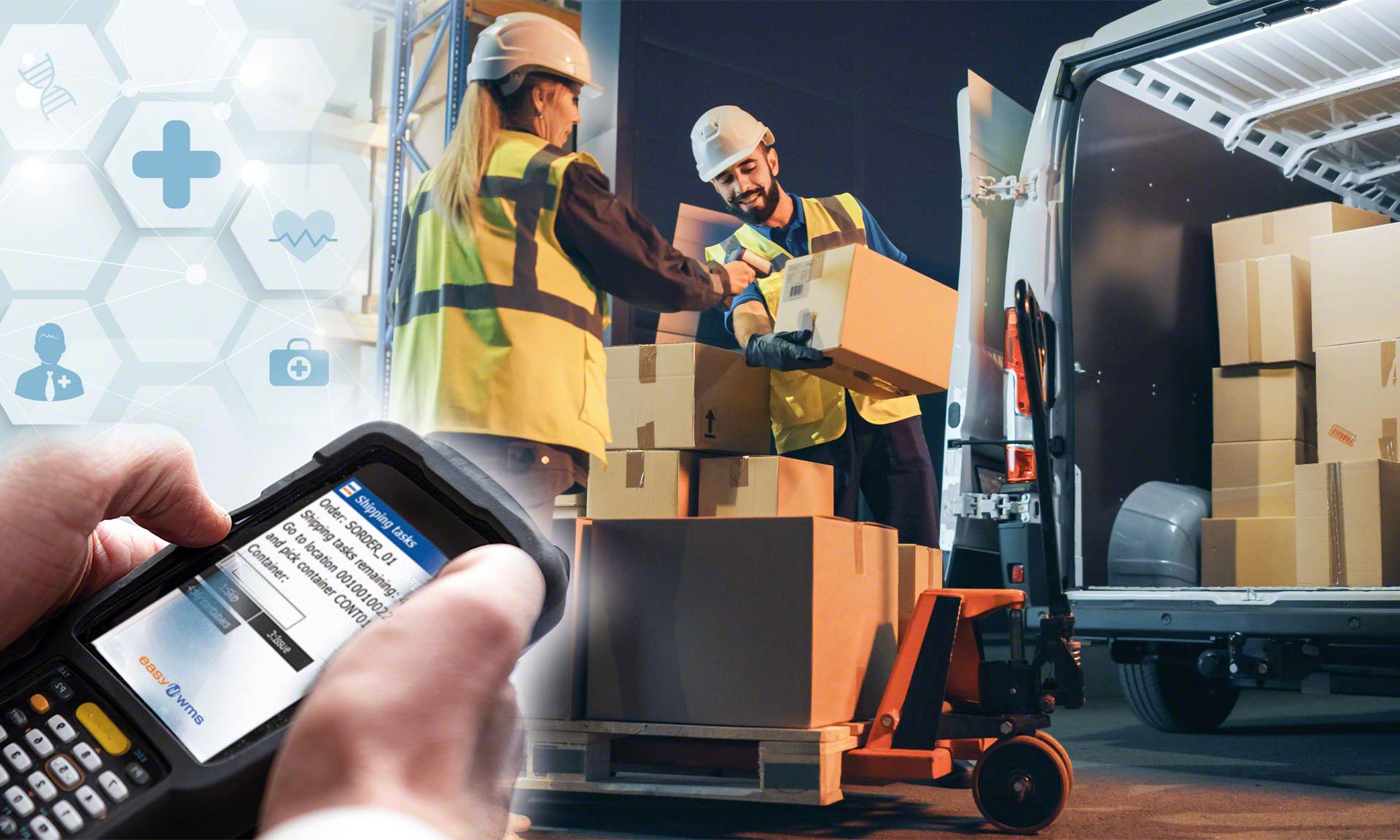
Digital control for demanding healthcare logistics operations
Medical supply wholesaler Medis-M eliminates order-picking errors with Easy WMS software.
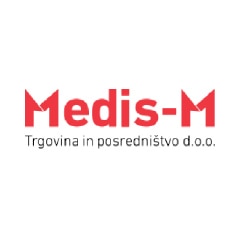
Medis-M, a wholesaler specializing in pharmaceuticals and medical devices, has optimized its healthcare logistics processes with Mecalux's Easy WMS. The software controls the traceability of all products and sends operators instructions to streamline operations such as picking.
Medis-M: putting people’s health first
Based in Maribor, Slovenia, Medis-M is a wholesaler specializing in pharmaceuticals and medical devices for pharmacies, hospitals, and nursing homes. People’s health is a top priority for this company. Accordingly, Medis-M has an extensive portfolio of medical supplies from the most renowned brands on the market to meet the most demanding needs of healthcare professionals.
