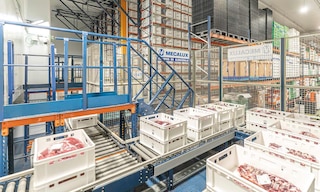
FEFO: optimizing inventory management for perishable goods
Managing inventory efficiently is crucial for any company that handles perishable products or materials with expiration dates. In this context, the FEFO (first expired, first out) method stands as a fundamental strategy to ensure that the items in storage the longest are used or sold first, minimizing waste and guaranteeing quality.
What are the rules of FEFO?
FEFO is an inventory management strategy employed by facilities and businesses that work with perishable goods or products with use-by dates.
The basic premise of FEFO is that items with the closest sell-by dates should be consumed before products with later expiration dates. In other words, the first product to expire is the first to be used or distributed. This stock management strategy helps to reduce waste, maintain product quality, and meet regulations and norms in sectors such as food and pharmaceuticals, where freshness and safety are paramount.
In the food industry, dairy products, meat, fruit, and vegetables are managed via FEFO to preserve quality and safety. This method is also essential in the pharma sector to avoid the shipment of expired medications. Ultimately, effectively implementing the FEFO method for goods with best-by dates helps protect consumer health and safety.
Advantages of FEFO in warehouses
FEFO in inventory management offers significant benefits, especially in industries with perishable goods or expiration dates.
- Reduction of waste. Using products with the closest sell-by dates first minimizes their likelihood of expiring or becoming obsolete in the warehouse. This results in fewer discarded items.
- Quality maintenance. The FEFO system safeguards the freshness and optimal conditions of the products to be sold or distributed.
- Compliance with regulations. In highly controlled industries, such as food and pharmaceuticals, this stock management strategy helps fulfill compliance with regulations and standards related to product safety and quality.
- Better stock turnover. The FEFO inventory method leads to higher stock turnover, meaning products move through the facility more quickly.
- Improved customer satisfaction. Ensuring that products delivered or sold are fresh and of high quality meets consumer expectations, enhancing customer satisfaction.
- Cost reduction. Decreasing waste and managing inventory efficiently will cut costs in the long term. Companies can optimize resources by preventing product obsolescence and requiring less storage space.
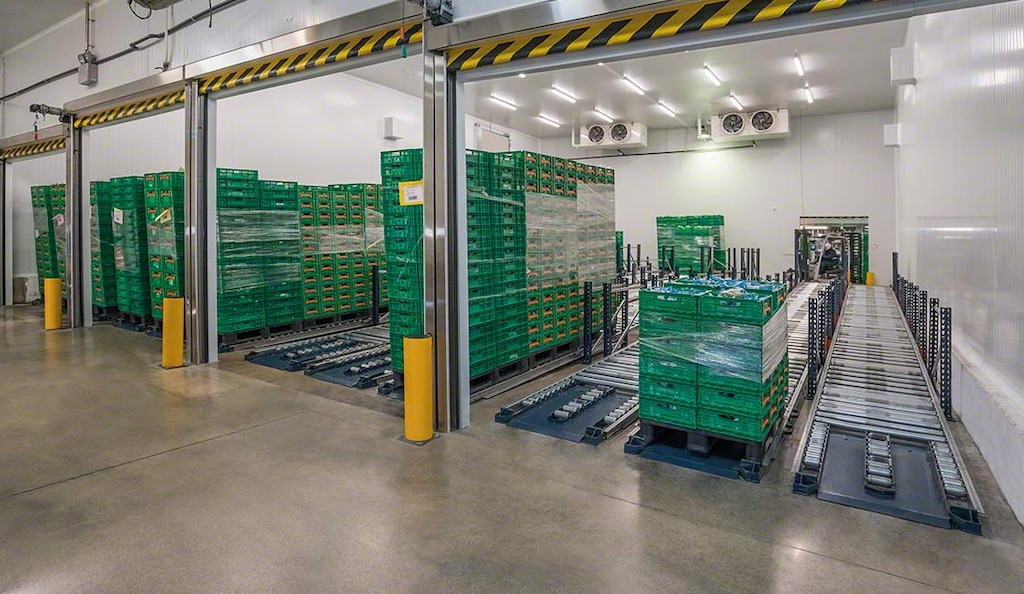
How to implement FEFO
To employ the FEFO method in your warehouse, be sure to follow these steps:
- Product labeling. Goods should be clearly labeled with their use-by dates, from their arrival at the warehouse to their shipment.
- Inventory record. Stock must be registered and kept up to date in the inventory records, including the expiration dates of each product. You can document your stock using spreadsheets, warehouse inventory management software, or other tools.
