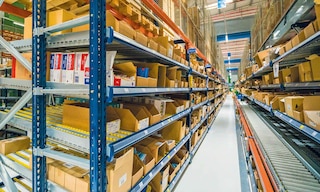
How to maintain optimal stock levels
Keeping the right stock levels for each product is key for eliminating cost overruns in warehousing and having a flexible, streamlined supply chain.
With logistics becoming more and more complex, companies need to control inventory demand in the warehouse to provide efficient service. Optimal stock levels let you know when to replenish product in the facility and how much safety stock is needed to prepare orders in progress.
What exactly is an optimal stock level?
Stock level refers to the quantity of stock available for an item in the warehouse at a given time. Maintaining an optimal inventory level ― the exact amount to cover demand ― is vital for dispatching orders without resulting in a stockout, i.e., not enough stock in the facility to guarantee the supply of goods.
The main goal of optimal stock levels is to achieve profitability in inventory management. Adjusting stock levels to demand avoids inefficiency arising from too much or too little inventory. Calculating stock levels to store only the necessary amount also optimizes storage space and helps to detect errors such as excessively long stock replenishment intervals, obsolete goods, and inflexible production processes.
When calculating optimal stock levels for each SKU in the warehouse, organizations need to take into account multiple variables: from stock turnover and characteristics to the configuration of warehouse operations, storage systems, and calculations like maximum stock level and safety stock.
Likewise, to reach optimal stock levels, companies have to have thorough knowledge of the demand for their products in addition to a long-term forecast. This information makes it possible to employ a goods procurement strategy based on the reorder point, i.e., exactly when the business should order stock from its suppliers to ensure efficient inventory management.
In logistics, there’s a mathematic stock levels formula applied to calculate when and how much stock a company needs to procure to ensure its target stock level: the EOQ (economic order quantity) formula, also known as the Wilson formula. This rule defines the ideal stock volumes and the frequency of procurement according to periodic stock demand, the cost of placing each order, and the expense of storing a unit load for a certain period of time.
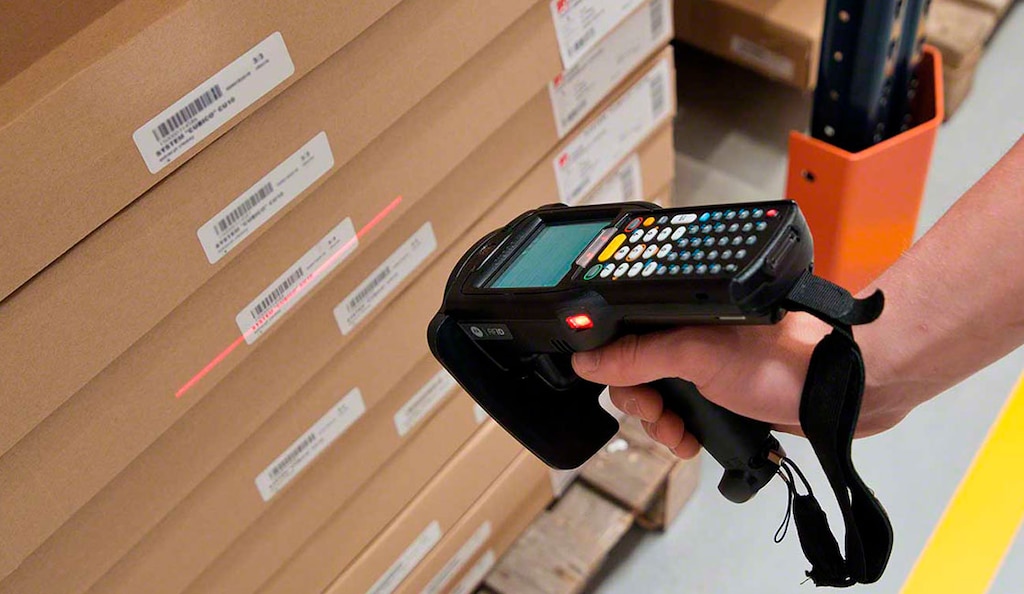
The importance of keeping optimal stock levels
Having ideal stock levels strikes a balance between fulfilling regular product demand and improving storage location efficiency. Optimal volumes of goods facilitate inventory control, ensuring product traceability and reducing the risk of obsolete stock.
In Logistics 4.0, warehouses call for flexible operations, especially in sectors such as e-commerce, food, and manufacturing, which require agile processes due to the high turnover of goods and strict storage conditions. An optimal stock level fosters more effective logistics processes, lowers logistics storage costs, and prevents the loss and deterioration of the stock stored.
Determining the right stock volume for each SKU is the first step towards establishing an efficient logistics planning strategy. By precisely calculating demand and the characteristics of the warehouse layout design, you can determine the most adequate storage and conveying systems and slotting and retrieval methods.
