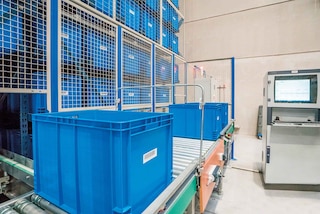
Bullwhip effect: whip it for good!
The bullwhip effect, as per its logistics definition, is an anomaly caused by inaccurate demand forecasts made by each member of the supply chain as a result of fluctuations in order volumes.
This effect is produced because, instead of having the end-customer demand as a reference point, the supply chain participants take as an indicator the demand communicated to them by an entity further down the supply chain (demand affected, for example, by safety stock or special orders). This causes increased procurement, which translates into inventory imbalances.
When does the bullwhip effect occur? Consequences
According to this concept, demand perception becomes distorted as you move further away from the end consumer. Let’s break this down with an example. The demand for product X is 100 units per day. However, there comes a day when customers request 200 units of product X. Under the bullwhip effect, the supply chain would react in the following way:
- At a store or business, there’s a demand for 100 units of product X. The store normally stocks 200 units: 100 to cover normal demand and 100 to be used as safety stock. At a certain point, demand increases by 100 units (to a total demand of 200 units). To serve its customers, the store dips into its safety stock. Thus, the next order it places to the distributor will be 300 units: 200 to cover the new demand and 100 to compensate for the safety stock used exceptionally.
- The retail outlet’s order of 300 units is sent to the distributor, which, because of the increase, also uses part of its warehouse inventory to cover that extra demand (200 more units compared to the usual 100). The distributor is under the impression that demand has risen to 300 units and will place an order to the manufacturer for 400 units (adding 100 more to supply its own safety stock).
- The manufacturer will draw upon its own safety stock to satisfy this demand of 400 units. However, it will begin to produce larger batches, thinking that consumption of its products has skyrocketed.
Each link in the supply chain is increasing the difference between real and perceived demand. In this example, the failure to take into account each member’s safety stock as part of that demand resulted in the proliferation of imbalances along the supply chain, causing:
- Increased inventory investments, due to both storage and logistics costs, that aren’t really necessary.
- Ironically, these irregularities can also lead to stockouts. This happens especially when attempting to mitigate the bullwhip effect after you realize you’ve overstocked your inventory. It can also occur when a reverse bullwhip effect has been produced because of negative fluctuation.
- The distortion can prompt the manufacturer to increase production, which will become inefficient by foisting product onto the market that far exceeds actual demand. In addition, this could cause prices to drop, as the overstock needs to be eliminated.
The image below illustrates the fluctuations associated with the bullwhip effect:
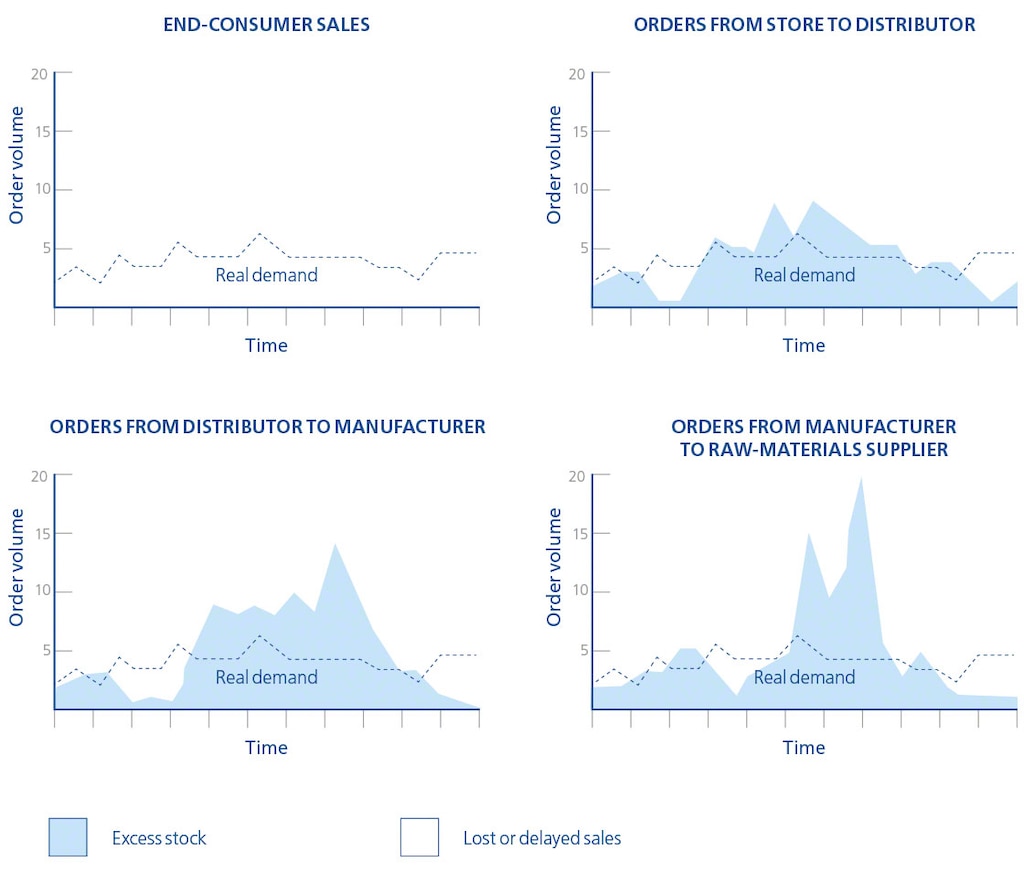
Causes of the bullwhip effect in logistics
The origin of the bullwhip effect in logistics goes back to problems each member of the supply chain is faced with when determining real demand for their products. This lack of clarity causes companies to allocate resources to procure stock based on distorted or poorly contextualized data.
