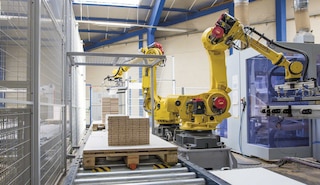
Industrial robotic arms take the wheel
Reduced logistics times have compelled companies to automate their processes to achieve maximum productivity. A good example of this is the prevalence of industrial robotic arms, as they speed up repetitive tasks that, in the past, were assigned to operators.
In fact, this technology not only improves production and supply chain efficiency, but also lets you load heavy objects and perform operations at height automatically — without human intervention.
Hence, more and more companies are choosing to implement this solution. A market research report by consulting firm Information and Communication Technology (ICT) indicates that the turnover of these devices will rise from $18.9 billion to $39 billion in 2024, accounting for a 206% increase.
In this post, we explain how they came about and when they gained a foothold in the warehouse, analyzing their advantages and main applications in industry.
What are robotic arms?
A robotic arm is a programmable device whose main functions and behavior mimic those of a human arm. The different parts that make up the robot are joined and connected to each other in such a way that the arm makes rotational and linear motions.
A robotic hand is attached to the end of the arm as an extension. Hands can take the form of a gripper, a suction cup, or a claw, depending on the functions they fulfill. These include fastening, goods movements, picking, and parts assembly, among others.
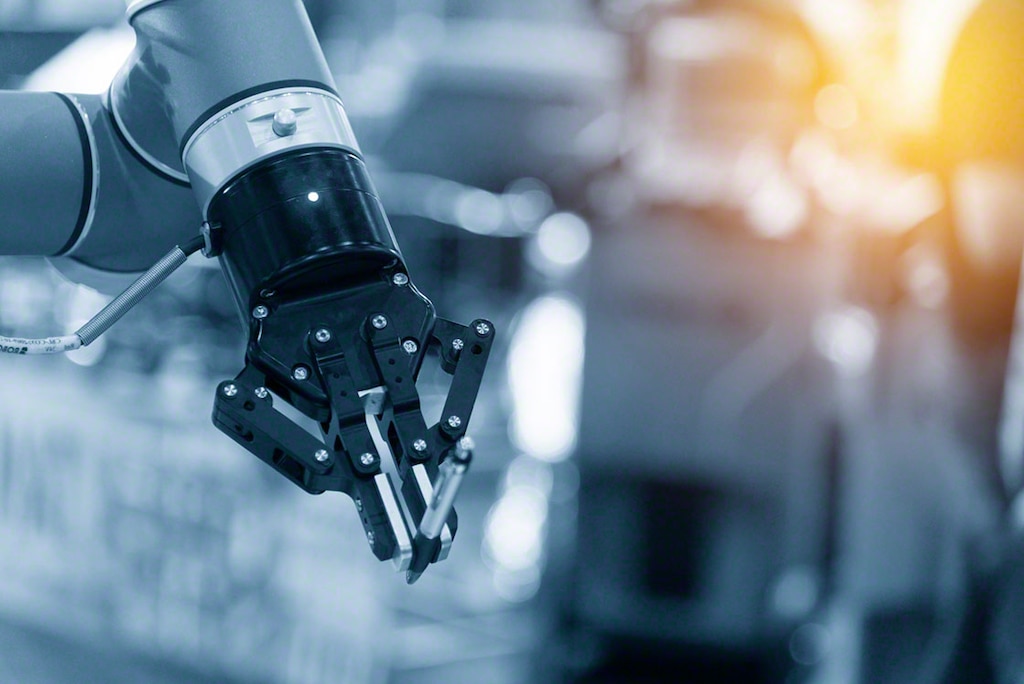
The first industrial robot prototype is considered to be that of English engineer Bill Griffith P. Taylor in 1938. It wasn’t until the 1970s, however, that a feverish technological race was underway, mainly between US and Japanese businesses, with the aim of revolutionizing the industrial mass production market through robotics. Nowadays, German company Kuka and Swiss firm ABB are two of the leading manufacturers in the development of these devices.
What’s their purpose? Industrial robotic arm applications
These machines are mainly employed to simulate or substitute the abilities of the human arm in production and logistics operations. As they are fully automated, industrial robotic arms carry out the same functions as operators but with the capacity to handle heavier loads at a quicker speed and without the fatigue that humans experience when making repetitive movements
These devices, which can operate alone or form part of an assembly line, are used in industries that call for extreme precision, such as the automotive sector. They’re also useful in fields requiring movements and in the pick and place of heavy loads.
This is the case, for example, of Porcelanosa, a leader in the ceramics industry. Our company equipped this firm with the latest technology at its logistics complex in Vila-Real, Spain, which supplies the eight businesses that make up the group. A robotic handling arm was installed at each pick station to help operators move the more cumbersome loads. This machine is charged with moving the heaviest packages from the buffer zone to the pick stations at the right time, without having to use pallet trucks or forklifts to handle these kinds of parcels.
