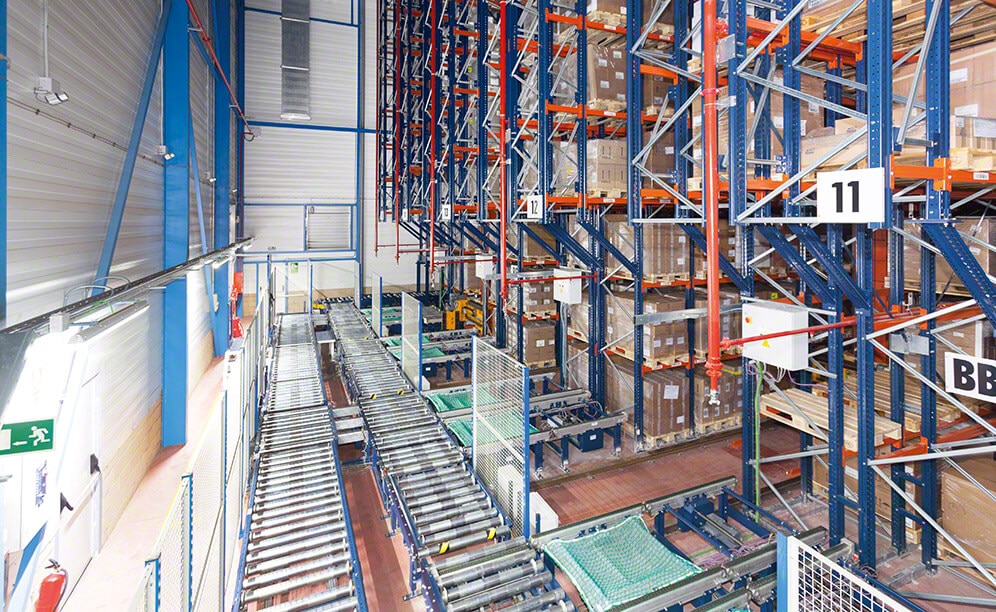
Disalfarm attains capacity, productivity and oversight with the automation in distinct phases of its traditional warehouse
Straightforward, budget conscious automation at Disalfarm with trilateral stack cranes
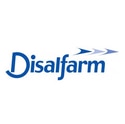
This logistics center located in the installations Disalfarm owns and runs near Barcelona (Spain) was built on a 9.64 acre area. The warehouse, now fully automated and with a storage capacity for more than 19,000 pallets, has significantly improved the productivity of the company. All this, while still providing full customer service during the expansion and modernization of the warehouse.
About Disalfarm
Disalfarm, S.A. is a logistics company founded in Spain by Bayer Laboratories, Boehringer Ingelheim and Novartis to consolidate their domestic operations, for both the storage and distribution of specialty pharmaceuticals.
The company started doing business in 2000, aspiring to be a leading distributor company in the pharmaceutical sector. To achieve this, it was essential to work with a quality system that ensured proper manufacture and distribution as required by legislation. Today, Disalfarm has a wide assortment of products ranging from specialized prescription pharmaceuticals, medication for hospital and veterinary use, nutritional supplements and other healthcare products.
Where is it located?
Disalfarm is located in the city of Rubí, an industrial zone near Barcelona that coincides with a major transportation hub. Its installations are close to the main logistics and distribution centers, which allows it to offer a fast, streamlined service to all its customers.Disalfarm’s needs: upgrade without reducing service
The growth that Disalfarm has experienced in recent years caused a substantial change in its storage needs. In 2000, a logistics center was set up combining storage and picking operations —less than 20% of orders corresponded to complete, single SKU pallets.
In this first phase, two warehouses were also created and dedicated to storage, with a prep and consolidation zone, the loading and unloading docks and, finally, the offices and utilities. As a whole, these installations occupy 2.4 acres. All the warehouse racks and the picking area were installed by Interlake Mecalux.
In 2007, there was barely enough room in the warehouse. The high number of forklift movements were overly expensive and, at the same time, increased the risk of workplace accidents, which Disalfarm wants to avoid.
In light of this situation, the challenge the company outlined to Interlake Mecalux was to update this logistics center without any change in its customer service.
The starting point: phase 1 and 2
The first phase, which took place in 2000, saw the building of:
- A ten-aisle warehouse with a capacity for 12,900 pallets of 32” x 48” in 50’ high racks.
