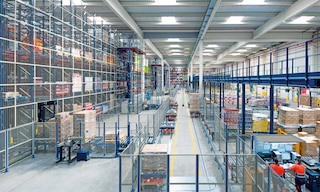
Just-in-case logistics: the alternative to JIT
Just-in-case (JIC) is a stock management strategy aimed at ensuring that companies have enough inventory to cover any kind of unforeseen circumstances. It’s the opposite of the just-in-time (JIT) method, whereby products are manufactured as orders are received.
So, is it better to cut storage costs at the risk of not being able to fulfill some orders? Or should you ensure you can fill all the orders in exchange for a higher investment in warehousing? In this post, we delve into just-in-case logistics, its main differences from just-in-time, and how to implement it in a warehouse.
How does just-in-case logistics work?
The just-in-case (JIC) inventory management strategy consists of producing, supplying, and/or storing raw materials and finished products ahead of time, having enough goods on hand at all times. The surplus inventory is stored in the company’s warehouses, preventing possible stockouts in the event of disruptions to the supply chain.
The just-in-case approach makes it possible to have available inventory when faced with unexpected demand, as the facility has enough reserve stock to fulfill new orders. JIC is a push production system in which manufacturing costs are lower due to the fact that production is carried out in advance and on a large scale. An example of a sector that routinely employs just-in-case manufacturing is the pharmaceutical industry. It works with small products that are easy to store and, if out of stock, would lead to serious consequences for the health of the community.
This method is the inverse of the just-in-time (JIT) approach, which is based on reacting to customer demand: the company produces the goods only when consumers order them (pull system), without keeping safety stock. Although just-in-time production brings down storage costs ― by not having excess stock ― businesses that implement JIT tend to be more vulnerable when faced with unexpected rises in demand, supply chain disruptions, or logistics planning errors.
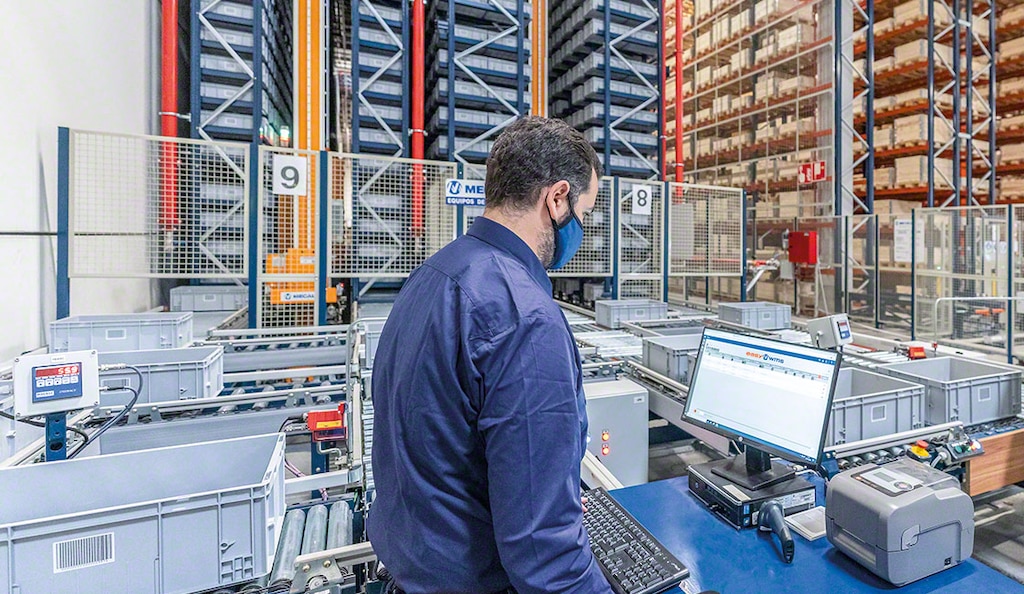
Pros and cons of just-in-case logistics
The just-in-case technique overproduces goods in exchange for guaranteed stock availability at any time. It is normally implemented in companies in which demand forecasting is complex, either because of the characteristics of the sector or due to a specific situation (lack of operators, supply issues, etc.)
In this sense, the JIC stock management method allows you to:
- Have extensive safety stock: companies will be able to fill all orders, and no customers will be disappointed.
- Plan expenses: JIC improves planning of expenses such as transportation, as certain stages can be prepared in advance, such as production and customer shipments.
- Manage peaks in demand efficiently: in the case of a drastic change in consumer trends, the firm can respond more quickly than its competition and strengthen its position in the market.
The main drawback with the just-in-case technique is that it involves taking higher storage costs compared to just-in-time, which could pose a serious problem in companies with diverse unit loads, irregular-sized products, or perishable goods.
