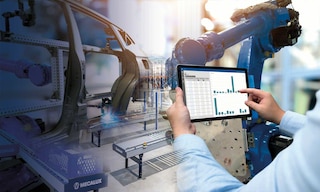
Push and pull system applied to manufacturing logistics
The push and pull system constitutes the two most common production methods. It has a direct impact on inventory management, the cornerstone of the warehouse. Should a product be manufactured beforehand or the moment it’s purchased? The choice of one strategy over the other has far-reaching consequences, not only on the production method, but on the way in which the company’s warehouse and logistics operations are organized. The choice will also directly affect the costs to be borne and the business’s profitability.
In this post, we analyze and explain the benefits, drawbacks, and differences between the push system and pull system, as well as their effect on each company’s manufacturing logistics.
Push and pull system: definition and differences
Push and pull are production systems characterized by organizing manufacturing based on demand. They differ precisely in terms of when production starts: before or after the sale of a product.
In the push system, the product is manufactured ahead of time. Therefore, this model is directly related to the predicted demand, as it’s vital to know in advance and with the utmost accuracy which merchandise customers will require, when, and in what quantity.
The pull system, on the other hand, adapts production to actual demand. This means that the product is manufactured only when a sale is made, that is, once the company receives the request. The customer is then given a specific delivery date. This method, which doesn’t consider the availability of finished product stock, tends to be adopted by businesses specializing in products manufactured on demand or completely personalized. It’s customary, for example, in the automotive industry.
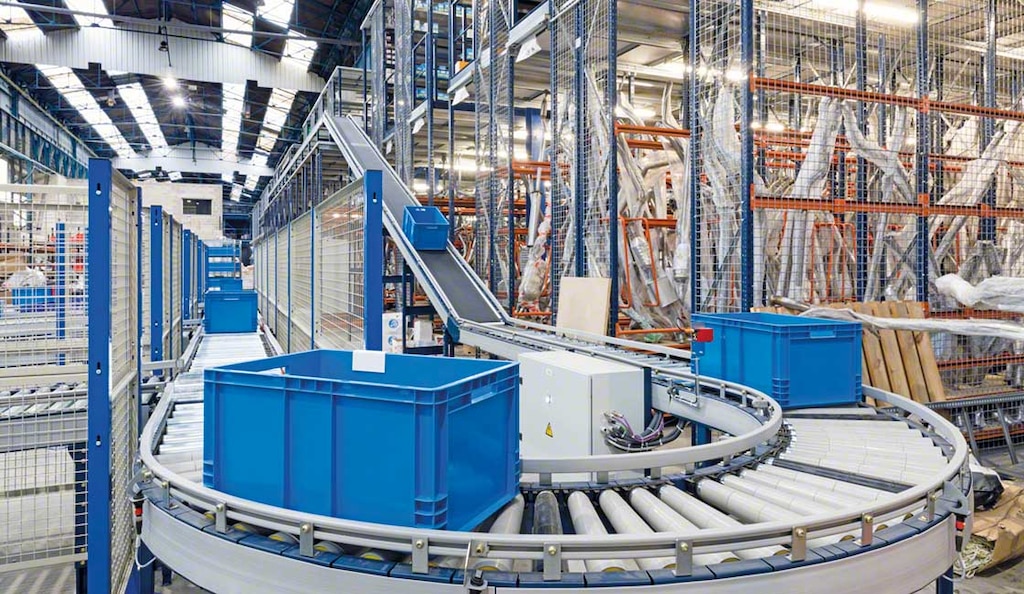
Push system: pros and cons
The main upside of the push system is that it reduces production costs per unit of product to a minimum, since it’s possible to produce in large quantities. This is known as economies of scale: the supplier brings down its costs by increasing its production volume. To adapt to possible variations in demand, it’s essential for the production system to be quick and flexible. This way, the business can carry out effective supply-chain procurement, satisfying demand and minimizing operating and storage costs by better planning its activity.
The main downside of this strategy has to do with possible errors in demand planning, such as the risk of a stockout (demand exceeds the forecasts) or the threat of overstock (production significantly outweighs estimated demand).
