
Stacker cranes: which type is best for your warehouse?
The market offers different types of stacker cranes to meet the needs and attributes of each warehouse: from installations ranging from 26' to 148' tall to those with different unit loads (boxes and pallets) and extremely varied movement flows.
Likewise, the stacker crane extraction system can be adapted to operate with single-, double-, and triple-deep racks, based on whether the goal is more agility or increased storage capacity.
In this post, we delve into the different kinds of stacker cranes installed in automated warehouses and their particular characteristics, advising you on the model that best fits your needs.
Types of stacker cranes for boxes and pallets
There are several varieties of stacker cranes available according to the goods to be handled: stacker cranes for pallets and those that work with lighter unit loads (e.g., boxes), also known as miniload AS/RS (automated storage and retrieval system). The main difference between them lies in the size of the stacker crane and the weight supported, as stacker cranes for pallets are much larger and robust than those for boxes.
In addition to the goods they handle, each type of stacker crane can be classified by its structure and, more specifically, the number of masts. The mast is the body of the stacker crane. It incorporates what’s known as the cradle, which comprises forks that support the unit load. Depending on the load dimensions or the desired operating speed, the stacker crane will be formed by one mast (single-mast) or by two (twin-mast).
The stacker crane moves along a bottom rail attached to the concrete floor slab and an upper guide rail fixed to the rack profiles. These are charged with stabilizing the stacker crane and absorbing lateral forces when inserting and removing goods from the racks.
All stacker cranes can operate 24/7 in temperatures as low as -22 °F. In order to operate in both cold storage and ambient temperature facilities, stacker cranes are equipped with a warehouse control system (WCS) that executes the movements indicated by the warehouse management system (WMS).
Single-mast stacker cranes
Available for both boxes and pallets, these machines are made up of a single mast and are designed to provide the utmost functionality and efficiency in installations with lighter loads.
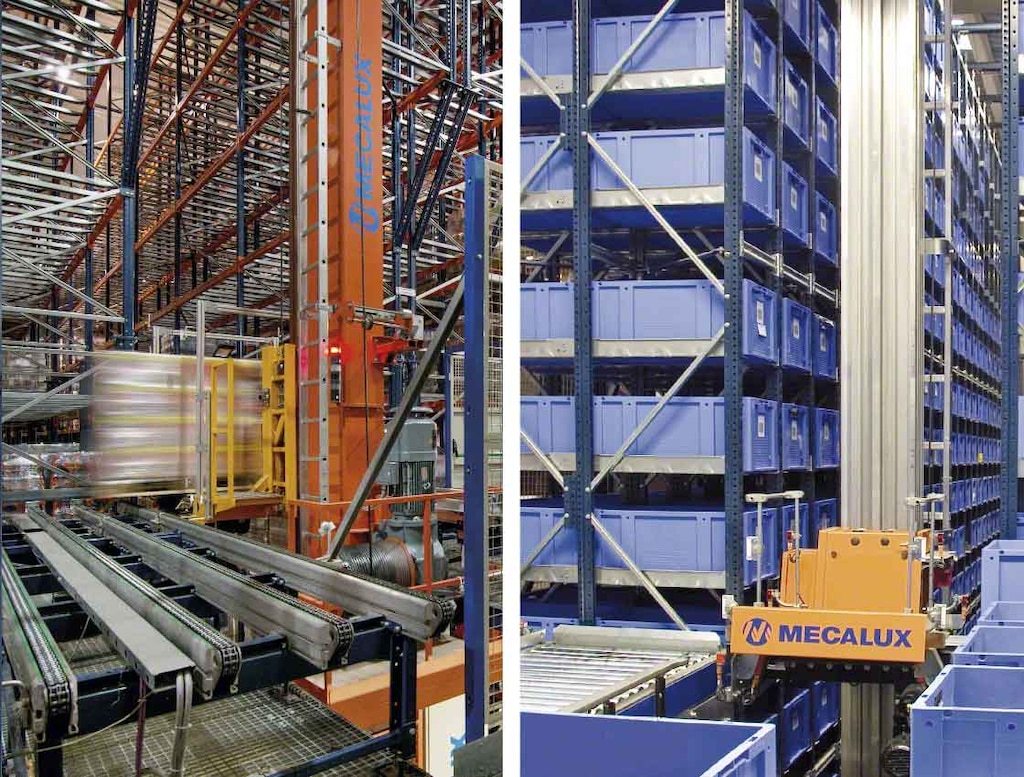
With regard to single-mast stacker cranes for pallets, Interlake Mecalux features up to five models. These range from the MT-1 model for shorter installations to the MT-5 model, capable of reaching 148' high.
