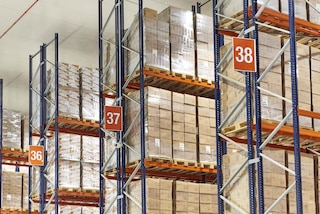
Palletization: the importance of getting it right
Palletization is the logistics process consisting of placing goods together on top of a pallet to consolidate the load, making it easier for the handling equipment to transport it. The pallet, a horizontal platform formed by boards, provides a base for the products so that the forks of a forklift or pallet jack can pick up and move the load as a whole.
In addition to facilitating transportation, the purpose of palletization is to protect the merchandise — from the start of its palletization to its destination — maintaining the product in perfect condition until it undergoes its next logistics process or reaches the end customer.
As your aim is to provide the goods with stability, the type of pallet you choose is fundamental. Therefore, you not only need to consider the material it’s made of (wood, plastic, or metal), but also their measurements: GMA pallets, half pallets, and Euro pallets, primarily.
Among other factors, the type of pallet you select will depend on:
- The different storage systems that make up the warehouse.
- The handling equipment (manual or automatic).
- The type of product stored.
- The company’s various suppliers.
Advantages of palletization
The establishment of the pallet as the standard unit load for warehousing has resulted in the following:
- More efficient goods loading and unloading: pallets enable operators (or automated loading docks) to insert and remove freight into/from the trucks in a more agile way. This is because the handling equipment can stack the products and, thus, reduce the number of movements.
- Streamlined goods flows in the installation: the products, piled atop pallets, are easily moved around the warehouse, ensuring that each item reaches the stage to which it is assigned when required.
- Improved safety for products and operators: pallets prevent workers from having to move the loads individually. This increases safety for both the goods and the employees.
- Inventory control: palletizing loads makes it possible to more strictly monitor each SKU. Since logistics managers know the volume of merchandise stored on each pallet, at a glance, they can get an idea of each product’s stock level.
- Optimization of storage space: when we talk about pallets, one key concept is stackability. The various storage systems, whether manual or automatic, make the most of the warehousing surface area, each with their pros and cons, of course.
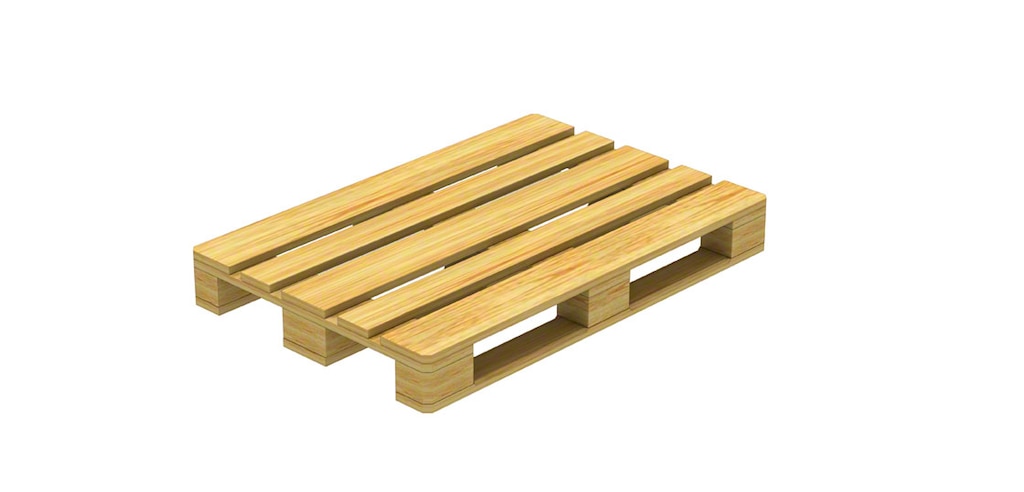
When did palletization begin? History of a logistics process
Pallets are considered the great supply-chain revolution of the 20th century. Faced with increasingly heavier products, at the beginning of the 1920s, US businesses began using wooden skids — precursors to the pallet — to streamline goods flows in installations.
But the pallet concept as we know it today was actually developed in the military field. During World War II (1939-1945), armies required a system for quickly transporting large quantities of weapons and supplies to troops on the front lines. From the Second World War to the beginning of the 21st century, pallets have been established as the main element in the supply chain, expediting product movements in phases such as goods receipt, storage, and delivery. Not surprisingly, both traditional and automated warehouses require that pallets be in excellent condition to function properly and ensure full throughput.
However, the e-commerce boom has made for more complex operations at most storage installations. Nowadays, goods are stored not only on pallets, but also in boxes.
So pallets no longer have a monopoly on being the standard unit load. Although they are still the most widespread component in the industrial, food, and automotive industries, in other sectors such as retail and e-commerce, in which orders are smaller and include one or very few SKUs, palletization has become practically obsolete.
