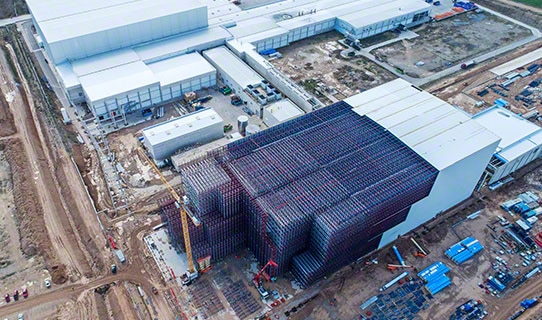
DECASA: High throughput picking and storage
A cutting-edge logistics complex, which combines management, efficiency and speed in its processes. It is noted for a high picking throughput, an essential solution for a company that manages more than 7,000 products.