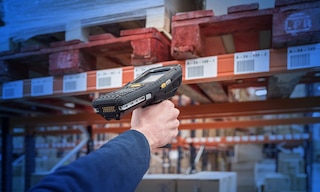
3 examples of inventory in a warehouse
Inventory is a process relating to the list of goods a company stores, reflected in physical or digital format in an orderly, detailed way. To carry it out, it’s necessary to verify that the stock for products stored, as well as their quantities and characteristics, coincide with the data that appears in the business’s records or computer system.
Although there are different types of inventory, they all have the same purpose: to maximize earnings while minimizing storage costs, all while maintaining activity levels and improving customer service.
But, how can you take inventory quickly and effectively? In this post we show you three examples of inventory to help you better understand how the process works: inventory management with Excel, another with inventory software, and a final example in a fully automated smart warehouse.
1. Example of inventory with paper or Excel
Canned vegetable company Organic Canned — a fictitious company — produces and distributes canned goods throughout the country. It has a small warehouse with drive-in pallet racks with capacity for 300 pallets containing finished product. It uses a high-density storage system because it works with few SKUs, six in total: asparagus, artichokes, roasted peppers, tomatoes, peas and green beans.
Every month, the warehouse manager takes advantage of off-peak hours to take inventory manually and check whether the pallets received and dispatched match the total quantities of stock in the facility. To do so, the manager goes around the warehouse with the list of products on paper and counts the number of pallets there are for each SKU. Then, he/she enters the information manually in an Excel table.
If the work is done correctly, the number of pallets per each SKU will be equal to the difference between entries and exits made since the last inventory done with Excel.
The Organic Canned facility began the month with 300 pallets stored and currently has 288 pallets. This is its warehouse inventory, which illustrates the beginning stock for each SKU, as well as the pallet units that have entered and left the facility during the month:
MONTHLY PRODUCT INVENTORY | |||||
---|---|---|---|---|---|
PRODUCT CODE | DESCRIPTION | PREVIOUS MONTH'S STOCK | ENTRIES | EXITS | STOCK |
001 | Asparagus | 85 | 19 | 28 | 76 |
002 | Artichokes | 80 | 31 | 39 | 72 |
003 | Roasted peppers | 55 | 16 | 14 | 57 |
004 | Tomatoes | 40 | 9 | 12 | 37 |
005 | Peas | 20 | 11 | 6 | 25 |
006 | Green beans | 20 | 7 | 6 | 21 |
TOTAL | 300 | 93 | 105 | 288 |
Taking inventory on paper is the most basic way of carrying out the processes. It’s only viable in companies with very low stock levels and limited inbound and outbound activity, as in the case of Organic Canned. If the volume of work of these firms grows, they should turn to digitization to avoid errors and speed up their operations.
2. Example of inventory with specialized software
After a major increase in sales, Organic Canned has expanded its warehouse to house a larger number of finished products. More specifically, it has a warehouse with capacity for 4,000 pallets where it continues to manage the same SKUs but now does so with the Pallet Shuttle system. This storage method, which, likewise, is compact, expedites movements, as an automatic shuttle moves the pallets inside the racking.
To carry out inventory, the company is equipped with inventory software, such as Easy WMS, a warehouse management system created to facilitate companies’ goods management. Integrated with the business’s ERP, the program automates product shipping and receiving carried out in the facility.
Before starting the inventory, it’s necessary to enter information relating to all the products with which Organic Canned works into the WMS: description, unit of measure, attributes, image, weight, etc. With all the data on the items incorporated into the database, the program generates a label for each item, which is adhered to the stock present in the facility.
To streamline the entire process, the warehouse operators use RF scanners to read the barcodes and register each item entering the facility into the system. The same is done with each dispatch. This way, each receipt and shipment of goods is recorded in the system.
Additionally, from time to time, (at least once a year), it’s advisable to conduct a physical inventory, which consists of traveling around the warehouse and counting the SKUs one by one. This contrasts the actual SKUs in the facility with those recorded in the book inventory (managed by the WMS).
With a WMS such as Easy WMS, the logistics manager has a perpetual inventory system (with stock updated in real time). The manager can use this to consult the stock on hand, its exact location, the type of container in which it’s stored, etc.