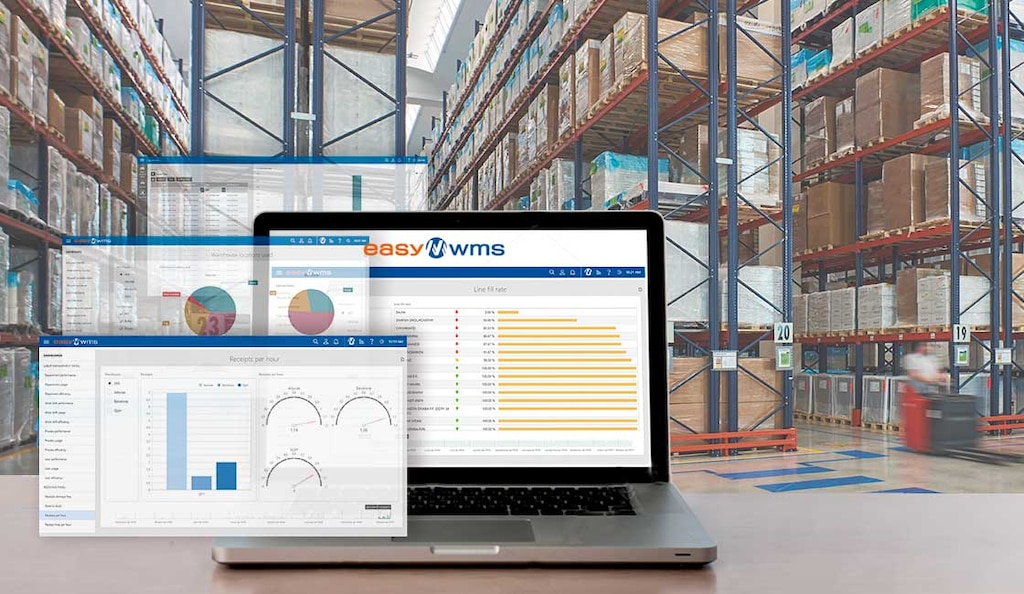
How to implement a just-in-case logistics strategy
To employ a just-in-case system, your warehouse needs to be organized, with everything in its place, especially if you have a high volume of stock. In this vein, it’s essential to invest in software that automates location management. A warehouse management system such as Easy WMS from Interlake Mecalux ensures control of product traceability and prevents picking errors. Samaniego, a Spanish company specializing in animal health, recently implemented Easy WMS in its facility. Warehouse Manager David García explains, “We were in urgent need of software that would allow us to manage our goods with complete accuracy.”
Likewise, a warehouse that follows the just-in-case inventory strategy requires a specific layout that enables goods to be stored without interfering in operator picking routes. This is the case of Alliance Healthcare, whose new facility was outfitted by our company. This logistics center is equipped with carton flow racks that store the goods in a compact way, with stock reserves housed behind the products in the same channels. At the top, these racks are combined with pallet racks, where these SKUs are stored on pallets.
In any case, it’s possible to automate picking to supply the locations, which comes particularly in handy in warehouses with a large number of goods inflows and outflows. Thus, companies that apply the just-in-case method and that have a high product demand can install automated transportation and storage systems. In combination with a WMS, these solutions ensure rigorous stock control while streamlining goods flows in the warehouse.
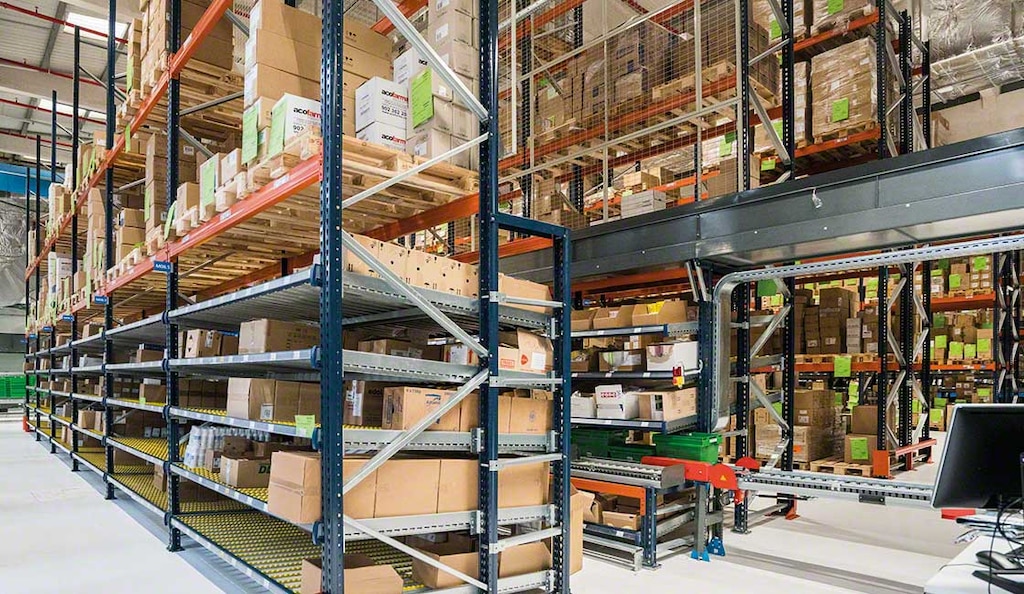
Logistics prepared at all times
Just-in-case logistics prevents vulnerability when it comes to supply chain disruptions. This logistics strategy makes it possible to have stock available to dispatch any order, but it does increase storage costs. Although just-in-time significantly reduces those costs, it also means that any logistics setback could damage the relationship between the company and its customers. Therefore, we really can’t say that one strategy is better than the other.
In short, there’s no single ideal production and storage system. Each company’s logistics strategy will depend on its planning and on the characteristics of its stock: type of product or consumer, facilities, etc. It’s up to the organization to consider the pros and cons of the different production and storage systems on their logistics strategy.
Questions on how to manage your inventory? Don’t hesitate to contact Interlake Mecalux. We’re your go-to provider of comprehensive logistics solutions: from a powerful warehouse management system such as Easy WMS to compact storage solutions that will let you implement just-in-case logistics efficiently.