Pull system: pros and cons
The main plus points of the pull system are that it eliminates overproduction and lowers storage costs. Additionally, it minimizes the strong dependence of manufacturing on predictive analysis, (designed to anticipate changes in consumer habits). Most businesses that choose the pull model adopt the just-in-time (JIT) system, which brings down management costs and is closely linked to the Lean logistics philosophy, whose main objective is to cut logistics costs by eliminating processes that don’t add real value.
Another strength of the pull system and of on-demand production is the ability to personalize a product for the customer, which constitutes a competitive advantage.
Likewise, the pull strategy is usually employed when opting for more sustainable logistics practices aimed at minimizing environmental impact in the manufacture and storage of products.
The biggest disadvantage of the pull system is that, generally, it requires longer production times, forcing companies to inform their customers that the delivery of the merchandise won’t be immediate. Moreover, the manufacturing cost per unit goes up: the product won’t be mass-produced and, thus, economies of scale can’t be exploited.
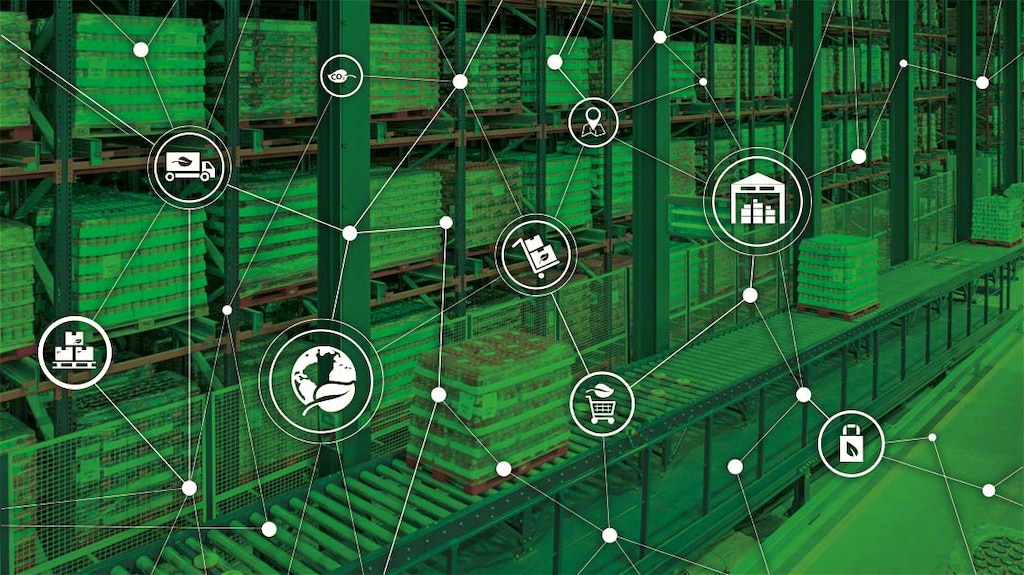
Adapting logistics operations to the push or pull strategy
In terms of logistics, the choice of a push or pull system has an effect on the different characteristics and operations of a warehouse:
- Storage capacity: if you decide on a push system, you’ll need to have a larger storage space, as all the stock you produce to anticipate demand will be stored in your facility. Drive-in/drive-thru pallet racks are ideal for optimizing warehouse space.
- Order preparation: this should be agile and efficient when implementing the pull strategy, to supply the production lines with the necessary goods at the right time.
- Movement flows: the use of automated storage systems and handling equipment, such as conveyors for pallets and electrified monorails, seamlessly connects the warehouse with the production plant, which is key in any pull model.
- Inventory management: regardless of the strategy employed, it’s fundamental to record all movements in the facility and, at the same time, assess the quantity of products in stock. To do this, it’s strongly recommended that you install a warehouse management system (WMS), in addition to an ERP and an MRP (material requirements planning) system.
All companies’ logistics operations are directly connected to the production strategy adopted. Therefore, it’s crucial to tweak that strategy to make the supply chain as efficient as possible.
Examples of the push and pull system
The choice of the production system is conditioned primarily by the type of product manufactured and its demand level.