- Storage and picking by expiration date. New products are stored behind those already in stock. When performing picking, operators retrieve goods with the closest best-by dates first.
- Monitoring and updating. It’s necessary to review your inventory, adjust the arrangement of your merchandise, and update sell-by dates whenever appropriate.
The FEFO method calls for tight stock control, which can sometimes be quite challenging to carry out manually. Digitalizing inventory management with a warehouse management system (WMS) ensures that product distribution is well-organized in line with the FEFO principle.
Examples of companies that use the FEFO method
There are multiple storage systems available on the market — from conventional to automated solutions — that are suitable for FEFO inventory management.
Argentine supermarket chain Coto, for example, houses high-turnover items like potatoes and onions on pallet flow racks: “We manage goods according to FEFO. So, the pallet with the nearest expiration date is the first out, making flawless product turnover a reality,” says a Coto engineer. The racks consist of a set of slightly inclined roller channels that allow the goods to move automatically by gravity. Operators load pallets on the higher side of the roller tracks, and they slide to the other end, ready to be picked.
In Spain, Congelados de Navarra has built one of Europe’s largest automated warehouses. This rack-supported building houses 83,300 pallets containing food products at -13 °F. Goods are stored and retrieved using Mecalux’s automated Pallet Shuttle system with transfer cars. Managed by Easy WMS software, the facility maximizes storage capacity and speeds up the flow of movements through FEFO when distributing goods: the first products to leave the warehouse are those with the closest best-by date.
Digitalization greatly facilitates FEFO. Medis-M, a wholesaler specializing in pharmaceuticals and medical devices, uses Mecalux’s Easy WMS in its facility in Slovenia. The software controls the traceability of 3,330 SKUs and devises the company’s putaway strategy. To optimize slotting, the program incorporates rules and algorithms that consider variables such as the SKU of each product and its size. “We manage materials following the FEFO method, where the first product to expire is the first out,” says Rok Krsnik, Logistics Manager at Medis-M.
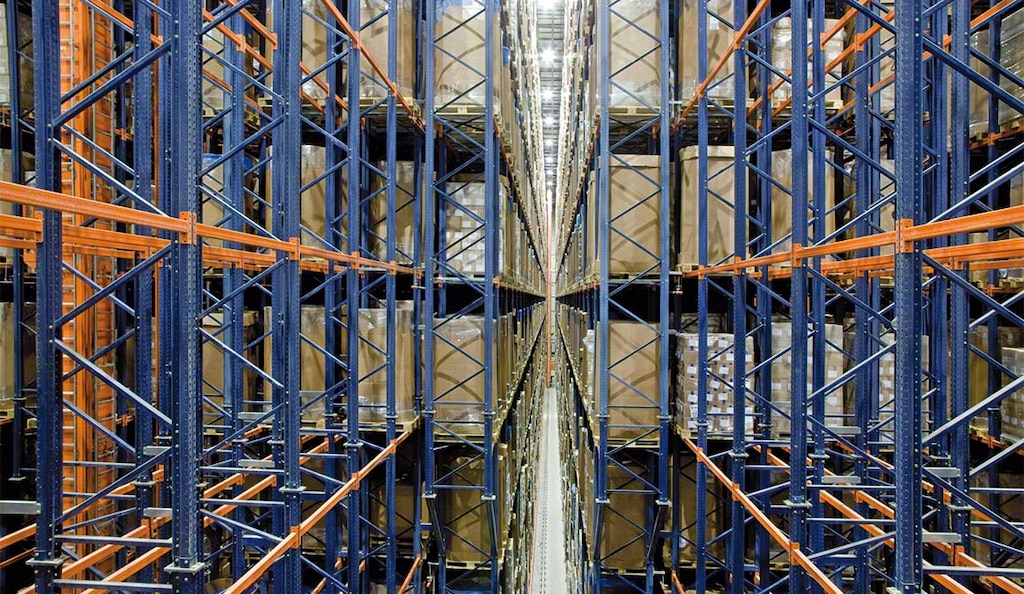
Perfect turnover for perishable goods
FEFO is a vital inventory management strategy in industries that deal with perishable products. Its benefits include waste reduction, merchandise quality maintenance, regulatory compliance, and enhanced customer satisfaction, among others.
To apply FEFO effectively, it’s important to invest in storage systems that enable flawless goods turnover. Likewise, businesses with a large number of high-turnover items turn to automation and digitalization to streamline operations and drive throughput.
When choosing storage systems to successfully implement FEFO, it’s advisable to rely on an integrated logistics provider with experience in designing and installing warehousing solutions. Looking to optimize your perishable goods warehouse? Be sure to get in touch. One of our expert consultants will be happy to advise you on the best option for your company.