The perfect breeding ground for the bullwhip effect is usually created by:
- Lack of strategic vision in supply chain planning.
- Lack of processes, tools, and information systems to strengthen collaboration between members.
- Difficulty in maintaining internal and external information flows due to the company’s corporate culture and employee training.
Before going over strategies to curb the bullwhip effect in logistics, remember: this is a problem that needs to be dealt with in a comprehensive and sustained manner over time.
Tips for mitigating the bullwhip effect in logistics
The solution for the bullwhip effect lies in improving your sales forecast accuracy. Let’s take a look at some good practices that can be applied to limit the bullwhip effect in logistics:
1. Implement the information systems needed to streamline logistics planning
Integrating various types of software in logistics operations lets you configure a cross-cutting IT system that improves data visibility and adjust sales forecasts for all supply chain stakeholders. With the complexity of the omnichannel logistics environment, more and more solutions are being developed to make data exchanges in logistics seamless.
For example, the installation of warehouse management system enhances the stock control carried out by an ERP (Enterprise Resource Planning) system. Similarly, it’s possible to add functionalities to monitor products in physical stores and record variations in real demand for each one. In the case of Interlake Mecalux’s Easy WMS ecosystem, this is performed by the Store Fulfillment module, which communicates directly with the WMS operating in the installation.
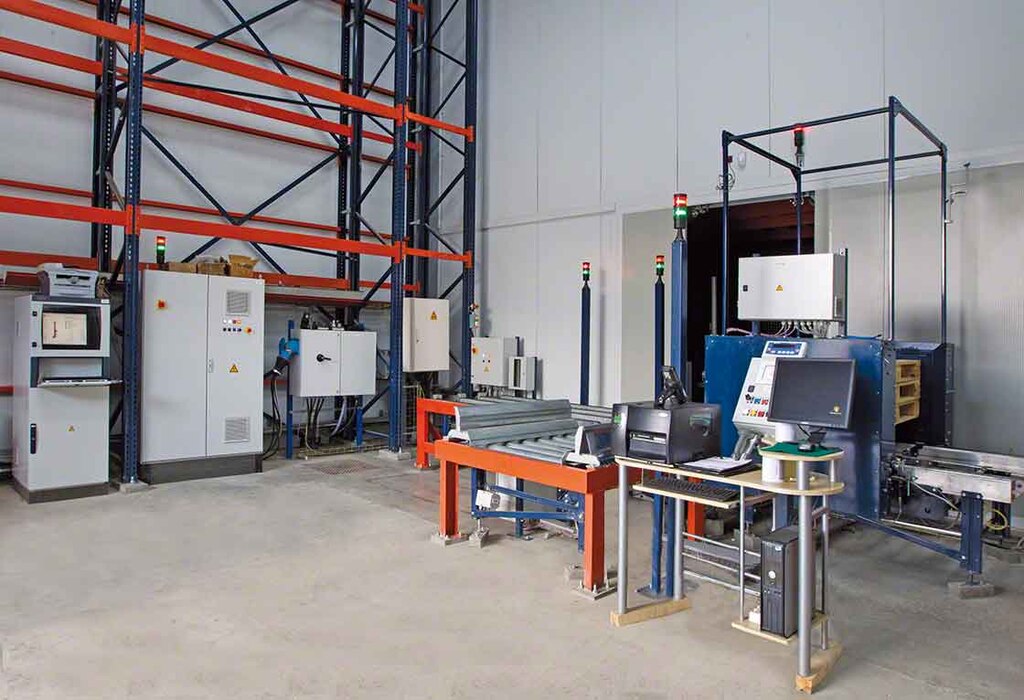
2. Make your internal team aware that their collaboration is crucial for reducing the bullwhip effect
Although tools and information systems pave the way, the truth is that the road will be bumpy if each area of the company operates independently from the rest. Working in a compartmentalized way in which each team guards its own data is a mistake. The commercial area should be a channel for sales information, not an obstacle that withholds it.
Planning that focuses on consumers rather than purchasers is extremely beneficial for the company as a whole. After all, consumers are the end customers who are going to use the product.
