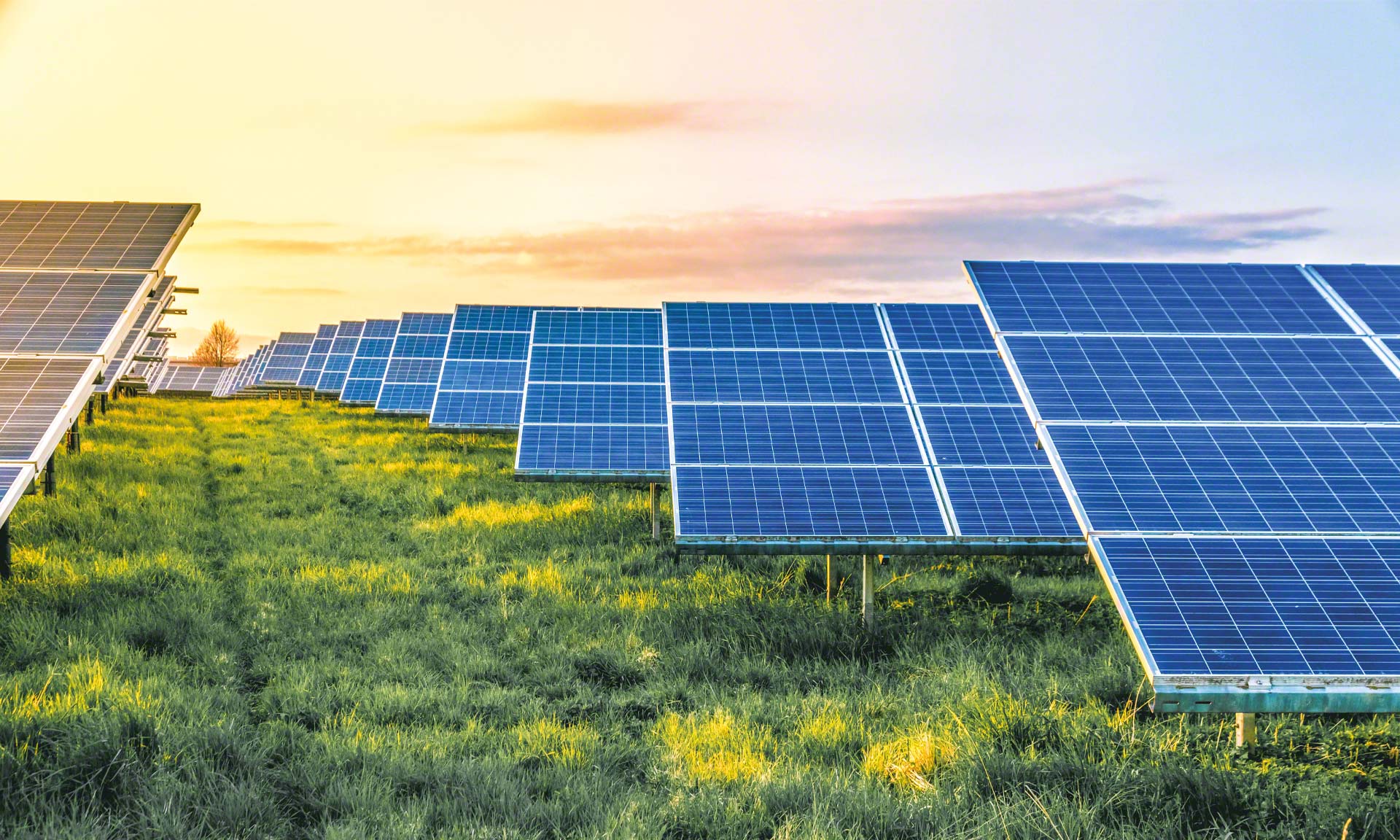
SumSol manages 3,000 SKUs across 2 warehouses
SumSol, a distributor of photovoltaic materials, combines the supervision of its Madrid and Seville warehouses with Mecalux’s Easy WMS.
SumSol, a pioneer in the distribution of photovoltaic materials in Spain, has equipped its logistics facility with Mecalux’s Easy WMS software. With the system in the SaaS model, SumSol ensures product traceability and monitors the status of its stock in real time.
SumSol: solar energy experts
SumSol is a pioneer in the distribution of photovoltaic material in Spain. Based in Madrid and with a branch office in Seville, the company works closely with the most prestigious brands in the market. With a clear commitment to customer service and support, SumSol aims to offer the best solution for each particular case and ensure the correct operation of the equipment it supplies. The business’s top priority is customer satisfaction. It strives to understand the needs of its clients and meet their product and service expectations. Founded in 1999, the company has a storage area spanning 1.48 acres.
