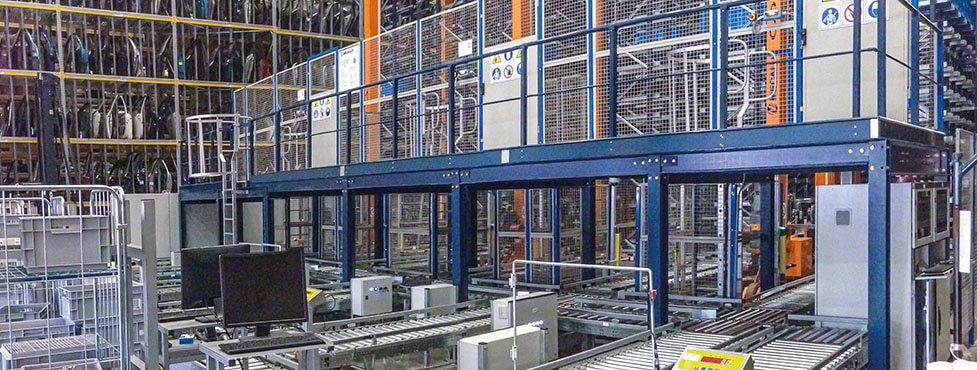
Zbeda Group: nearly 20,000 boxes in only 7,535 ft²
Every day, 500 just-in-time orders are distributed to garages and carmakers in Israel
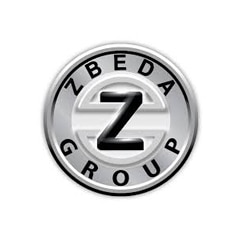
Zbeda Group, Israel's leading automotive components company, has modernized its logistics center in the city of Rosh HaAyin with an automated warehouse for boxes. Occupying merely 5.3% of the installation’s total surface area, this facility provides storage capacity for 19,320 boxes. Picking is the primary operation carried out at this installation. According to orders from Easy WMS, the warehouse management system (WMS) by Interlake Mecalux, 500 just-in-time orders are distributed daily to multiple garages and carmakers all over the country.
Logistics on wheels
Founded in 1965, Zbeda Group is Israel’s top manufacturer and distributor of spare parts for automobiles. The group is a conglomerate of subsidiary companies (Sher, Ferromat, Elrom and Drive, to name a few), each specializing in a specific range of parts.
The automotive industry requires flexible logistics adapted to customer needs. For this reason, car manufacturers are perfectly in tune with companies that supply them with parts (as is the case with Zbeda Group) to ensure just-in-time deliveries without interruption in vehicle production.
In the Israeli city of Rosh HaAyin, Zbeda Group has a 3.21 acre logistics center from which it supplies its customers, primarily garages and carmakers. In the words of Shuly Bushari, the company’s Vice President of Logistics, this center “has to offer maximum storage capacity and, at the same time, have streamlined operations that guarantee speedy goods prep and dispatch.”
Zbeda Group commissioned this logistics center at the end of 2015. Since then, the firm has constantly expanded and remodeled the installation to respond to increased sales.
High throughput in a small space
To manage small parts, such as valves and filters, the firm has installed an automated warehouse for boxes. This solution accommodates a large number of products in a confined space and, in addition, provides the main advantages of automation: “It minimizes errors and reduces the number of goods movements inside the installation,” asserts Shuly Bushari.
Measuring 33' high, the facility comprises three aisles with double-deep racking on both sides. It has a storage capacity of 19,320 boxes in a surface area of merely 7,535 ft². A twin-mast stacker crane incorporating a double-box, double-depth extraction system moves along each aisle and can handle up to four boxes at the same time. In this way, the flow of goods from the automated installation increases considerably, and 730 boxes/hour (365 incoming and 365 outgoing) can be stored and retrieved.
Easy WMS, the warehouse management system (WMS) by Interlake Mecalux, is tasked with directing all the processes in the automated installation and assigning a location to the boxes sent by suppliers. To do so, it takes into account variables such as the characteristics and demand level of each item. Optimal goods distribution not only improves flows, but also enhances the movements of the stacker cranes and conveyors.
Easy WMS is integrated with Zbeda Group’s ERP to manage the facility with the utmost efficiency and leverage all processes carried out. Thanks to fluid communication, Easy WMS knows what orders need to be dispatched and, thus, directs them to be prepared immediately.
Dedicated to order prep
The main operation of this installation is picking. Every day, around 500 orders are dispatched and delivered to multiple garages and manufacturers throughout Israel. According to Zbeda Group’s Vice President of Logistics, the company’s priority is “to make order preparation quicker and less costly.”
Given the importance of picking for its business, Zbeda Group sought a solution that would foster and facilitate the preparation of a greater number of orders in the shortest possible time. The automated warehouse for boxes is ideal for this, as it is designed specifically to boost order prep based on two principles:
- Efficient goods management. Easy WMS knows the status of stock in real time, preventing stockouts and, therefore, any potential interruptions.
