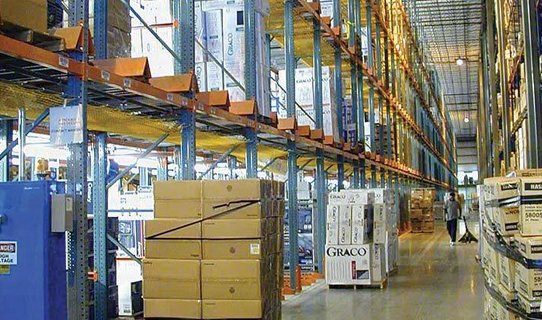
Mecalux builds one of the tallest logistics centers in Europe
The new logistics center for Hayat Kimya, in Turkey, with a capacity of 161,000 pallets has become a global benchmark in automated clad-rack warehouses. The colossal facility, 150 feet high, has allowed this leader in the chemical sector to tackle the centralization logistics and production processes.