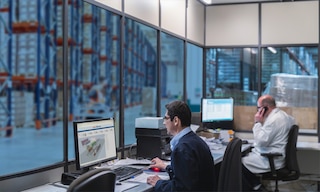
The logistics department: Functions and responsibilities
The logistics department has evolved from playing a purely operational role to becoming a key strategic differentiator. For companies involved in manufacturing or distribution — especially those with e-commerce sales — efficient logistics management is the cornerstone of both profitability and customer satisfaction. Therefore, it’s essential to have a solid grasp of its ins and outs, streamline its internal organization, and master its various functions.
What is a logistics department?
A logistics department is the company division charged with ensuring that goods and services reach customers or production lines as efficiently as possible and at the expected time. Its responsibilities range from sourcing raw materials to distributing and delivering finished products to businesses and/or individual customers.
Functions of the logistics department
To achieve the goals of logistics — namely, guaranteeing a smooth and efficient flow of goods in procurement and distribution — this department takes on multiple roles. Leveraging a warehouse management system like Interlake Mecalux’s Easy WMS greatly improves the performance of these logistics processes.
Supply and procurement management
Procurement in logistics plays a crucial role in making sure companies have the right merchandise on hand at the right time. The logistics department is tasked with managing product availability in the warehouse and streamlining goods receipt, storage, and shipping.
Inventory control
Logistics managers and their teams are also responsible for managing merchandise in the facility. They must monitor inventory accurately to avoid overstock as well as stockouts. This not only keeps costs down but also leads to customer satisfaction, as goods will be available when needed.
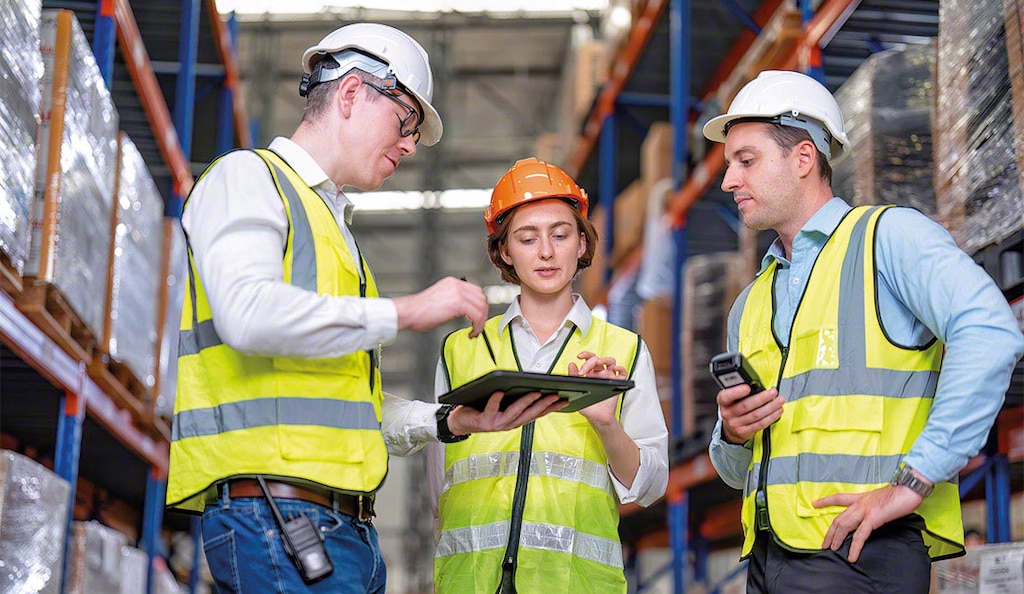
Order fulfillment and shipping
The logistics department ensures products are delivered on time and to the agreed location through a comprehensive management approach. This covers everything from receiving and validating orders to coordinating the employees in the warehouse organizational chart to achieve accurate picking and packing. The logistics department then oversees the shipping process by selecting carriers, generating the necessary documentation, and tracking the goods sent. This end-to-end workflow also includes resolving potential issues and efficiently handling returns. The ultimate goal is to meet deadlines and guarantee customer satisfaction through careful planning, coordination, and execution.
Cost optimization
By thoroughly analyzing supply chain activities, the logistics department can implement changes aimed at reducing operational expenses without compromising service quality.
Planning and data analysis
Well-structured logistics planning at every stage fosters smooth supply chain operations. When procurement, manufacturing, storage, and distribution are coordinated, overall efficiency improves. Capturing historical data through warehouse management software helps lay the groundwork for these plans. For example, Easy WMS’s Supply Chain Analytics functionality segments, processes, and structures the thousands of data points generated daily in a facility, transforming them into valuable insights for decision-making.
