
How does an AS/RS work?
A big question that comes to mind when exploring automated warehouses is how to integrate the different systems so that operational logic is free-flowing. Since we have covered the main characteristics that define warehouse automation, today’s article will try to answer these questions: How does an automated warehouse work? And, what operations can be automated?
First and foremost, when it gets down to choosing what to automate in a warehouse, this automation must equal more profits.
Automated warehouse operations
To the naked eye, AS/RSs in operation might seem like something out of science fiction due to their size and complexity. However, if you analyze this in further detail, you’ll realize a simple logic lays behind the used of automated systems for a warehouse. In a nutshell, how an AS/RS works really comes down to the operations that can be automated:
1. Systems that automate load transportation in a warehouse
Distribution of resources in a company’s warehouse flows in large part to picking operations, that can end up consuming more than 60% of operational costs. Massive amounts of time are spent on picking, dedicated to locating and sending unit loads between different points of a warehouse. These movements or routes can be automated in sections:
-Locate and extract unit loads from the racks
A strategy followed by many logistics centers faced with space deficits involves looking upwards and into what high-density vertical storage can offer. Running a manual handling framework means management of loads at heights is complicated and opens the door for new, risky situations in terms of workplace safety and the goods.
In this sense, automated systems have emerged as the solution, featuring:
- Automatic stacker cranes: How do they run inside an AS/RS? They replace your manual forklifts: These machines collect the load from the end of the aisle and move them to a specific location (and vice versa). The automatic stacker cranes' movements can be single (hauling a load one-way) or combined (using the trip back from the pallet racks to retrieve another SKU). Stacker cranes are able to move pallets that weigh up to 1,500 kg in single-depth racks and 1,300 kg in double-depth racks.
- Pallet Shuttles: this involves a moving shuttle that runs along the racking structure to place and retrieve pallets. It automates the movement that, otherwise, would be done via manual forklift with more speed, precision, and safety.
- Miniload systems: mimic stacker crane operations but applied to the slotting of boxes, totes or small-sized unit loads. Miniload systems speed up small item picking.
- Connect different warehouse zones
Connecting different warehouse zones is another of the operations that can be automated, normally making use of roller or chain conveyors or electrified monorails (EMS).
These elements come with a pre-established circuit that starts out from the simplest designs up to highly complex ones that can string together logistics facilities and even different floors of a plant.
Another common use of conveyors is to help load and unload pallets. Located in the reception and/or dispatch docks, these units are capable of unloading full trailer loads packed with palletized goods in a quick, safe manner.
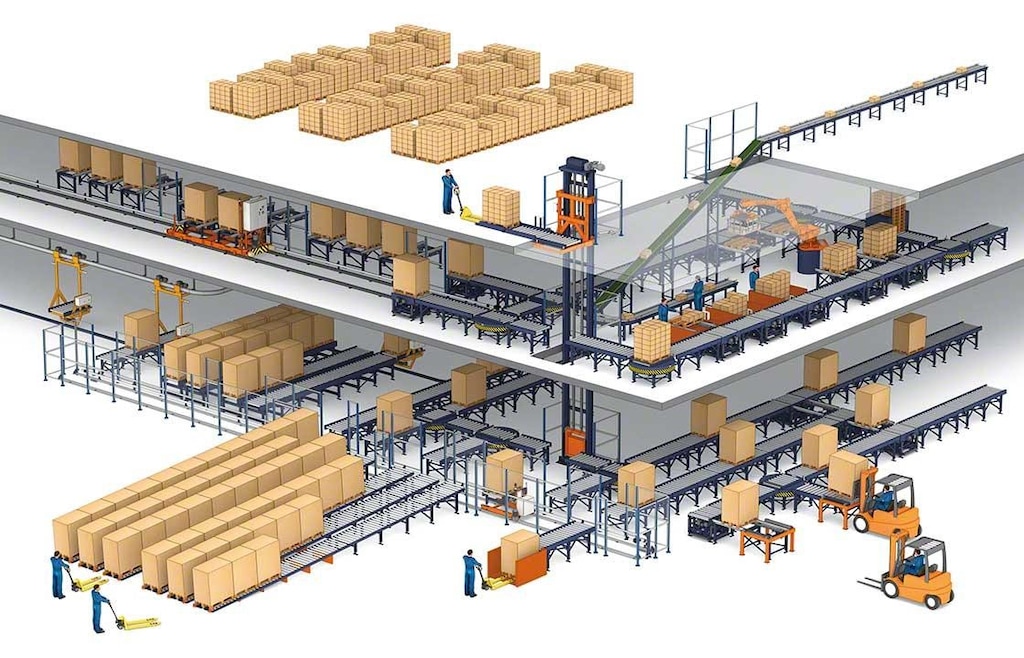
2. Control software and warehouse management software
If you want to talk about how an AS/RS works, you can’t forget that your logistics software is a key player. In this context, here are two main types of software:
- Control software: it executes the movements of the machines. This is the case of the Galileo system by Mecalux, which guarantees the precise transportation of goods and allows programming of safely run, ever variable and complex machine movements. It integrates with a WMS.
- Warehouse management system (WMS): it decides where to place the goods and keeps continuous control of their locations (perpetual inventory). A WMS like Easy WMS communicates with the control software telling it where to send the machines, optimizing the routes they follow.
By joining both facets (location/extraction of goods and their transportation), we find the answer to how an AS/RS works. The automated systems and the corresponding software make it possible to increase the productivity ratios, reducing the space and number of movements needed to carry out warehousing operations.