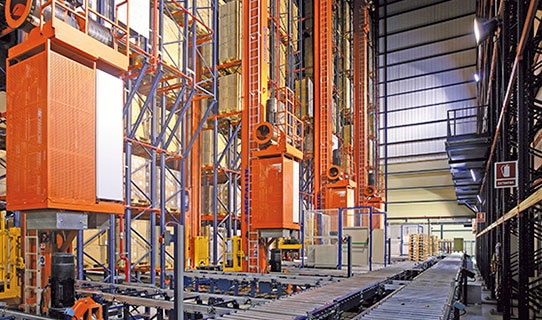
British Sugar: automated systems to meet future supply chain challenges
British Sugar has consolidated its logistics processes thanks to the speed and efficiency of its new warehouse at the Wissington refinery.
British Sugar has consolidated its logistics processes thanks to the speed and efficiency of its new warehouse at the Wissington refinery.