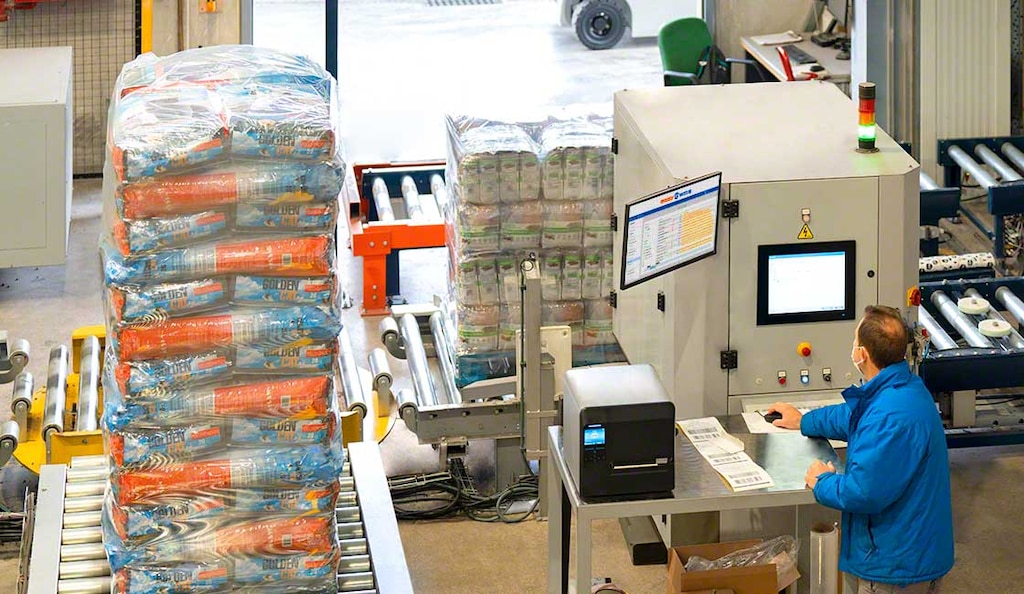
Advice for maintaining optimal stock levels
Ideal stock levels ensure that only the unit loads essential for covering demand are stored, optimizing the facility’s storage capacity and, above all, speeding up goods dispatch. Here are three tips for ensuring efficient stock levels:
- Understand and forecast demand for each SKU in the warehouse: implementing supply chain KPIs allows you to pinpoint how often each product is shipped. The information collected about the business is extremely valuable for knowing exactly how much product to store in the facility.
- Determine reorder points: this logistics calculation establishes when and how often to order more goods from suppliers based on product demand. The main objective of the reorder point is to achieve the perfect balance between the investment in goods — and their storage cost — and the probability of a stockout. The calculation of this mathematic formula can be scheduled periodically or revised as the logistics manager sees fit.
- Automate stock management: swapping manual management techniques for digital systems such as warehouse management software minimizes the risk of error in calculations such as maximum, minimum, and safety stock levels. A WMS automates replenishment tasks for automated systems. It also manages locations according to rules and criteria set in advance by the logistics manager.
Digitizing stock control levels in real time
Omnichannel and the ever increasing mixed bag of SKUs in warehouses have raised the complexity of stock management. More and more companies require synchronization between the stock in their logistics facilities and the goods distributed across their various points of sale.
In this context, a warehouse management system (WMS) could be the answer to the challenges posed by the new logistics scenario. This application eliminates the probability of error by automating inventory calculations, collecting information on stock demand, and providing full product traceability.
The WMS coordinates the movement of stock throughout the different logistics phases: storage, replenishment, order preparation, and product returns, among others. The result? Optimal stock levels and the most profitability from each unit load. The WMS software also enables stock control in real time, collecting information relating to orders. These data help to identify trends and regularly plan the ideal volumes of stock for each SKU.
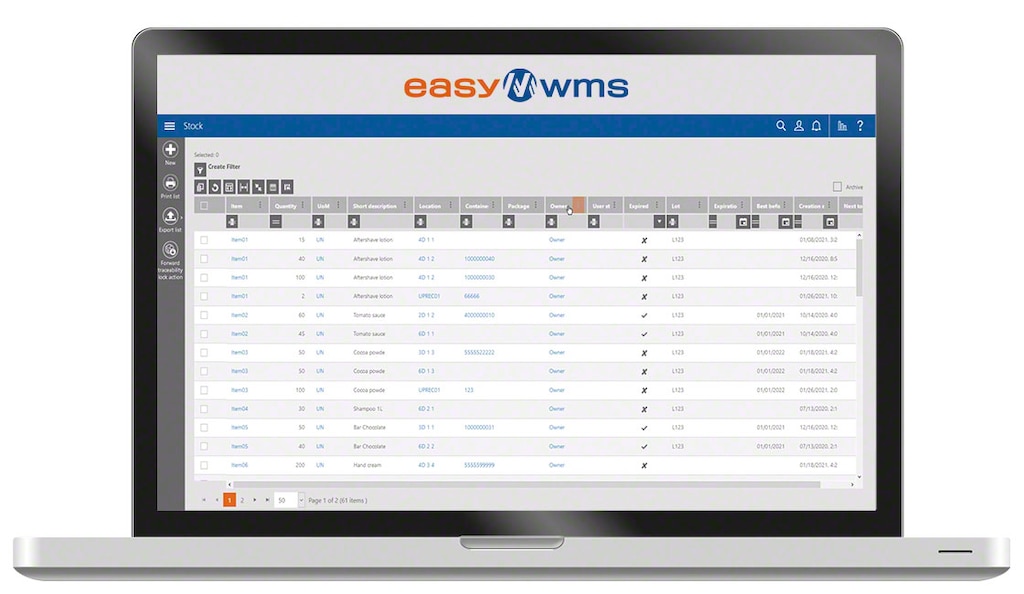
Calculating stock levels automatically for efficient management
Optimal stock volumes enable advanced warehouse management, reducing storage costs and promoting more effective logistics operations. Nevertheless, the incorporation of new sales channels and the steady increase in SKUs in warehouses complicates control over this process.
A warehouse management software program such as Easy WMS from Interlake Mecalux automates the calculation of key variables to identify the best inventory level for each product. Interested in improving stock management in your warehouse and improving the throughput of your logistics operations? Don’t hesitate to contact us. One of our expert consultants will advise you on the best solution for your business.