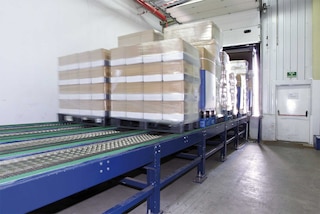
Automatic truck loading and unloading systems
Automatic truck loading and unloading systems have become the ideal solution for improving agility and safety during the goods receipt and dispatch process at the warehouse docks.
The loading docks are a vital part of any distribution center. The more docks an installation has, the greater the goods flows or, in other words, the number of trucks that enter and leave the warehouse. As a rule, it usually takes about 30 minutes to unload a truck manually, depending on the type of products and their weight. Automating this operation could cut this time to under 10 minutes.
In this post, we’ll explain what exactly an automatic truck loading and unloading system is, how it works, and what advantages it brings.
What’s an automatic truck loading and unloading system?
Also known as an ATLS (automated truck loading system), an automatic truck loading and unloading system refers to the automatic insertion and removal of pallets into/from a truck with minimal operator intervention.
These systems are located in the docking area, a key point of access for every installation. Therefore, it’s necessary to design their layout down to the last detail, choose the type of dock to be built based on the space available, and, above all, define the exact number of docks. This last element will hinge on the material flows, delivery volume, time when most of the goods are received, time needed to unload and move the freight, etc.
The emergence of automatic truck loading and unloading systems is forcing companies to adjust the design of their installations. The reason? The flexibility they provide. It’s pretty clear that if you reduce your truck loading and unloading times, you’ll most likely need fewer loading docks because the ones you have will be more efficient. As a result, warehouse layout design will vary in that part of the space earmarked for the docking area can be used for other operations.
How does automatic truck loading and unloading work?
Automatic truck loading and unloading is performed as follows (in general terms, as there are details that will change as per the system and its components):
- The truck, with its doors already open, backs up to align itself with the loading dock. Once it’s arrived at the limit, the dock door opens.
- After connecting the truck to the loading dock power source, the automatic goods loading and unloading can begin.
- When unloading, pallets enter the facility via a conveyor system (in the case of a fully automated warehouse). Meanwhile, for loading, when this operation has finished, the truck is ready to transport the freight.
In a matter of minutes, the goods loading and/or unloading process has been carried out successfully, without accidents, and with minimum staff intervention.
Elements of an automatic loading dock
The parts involved in an automatic truck loading and unloading system depend on the type of solution implemented. As of today, there’s no standard system, as each supplier offers a personalized solution tailored to the type of goods, truck, dock, etc.
With this in mind, the main components of an automatic truck loading and unloading system are:
- Roller and/or chain system. This drive system consists of chains, rollers, or a mix of both. For example, in the warehouse our company built for hygiene product manufacturer Hayat, the solution is based on two central chains and four lines of rollers that go up and down hydraulically to transport the pallets.
- Extendable forks. The system features the movement of extendable forks, which are linked to some of the rails.
- Skids. This relates to the positioning of hydraulic skids that raise the load and transport it to the required position.
These elements are often complemented with lifting platforms, hydraulic tables, and chain or roller conveyors that interact with the automatic loading and unloading systems.
Do I need to modify my trucks?
One common question concerning automatic loading and unloading is whether you should make modifications to the trucks. The answer is yes, as you need two combined systems to carry out automatic loading and unloading: one on the truck and the other on the warehouse loading dock platform.
This is why automatic truck loading and unloading systems are primarily used for internal transportation within a single company (between the production and distribution centers).
On the other hand, if you merely want to load goods onto the trucks automatically, there are, in this case, systems that don’t require you to change any aspect of the vehicles. These solutions, however, are less common and more complex. They can include, for instance, an arm that loads, lifts, and inserts the pallets into the truck or an automatic transfer car that moves along the various loading docks.
Advantages of automatic truck loading and unloading systems
Automatic loading docks offer numerous benefits that help to significantly improve a business’s profitability:
- Raised productivity: automatic loading platforms let you load and/or unload a full truck holding 33 pallets in just a few minutes, thus increasing the number of goods dispatches and receipts.
- Leveraged surface area: streamlining truck unloading shortens the time taken to complete the dock-to-stock process. This means you’ll need less space in the staging area and can dedicate that surface area to other operations.