Industrial robotic arms: advantages to automating operations
The implementation of industrial robotic arms in production or storage installations helps you to achieve the following:
- Significantly boost operational throughput: in contrast to operators, industrial robotic arms can repeat the same task for as long as necessary.
- Optimize complex processes and make them efficient: in terms of heavy loads and operations requiring great precision, such as the assembly of certain parts in the automotive sector, a robotic arm alone can achieve optimum throughput.
- Ensure the utmost safety of all operators: the inclusion of these robots in production lines and logistics processes prevents workers from having to carry out operations that aren’t ergonomic and that pose greater risks.
- Reduce production costs and workforce: despite the initial investment, in the long term, automation cuts costs and boosts the staff necessary in line with the installation, providing a quick return on investment (ROI).
- Guarantee the viability of operations in extreme conditions: only an industrial robotic arm can ensure productivity in refrigerated and controlled environments.
As for drawbacks, the implementation of robotic arms constitutes a high initial investment on the part of the company. And their true benefits are only really derived from very specific repetitive tasks involving similar-sized loads. That’s why robotic arms aren’t advisable for repetitive movements unlike those of an arm (which makes small movements or turns) or for goods that aren’t similar.
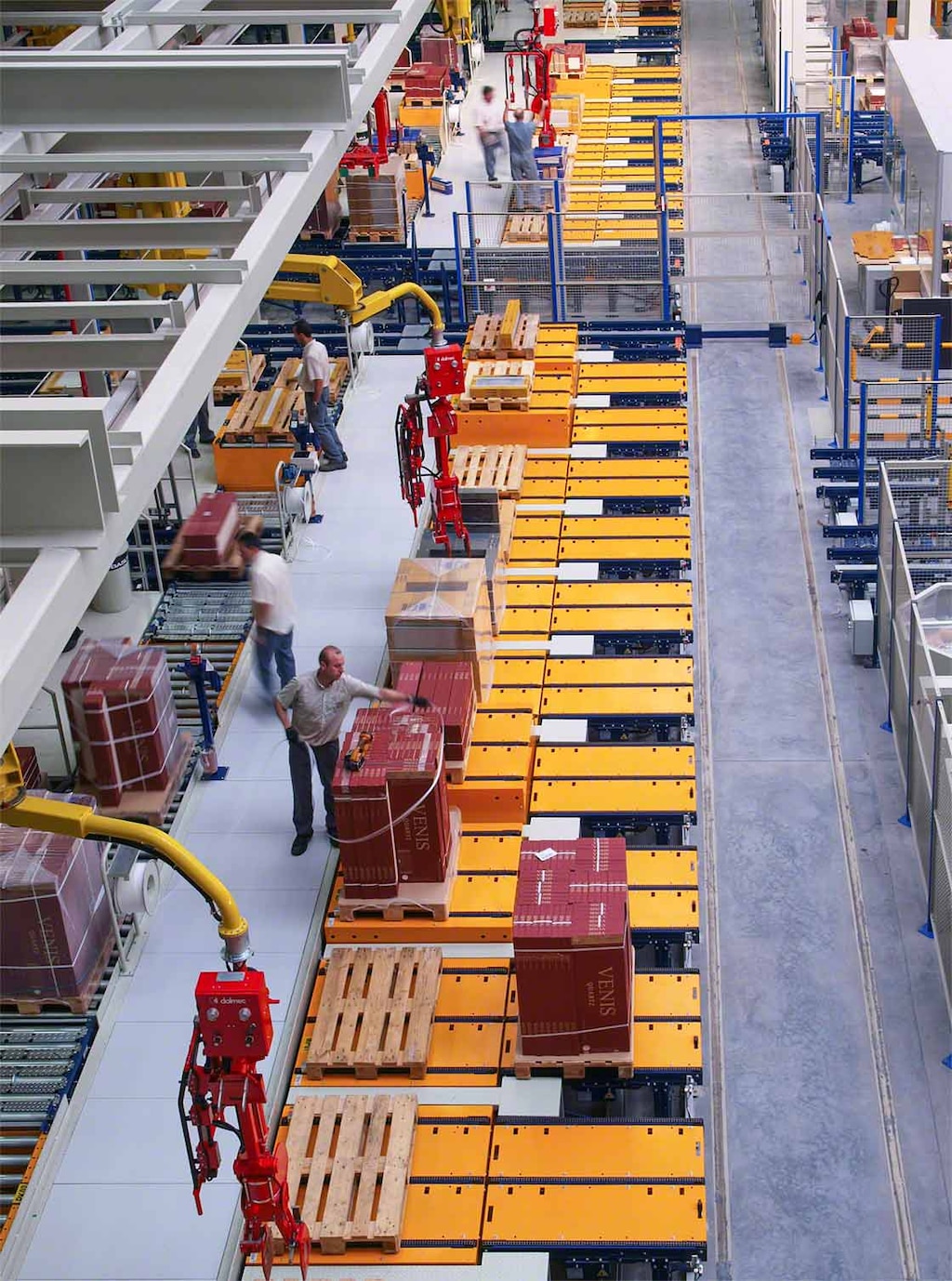
Types of industrial robotic arms
There are multiple varieties of robotic arms according to the movements they produce, the products they handle, and the operations in which they participate. Let’s take a look at the main kinds on the market today:
- Cartesian robot: device with three linear axes that, thus, only moves in a straight line. This variety is employed especially in pick and place and assembly tasks.