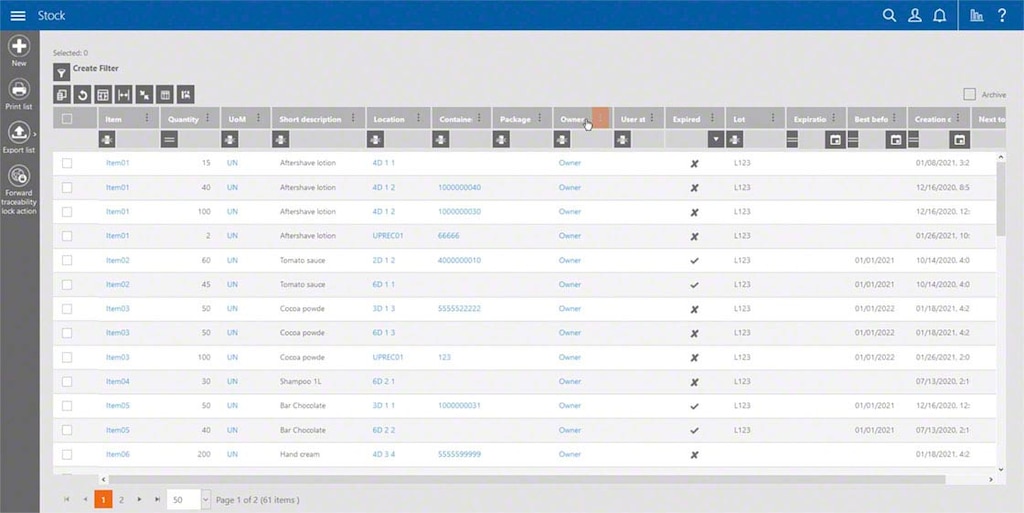
3. Example of inventory in a fully automated warehouse
In line with its expansion plan, Organic Canned has completely automated its logistics operations. Its facility suddenly became too small when the production pace increased. As a result, it built an automated clad-rack warehouse with capacity for 30,000 pallets managed by Easy WMS.
Taking inventory is practically identical to when a non-automated storage system was employed; the only difference is that, now, operators no longer have to read the barcodes on the goods manually. How is this possible? Thanks to a pallet checkpoint, responsible for checking the condition of the pallets, reading the barcode of each product, and sending the data to the WMS (which, in turn, dumps them in the ERP database).
Every time an item enters or leaves the facility via the pallet conveyors, the system records a change in the number of units available in stock: the quantity that enters and the final stock, or the quantities that leave and the remaining stock. Consequently, the company has full product traceability in its automated warehouse. This increases product safety, improves risk control, and guarantees the quality of the products and processes. The high degree of automation provides Organic Canned with perpetual inventory, whereby stock is updated in real time.
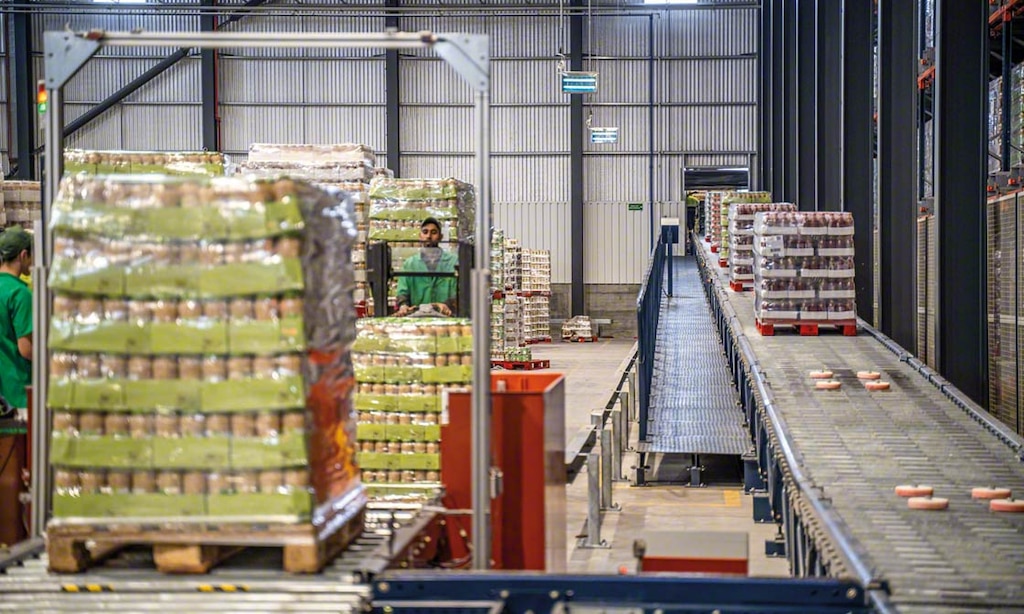
WMS, the perfect ally for your inventory
Inventory management is one of the key pillars of the supply chain. Calculating the number of items a company should have in stock ensures smoother operations and prevents interruptions and delays.
Easy WMS from Interlake Mecalux is software that will enable you to have a perpetual inventory system, with your stock updated in real time. Plus, it features different modules, for example, Store Fulfillment, which syncs the stock in your warehouse with that in your stores. Thus, the inventory is linked to sales records in that each time a product is sold, the system removes it from stock. Feel free to get in touch. We’ll walk you through the features of this software and show you how it can help you control your inventory in real time.