- Protected goods: automation does away with sudden movements when loading and unloading freight from the truck, preventing damage to products. Consequently, reverse logistics activity will diminish.
- Workforce optimization: the docks are one of the busiest areas of a warehouse. Automatic truck loading and unloading systems reduce the number of workers required in this zone, allowing them to be assigned to other tasks.
- Operator safety: the goods loading and unloading process is one of the most critical and high-risk operations in the warehouse. Automating this process eliminates the possibility of accident, making this area safer and less crowded.
Lastly, all these plus points have a direct effect on lowering operating costs. A reduction in staff required, less wear and tear on handling equipment, more safety, increased productivity … with all these advantages, it’s fair to say that automatic truck loading and unloading systems ensure a fast ROI (return on investment).
Fully automated dock to stock
Automatic truck loading and unloading systems are the first and last link in a 100% automated supply chain.
With them, and with the implementation of a pallet checkpoint, conveyors, and stacker cranes, any company can completely automate its dock-to-stock process. At the same time, automatic truck loading and unloading systems use conveyors to collect the goods that the stacker cranes have removed from the racks to be loaded onto the truck.
Warehouse management systems are fundamental in both goods receipt and dispatch. In the case of goods pending arrival, the company’s ERP notifies the WMS — both communicate continuously and bidirectionally — that a truck will arrive with the stipulated pallets (ASN – advance shipping notice).
As for dispatches, the WMS is charged with organizing the pallets to be distributed. It assigns each product to a preload channel according to its route or customer.
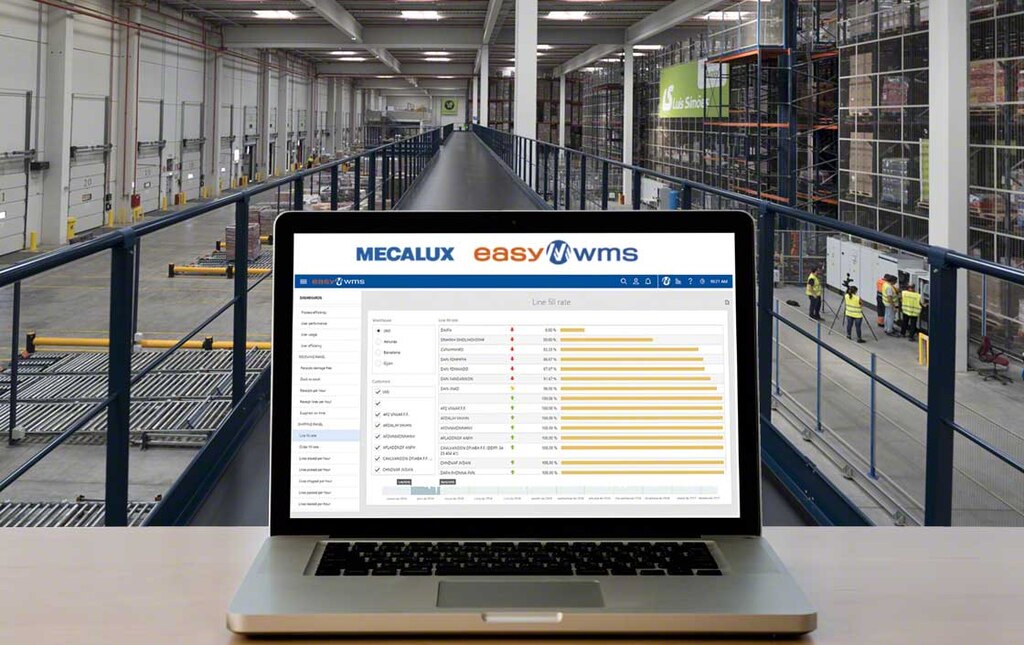
Do I need an automatic truck loading and unloading system?
Automating truck loading and unloading is extremely efficient when working with heavy merchandise and stock flows requiring speed (for example, with just-in-time systems).
In addition to agility, automation gives installations a plethora of advantages, among them, operator as well as product safety. Safety is an essential requirement in sectors such as the pharmaceutical and food industries. For example, we built an automated clad-rack warehouse for Grupo Siro, one of the largest companies in Spain’s food sector, with automatic truck loading and unloading systems.
If you think it’s time to improve throughput as well as safety in your installation, don’t hesitate to contact Interlake Mecalux. We’ll advise you and show you all the advantages automation brings to the entire supply chain.