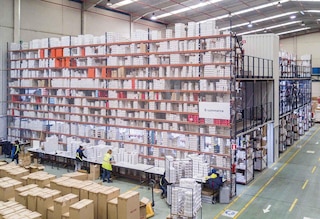
Warehouse space purposing: tips and strategies
Optimizing effective storage spaces is one of the primary objectives of any warehouse. The demand for more logistics warehouses and higher occupancy in general means many companies now face a land shortage that limits storage area expansion.
Given this situation, how can you adapt your warehouse to maximize its capacity while not changing its surface area? Let’s analyze different strategies to achieve this.
1. Make the most of space at height
When there is insufficient warehousing space, one of the most commonly used strategies is to exploit the vertical space of a facility. Following this premise, in-warehouse space can be optimized in different ways:
- Choose taller racks
Choosing industrial racks that add storage levels is a natural way to go when square footage comes up short. However, before opting for taller racks that fill up those cubic feet being wasted, it is important to consider the structure of the building (layout of beams and columns, for example). Also, look at the installation's safety requirements, the lift limitations of the handling equipment and the extra time it will take to extract the loads at height.
- Rack-supported structures (if the warehouse is to be built from scratch)
Rack-supported installations are the best example of optimizing warehouse space. In this type of logistics warehouse, every drop of storage space is squeezed out of the installation since the racks comprise the metal structure that supports the building.
So, this solution is considered especially for newly built warehouses. It is worth noting that most of these warehouses have fully automated operations, which enables work with loads at high levels (up to 40 meters high), without handling equipment being an obstacle.
- Mezzanines and walkways
Mezzanines and walkways are big allies for warehouses whose operations revolve around picking and order preparation tasks and where direct access to products is required. Not surprisingly, adding storage levels also means making good use of your site's vertical height. It is the best pick for those warehouses where person-to-product picking is carried out, where a wide variety of products and a flexible demand are available.
Successful examples of this strategy in action include: the spare parts warehouse of French company PAVI-Groupauto and the facility of Spanish 3PL provider Eralogistics, dedicated to the distribution of products sold online.
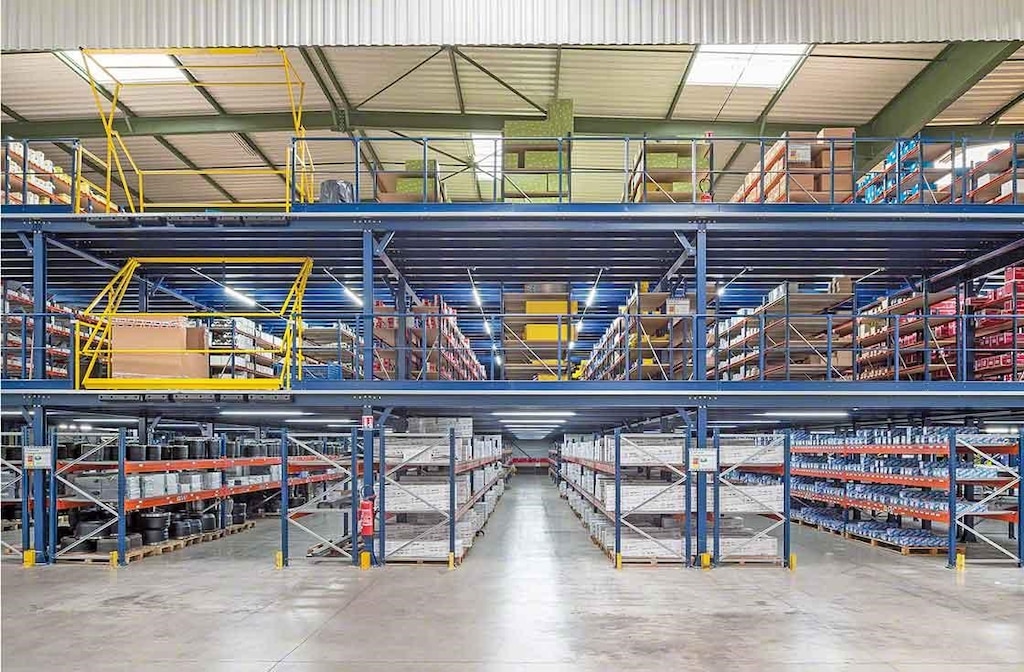
2. Reduce aisle width or make use of compact storage systems
Narrowing aisleways has a direct bearing on handling equipment, as they must be adapted to maneuver safely in less space. In many cases, the automation of certain operations is chosen to avoid setbacks. Thus, stacker cranes save space allocated to aisles. This is also done through:
- compact storage solutions or these combined with automated systems as illustrated by the advantageous connection between compact racking and the Pallet Shuttle.
- Mobile pallet racks, which open aisles automatically thanks to the motorized bases that move them.
3. Optimize warehouse inventory
Sometimes the lack of space in a warehouse is a direct result of stock disorganization. What can I do to optimize in-house inventory? Here are some tips:
- Evaluate the method you have chosen for managing storage locations, namely, what criteria you use to slot the goods. Then, estimate whether it needs to be adjusted or changed. For example, following the emergence of warehouse management systems, the computerization of information makes it possible to implement chaotic or “disorderly” storage, which has a domino effect on optimizing warehouse space.
- Detecting obsolete inventory and disposing of it: don't forget that when SKUs spend too much time stuck in a warehouse, this increases storage costs. Action should be taken before obsolete stock becomes a chronic problem, overloading an installation’s capacity.
These are some of the strategies that many companies have applied to optimize warehouse space without having to undertake expansion projects. Don’t hesitate to get in touch if you would like an Interlake Mecalux's expert to analyze your storage facility and provide you with personalized advice.