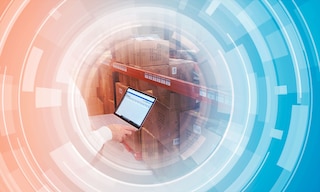
Inventory models: stock optimization for efficient logistics operations
In logistics, inventory management is essential to an organization’s success and performance. Inventory models are tools that help to optimize the number of products companies need to keep in their warehouses or points of sale do business.
The various applications of inventory models enable you to reduce stock-related costs, avoiding surpluses and ensuring you always have enough merchandise on hand to meet your customers’ needs. Maintaining adequate stock levels streamlines operations. It also facilitates the transportation and distribution of the products, improving customer service.
Deterministic vs. probabilistic inventory models
Both deterministic and probabilistic inventory models are methods used to manage a company’s stock levels. Each model has its own characteristics and adapts to multiple situations. Let’s take a look at the differences between them:
- Predictable vs. uncertain demand. In demand planning, deterministic models assume that the demand for products is constant and known for each period. Probabilistic models, meanwhile, posit that demand is uncertain and subject to variation.
- Fixed vs. probabilistic replenishment. While deterministic models are based on the replenishment of products when the stock level reaches a reorder point, probabilistic models consider additional factors, e.g., the desired service level and the risk of inventory depletion.
- Simplicity vs. accuracy. Deterministic models are relatively simpler to implement and calculate since they’re based on constant suppositions. Probabilistic models are more sophisticated as well as more accurate in reflecting actual demand fluctuations and associated uncertainty.
To sum up, deterministic inventory models are more appropriate when demand is stable and predictable, allowing for fixed stock levels and simpler calculations. Probabilistic inventory models, on the other hand, are more appropriate when demand is uncertain and variable. Thus, they require more careful planning to optimize stock levels and ensure adequate service. Your choice of model will depend largely on the nature of demand and the complexity of your company’s operations.
Characteristics of the main inventory models
There are different types of inventory models, each designed to address different business situations and scenarios. Below, we describe some of the most common models:
Economic order quantity (EOQ) model
The EOQ model is a formula used to determine the optimal number of products a business should purchase every time it places an order with a supplier. The aim of the EOQ model — also known as the Wilson model — is to balance the costs of acquiring and holding inventory.
The EOQ model is based on certain assumptions, such as constant and known demand, inventory ordering and holding costs, and the absence of quantity discounts and product shortages. The following is the EOQ formula:
- Q: Optimal order quantity
- D: Annual demand for the product.
- K: Cost of placing each order.
- G: Cost of storing a product for a given period.

Although the EOQ model is a helpful tool, it should be used in conjunction with other stock management techniques. You should also consider factors such as demand variability, lead times, and potential quantity discounts. Moreover, in practice, conditions may change, so you might need to adjust your order quantities from time to time.
Economic production quantity (EPQ) model
The EPQ model determines the optimal quantity of goods a company should produce in a single batch to minimize total costs (i.e., manufacturing, maintenance, and inventory holding costs during the production cycle).
This inventory control model is employed in organizations that manufacture their own merchandise as opposed to simply purchasing it from suppliers. It’s suitable for situations where the production of an additional batch has associated costs (e.g., labor or costs generated by the storage of stock during the manufacturing process).
The EPQ model is based on certain suppositions — a constant demand rate and a periodic production rate — so it can’t be applied in all business situations. Some of the model’s limitations include the fact that it does not consider possible variations in demand or costs, nor does it take into account the deterioration of perishable goods. Therefore, it’s vital to adapt the model to the specific conditions of each company and industry to make more accurate and appropriate inventory management decisions.
ABC model
The ABC analysis for inventory classification is a stock management technique used to divide stored products into three categories: A, B, and C. This model helps to prioritize the most valuable merchandise, enabling more strategic inventory management. The classification is based on the products’ relevance to the company, their value, and their turnover. It’s used to redirect management effectively and concentrate efforts on the most critical elements.
The ABC analysis is based on the Pareto principle, which states that a small percentage of the goods is responsible for most of the total inventory worth. Generally, the 80/20 rule applies: approximately 20% of the items account for 80% of the total value of the inventory.