CHALLENGES
|
SOLUTION
|
BENEFITS
|
---|
Multi-location inventory management involves overseeing and organizing stock and operations in different logistics facilities in a unified manner. SumSol, a Spanish distributor of photovoltaic materials, has a warehouse in Seville and another in Madrid. From these locations, it supplies photovoltaic products from leading manufacturers in the energy sector to approximately 3,000 customers anywhere in Spain.
The company, which tripled its revenue in 2022, is aware that logistics — and particularly, communication between its two facilities — is crucial for achieving success. So, how did SumSol manage to ensure seamless communication between its two logistics centers? With Mecalux’s Easy WMS warehouse management system in the software-as-a-service (SaaS) model.
The SaaS version employs cloud computing technology, allowing users to access the software functionalities from any device with internet access. It provides real-time inventory visibility and complete traceability of SumSol’s 3,000 SKUs. “Easy WMS controls both facilities, in Seville and Madrid, in an integrated, simultaneous way. With regard to logistics, multi-warehouse management helps us tremendously: if a product is missing in one center, the software immediately recognizes its availability in the other. Additionally, certain user profiles can operate as if they were in the other facility even if they’re not physically present,” says Logistics Manager Tomás Sieteiglesias.
The logistics operations of a company like SumSol are characterized by order personalization in line with customer needs. “That means we have to adapt to the requirements of each client in terms of the product, quantity, packaging type, and delivery method. We offer the option to pick orders up at our counters, send them to an address, and even deliver them directly to worksites to make sure projects are completed on time,” says Sieteiglesias.
Previously, all SumSol warehouse operations were manual, from goods storage and distribution to order processing. Operators relied solely on an ERP system. “We have ERP software for administrative and facility monitoring purposes, but it’s not enough. It lacks the capacity to manage locations and real-time SKU status,” says Sieteiglesias.
Processes under control
SumSol has deployed Mecalux’s Easy WMS in its two logistics centers with specific objectives: to organize and optimize products and operations, shorten operational times, and eliminate errors. The software plays a role in all processes taking place in both warehouses, from receiving photovoltaic materials sent by suppliers to shipping orders to customers.
“Once the goods arrive and we enter them into the system, we have a record of their location at any point in the logistics process. We can locate any item, whether it’s in an inbound buffer, in transit, or being used to fulfill an order. Easy WMS provides total traceability,” says Óscar Jiménez, Warehouse Manager at SumSol’s Madrid center.
Sieteiglesias says: “Another reason we decided to install Easy WMS was to facilitate the work of operators and establish processes for performing each operation. This takes the burden off our employees; to fill orders without making mistakes, they simply follow instructions from the software. Now, the working method in our Seville and Madrid warehouses is the same, regardless of product volume or order quantity.”
We’re thrilled with Easy WMS. It monitors the 3,000 SKUs stocked across our Madrid and Seville facilities in an integrated, simultaneous way.
Operational optimization
“Easy WMS manages all logistics operations in both centers. These include the distribution of locations and order picking, which we’ve streamlined,” says Sieteiglesias.
The system identifies all items, from their arrival at the facility to their shipment to clients. By tracing the movement of each product, SumSol has significantly decreased the number of errors made and can guarantee that its end customers receive top-quality orders. Easy WMS has also been integrated with SumSol’s ERP system to maintain tight inventory control. The logistics software informs the ERP of the stock required so that it can arrange for replenishment. This prevents stockouts and thus delays.
“Easy WMS stores goods by SKU type and turnover rate,” says Jiménez. The Mecalux software optimizes operator travel and expedites putaway and order picking tasks. “Of all the benefits we’ve obtained, I’d highlight the organization Easy WMS has provided us with. Ultimately, if you don’t have a system offering the traceability you need or efficient stock management, maintaining an organized warehouse will be a challenge,” says Jiménez.
The proper distribution of items directly impacts order picking: operators are quicker when locating SKUs to be sent to production or end-customers. “Easy WMS has also enhanced order processing, especially when it comes to speed and reliability,” says Jiménez. Operators merely go to the location indicated by the software instead of traveling around the facility in search of the required merchandise. Digitalization was instrumental in reducing mistakes stemming from manual order picking: “Thanks to Easy WMS, we’ve minimized the number of errors and improved customer satisfaction,” says Jiménez.
Logistics in growth mode
With Easy WMS, SumSol is equipped with a digital tool that will support it in implementing its plans for expansion. One of the advantages of cloud technology is its ability for multi-location inventory management. In other words, the software is designed to supervise any new warehouses the company opens in the coming years.
“We constantly refine our business and logistics processes. In the short term, we intend to open more branch offices and expand within the national market. Being equipped with scalable software that allows us to consolidate all our logistics processes into a single program is key for successfully achieving this growth,” says Sieteiglesias.
Of all the benefits we’ve obtained, I’d highlight the organization Easy WMS has provided us with. If you don’t have a system offering the traceability you need or efficient stock management, maintaining an organized warehouse will be a challenge.
Ask an expert