
Case Studies
See some of the projects undertaken by Interlake Mecalux, how we met our customers’ needs and the unique solution adopted in each facility. Whatever your product is, we will find a suitable solution to store it, transport it, and even streamline its management within the warehouse.


Manitou prepares 500 order lines per hour at its warehouse in France

Viñas Familia Gil manages the production of up to 700 SKUs of wine with Easy WMS

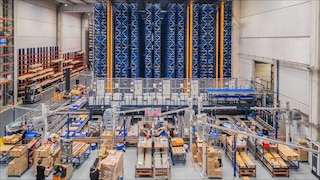
Hispanox fills 1,800 order lines a day in 3 warehouses

Surplus Motos recycles 10,000 motorcycles a year with Easy WMS in its new automated warehouse

Jim Sports digitizes its warehouse with a comprehensive logistics solution from Mecalux

Moderna products’ cutting-edge automated warehouse – Logistics redefined


A manual warehouse is automated without disrupting operations

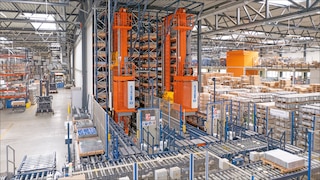
Blechwarenfabrik Limburg opts for Industry 4.0 in its new warehouse

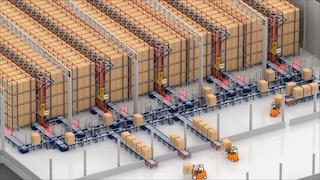
British Sugar: automated systems to meet future supply chain challenges

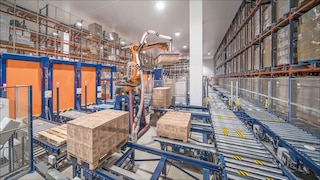
HAVI's three-temperature food storage system

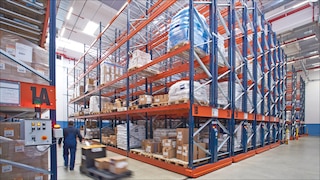
Vibar Nord: robotics and digitization

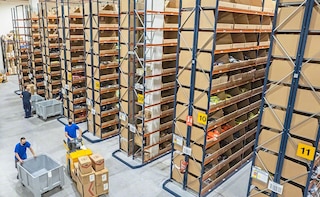
Würth Modyf adapts its logistics to omnichannel with the Easy WMS warehouse management system

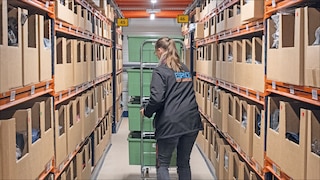
Remote installation of Easy WMS

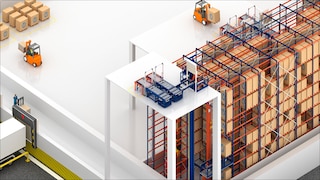
Natura Bissé: A tailor-made automated warehouse


FIC: an integrated logistics solution with automatic and manual systems

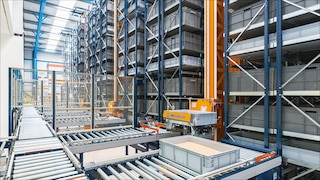
Normagrup: automation shines a light on logistics

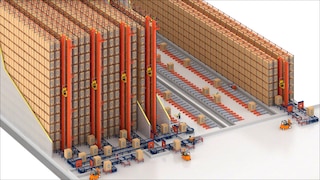
Copacol: automation and digitization

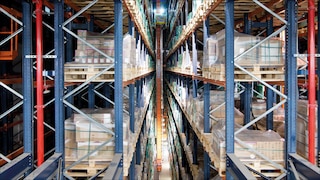
Ceramika Paradyż: High capacity and picking speeds in its automated rack-supported warehouse

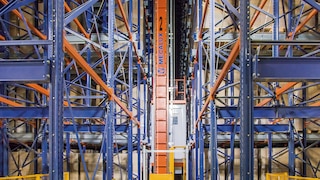
A smart warehouse for Bem Brasil

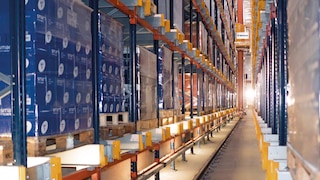
Clairefontaine: High productivity in automated warehouses

