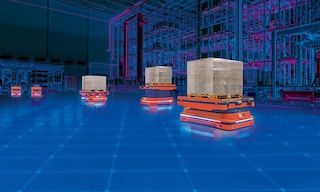
SLAM in robotics: Industrial applications
SLAM robotics is gaining momentum as more companies turn to autonomous mobile robots and vehicles to streamline operations. This technology enables these machines to navigate unfamiliar environments without human intervention, allowing them to perform tasks on their own. But what exactly is a SLAM system? Let’s take a closer look at its benefits and industrial applications.
SLAM in robotics and how it works
SLAM (simultaneous localization and mapping) is a set of techniques that allows robots and autonomous vehicles to map out unknown environments and navigate them without external guidance. By analyzing data from their onboard sensors, these machines can pinpoint their position with high accuracy.
SLAM systems typically rely on the information LiDAR scanners gather on the robot’s surroundings, supplementing this with other sensors such as depth cameras. Then, an AI-powered algorithm processes this data to build a usable map. SLAM navigation leverages mapping and artificial intelligence to help robots make smart decisions in dynamic environments such as warehouses, where autonomous mobile robots (AMRs) often work alongside humans and other machines.
AMRs use SLAM mapping to orient themselves. These intelligent vehicles navigate logistics centers and industrial facilities independently, automating and streamlining internal goods transport. Implementing AMR warehouse solutions accelerates internal flows in multiple intralogistics operations, driving productivity and efficiency. These machines detect and avoid all kinds of stationary and moving obstacles, readjusting their route in real time.
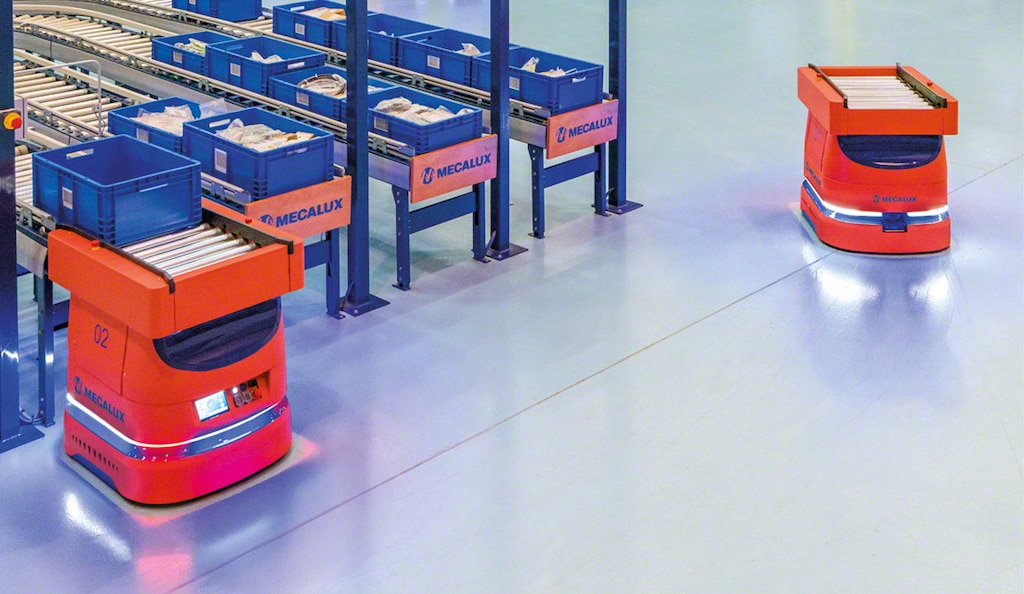
Applications of SLAM in robotics
Robots equipped with SLAM technology offer major advantages for companies investing in industrial automation. For instance, as AMRs can generate their own maps, they adjust easily to the warehouse layout, eliminating the need for beacons or other fixed infrastructure.
These are some of the most common applications of SLAM in robotics:
- Internal material transport. In warehouses, AMRs can move loads from one point to another independently. These machines navigate freely using routes generated by software that assigns the optimal path for each task.
- Self-driving vehicles. Autonomous cars rely on SLAM to drive safely, employing LiDAR sensors, cameras, and radar to perceive their surroundings and create detailed maps in real time.
