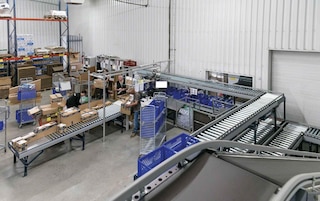
Stockouts: what they are and how to prevent them
A stockout happens when, on receiving an order for a certain product or raw material from a customer, your company does not have that item(s) in stock in the required quantities and conditions. For that reason, purchases cannot be fulfilled. This incidence has very negative repercussions, since not only is the sale lost, but the company's image is damaged in the eyes of the customer.
In our article, we discuss the key concepts related to stockouts: how to calculate this indicator, what the causes and consequences of this phenomenon are, as well as the main strategies to follow to prevent stockouts.
1. Stockout rates
Every stock management maneuver is based on a delicate balance between the demand for the product and its in-warehouse availability. Stockouts occur when this balance is tipped.
Within the KPIs to be measured (as part of logistics management) is the stockout rate, which is calculated as follows:
Stockoutrate = unfulfilled orders / total orders x 100
2. Consequences of stockouts
The immediate consequence of a stock shortage is an increase in logistics costs. The risk of stockouts is greater in the current climate because companies are faced with the daunting challenge that a larger inventory brings, as well as higher costs linked to logistics storage. So, in general, companies tend to keep these costs to a minimum. Methodologies such as just-in-time or cross-docking were conceived around this idea.
In this sense, it is clear that costs increase when a stockout occurs, but calculating all the losses resulting from this is complicated. Plus, these estimates will always be approximate because subjective factors come into play.
On the one hand, you find the clear loss of that particular sale that cannot be made (target value). However, other aspects must also be considered, such as the fact that stockouts lead to a flood of customers going over to competing companies in search of the requested product (subjective value). In addition, your brand image has been damaged which, in sectors such as e-commerce logistics, leads to a loss of confidence and seriously hinders future demand (subjective value).
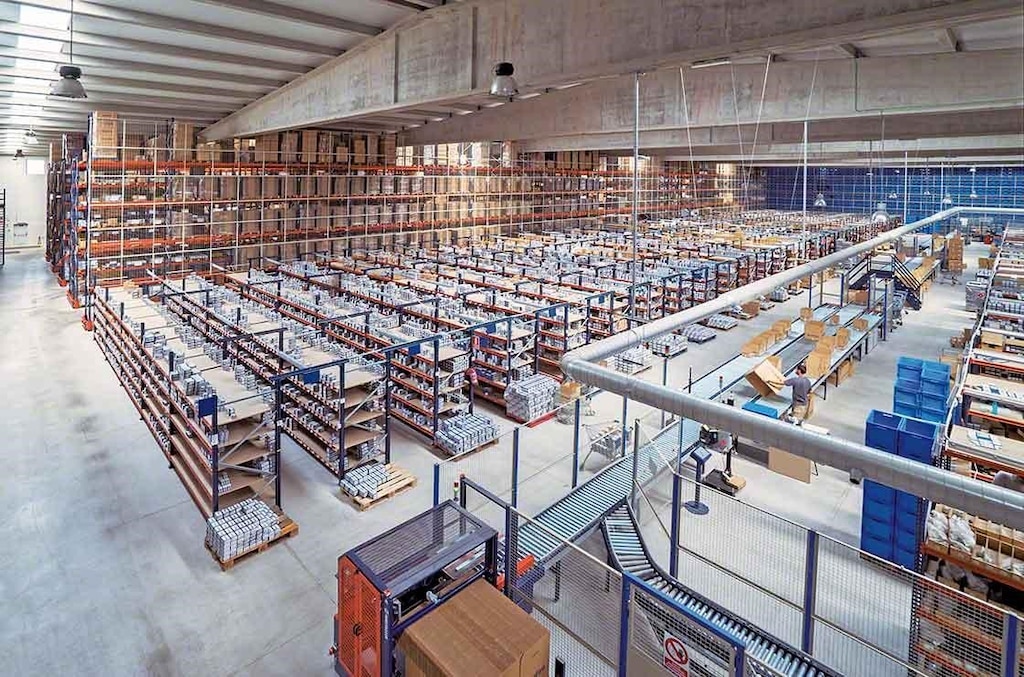
3. Causes of stockouts
Reasons for stockouts are heterogeneous and can be traced to different points in the supply chain. Take for example:
- An unexpected increase in demand: a very common example is that “favorite toy” which becomes hyper-popular during the holiday season. As the lead time for production and distribution is greater than the margin that the dates allow, a manual stockout usually occurs.
- Poor demand planning: demand forecasting is one of the most challenging areas in logistics. A wide variety of data needs to be analyzed to estimate future demand, including sales history, seasonality and key dates.
- Lack of accurate inventory data compared to what is actually happening, due to human error when locating products or when updating stock data.
- Shipment delays: if goods are received in the warehouse later than planned, this can lead to delayed delivery dates for the end customer.
- Supplier delays: if the suppliers are manufacturers, the lack of a single type of raw material can slow down an entire production line.
- Human error at different points in the supply chain.
4. Efficient management strategies to avoid stockouts
- Carry out demand forecasting properly
In today's highly variable logistics landscape, companies need to reduce uncertainty in demand forecasts and adjust supply as much as possible. In fact, big data applications have some of the most potential in logistics.
