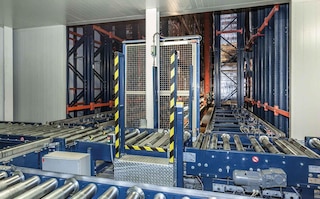
Automated picking: accelerate your pick tasks
Striking up a conversation about automatic picking means talking about the application of systems that completely take over picking tasks (i.e., order fulfillment), whether these are related to the collection or extraction of goods, their transport inside your warehouse, or sealing and shipping these items out. Just like there are different levels of warehouse automation (asrs), picking can be automated in various degrees.
What do you get out of automatic picking?
The installation of automated systems to streamline pick tasks means achieving:
- Speed: fully-automated order fulfillment is the way to go if you are managing many SKUs or if order flows intensify in specific time slots since the machinery and robots involved in these instances can reach higher speeds compared to manual processes.
- Safety: the machines and robots that perform automatic picking tasks fulfill several very stringent safety measures thanks to tech the system is equipped with like sensors and detectors.
- Precision: all systems are equipped with cutting-edge software and sensors to run tasks with the highest accuracy. Thus, these features reduce damage and accidents involving palletized loads.
These advantages return significant operational cost savings, since the process requires a small labor force.
Key elements of automatic picking
In a fully automated installation, if you focus in on an automated picking sequence, you will normally to see the following types of elements:
1. Stacker cranes
Stacker cranes that extract and slot goods into and out of their racking locations. These can mean AS/RS stacker cranes for boxes (light loads) or AS/RS stack cranes for pallets. Depending on the model and its functionalities, these stacker cranes can carry out replenishment and extraction of the goods in a single movement (called a combine cycled) to make the best use of operational times.
2. Roller conveyors and electrified monorail systems
Conveyors are used to move single products or prewrapped/palletized ones between the different warehouse zones. They are often located in the reception and shipping docks, since specially designed sections of conveyors can be set up for fast loading and unloading of trucks or trailers.
3. Anthropomorphic Robots
Anthropomorphic robots (also called Automated Picking Systems) contain a mechanized arm that is tasked with moving the goods on top of the pallet. It is run by cutting-edge software that can analyze the product’s parameters (e.g. weight, shape) and calculate the best way to pile the load on the pallet.
The big advantage of these types of machines is the speed at which they can reach during pick tasks. They can prepare several orders simultaneously and can even safely pick up whole layers of packages at once (thanks to its vacuum and pressure systems), at handling speeds of more than 1,000 boxes per hour. In our video you can see an automatic picking zone running at full power.
This is the perfect solutions for warehouses which need to tackle intense order fulfillment activity (especially for palletized goods) and entails a certain level of stability in terms of run times. Case and point are the farming equipment sector and production centers that connect plants to warehouses and vice versa, as shown in our automated designs set up in a French company called Grégoire-Besson.
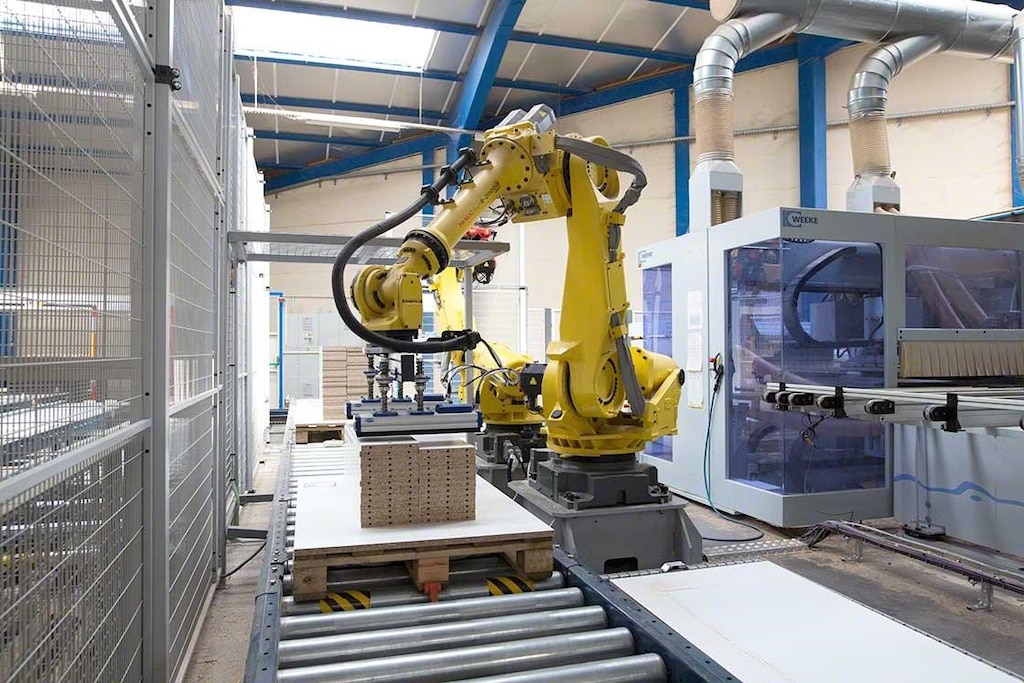
4. Checkpoint arches, stretch wrappers and automatic labeling
For stricter control over inputs and outputs, there are inspection zones with checkpoints, i.e., arch-type devices, whose built-in sensors are responsible for analyzing the pallet’s contents. Running your operations this way guarantees the load is arranged right and the information about it is sent to the WMS. Labeling is also done automatically.
On the other hand, stretch wrapping machines apply plastic film around pallets to make sure goods are held firmly in place.
5. Warehouse Management System or WMS
A warehouse’s management system is crucial for automatic picking to work at top efficiency. On this basis, it is fundamental that this system is versatile and can blend with a warehouse’s other software. The WMS integrates all the installation’s info in real-time and ensures your warehouse operates like a well-oiled machine.
Automatic picking embodied by these elements above is a prime example of this task’s robotization. However, there is also very different system mixtures that lay the way for efficient semi-automatic work formulas.
If you are looking at how to optimize your order fulfillment processes and don’t know that picking strategy will do the trick, feel free to contact us: we will analyze your operations and assess your business as we have done in companies around the world.