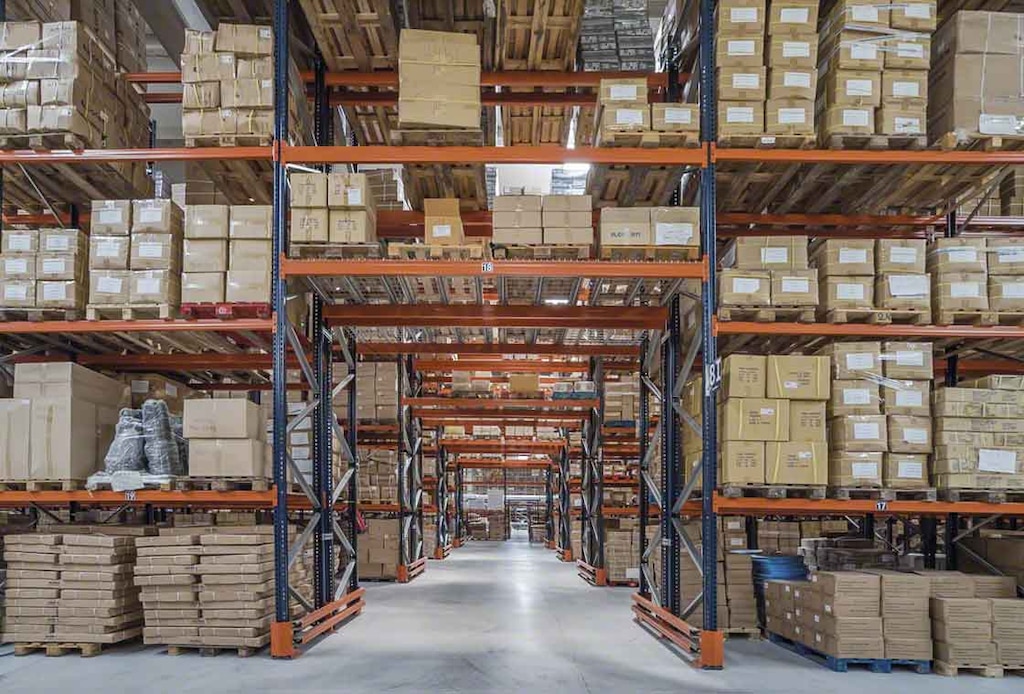
How to palletize goods properly
The palletization process has two phases: the loading of material and the securing of the goods. First, it’s necessary to deposit all the unit loads uniformly, stacking them appropriately. As a general rule, small boxes are used; due to their regular shape, they can be easily and neatly piled one on top of the other.
Additionally, when palletizing, you have to bear in mind that the weight of the pallet must be evenly distributed, never concentrated in the center or on one side. Otherwise, the pallet would become deformed, putting the goods as well as the operators at risk. Evidently, the material making up the package can’t overhang horizontally or vertically; this could cause the load to fall over when being stored or transported, representing a severe handicap for the company.
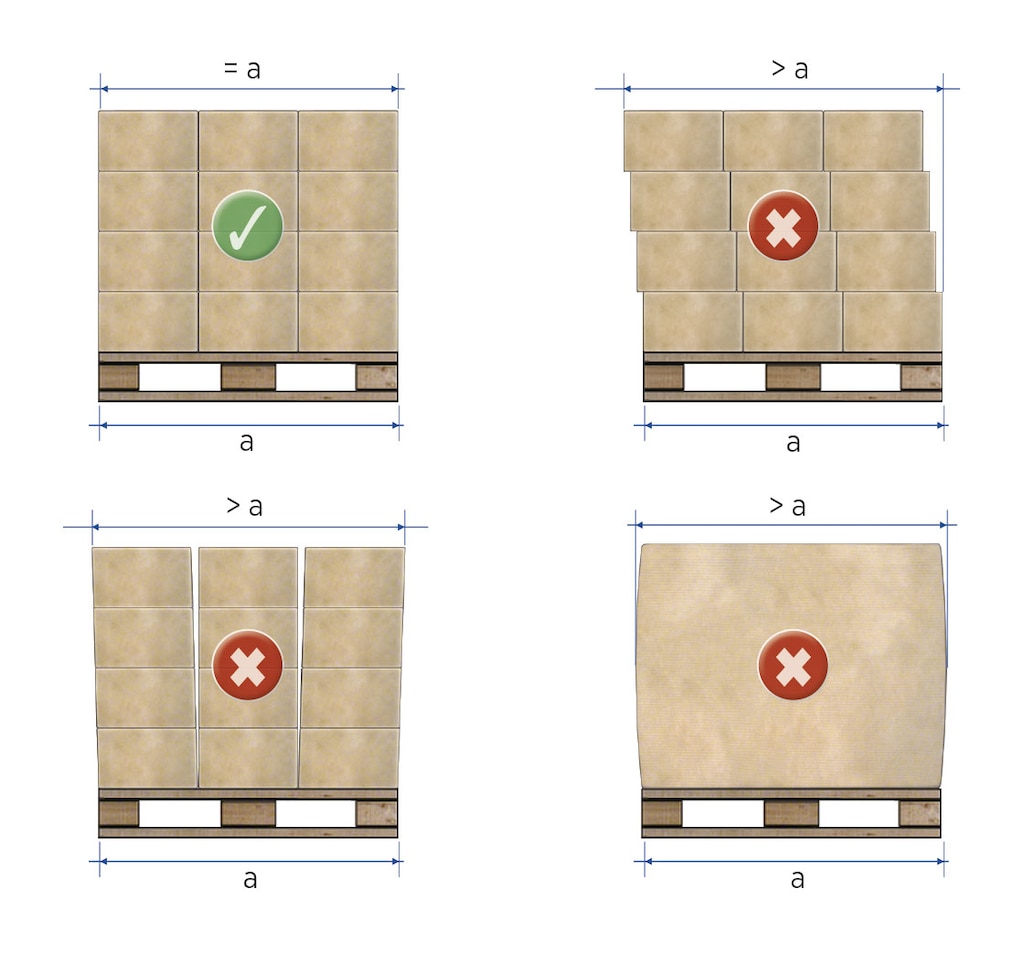
Once the load is stacked on the pallet, it’s essential to create a compact structure that ensures that the set of grouped goods remains stable during the various operations. This is normally done by applying transparent film in the stretch wrapping process, which protects the goods and binds them together. Although this used to be done manually, there are now dozens of automatic solutions on the market.