- Cylindrical robot: commonly used to handle die-casting and spot-welding machines and to perform highly complex assembly operations. Its cylindrical configuration enables it to make one rotational and two linear movements.
- Polar/spherical robot: it owes its name to the fact that it’s precisely the spherical coordinates that mark this device’s movements with respect to another reference system. These machines are helpful in gas welding, metal casting, and milling production processes.
- SCARA robot: the acronym of Selective Compliant Assembly Robot Arm, this technology stands out for its flexibility, as it has up to four degrees of freedom. This allows for quick and easy movements in comparison with other types of robots, such as Cartesian.
- Articulated robot: this machine has a minimum of three rotary joints, making it popular in more complex production processes. This robot is used in the automotive industry, for example, in spray painting.
- Parallel robot: this category includes delta robots and features a mobile platform and rotary joints, guaranteeing a wide range of movements. These machines serve to prepare orders of smaller products in particular.
When automating an installation, the logistics manager is responsible for deciding which type of robotic arm to install, based on the warehouse layout, goods flow, type of loads, and picking volume, among other factors.
Progressive implementation of AI
Articulated robotic arms are just another example of the commitment to automation gradually being made in warehouses and production centers. It’s clear that the incorporation of these machines ensures maximum business productivity and competitiveness.
Therefore, these robots will increasingly complement the automated storage systems already well-established in Industry 4.0 facilities, such as stacker cranes, conveyors, and the Pallet Shuttle system.
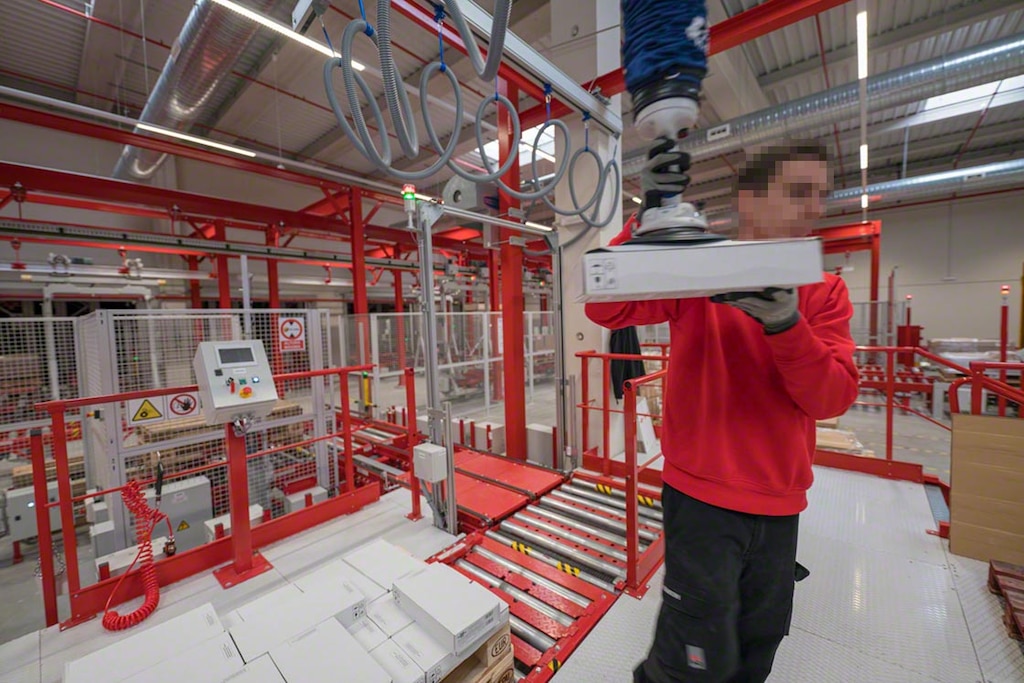
Ultimately, industry requires efficiency and safety in each of the operations that make up the supply chain. Industrial robotic arms ensure more agile, error-free production.
If you’re interested in deploying automated solutions in your installation, don’t hesitate to contact us. One of our expert consultants will give you advice on how to automate your warehouse.