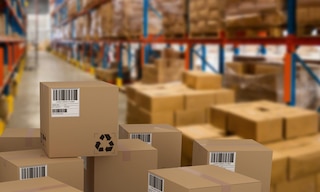
15 signs of a cluttered warehouse (and how to organize it)
A cluttered warehouse is the main cause of unproductive and inefficient logistics processes. Lack of order in a logistics facility reduces operational effectiveness and increases the risk of accidents not only for operators but also for the goods and the storage systems.
In this post, we examine the top 15 signs of a messy warehouse and offer solutions to ensure that they don’t stand in the way of your company’s competitiveness.
Cluttered warehouse: main signs
1) Poor warehouse layout design. The facility might not be configured in line with the reality of the business, or it might not consider the warehouse’s potential growth and the need to adapt to possible changes in the organization’s logistics planning. The warehouse layout design should be flexible enough to grow with these changes; for example, more areas could be allocated to order picking, or the loading docks could be expanded.
2) Underleveraged storage space. The warehouse should be equipped with a storage system that accommodates all the products and makes the most of the available surface area. This system must also be adapted to the characteristics of the goods. For example, if the warehouse manages a large number of pallets of each SKU, it would be best to implement a compact storage system (such as the Pallet Shuttle).
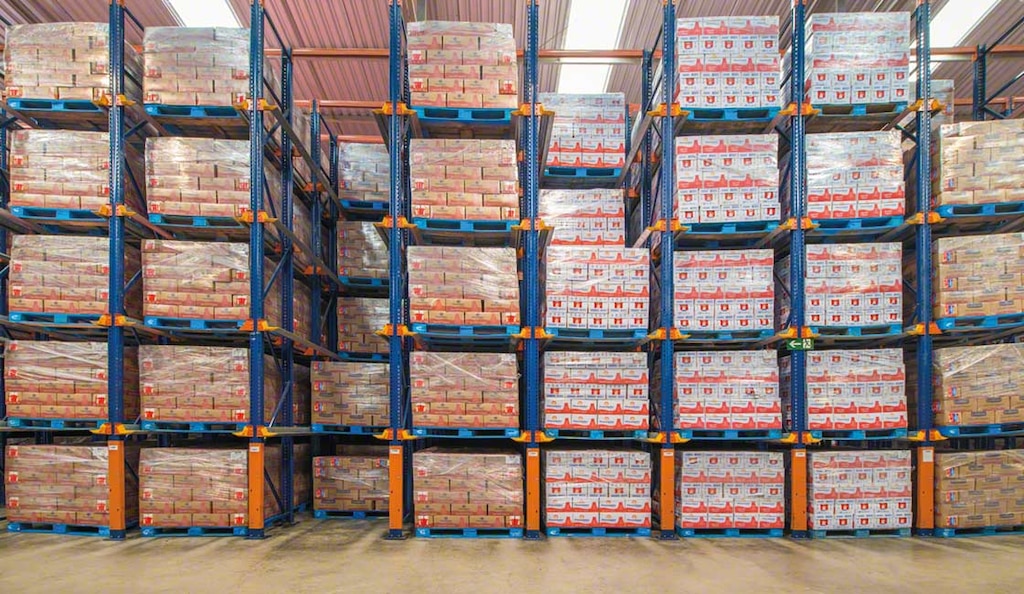
3) Excessive operator travel. In a cluttered warehouse, movements are neither coordinated nor optimized. That is, operators have to move around more than they actually need to when carrying out any task, such as storing goods or putting together an order. To resolve this, it’s advisable to resort to a warehouse management system (i.e., Easy WMS), which sends workers instructions on how to perform all operations, telling them exactly which location to go to. This program generates the fastest route, ensuring that operators travel the shortest distances.
4) Operator workload imbalances. Poor task distribution on the part of the logistics manager can lead to uneven workloads among the different operators and the creation of bottlenecks. To address this inefficiency, logistics planning needs to be carried out in keeping with the company’s strategic objectives. Additionally, the Easy WMS warehouse management system from Interlake Mecalux features modules — Supply Chain Analytics and Labor Management System, for instance — that are able to monitor activity in each part of the building to identify any disproportion in the facility.
5) Chaotic goods receipt and dispatch processes. A buffer with overstock and bottlenecks at the loading docks are very common symptoms of a cluttered warehouse. These situations can be remedied with proper logistics planning that takes into account and regulates goods flows in the facility, assigns suitable loading and unloading docks, and determines the role that the logistics staging area will play.
6) Lack of coordination with the production lines. A warehouse located near the production lines tends to act as a buffer, temporarily storing raw materials until they are required for production orders. Incoordination could cause imbalances in the production supply process, resulting in delays and errors when delivering the raw materials. Digitizing this supply process with a manufacturing execution system (MES) or with a WMS for Manufacturing software app is the solution for guaranteeing error-free, uninterrupted production.
7) Mistakes in product turnover assignment. Stock turnover refers to the number of times a warehouse’s inventory needs to be replenished in a given period of time, usually one year. In a cluttered warehouse, it’s very complicated to monitor all the SKUs, which is vital for planning the layout correctly. With a warehouse management system, it’s possible to define the turnover of the goods to calculate the necessary storage capacity, inflows and outflows, and planning of the facility’s overall activity.