Distribution and transportation
Streamlining the handoff of goods to carriers speeds up shipping times and positively impacts customer satisfaction — especially during the critical last mile. The logistics department optimizes this process, often implementing solutions such as Multi-Carrier Shipping Software. This Easy WMS module efficiently organizes packaging, labeling, and shipping to each transportation company. Additionally, it generates tracking codes that allow full visibility of an order’s journey to its final destination. The result is efficient distribution and last-mile transparency.
Supplier and quality management
The logistics department is also tasked with maintaining strong relationships with suppliers to guarantee a steady flow of goods delivered on time and in the right condition. The warehouse manager must verify that suppliers are meeting their delivery commitments and that products arrive with the expected level of quality.
Continuous improvement and innovation
Beyond overseeing the daily movement of goods, an efficient logistics department regularly assesses its operations to identify opportunities for improvement and increased productivity. Investing in the latest intralogistics and warehouse software and technologies provides a competitive edge and drives long-term efficiency.
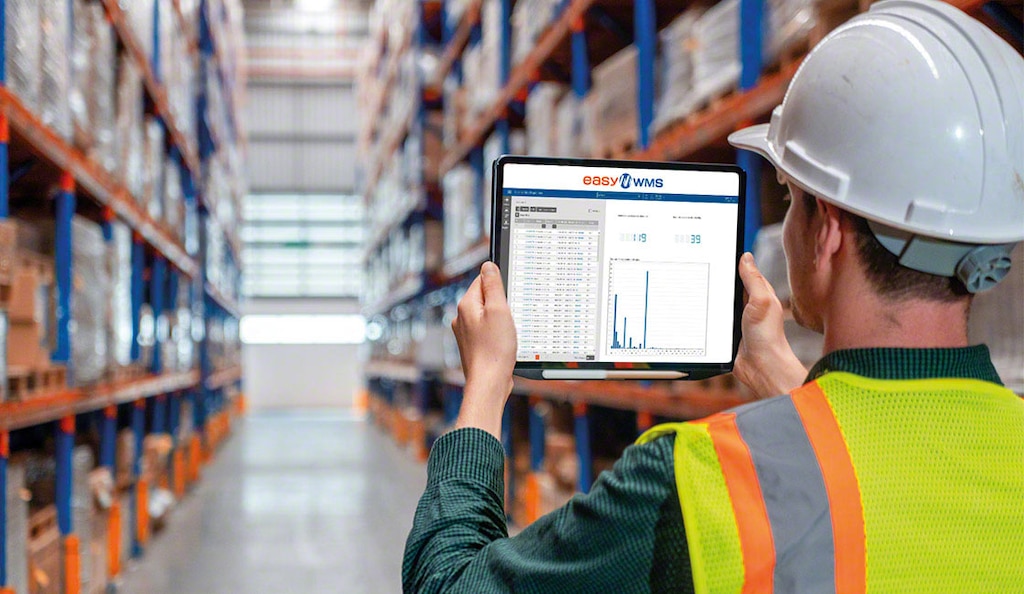
Logistics department structure
The logistics department typically follows a hierarchical structure, with a logistics manager at the top. Depending on the company’s size, there may be team leaders overseeing specific areas, who in turn supervise analysts, specialists, and operators who carry out specific tasks.
However, there’s no one-size-fits-all organizational model. The ideal structure is the one that enables the business to meet its goals by making the most of its current and future human and material resources. An efficient warehouse organizational chart should clearly define each role, outline job responsibilities within the logistics department, logically group positions, and establish both hierarchical and functional reporting lines.
Digital transformation of the logistics department
When companies have the tools to track inventory levels and locations in real time, their logistics departments can drive the business to the next level. Here are some examples of organizations that have overhauled their logistics operations with Mecalux solutions:
- Multi-warehouse management. Spanish photovoltaic material distributor SumSol has achieved seamless communication between its logistics centers in Seville and Madrid. “Multi-warehouse management helps us tremendously on a logistics level: if a product is missing in one center, the software immediately recognizes its availability in the other,” says Tomás Sieteiglesias, Logistics Department Manager.
- Digital delivery notes. Slovenian glassware specialist Steklarna Rogaška uses Easy WMS to assign ready orders to designated carriers for shipment to end customers. “Having the system automatically generate the delivery note has saved us significant time and costs,” says Gregor Vaukan, head of the company’s logistics department.
- Food traceability. Dry food distributor Masgrau Alimentació needed to broaden its SKU base, prompting the logistics department to implement a warehouse management system. “Easy WMS has given us tighter control over processes in our facility: inventory status, expiration dates, lots, staff fulfilling orders, and other aspects,” says Logistics Department Manager Alex Masgrau.
Empower your logistics department
The department of logistics management is instrumental to supply chain optimization. Supported by advanced technologies, it can streamline operations and respond quickly to customer demands. If you’re looking for a warehouse management system to boost your company’s efficiency, Interlake Mecalux has the solution. Get in touch — we’ll help you bolster your supply chain, cut costs, and strengthen your market position.