The height of the stacker cranes is conditioned by the weight of the unit load, that is, the taller the stacker crane, the lighter the weight of the pallet. Therefore, the ideal pallet weight for these types of stacker cranes is between 1.1 and 1.65 tons. The wide array of models makes it possible to choose the most appropriate stacker crane for the available space and the goods to be handled.
FEATURES | MT-1 | MT-2 | MT-3 | MT-4 | MT-5 |
---|---|---|---|---|---|
Max. height – single-deep | 59' | 79' | 108' | 118' | 148' |
Max. height – double-deep | 51' | 72' | 89' | 108' | 148' |
Single-deep telescopic fork | Yes | ||||
Double/triple-deep telescopic fork | Optional | ||||
Automated Pallet Shuttle | Optional | ||||
Max. permitted load – single-deep | 1.65 t | 1.65 t | 1.65 t | 1.1 t | 1.1 t |
Max. permitted load – double-deep | 1.1 t | 1.1 t | 1.1 t | 1.1 t | 1.1 t |
Max. travel speed | 722'/min | ||||
Max. travel acceleration | 2'/s | ||||
Max lift speed | 217'/min | ||||
Max. lift acceleration | 2'/s | ||||
Side-mounted cabin | Optional | ||||
Operations temperature range | From -22 °F to 104 °F | ||||
Max. load dimensions | 39" x 51" x 94" | ||||
Pallet type | 48" x 40" GMA pallets/31.5"- and 39"-wide Euro pallets | ||||
Energy recovery system | Optional |
In terms of boxes, we offer two varieties of single-mast stacker cranes. The ML-50 is lighter and devised to achieve high productivity when handling 110-lb-boxes at heights of 39'. The other intermediate variety (ML-100) is sturdier and can load two boxes, each weighing 110 lb, at 39'.
FEATURES | ML-50 | ML-100 |
---|---|---|
Load capacity | Up to 110 lb | Up to 220 lb |
Max. height | 39' | 39' |
Unit load | Box, 1 unit: 16" x 24" | Box, 1 unit: 24" x 32" / 2 units: 16" x 24" |
Double-deep telescopic forks | Yes | Yes |
Twin-load extraction fork | No | Yes |
Max. travel speed | 590'/min | 656'/min |
Max. travel acceleration | 3'/s | 2'/s |
Max. lift speed | 328'/min | 295'/min |
Max. lift acceleration | 4'/s | 2.5' /s |
Extraction type | Telescopic fork | Adaptable to box type |
Twin-mast stacker cranes
Their structure consists of two vertical masts with a lifting cradle in the middle that’s used to access all the storage levels. These types of stacker cranes are more resistant and robust than the twin-mast variety, which makes them perfect for handling heavy loads. They also enable high throughput due to their to agility.