- Product-to-person system. With this working method, three stacker cranes and conveyors automatically move the goods needed for each order to the pick stations.
This installation has three stations where operators prepare orders in waves, that is, operators sort the products by order as soon as they extract them from inside the boxes. Each pick station has two carts (with nine locations each, 18 in total) equipped with put-to-light devices that help operators distribute the goods into various orders simultaneously. Once the product is received, the display lights up and shows the number of items the order requires, boosting efficiency and reducing possible errors.
“The incorporation of the automatic equipment and of auxiliary devices has helped make order preparation much faster. Operators barely have to move from their workstations; they merely extract the items from the boxes, sort them, and then pack and wrap them,” explains Shuly Bushari.
Shuly Bushari - Vice President of Logistics at Zbeda Group
“The automated warehouse for boxes is the ideal solution for carrying out storage and picking tasks according to the product-to-person method. The main advantage this system has provided us with is speedy order preparation.”
How are orders picked by wave?
Wave picking is a method of organizing order prep in which multiple orders are put together at the same time. Operators use a cart containing as many slots or boxes as there are orders to be prepared (nine, in the case of Zbeda Group).
The WMS groups the orders according to various logistics criteria, such as delivery route and shipping priority, and assigns a cart to each operator. These workers systematically arrange the products by order while extracting them from the boxes they have received from the automated warehouse.
Once this process has finished, the carts, which contain the already completed and sorted orders, are moved to the consolidation area. All that remains to be done is to check, package and wrap the orders and print the necessary documentation.
The perfect solution for a leading company
Automation has directly affected Zbeda Group’s supply chain productivity. With the automated warehouse for boxes, the company has benefited from the product-to-person principle in terms of cutting costs and increasing speed.
As a result of the just-in-time system, Zbeda Group’s components are perfectly aligned with its supply chain operations. Automation and the WMS have contributed towards optimizing inventory, controlling goods traceability and eliminating errors stemming from manual handling.
In addition, this solution has helped maximize available space to obtain the greatest possible storage capacity: up to 19,320 boxes in merely 5.3% of the logistics center's surface area.
Advantages for Zbeda Group
- Fast order prep: automation and the product-to-person principle help prepare 500 daily orders as quickly as possible.
- Management and integration: Easy WMS, integrated with the automated warehouse for boxes, provides total traceability for 19,320 boxes and directs storage and picking tasks.
- Space optimisation: 19,320 boxes with multiple small items can be stored in just 7,535 ft² (amounting to 5.3% of the logistics center's total surface area).
Automated warehouse for boxes | |
---|---|
Storage capacity: | 19,320 boxes |
Box dimensions: | 14" x 22" |
Max. box weight: | 110 lb |
Racking height: | 33' |
Racking length: | 164' |
Gallery
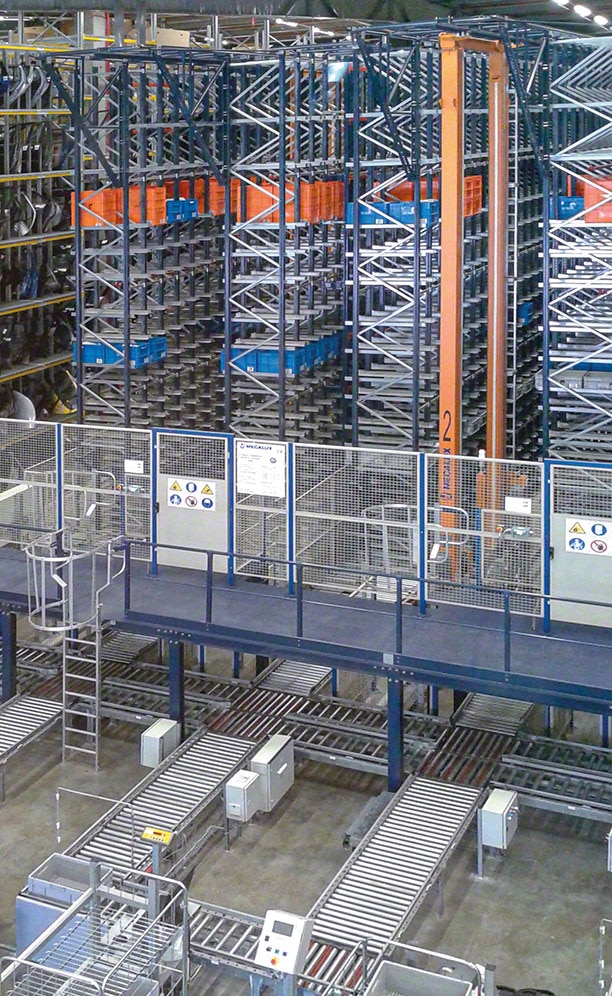
Zbeda's automated warehouses for boxes in Israel
Ask an expert