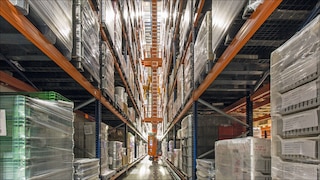
When refrigeration meets automation: a perfect warehouse match for Schaal Chocolatier

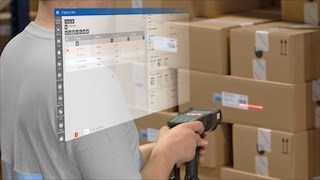
Omnichannel solution for Danone's logistics operations

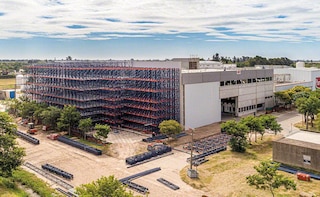
La Piamontesa upgrades its new automated warehouse in Argentina

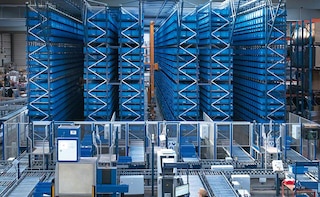
Sam Outillage: A high-throughput warehouse


Finieco has revamped its logistics systems with the start-up of a new automated warehouse in Portugal

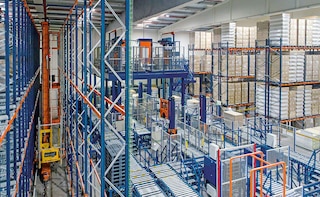
Automation of Maverick Laboratories' logistics centre

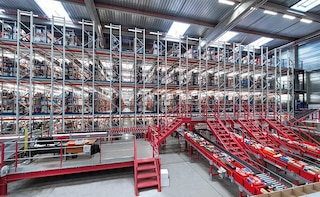
A large picking warehouse to manage online shoes sales

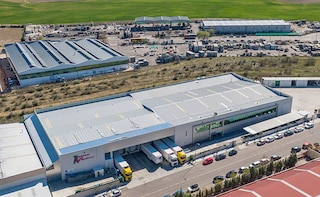
The fully-automated frozen-storage installation of Cárnicas Chamberí


The new Grégoire-Besson distribution centre guarantees fast, accurate order preparation

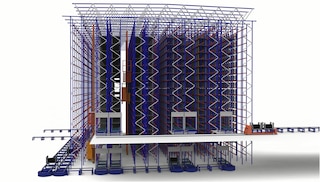
Mecalux delivers a turnkey installation to the highest producing Michelin tire plants in Europe

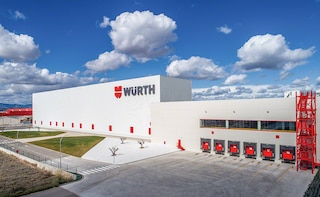
Würth expands its storage capacity with a Mecalux “turnkey” project

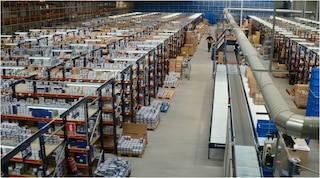
Logistics remodeling of Cofan Center to reduce operating costs

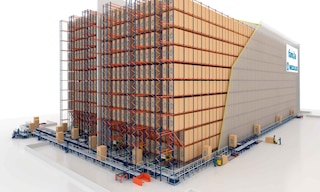
Grupo Familia warehouse can accommodate 19,000 pallets and workflows of 140 combined cycles per hour.

