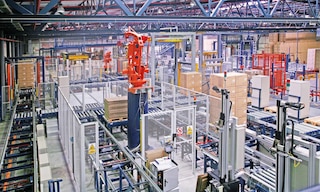
25 tips for optimizing safety in your warehouse
Following a series of warehouse safety tips is key for ensuring the physical integrity of the operators, the preservation of the goods stored, and the proper operation of the storage and transportation systems.
Keeping these recommendations in mind not only fosters a safe environment, but also boosts warehouse productivity: it guarantees optimal operating conditions for carrying out the various tasks.
The following are the main hazards associated with logistics activity:
- Fall of goods from the racks due to poor stacking of the stored loads, impacts against the racking structure, etc.
- Accidents such as falls, slips, blows, cuts, entrapment, or collisions resulting from movement through the warehouse or the operation of machines, tools, or handling equipment.
- Fires caused by the uncontrolled combustion of flammable substances, the accumulation of vapors, earthquakes, electrocutions or burns due to deficiencies in the electrical installation, etc.
In this post, we run through 25 warehouse safety tips and explain how to implement them.
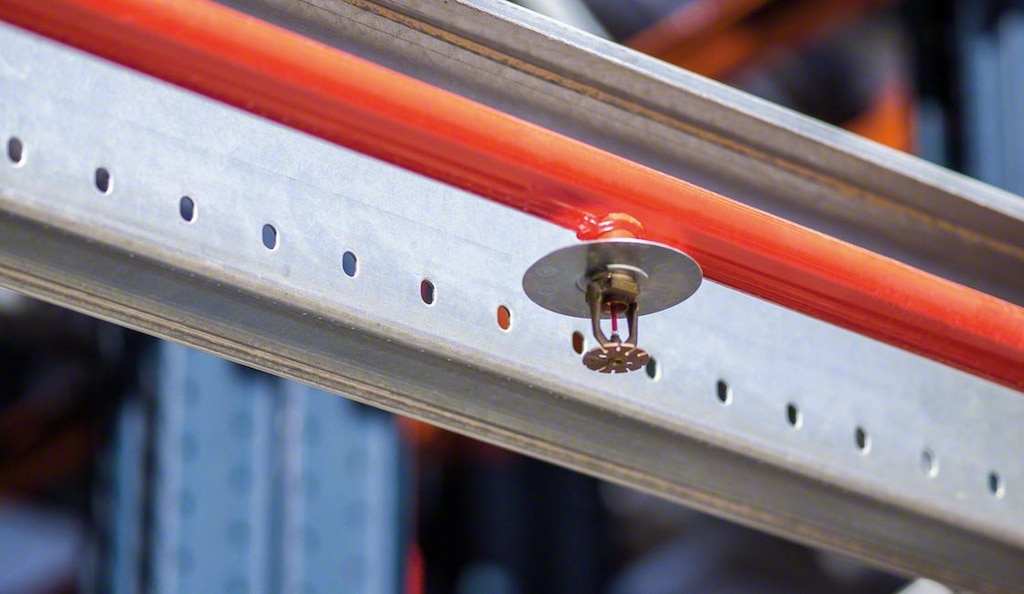
Tips for a safe warehouse environment
We’ll begin with a number of tips that help to significantly reduce the risk of falling goods or the collapse of the racks:
- Use appropriate PPE. The use of warehouse PPE protects operators from risks that could jeopardize their health at work. The most common types of personal protective equipment are: helmets, gloves, goggles, footwear, earmuffs, and earplugs.
- Carry out periodic inspections of the storage systems. Warehouse owners should schedule technical inspections of the racks or shelves at regular intervals. These are to be conducted by qualified technicians, who will assess the condition of all the elements in the system(s) installed.
- Respect the maximum rack capacities and measurements. Each storage system is designed to support certain maximum weights and goods with specific dimensions.
- Do not make any changes without consulting the supplier. The racks and/or shelves were configured by a team of professionals taking into account all technical details in order to ensure their safety. Therefore, it is totally inadvisable to make any modifications without first checking with the supplier.
- Read and bear in mind the safe load warning notice. This element, provided by the supplier, includes the technical specifications of the system installed. This plate should be posted in a plainly visible location and inspected periodically to check that the information contained in it corresponds to the actual installation.
- Inspect the condition of the pallets. This procedure can be carried out automatically via a pallet checkpoint. The aim is to guarantee that both the goods and the pallets are fit to be moved around the facility and won’t cause any accidents.
- Load pallets correctly. To prevent goods from falling and ensure the stability of the load as a whole, it’s vital to load pallets properly.
- Mount pallet rack guards. There are several kinds of pallet rack guards available. They’re designed to absorb different types of impacts and ensure that the load-bearing structure remains intact. Side protectors safeguard the lower lateral part of the pallet racks, while upright and frame protectors are anchored to the floor and cover the rack uprights.
- Install fall protection netting. This is installed on the back of racking that coincides with a working area or passageway to prevent goods from inadvertently falling. This netting must also be fixed to the top of the cross passages.