For instance, for a retail business, the consumer and purchaser are the same. However, as we move upstream along the supply chain, this is not the case: for the manufacturer, the purchaser is the distributor, and this is not the person who will be using the product. Gearing the strategy towards end-consumer demand is fundamental for limiting the bullwhip effect, since these data aren’t altered by added safety stock.
3. Ensure close coordination between supply-chain stakeholders
In our article on Lean logistics, we examined the disadvantages of overstocking: it’s one of the main drawbacks to operational efficiency.
Coordination between the various links in the supply chain becomes more important than ever for thwarting the bullwhip effect and, above all, preventing it from happening. To do that, it’s advisable to:
1. When selecting suppliers, add as a criterion the requirement to share this information, and establish the necessary legal framework to enter into this type of agreement. Your suppliers should be willing to adopt a common supply chain management strategy that leverages synergies.
2. Make sure your own data are reliable: in this vein, the Supply Chain Analytics Software module is extremely helpful, as it keeps a log of all stock movements.
3. Create processes and design teams to control incoming information: despite the fact that it’s possible to set up alerts via the WMS that inform you about any unusual deviations, it’s advisable for the team to review and monitor the proper functioning of the processes.
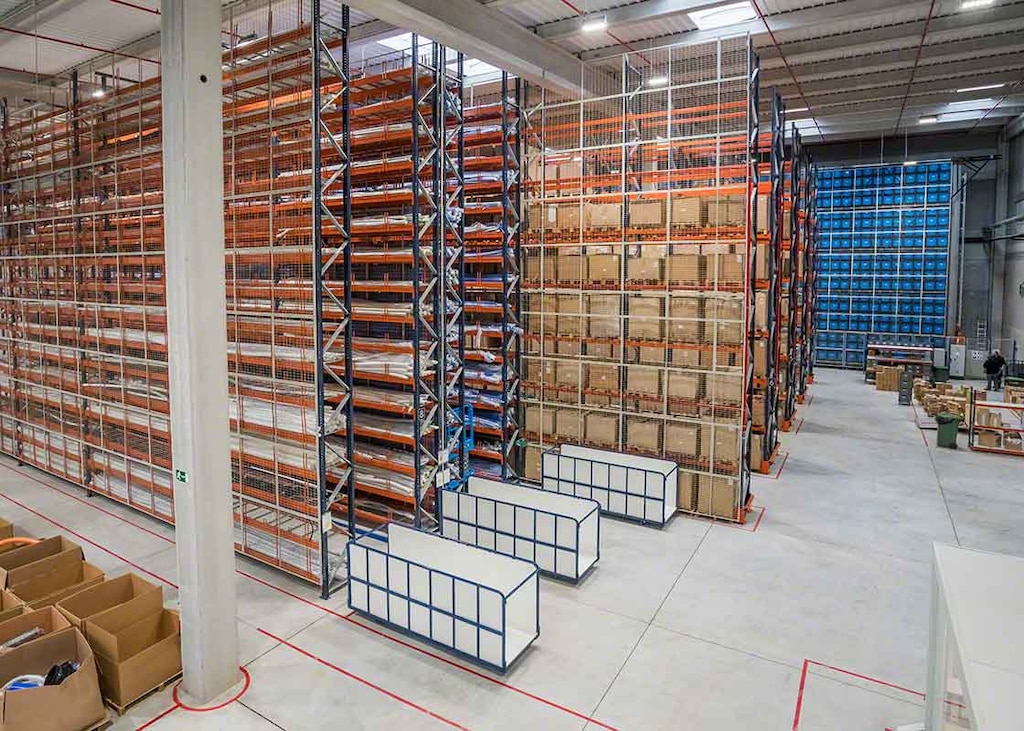
The role of the warehouse in combating the bullwhip effect
The installation can also be subject to additional pressure as a result of the bullwhip effect. In fact, its storage space could become compromised as a consequence of a disproportionate rise in inventory, thus, complicating its management.
Thanks to tools such as warehouse management systems it’s possible to:
1. Employ an adaptive rather than a reactive working method in the warehouse
With an adaptive approach, the installation is prepared to deal with changes effectively because you can rely on prior experience and devise a response based on the information contained in the software. The reactive approach, on the other hand, lacks this previous knowledge and operates on the fly to try to resolve the unforeseen event, generating a less optimal response.
2. Facilitate interconnection between all supply chain stakeholders
Various Easy WMS modules can achieve this task, namely:
- WMS for e-commerce: adapts ways of working in the installation to online stores’ requirements to better meet demand expectations. Features include few units per order, minimum shipping times, updated order status, and goods traceability.
- Multi Carrier Shipping Software: streamlines work with the main transportation agencies, integrating their coding and labeling systems.
- WMS for Manufacturing: coordinates procurement with raw material suppliers, enabling real-time visibility of stock, semi-finished goods, and finished products.
Bullwhip effect: rid your logistics and supply chain management of this anomaly with our WMS
WMSs open up vast opportunities for improving processes not only in the warehouse, but throughout the supply chain. To see how the various modules and functionalities can help limit the bullwhip effect in your supply chain, get in touch. We’ll provide you with a personalized demo.