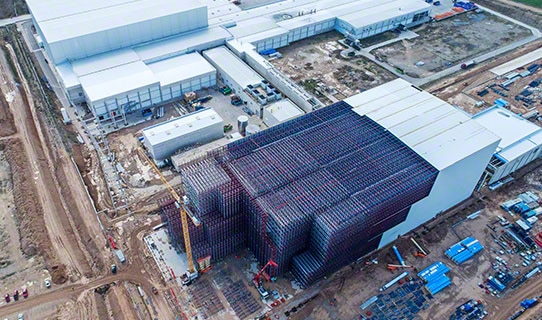
Mecalux has build an automated clad-rack warehouse with over 49,000 ft2 for Cepsa
The new automated warehouse is one of the largest investments made by Cepsa’s lubricants business
The new automated warehouse is one of the largest investments made by Cepsa’s lubricants business