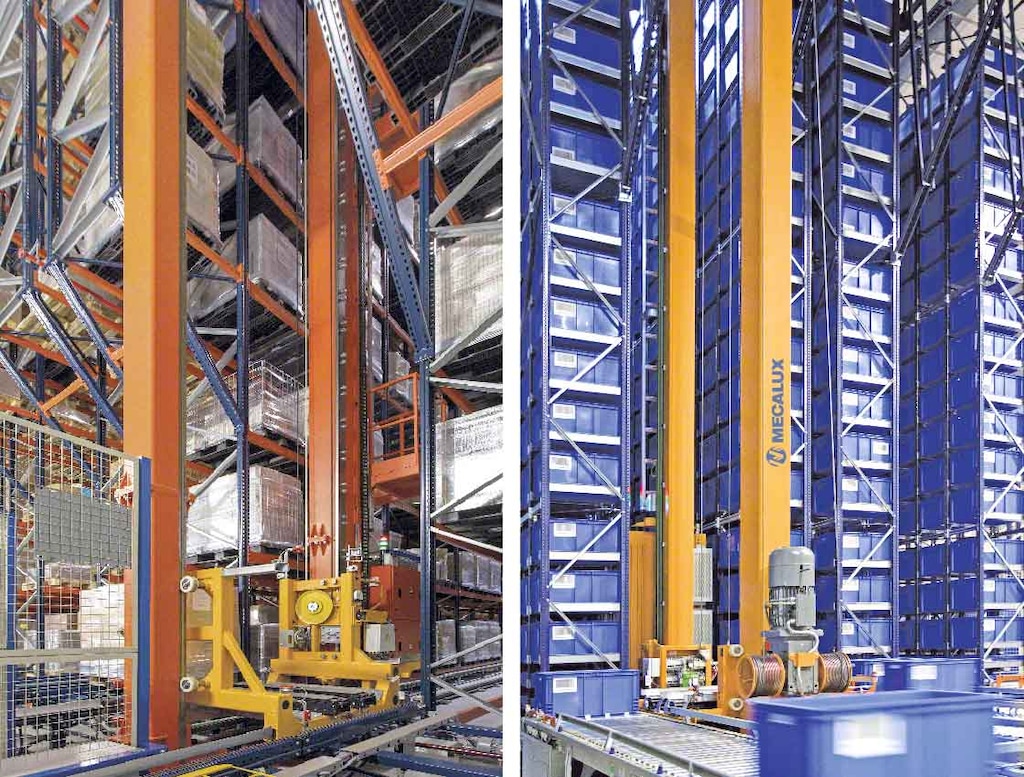
The pallet variety of these stacker cranes is ideal for handling pallets weighing up to 1.65 t. In accordance with the required height, Interlake Mecalux has seven available models of twin-mast MTB stacker cranes. The MTB0 stacker crane has been added to this family. It’s a more affordable, energy-efficient model that handles 1.65-ton pallets but at a limited height: 59'.
FEATURES | MTB-1 | MTB-2 | MTB-3 | MTB-4 | MTB-5 | MTB-6 | MTB-7 |
---|---|---|---|---|---|---|---|
Max. height – single-deep | 39' | 56' | 72' | 89' | 115' | 131' | 148' |
Max. height – double-deep | - | 39' | 66' | 89' | 115' | 131' | 148' |
Single-deep telescopic fork | Yes | ||||||
Double/triple-deep telescopic fork | Optional | ||||||
Max. permitted load | 1.65 t | ||||||
Max. travel speed | 722'/min | ||||||
Max. travel acceleration | 1.6'/s | ||||||
Max. lift speed | 217'/min | ||||||
Max. lift acceleration | 2.6'/s | ||||||
Automated Pallet Shuttle | Optional | ||||||
Optional raisable maintenance cabin or onboard static cabin | Yes | ||||||
Operation temperature range | From -22 °F to 104 °F | ||||||
Max. load dimensions | 43" x 51" x 94" | ||||||
Pallet type | 48" x 40" GMA pallets/31.5"- and 39"-wide Euro pallets | ||||||
Energy recovery system | Optional |
For their part, twin-mast stacker cranes for boxes can reach heights of 66' and handle up to four boxes, each weighing 110 lb.
