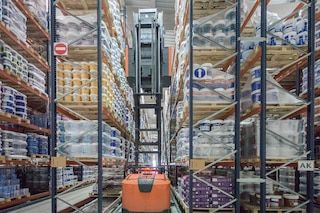
Overstock: how to avoid it
Overstock is one of the most common logistics issues in storage installations. Excess inventory stems mainly from improper planning and/or poor coordination between the different links in the supply chain. But what are its consequences?
In this post, we’ll analyze the concept overstock, its causes, and its effects on the warehouse. Most importantly, we’ll give you three strategies for getting rid of excessive stock in your installation.
What’s overstock?
Overstock occurs when the raw materials and finished products stored in a warehouse far outweigh demand. Against this backdrop, product inflows exceed outflows, resulting in a bottleneck.
This happens because of inadequate planning and/or coordination between the sales, logistics, and production departments, among others. Many companies make the mistake of not assigning the right turnover to a product, which leads to overstock. In fact, excess inventory is often seen in logistics installations that supply or store goods produced on assembly lines. But why is overstock generated?
Excessive stock can be produced for multiple reasons related to, for example, product seasonality, brand reputation, the entry of new players in the market, or the deterioration of a market’s socioeconomic conditions.
With that in mind, we can group the causes of overstock into two major groups:
- External factors: these result from socioeconomic changes unrelated to the company’s business activity. In this case, the warehouse continues to have the same stock levels in its logistics planning; product demand, however, isn’t the same. This leads to a situation where the installation has to reassign goods shipping and receiving orders to even out the imbalance. An example of this would be a shift in fashion trends or a financial crisis.
- Internal factors: these derive from errors made in the company’s own organization. These may be logistics mistakes (bad inventory management), or the sales/purchasing department might have been off on its growth forecasts.
Four problems arising from overstock
Excess inventory in the warehouse could lead to serious logistics cost overruns. These are some of its main repercussions:
- Inefficient goods movement flows: the need to store more merchandise in the installation makes it impossible to set up efficient slotting, extraction, and picking routes. The greater the number of items to store, the more difficult it will be to establish order in the warehouse.
- Stock spoilage: careless control of installation inflows and outflows could thwart product traceability. The pharmaceutical and food industries need to pay special attention to this, as their products are regulated by expiration and use-by dates. If there’s an abundance of stock for each SKU in the warehouse, it’s more likely that mistakes will be made in operations such as order prep and dispatch.
- Higher storage costs: excess inventory triggers increased investment in logistics land and more expenditure on equipment and labor to manage the installation.
- Bad corporate reputation: a blunder in any warehouse operation will preclude a company from providing top-notch logistics service. Consequently, when faced with excess merchandise, operators are more likely to make mistakes in purchase orders, leading to customer dissatisfaction and complaints. This constitutes a great risk these days, which is especially crucial in light of the e-commerce boom. A negative user experience might cause customers to turn to the competition.
Overstock lowers a company’s profit margin, whether due to decreased demand or to an increase in supply. In the event of the latter, the firm needs to reinvest in storage installations to boost its capacity. The solution, in many cases, is not to acquire more logistics square footage, but to implement static or automated storage systems adapted to the warehouse’s workflow.
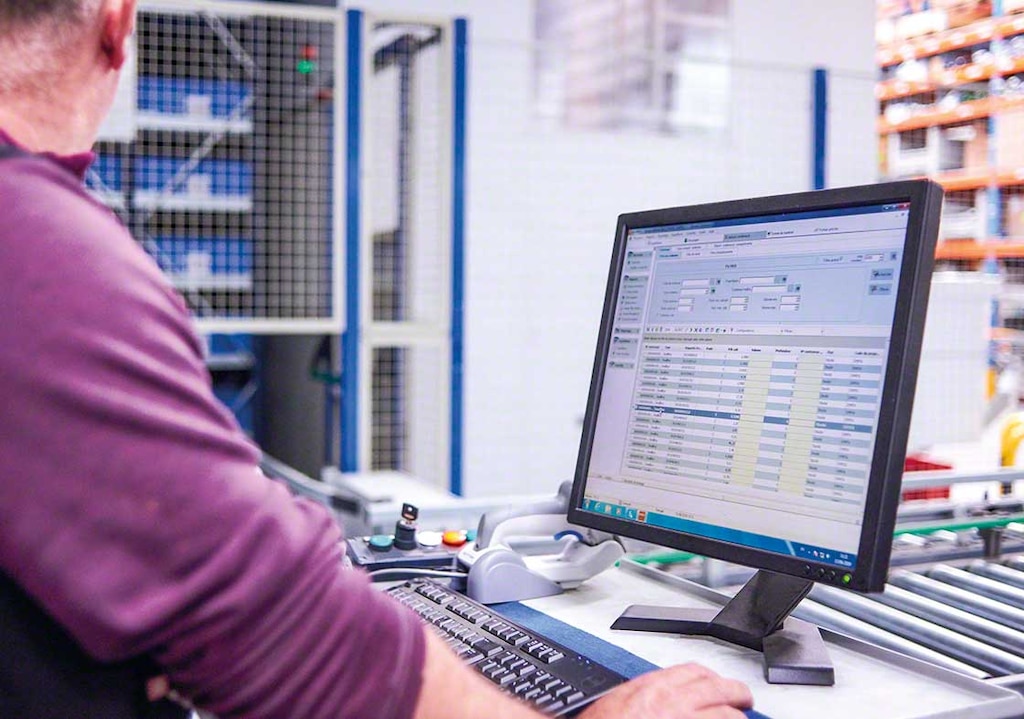
Three strategies for mitigating overstock
Excess inventory is a problem that can be solved with intralogistics solutions that ensure the installation’s efficiency and productivity. Although every business has its own particular needs, these are the three main ways to reduce overstock:
- Warehouse management system (WMS): a digital tool such as a warehouse management system predicts the exact stock supply based on the demand for and characteristics of each SKU. Thus, this software optimizes the company’s workflow, prevents the accumulation of excess stock for all SKUs, and assigns the most ideal product slots and picking routes. And it does all this to maximize the installation’s productivity.
- Appropriate storage systems: whether static or automated, the warehouse should be equipped with solutions that adapt to the business’s real needs. For example, when product turnover isn’t a priority, drive-in drive-thru pallet racks make the most of the storage capacity; this does away with having extra stock of a certain product.
- Optimized working methods: overstock can be minimized with operations such as just-in-time production and the cross-docking logistics practice. The warehouse doesn’t require a large amount of SKUs in either case, as it is coordinated with other installations to have the raw materials or semi-finished products at just the right time.
Overstock: a burden on the warehouse
The proliferation of sales channels — that is, omnichannel retail — has changed the two-way relationship between customers and businesses. Nowadays, organizations must maximize their efficiency to remain competitive in an increasingly complex environment.
For that reason, one of the primary logistics strategies every company should establish is how to optimize warehouse resources, especially to cut costs. In this scenario in which installations are more and more diverse, businesses have to invest in new methodologies that enable them to be efficient — even when they don’t have every SKU in stock.
Proper management of backorders (pending orders) starts with streamlining logistics processes and implementing automated storage and retrieval systems and digital tools. These guarantee maximum throughput and the elimination of errors in the warehouse.
For over 50 years, Interlake Mecalux has been providing intralogistics solutions that ensure warehouse productivity. If you have overstock in your installation, don’t hesitate to contact us. One of our expert consultants will offer you the best solution for your business.