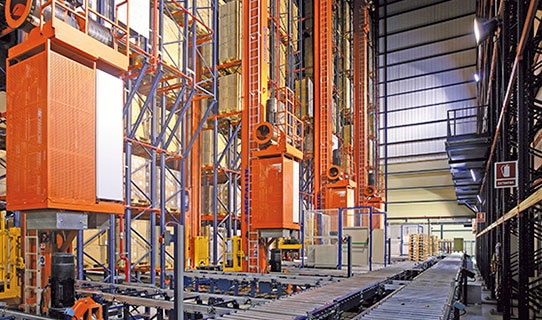
The Porcelanosa Group entrusts Mecalux with the completion of their logistics complex
With the addition of this automated warehouse to Porcelanosa’s logistics complex, Mecalux completes one of the most advanced logistics infrastructures in the ceramic industry.