8) Frequent stockouts. In a cluttered warehouse, it’s very difficult to know which items are available and which are out of stock. Consequently, a stockout could occur, that is, a lack of stock to fill current orders, leading to delays in order deliveries. One way to solve this problem is to rely on safety stock, in other words, extra inventory to cope with unforeseen events stemming from changes in demand or supplier delays.
9) Overstock. Without precise product control, a warehouse could end up storing more items than those strictly needed to serve customers, thus exceeding demand. Overstock has a huge downside: it increases storage costs and the risk of making mistakes. To avoid this, it’s advisable to implement predictive analytics to calculate the amount of necessary items and improve demand planning.
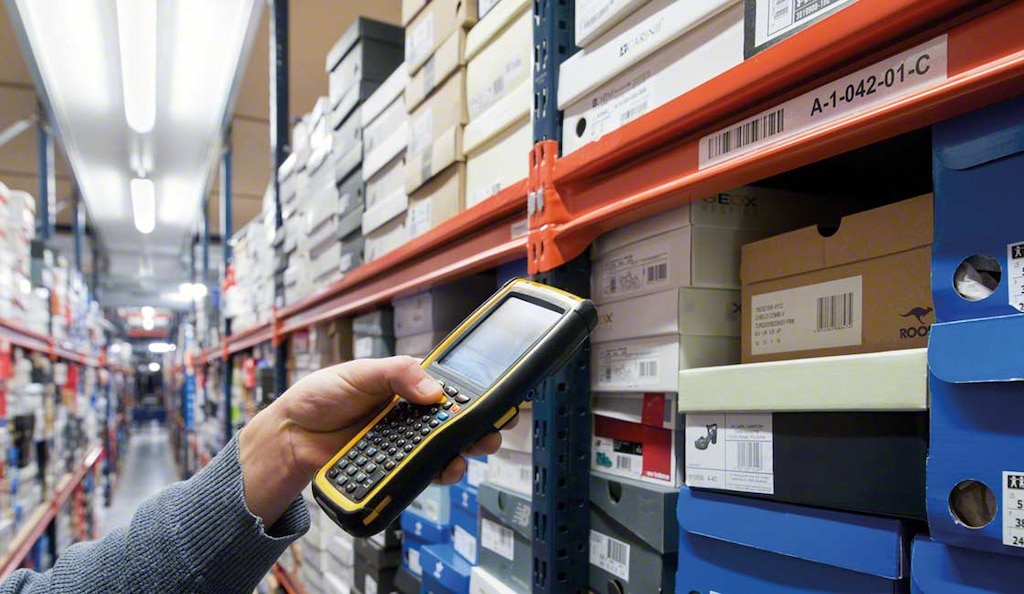
10) Stock losses. In a cluttered warehouse, there aren’t usually areas or locations allotted to the products (or these spaces aren’t respected due to the chaos produced by the lack of order). If the company doesn’t know what goods it has, some of them could be stored for too long and become obsolete (preventing them from being sold or delivered to customers). To avoid stock losses, it’s advantageous to digitize inventory management with a warehouse management system. This technology makes it possible to know exactly which products are stored and organize order picking taking into account the available stock.
11) Phantom inventory. Phantom inventory refers to mismatches between the stock in the store or warehouse and the stock recorded in an inventory program. In a cluttered warehouse, errors are commonly found in stock management. An example would be the organization of an order containing a product that’s not physically in stock in the warehouse. To avoid this, it’s a good idea to conduct periodic inventory checks to verify that the stock in the system and in the warehouse match. You can also implement a perpetual inventory system with the help of a WMS.
12) Inefficient picking. Order preparation is one of the costliest phases for warehousing logistics. Therefore, the picking method chosen should simplify operator tasks, ensuring that orders are fulfilled effectively and preventing errors stemming from manual management. Deploying a warehouse management system or employing picking assistance devices, such as pick-to-light or voice picking, are excellent options for achieving efficient order picking.
13) Picking errors. Mistakes arising from manual management of the picking process lead to an increase in the rate of returns. Organizing reverse logistics is a real headache for many companies. It also entails cost overruns that could jeopardize an organization’s competitiveness. For this reason, it’s important to cut down on errors in order picking and dispatch. A WMS simplifies operators’ tasks, telling them what to do step by step. This is especially important in the returns process, where the software automates the relocation of the product to the rack or to another order, minimizing costs.
14) Lack of coordination with carriers and logistics providers. The goods dispatch and shipping process must be agile and efficient to meet the delivery terms previously agreed upon with the customer. Lack of coordination between the facility and the various partners in these processes could prevent the order from being managed efficiently in the warehouse. For this reason, it’s essential to communicate with the delivery agencies via a warehouse management system that guarantees clear visibility of stock in all logistics stages. Specific modules can help to minimize errors in order delivery. One of these is Multi Carrier Shipping Software from Easy WMS, which coordinates with the carrier’s software, automating the shipping process and automatically generating the labels needed to ship the product correctly.