- A picking zone comprised of carton flow racks with pick-to-light devices and box conveyors that connected this area with the one for packaging and consolidation.
- A zone for picking complete boxes directly from pallets.
- A warehouse for refrigerated products with a 290-pallet capacity.
- A closed warehouse for psychotropic products.
- Nine loading docks with an extensive maneuvering area.
In the second phase, five selective pallet rack aisles were added to accommodate 6,450 pallets, for a total of 19,350 pallets.
In addition, three new loading docks were completed.
Workflows have also increased considerably, reaching 1,100 pallets per day (500 incoming and 600 outgoing).
The following resources are used to move these many pallets:
- Seven front-loading forklifts to work in the docks, to supply the picking areas and deposit and extract pallets from the beginning of the aisle.
- Five trilateral forklifts to work exclusively within the inner storage aisles.
- 24 forklift operators (12 per shift).
The flow of merchandise in phases 1 and 2
Merchandise used to arrive at the warehouse fully palletized. The operator scanned the bar code on each pallet using a computer terminal and the warehouse management system (WMS) indicated which aisle it was assigned. Once the position was determined, front-loading forklifts were used to bring the pallets to the consoles at the end of the storage aisle. Then, trilateral forklifts could store the pallets in the locations established by the management system.
Output operations took place in reverse order. However, the majority of pallets moved on towards picking areas.
Phase 3: removing the in-warehouse transport of complete pallets
The growth of the company did not require a higher number of locations, but instead an increase in pallet flows. To achieve this, increasing the number of forklifts and operators was considered, with the consequent risk this would involve.
The installation had fifteen storage aisles, with five trilateral forklifts already in use. Although five more could be brought in, this was ruled out because the machines are semi-automatic and not very fast. So, the number of cycles was insufficient to fulfill its requirements.
Then, Interlake Mecalux brought up two options based on automatic roller and chain conveyors to eliminate all movements carried out by counterbalanced forklifts in the warehouse.
Phase 3: first option discarded
The proposed design had a primary conveyor circuit comprised of the following elements:
- Two main branches, perpendicular to the racks.
- Two conveyor lines (one input and one output) in each storage aisle.
- A pallet entrance and checkpoint in the docking area with rejects of unfit pallets.
- A direct exit to dispatch.
- Two exits to the picking areas.
It was the option that was most consistent with staying close to the docks, and was also a reliable solution to supply picking stations.
For storage operations, trilateral forklifts would be used and, in the future, increasing the number of forklifts or finding an automated solution would be considered. On top of this, the rear area would be set aside as an aisle-changing zone for the trilateral forklifts, as pre-planned in the first phase.
Phase 3: the solution in option 2
It was decided that the main part of the conveyor system would be located at the rear of the warehouse. That way, as had been customary, the main aisle would be kept for trilateral forklift maneuvers and the circulation of the front-loading forklifts.
This solution was more complex and costly because it involved setting up a circuit of conveyors on the bottom of one of the racks to move all the goods coming from the docks. However, this became the only feasible solution that did not interfere with day-to-day operations.
The movements between the entry conveyor lines and the locations were performed by trilateral forklifts. When the reconstruction was completed, the main aisle was enabled exclusively for trilateral forklifts to change aisles and for the few direct outputs that were sent to dispatch. From then on, the Galileo control program of Interlake Mecalux was incorporated, responsible for governing all automatic conveyor movements, from the entry and exit points, threading through the picking zone. RF devices would still be used to give instructions to the trilateral turret truck operators.
Phase 4: total warehouse automation
With the success achieved in automating the incoming and outgoing movements, and given the foreseen growth, it made sense to automate the entire warehouse.
Full automation brought up a new issue: the automatic machines (stacker cranes) on the market did not allow pallets to be placed at ground level. To remedy this, the only viable option was to raise the first level 24” to 28” off the ground and to set up a guide rail above the aisles. This solution entailed the loss of a whole warehousing level, or the equivalent of 1,290 fewer pallets.
As Disalfarm's needs could not tolerate such a loss in storage capacity, another way to automate had to be found or another logistics center needed to be built.
That is when Interlake Mecalux put the trilateral stacker crane on the market, a natural replacement for trilateral forklifts. It adapted perfectly to the features required by the Disalfarm logistics center, with the following:
- Pallets can be put as little as 4” off the floor.
- It has trilateral forks instead of the standard side-facing telescopic ones.
- A top-aisle guide is not needed, only the two guides on the floor.