Double-deep twin telescopic forksFEATURES | MLB100Q-2EPSF | MLB100Q-2EPDF | MLB100Q-2ECDF |
---|---|---|---|
Max. height | 40' | 40' | 40' |
Min. height | 16.5' | 16.5' | 16.5' |
Type of extraction system | Single-deep twin telescopic forks | Double-deep twin telescopic forks with belt | |
Max. permitted load | 2 x 110 lb / 2 x 220 lb | 2 x 110 lb | 2 x (110 + 110) lb |
Box/container size | 16" x 24" / 24" x 32" | 16" x 24" | 16" x 24" |
Max. travel speed | 250'/min | 250'/min | 820'/min |
Max travel acceleration | 4.8'/s | 4.8'/s | 5.9'/s |
Max. lift speed | 295'/min | 295'/min | 295'/min |
Max. lift acceleration | 4.9'/s | 4.9'/s | 4.9'/s |
Twin-mast stacker cranes with Pallet Shuttle
This combination of a stacker crane with the Pallet Shuttle system is only applicable to palletized goods. It is the evolution of the twin-mast stacker crane described above, the difference being that it incorporates a motorized shuttle tasked with extracting and depositing the pallets from and on the racks. The shuttle can enter channels up to 131' deep.
It’s a widely-used solution for maximizing storage capacity. This optimization of space involves less accessibility to the goods, so it’s especially advantageous for companies with diverse low-to-medium-turnover SKUs. On the other hand, it’s a very handy option for automated cold stores, as it results in major savings in energy consumption.
Trilateral stacker cranes
As opposed to those above, trilateral stacker cranes have the ability to retrieve and deposit pallets from/in the racks in three positions — from the front and either side — thanks to their rotating head. In contrast, single-mast and twin-mast stacker cranes can only operate in two positions, preventing them, for example, from leaving pallets on consoles located at the ends of the racks or to pick pallets from the ground level in the front position.
Trilateral stacker cranes are the go-to solution for warehouses already working with manual trilateral turret trucks and that want to automate processes without interrupting operations. Why? They are very simple to install: they also move along rails, but, unlike other stacker cranes, they don’t require an upper guide rail. (That is, there is no fastening device at the top of the stacker crane). This allows for easier installation in warehouses that already have racking set up, without having to modify the building structure.
A case study illustrating this type of facility is that of Disalfarm at its warehouse in Rubí (Barcelona, Spain). This leader in the pharmaceutical distribution sector transformed 15 aisles of pallet racks managed with manual forklifts into a fully automated installation operated by means of trilateral stacker cranes What’s most remarkable about this project is that our company optimized the warehouse without requiring the company to stop its activity at any time.
Types of extraction systems
Within the configuration of each type of stacker crane, you can choose the type of extraction system that best fits the unit-load depth (number of pallets deep) of the racks. It should be noted that the cradles of the stacker cranes can be customized to be able to handle several unit loads simultaneously (one on each side).
The extraction system is a decisive element for the performance of the stacker cranes. The choice of extraction system is directly related to the agility and/or storage capacity required by each warehouse. In other words, the fewer the unit-loads deep, the greater the flexibility in movements; meanwhile, the more positions in depth, the higher the capacity and the lower the performance.
Extraction systems for pallets generally comprise telescopic forks made up of two arms joined together by a motor-driven drive shaft. One motor is installed when working with single-deep racks, while two motors are used in the case of double-deep racks.
The extraction system of stacker cranes for boxes, in turn, consists of telescopic forks composed of two sliding structures. It’s also very common to employ a motorized belt fork, operated by a dual-belt system that pulls the box.
