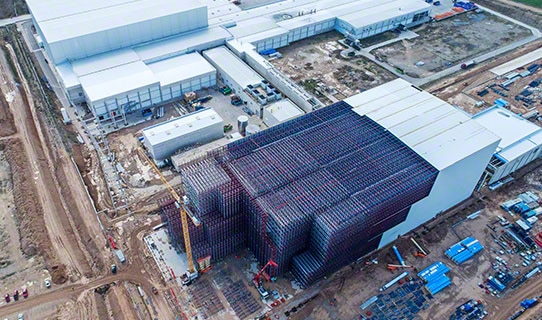
Ceramika Paradyż: High capacity and picking speeds in its automated rack-supported warehouse
Mecalux has designed Ceramika Paradyż an automated rack-supported warehouse with a capacity for more than 20,200 pallets in Poland
Mecalux has designed Ceramika Paradyż an automated rack-supported warehouse with a capacity for more than 20,200 pallets in Poland