In the ABC model, stock is grouped into three categories, applying different inventory policies to each one:
- A items. These include the most relevant products, typically 20%, representing 80% of the total inventory value. For A items, you can implement more stringent stock control strategies due to their overall worth and significant impact on financial results.
- B items. These represent an intermediate position in terms of value. They account for around 30% of inventory and 15% of its total worth. You can apply more moderate inventory policies to B items since their value is moderate.
- C items. These goods have the lowest profit margin. They make up the remaining 50% of the products but represent only 5% of the total inventory value. For C items, you can adopt more relaxed inventory policies: they’re worth less and are cheaper to manage.
The ABC method is advantageous for streamlining stock management, as it focuses resources and effort on the most critical items. This brings down costs and improves the overall efficiency of the inventory system. The ABC classification should be reviewed and updated periodically; the relative importance of items may change over time due to demand fluctuations or changes in costs.
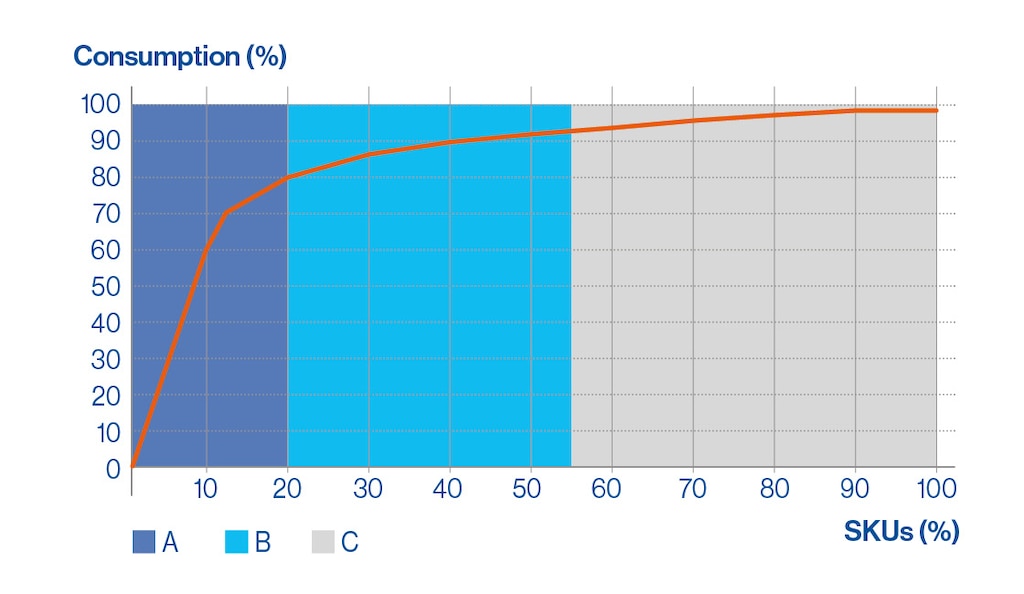
Benefits of proper application of inventory systems
Implementing inventory models appropriately can bring your company the following advantages:
- Cost optimization. Inventory models help you determine optimal stock levels in your facility, avoiding overstock and reducing costs linked to storage. Furthermore, they ensure you’ll always have safety stock to meet demand, minimizing loss of sales due to product shortages.
- Improved operational efficiency. Efficient inventory management results in better utilization of resources and smoother operations. Replenishment and tracking processes become more accurate and less error-prone, saving time and effort.
- Greater customer satisfaction. Effective inventory management translates into greater product availability, avoiding stockouts. This ensures that products are available when customers need them, increasing their satisfaction and loyalty to your company.
- Informed decision-making. Inventory models provide data to support decision-making in goods management. With these tools, you can base your actions on solid and accurate information, boosting your chances of product management success.
Inventory models: more productivity, lower costs
Inventory models are fundamental tools for efficient stock management. By integrating them effectively into management, you can enhance your competitiveness, optimize your operations, and achieve a higher level of business success.
Implementing a warehouse management system such as Easy WMS, for instance, will enable you to implement different inventory models based on your particular needs. Be sure to get in touch. One of our expert consultants will be happy to explain how Easy WMS can help you automate inventory management to empower your business.