- Its maximum height is 50’.
- It can hold a transfer bridge to change aisles.
- The Galileo control program is also used.
- As a minimum, this achieves the same capacity when using trilateral machines.
The changes made in phase 4
Minimal, easily done changes were applied. Basically:
- Install the two floor-level guide rails.
- Slight modification of the height between levels.
- Extend the checkpoint installed on conveyors at the front of the installation.
- Place safety enclosures to fit the entire installation according to the regulations on warehouse automation, especially those related to safe practices in aisles where AS/RS stacker cranes operate.
Entry into the aisles for warehouse maintenance tasks is carried out opposite to the conveyor, i.e., where the main aisle was when trilateral forklifts were used.
For the few outgoing operations with complete pallets, a pallet flow channel was arranged in each aisle above the pallet consoles in the old header. Counterbalanced forklifts can gain access to the consoles without having to enter the automated zones.
Communicating with the software
From the beginning, Disalfarm had a powerful warehouse management system (WMS) that adapted to its operational needs. Continuing to use this system was a must for managing the entire warehouse. For that reason, only the standard Interlake Mecalux control program needed to be implemented.
Namely, the Galileo Control System would perform all the movements inside the warehouse. IMecalux also developed a communication interface meaning both systems share information properly, as well as an intermediate management layer to avoid inconsistencies in orders of reserve products and location occupancy.
Advantages for Disalfarm
- Small space, big storage: the Disalfarm warehouse can locate 19,350 pallets of 32" x 48".
- Continued customer care: Interlake Mecalux optimized the logistics center of Disalfarm. Meanwhile, the company never had to stop serving customers and stayed in-house for the duration.
- High productivity: the automation of different storage processes has increased workflows, adapting to the needs of the company.
- Total control: the communication interface between the Disalfarm warehouse management system and Interlake Mecalux's standard control program makes it possible to manage all processes and operations that take place inside the warehouse.
Disalfarm warehouse in Barcelona | |
---|---|
Storage capacity: | 19,350 pallets |
Pallet size: | 32" x 48" |
Max. pallet weight: | 1,764 lb |
Racking height: | 43' |
Racking length: | 197' |
No. of stacker cranes: | 15 |
Type of stacker crane: | automatic trilateral |
Gallery
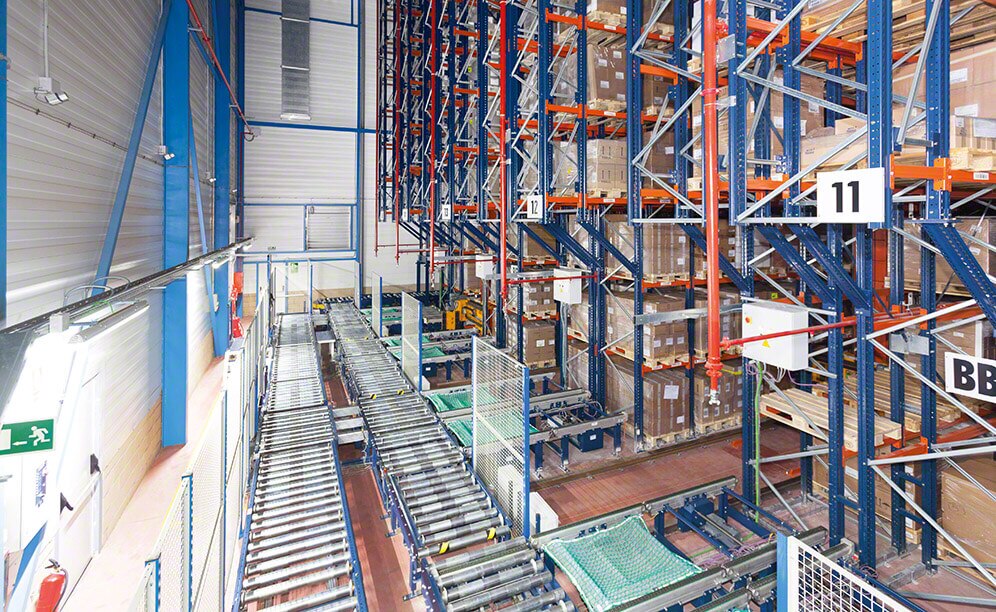
The warehouse, now fully automated and with a storage capacity for more than 19,000 pallets, has significantly improved the productivity of the company
Ask an expert