- Robot vacuums. Robotic vacuum cleaners utilize SLAM to avoid obstacles and prevent falls while cleaning rooms (or even large industrial spaces) efficiently and thoroughly.
- Inspection and maintenance. Robots equipped with SLAM can explore complex infrastructure like pipelines or power plants, detecting anomalies.
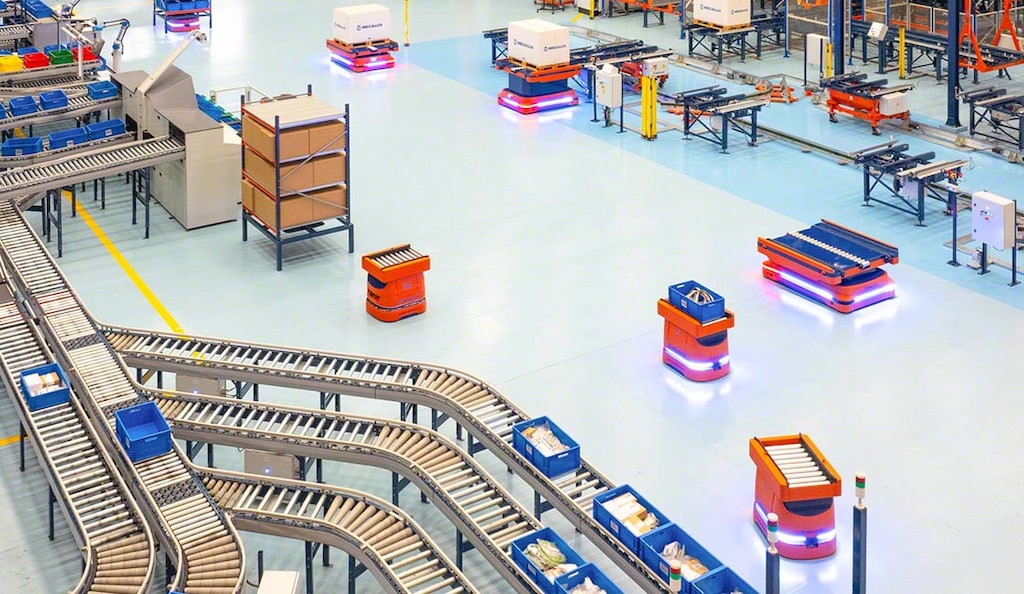
SLAM robotics examples in industrial settings
AMRs operating in warehouses and other industrial environments are designed to navigate complex spaces with people, goods, storage systems, and other machinery. Thanks to collision avoidance sensors and scanners, their movements are stable, reliable, and continuously monitored by fleet management software. These applications also allow updates to the maps originally generated using SLAM. Once a robot maps a facility, that initial layout can be edited to mark off restricted zones or highlight workstations that require interaction.
This level of adaptability makes AMRs a perfect fit for industrial settings. They’re easy to integrate, requiring no changes to existing infrastructure. And since fleets can be expanded by simply adding new robots, AMRs offer a scalable solution for companies looking to grow or handle seasonal peaks in demand.
SLAM technology in 5 questions
How does SLAM technology work in robotics?
In robotics, SLAM enables autonomous robots and vehicles (e.g., AMRs) to map unknown environments using data from sensors like LiDAR and cameras, all guided by AI-powered algorithms.
What are the benefits of SLAM in robotics?
SLAM enables robots to build a map of their environment while simultaneously determining their location within it. This results in greater autonomy, accurate navigation, collision avoidance, and the ability to handle complex tasks such as exploration and object manipulation in unfamiliar spaces.
What types of SLAM systems are used in robotics?
Several types of SLAM technologies are employed in robotics. The most common are visual SLAM (vSLAM), which utilizes cameras to identify features in images, and LiDAR-based SLAM, which relies on laser scanners to generate point clouds of the environment.
What are some real-world applications of SLAM in robotics?
In warehouse environments, AMRs equipped with SLAM sensors can safely navigate complex layouts. Their movements are monitored via software, and their maps can be edited to improve efficiency.
How can businesses leverage SLAM technology?
AMRs incorporating SLAM are easy to integrate and scale without modifying existing infrastructure. They help optimize workflows and adapt to business growth or seasonal demand peaks.