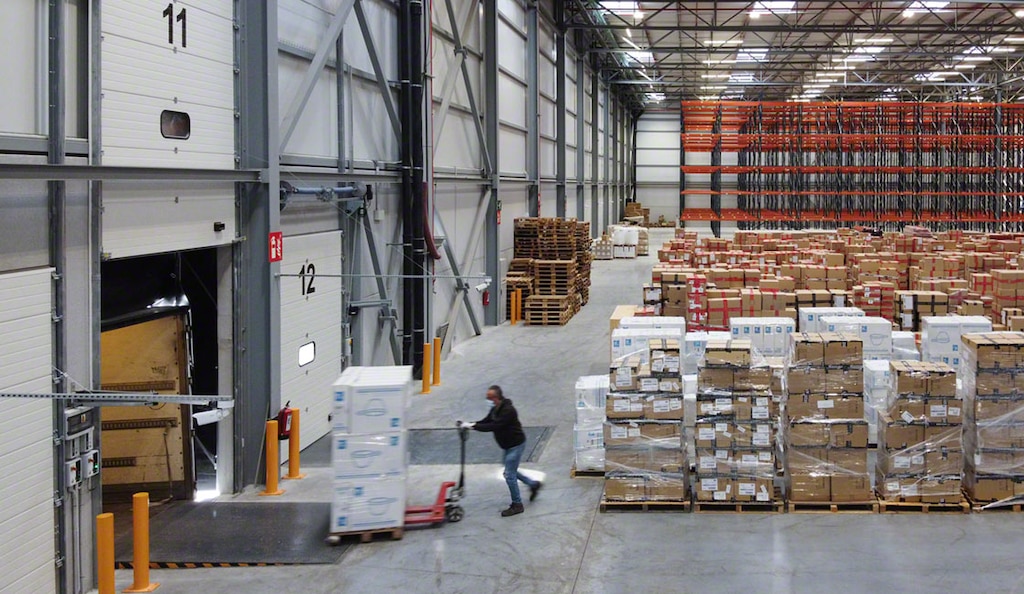
15) High accident rate. uClutter makes operator tasks difficult and increases the risk of striking various elements in the warehouse (other operators, the goods, or the racks). With proper warehouse signage, operators can identify the different areas by means of signs with specific colors and geometric shapes, thus, avoiding potential risks. Regular inspections of storage systems should also be carried out to check their condition and ensure the safe operation of the warehouse.
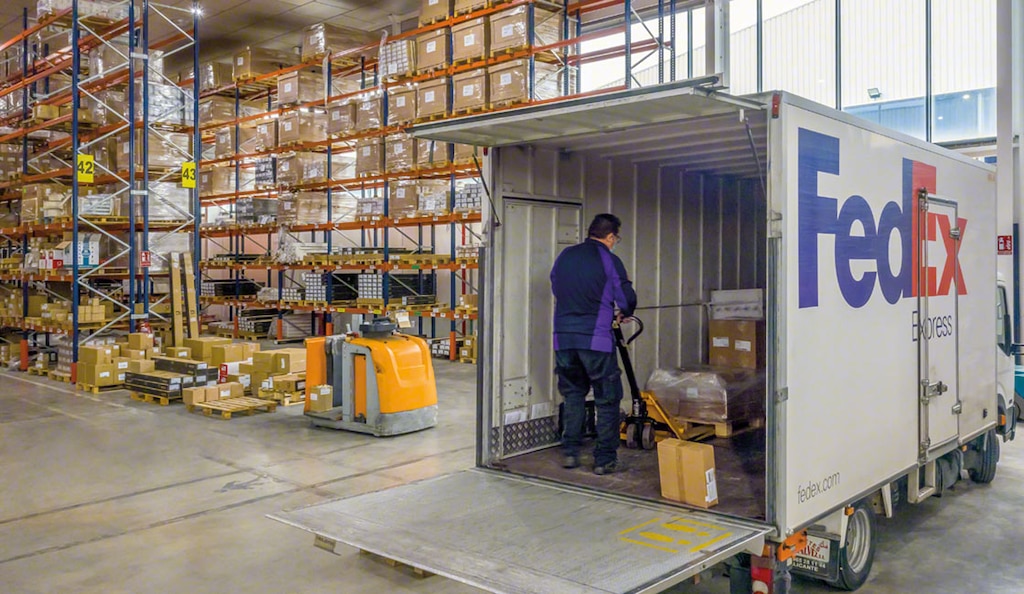
Cluttered warehouse: critical point for logistics planning
A cluttered warehouse will entail serious structural problems for a company’s logistics operations. Organizational chaos and poor stock and dispatch management, for example, impede process efficiency, reduce profit margins, and damage the reputation of any company. It’s crucial to identify the symptoms resulting in these scenarios in good time to implement the right solutions and restore optimal operating conditions.
If you detect any of the signs in this post in your warehouse, be sure to talk with a global intralogistics solutions provider such as Interlake Mecalux. Get in touch. One of our expert consultants will give you advice on the best solution for your company’s logistics operations.