As a rule, the push model is used in industries or companies in which it’s easier to predict demand, such as those with highly seasonal products. An example of this is Schaal Chocolatier, a leading French gourmet chocolate producer that uses the push production system to anticipate rises in demand at specific times of the year, especially during the Easter and Christmas seasons. To maintain an efficient supply chain, Schaal Chocolatier has a modern, high-tech automated storage and retrieval system (AS/RS) for pallets implemented by the Mecalux Group.
The pull method is especially suitable for companies that sell products with a high production cost, as it would be impractical to keep them in stock, pending a sale. This strategy is also employed for goods that allow for a high degree of personalization to adapt as much as possible to customer demands. This is the case of furniture manufacturer Forma 5. All its logistics operations are just-in-time. That is, the Easy WMS warehouse management system from Interlake Mecalux connects the production plant with the 35 facilities of its suppliers so that Forma 5 can receive the semi-finished products it needs at the right time.
There are also sectors that use a combined push and pull management strategy. The automotive industry, for instance, manufactures standard vehicles with certain features (push system). However, it produces others with personalized characteristics on demand (pull system). Israeli car manufacturer Zbeda Group has a miniload system (AS/RS for boxes) — also designed and installed by the Mecalux Group — that supplies the production lines when manufacturing both on-demand and mass-produced cars.
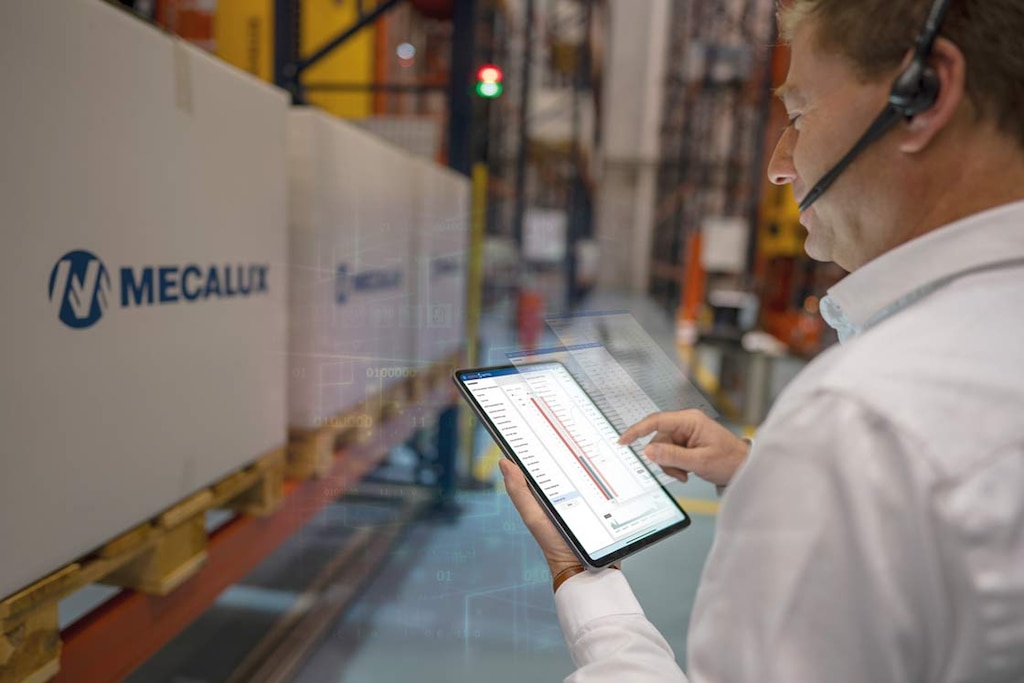
Strategies adapted to manufacturing logistics demands
Properly managing procurement and successfully controlling demand forecasting and its effect on inventory are major logistics challenges for any manufacturer. The particulars of these requirements, though, will be determined by the organization’s production strategy.
If you’re thinking about implementing a push or pull system, but your intralogistics operations aren’t quite up to the task, get in touch with Interlake Mecalux. One of our expert consultants will help you come up with the most effective solution for your company’s needs.