The new logistics scenario: warehouses with multiple load units
The rise of e-commerce has led many installations to replace their traditional pallets with boxes, especially in the fashion and retail sector. Nevertheless, there are still many warehouses whose operations revolve around pallets.
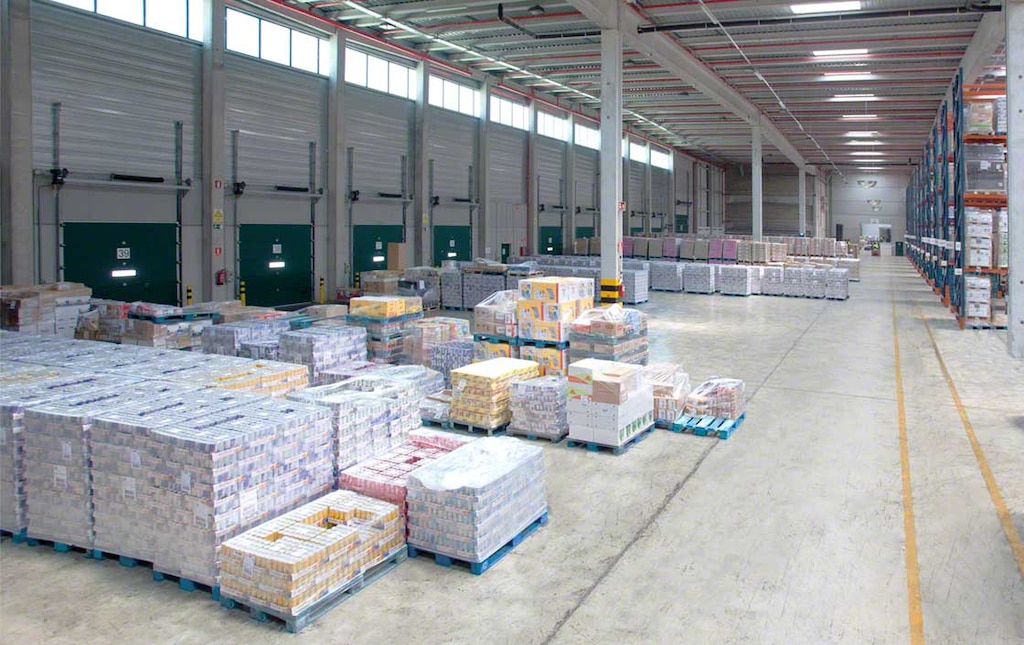
It’s a fact: more and more companies are implementing automated logistics solutions. This makes it even more important for palletizing to be done properly. All automated — and even semiautomated — installations call for the condition of the pallet and for the shrink wrapping to be appropriate so that the goods don’t overturn or hinder the normal course of operations.
At Interlake Mecalux, we have extensive experience in setting up logistics centers adapted to our customers’ needs. In fact, we have a wide range of both traditional and automated storage systems for pallets. Don’t hesitate to contact us. One of our expert consultants will show you the best solution for your requirements.