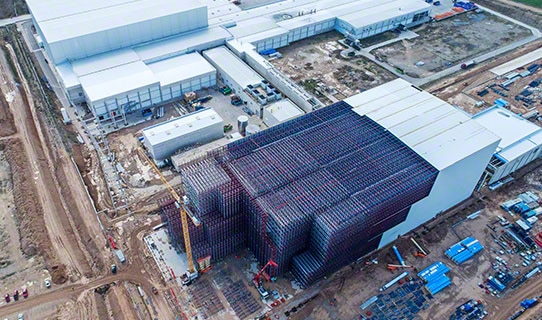
A smart warehouse for Bem Brasil
Bem Brasil has built an 82' high automated rack-supported warehouse with a capacity for more than 33,000 pallets
Bem Brasil has built an 82' high automated rack-supported warehouse with a capacity for more than 33,000 pallets