Meanwhile, it’s crucial to follow a series of recommendations to minimize hazards linked to warehouse traffic and the operation of the various machines and pieces of equipment:
- Properly illuminate the warehouse. A well-lit facility makes it more difficult for accidents to occur. Visibility of all warehouse elements is fundamental for ensuring the safety of the operators and the racking.
- Use safety enclosures. These are installed around the perimeter of an AS/RS (automated storage and retrieval system) or area in which a robot operates to protect the workers from materials that could become dislodged. Mesh partitioning, for instance, creates a protected space with restricted access.
- Install mirrors at crossings and in aisles. Mirrors increase visibility and prevent blind spots in aisles and crossings transited by forklifts and other handling equipment.
- Set up emergency underpasses. These run crosswise through the storage aisles of the racking system and act as emergency exits. They’re vital when the storage aisles are very long.
- Signpost the warehouse correctly. The objective is to inform operators of possible risks so as to identity restricted access zones, forklift operating areas, and order picking and conditioning spaces. Warehouse signage consists of panels with specific colors and geometric shapes.
- Operate handling equipment with caution. Workers must be extremely careful when driving forklifts in the warehouse in order to avoid impacts with other employees, the racks, and other handling equipment.
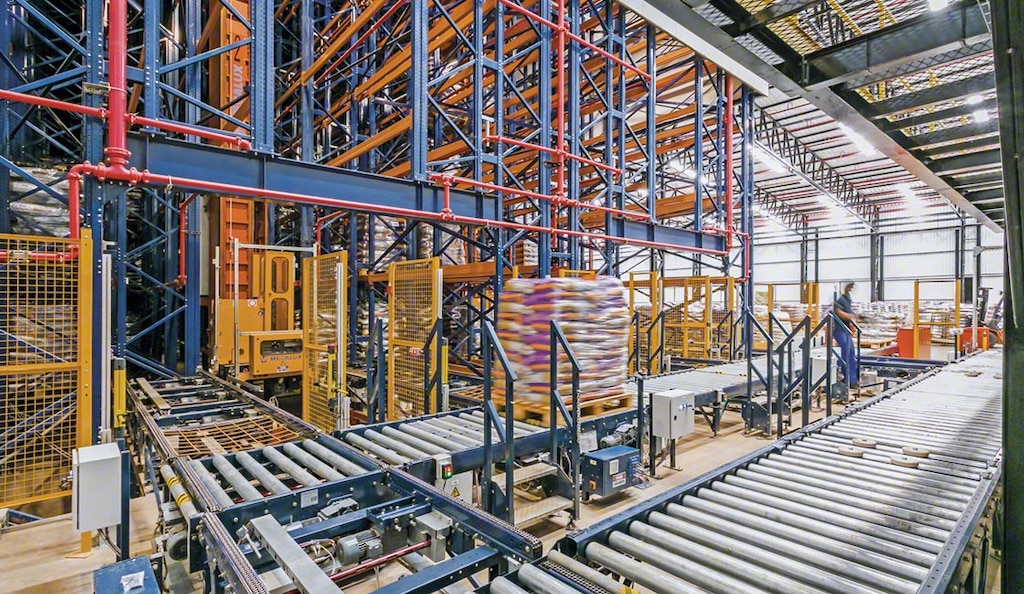
Likewise, it’s important to heed the warehouse safety tips below, which are more general in nature but just as relevant: they range from preventive maintenance of machinery and equipment to staff training and the proper hygiene of the storage solutions:
- Install fire safety systems. There are several varieties of fire protection systems that are fundamental in every warehouse: manual (extinguishers or hoses), alarm and automatic detection (smoke detectors), automatic fire control or extinguishing (automatic sprinklers), and temperature control and smoke evacuation systems.
- Perform regular maintenance of machinery. The implementation of an industrial maintenance plan — a set of actions carried out to compensate for wear and tear on the equipment and storage systems and, thus, prevent breakdowns — is a must for ramping up the throughput of the machines and improving warehouse safety.
- Ensure the order and cleanliness of the facility. A neat, tidy warehouse reduces the risk of incidents and enhances productivity. Industrial cleaning of the warehouse is basic for maintaining orderly work spaces and product handling as well as good hygiene when it comes to floors, ceilings, walls, racking, piping, lights, and machinery.
- Work at a suitable temperature. The automation of cold-storage warehouses helps to protect operators from prolonged exposure to cold temperatures.
- Train workers properly. Operators should be adequately trained on the correct use of the equipment. For example, in terms of software, Interlake Mecalux offers a customer training service that helps operators to make excellent use of Easy WMS and its design and configuration tools, as well as the rest of Interlake Mecalux’s products.
Lastly, it’s also advisable to automate different processes and operations. This notably improves the safety levels of a large part of the tasks performed in the facility:
- Implement automated transportation systems. The greater the number of movements made by operator-driven handling equipment, the higher the risk of incidents in the warehouse. To reduce the number of movements, automated transportation systems can be implemented to ferry the goods between different points in the facility. Options include roller conveyors, automatic guided vehicles (AGVs), and autonomous mobile robots (AMRs).
- Implement ergonomic workstations. Pick stations must guarantee that order preparation is efficient and, at the same time, safe, agile, and comfortable for the operator. For that reason, hydraulic arms and height-adjustable tables are often used to manage heavy loads and make picking more ergonomic.
