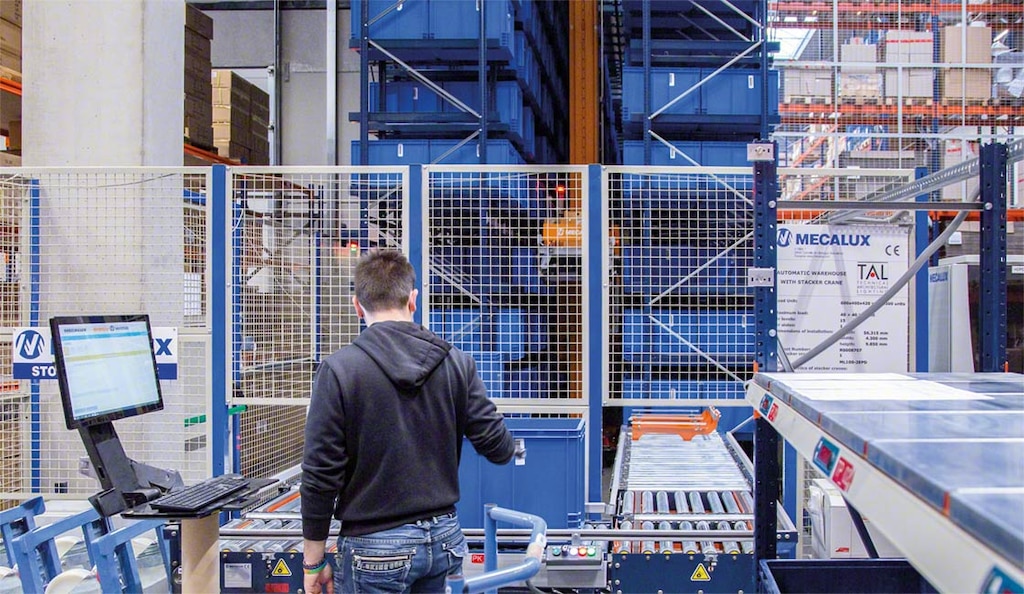
Choose the best machine for your logistics facility
There’s a wide variety of warehouse machinery on the market, so choosing the right one is decisive for ensuring maximum logistics efficiency. This decision depends on multiple factors, but three of them stand out above the rest: the warehouse layout design, the supply chain flow required, and the type of goods managed.
At Interlake Mecalux, we’re specialists in personalized logistics solutions, designing and implementing facilities in which manual and automatic warehouse machines coexist. Don’t hesitate to contact us. One of our expert consultants will offer you the best solution for ensuring maximum logistics effectiveness.