In order to achieve a solid demand forecast and, to a certain extent, to prevent stockouts, you need to:
- Understand that in any prediction you must consider a certain margin of error.
- Identify the current product life-cycle phase: it is only natural that products go through the market introduction (newness), growth, maturity and decline stages.
- Anticipate peaks of activity on key days and take into account your industry's seasonality.
- Calculate forecasts for the closest possible time periods, as the distant future is more uncertain than what lies right in front of you. Operating with a reduced lead time helps a lot in this sense.
- Have a computer system that structures the processes in the supply chain
Deploy specialized business management software. This has proved to be a powerful strategy for controlling and optimizing logistics flows. Due to the high complexity of the processes, different types of systems usually need to be integrated. In this line, Enterprise Resource Planning (ERP) stands out as a backbone linked to more specific systems such as warehouse management software or transport fleet management programs.
One of the main objectives of using these systems is to control available inventory levels at different points in the supply chain (these may be warehouses, but also physical stores, for example) and to establish alerts indicating when certain SKUs need to be replenished. These programs also minimize human errors in process management.
- Control stock management KPIs and be proactive with the data
Keeping track of key indicators in inventory management is a must to prevent inconsistencies that can lead to stockouts. So, here are some strategies to consider:
- Check the reorder point: i.e. the time when a replenishment purchase order should be issued to a supplier. The reorder point must be constantly reviewed, since it determines the minimum stock level a company should maintain to avoid stockouts.
- Mark the quantities to be purchased based on indicators such as goods turnover, coverage index (shows how long the company has stock for), and storage space occupation.
- Have enough safety stock to offset demand or supplier deviations, but without overstocking your warehouse.
- Adopt a perpetual inventory system
Occasionally, stockouts are triggered when you can’t locate products within your facility, even if they are readily in stock. This is a complex issue that can be solved by deploying a WMS that allows you to operate with a permanent inventory system. It is an ideal solution for businesses with a complicated, broad SKU base.
In this regard, our warehouse management software guarantees access to stock data in real time, so that you can control what is in the warehouse and where it is located. Plus, computerizing your stock database allows you to analyze your logs and view stock fluctuations to identify key products for your business.
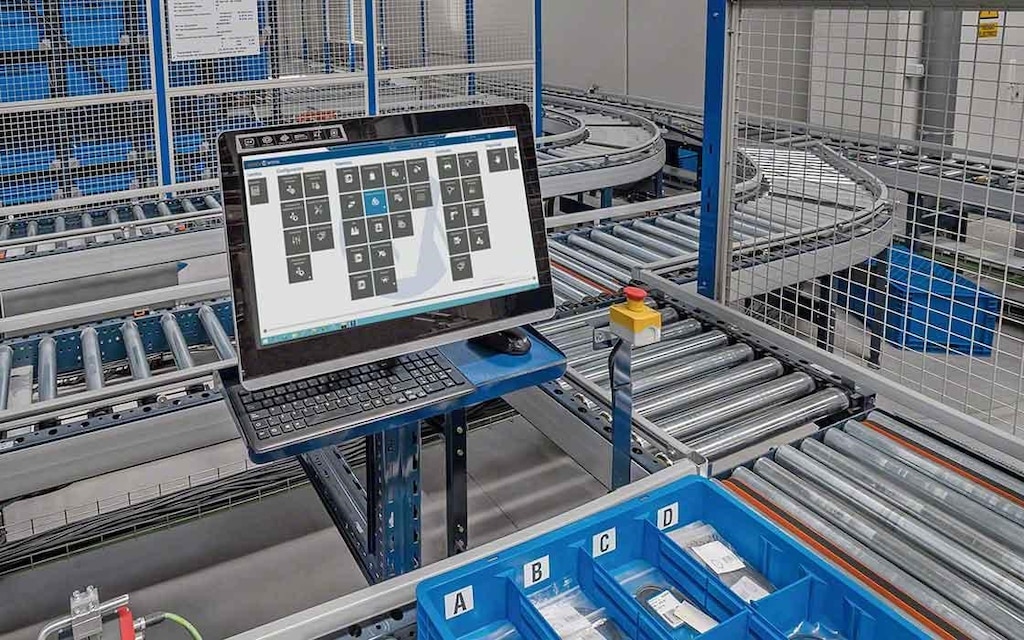
- Automate intralogistics processes and reduce spoilage of goods
In any inventory, there is shrinkage — in other words, lost goods due to deterioration, poor conservation, handling errors and even theft. Shrinkage is an issue that must be controlled so as not to precipitate stockouts. However, it is possible to implement measures that reduce shrinkage to a minimum. For example:
- Restrict access to you inventory data base. This is a piece of cake with a WMS such as Interlake Mecalux’s Easy WMS. You can manage access to the system by the work team and prevent unwanted tampering or pilfering.
- Automate load handling, as this greatly improves the safety of all movements and prevents accidents that can injure personnel or damage the goods. Use of machines also reinforces compliance with FIFO or LIFO goods flows.
- Automatically control SKU identification and data dumping into the system. For example, this is achieved through elements such as checkpoints, which guarantee the accuracy of the data shown in the WMS.
In short, despite the fact that having less stock might help you sleep better at night, inventory is a key regulatory element to ensure your supply chain runs smoothly. Preventing stockouts, then, becomes a clear objective for any company that wants to make gains. New technologies such as warehouse management software or automated systems are making it easier to achieve.