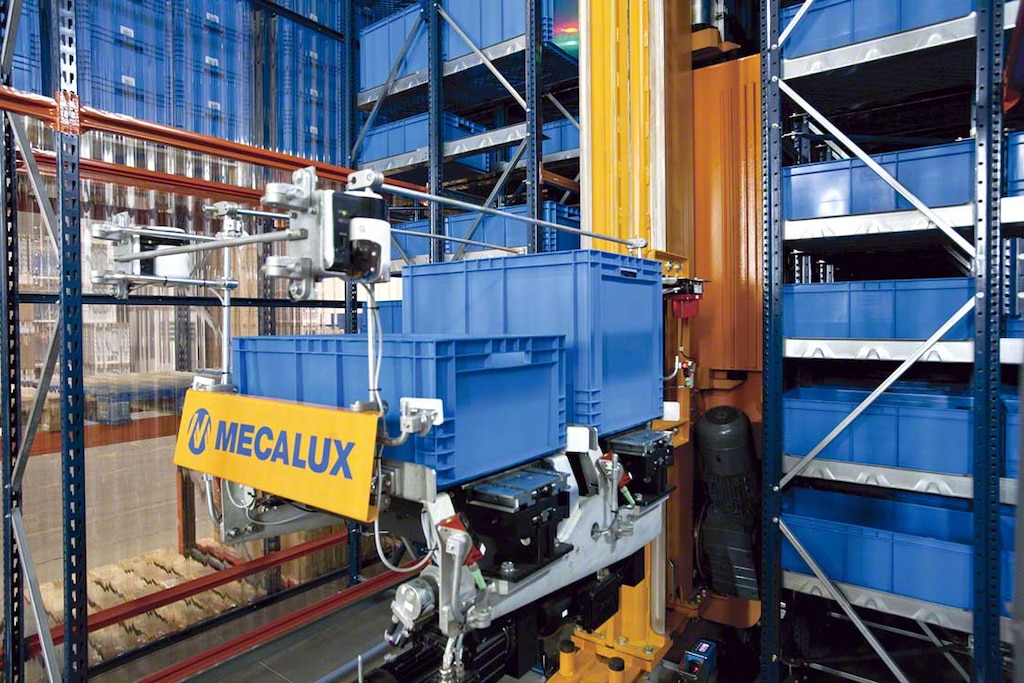
Single-deep system
The single-deep system is a mechanism that makes it possible to extract load units from single-deep racks.
This type of extraction system provides the highest throughput, as, when loading a single unit load, agility in handling takes priority over storage capacity. This is also the most recommended system for working with very heavy loads.
Double-deep system
With the help of telescopic forks, it’s possible to extract or deposit pallets or boxes in double-deep racks. This way, you achieve a balance between agility and storage capacity.
It’s a common solution for optimizing storage space when you don’t require high movement flows and work with few SKUs.
Triple- or quadruple-deep
This extraction system works with racks that are three or four unit-loads deep. This exceptional solution is only implemented when there’s a very specific need and the warehouse prioritizes capacity over agility.
This is the case of the WOK facility in Poland, where our company outfitted two 283-foot-long aisles with four-pallet-deep racks on each level. Two twin-mast stacker cranes are tasked with handling up to four pallets weighing no more than 1323 lb.
Motorized roller conveyor platform
This extraction system is used to feed pallet flow racks composed of rollers and with several positions deep. It ensures high loading and unloading speeds, since movements are continuous and synchronized.
This is the system installed at the Laboratorios Maverick warehouse in Tarragona, Spain, where a single-mast stacker crane with an onboard roller conveyor inserts pallets in flow channels This facilitates the gravity displacement of the load from the highest to the lowest part of the channel.
Which stacker crane do I need?
Choosing the right stacker crane for your warehouse is no easy task. There’s no rule of thumb, as each installation has its own quirks. Likewise, the different varieties of stacker cranes can be modified to provide a more personalized solution.
With this in mind, first, you need to be absolutely certain of your company’s needs and goals, the type of product to be stored (quantity, size, weight, number of SKUs, etc.), the type of material flows required, the warehouse layout, and your budget.
Then, we’ll be able to analyze the movements the different types of stacker cranes are able to execute, always according to the extraction system used. This will depend on:
- Travel speed
- Lift speed
- Accelerations at any axis
- The time needed to remove or deposit the unit load
Out of all the options, it’s important to assess which one will give you the most functional and cost-effective features, always striving to strike a balance.
Of course, the various types of stacker cranes can be adjusted and adapted to the demands of each warehouse. However, both the height and type of extraction system are conditioned by, among other factors, the depth and dimensions of the racks.
If you’re not sure which stacker crane is the one for you, get in touch with Interlake Mecalux. Our team of experts will help you choose the stacker crane that will provide you with agile, efficient, error-free, and cost-effective service.