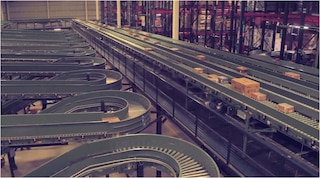
DECASA: High throughput picking and storage

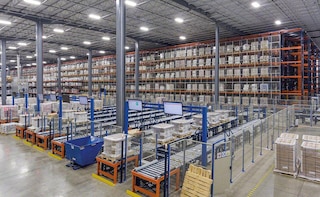
Charter Next Generation is continuously improving their people, processes, and product

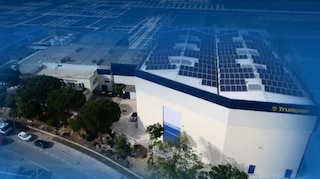
Trumpler, a warehouse where capacity and control are a priority, with streamlined runtimes and lower costs

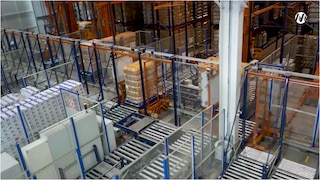
Salvesen controlled temperature logistics center

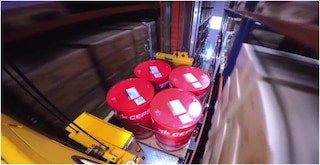
Mecalux has build an automated clad-rack warehouse with over 49,000 ft2 for Cepsa

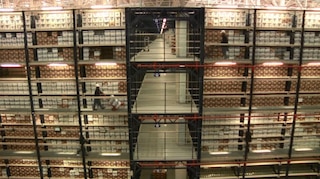
Mecalux builds earthquake-proof warehouses for Iron Mountain Chile

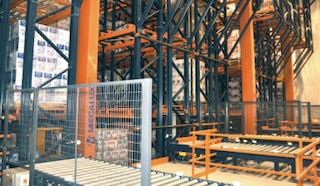
Mecalux installs its latest warehouse technology for the Idaho State Liquor Dispensary

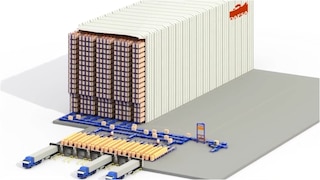
Mecalux builds a spectacular automated rack supported warehouse ready for the future

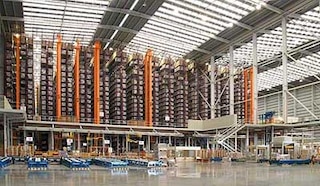
The Porcelanosa Group entrusts Mecalux with the completion of their logistics complex

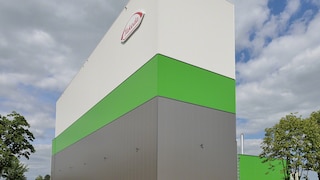
Step-by-step view of the installation of a clad-rack warehouse

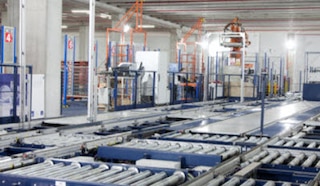
Mecalux centralizes logistics at Nupik International

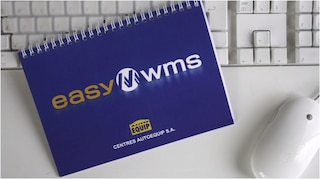
How do you ensure error-free management of 6,000 different references from the automotive industry?

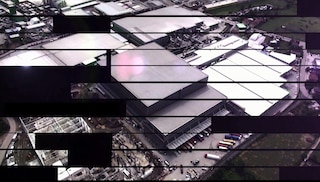
Mecalux builds one of the tallest logistics centers in Europe

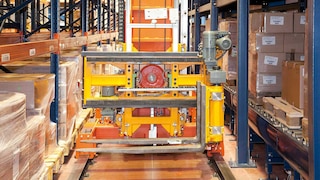
Mecalux keeps the logistics operator Disalfarm in action

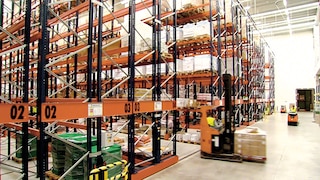
Havi Logistics finds the Movirack system to be the perfect solution to increase their capacity

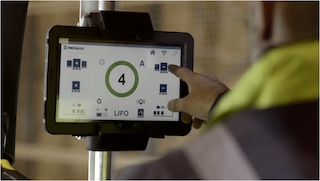
Mecalux helped Didactic take a step forward with the Pallet Shuttle System
Ask an expert