- Employ safety sensors. These detect any element interfering with the movement of the automatic equipment to stop the system and avoid any mishaps. One of the most useful devices are the sensors incorporated in many automated systems such as the various types of stacker cranes and mobile racking systems.
- Automate pick paths. Implementing a warehouse management system (WMS) makes it possible to optimize operator order picking routes. This cuts down on warehouse traffic and reduces the risk of accidents.
- Automate the movement of goods in the racking. Using automated storage systems — such as stacker cranes (AS/RS for pallets), miniload systems (AS/RS for boxes), and the Pallet Shuttle system — also significantly limits movements made by forklifts and pallet jacks in the warehouse.
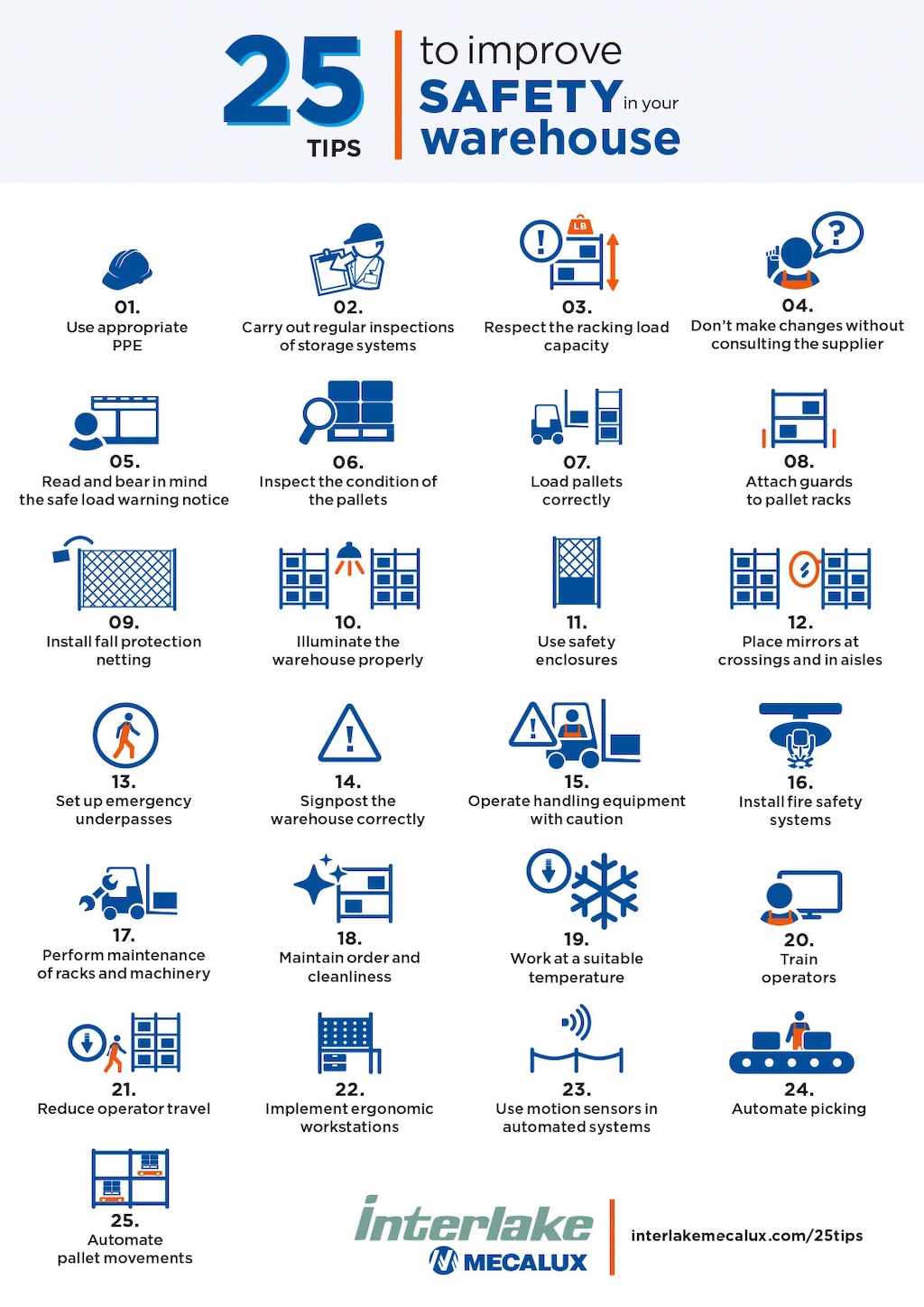
The road to a 100% safe warehouse
By following these 25 warehouse safety tips, you’ll bolster the safety of your operators, your products, and your transportation and storage systems. And this will help to boost your company’s productivity.
A safe warehouse is synonymous with logistics efficiency. This makes it easier to have a competitive supply chain while reducing errors, cost overruns, and a myriad of situations that are detrimental for the company.
Want to risk-proof your warehouse? Get in touch. One of our specialists will analyze your case and offer you a solution adapted to your needs.