- Founded in: 1996
- Customers: 300+
- No. of SKUs: 3,330
CHALLENGES
|
SOLUTION
|
BENEFITS
|
---|
The logistics processes of healthcare industry businesses are becoming more demanding by the day. After all, behind the processes that make up the supply chains of these types of organizations, there is a lot at stake: people’s health. Globalization, commercial needs, and legal requirements are compelling companies like Medis-M to fine-tune their operations to provide their customers with differentiated service.
Maribor, Slovenia’s second-largest city, is home to medical supply wholesaler Medis-M. The organization recently decided to boost its business with Mecalux software. Rok Krsnik, Logistics Manager at Medis-M, explains what led Medis-M to modernize its processes: “The minute we began to see a rise in the number of orders and shipments, we realized we needed to improve our customer service. We had to change.”
For Medis-M, managing 3,330 SKUs is a central process in its day-to-day activity: “We wanted strict control over our inventory status,” says Krsnik. Pharmaceuticals and other medical products require specialized treatment to guarantee their integrity and risk-free consumption. Identifying all items from their arrival at the warehouse and controlling their traceability are essential for storing them in ideal conditions.
Prior to digitizing the facility, Medis-M managed its goods manually. In the receiving area, operators would write down the batch number and expiration date of each item on a delivery note. Then, they would enter the data into the company’s ERP system. “It was a clunky process, and the risk of making mistakes was high — especially since certain products are very similar,” says Krsnik.
One of the challenges for organizations that work with pharmaceuticals is to make product distribution agile to meet tight delivery times. “Another process we wanted to improve was order picking,” says Krsnik. The throughput of picking operations has a direct impact on customer satisfaction.
The Medis-M warehouse is divided into two zones: a 3,337 ft² area for storing small items and a 6,071 ft² space for bulky products. Operators pick the items that make up orders in both zones and then group them in the consolidation area. In the past, the lack of coordination between the two storage zones meant that some orders could not be filled immediately, delaying their distribution to pharmacies, hospitals, and nursing homes.
Digitization of logistics operations
Medis-M felt that the best way to monitor its goods and processes was through digital technologies. “We used to use an ERP to control our logistics operations. But we were looking for a more sophisticated system, specifically designed to ramp up our warehouse productivity,” says Krsnik.
The company decided to digitize its logistics operations with a warehouse management system (WMS) that would enable full product traceability and decision-making to enhance operations. Medis-M sought the cooperation of technology company Špica because “they’re experts in digital solutions for supply chain management,” says Krsnik. After analyzing Medis-M’s logistics needs, Špica proposed installing Easy WMS. This Mecalux-developed software is implemented in more than 1,000 facilities in 36 countries. “They assured us it could be tailored to the characteristics of our business,” says Krsnik.
Mecalux integrated Easy WMS with Medis-M’s ERP system. The two programs now transfer data and information to increase operational productivity. Through this interfacing, Easy WMS knows all the product details and notifies the ERP system of any movement an item makes in real time. Since Easy WMS was installed, Medis-M's warehouse productivity has risen by 36%, and order-fulfillment errors have fallen by 51%.
Operations management with Easy WMS
“One of the features we like most about Easy WMS is its ability to supervise all warehouse processes to minimize any possibility of error. The program is extremely intuitive and user-friendly. New workers joining the company learn how to work with Easy WMS in no time,” says Krsnik.
The Mecalux software intervenes in all of Medis-M’s warehouse processes, from goods receipt to the distribution of orders to customers.
- Goods receipt. Products sent by suppliers in Slovenia, Germany, and the US arrive at the facility. Operators read the barcode of each item with their RF scanners, and the WMS records these materials automatically. “Now, work in the receiving area is much easier: operators simply have to scan the barcodes on the products,” says Krsnik. Thanks to the integration with the ERP system, Easy WMS logs the logistics attributes of each product.
- Storage. Easy WMS assigns each item a location. To optimize slotting, the program incorporates rules and algorithms that take into account variables for each product, e.g., SKU number and size. “We manage goods in line with the FEFO method — first expired, first out,” says Krsnik.
- Stock control. By identifying all products as they arrive at the facility, Easy WMS can effectively supervise and organize all the goods. The software balances the items that have arrived against those that have been dispatched to determine the available number of units for each SKU. Thus, to take care of replenishment, Easy WMS notifies the ERP system of the number of products to purchase from suppliers to guarantee their availability for picking.
- Order picking. Orders are prepared by grouping and by zone. “Operators work only in the area Easy WMS assigns to them. Once there, they pick products belonging to several orders on a single run,” says Krsnik. If an order includes items from both storage zones, Easy WMS arranges for them to be picked immediately in the two spaces. The merchandise is then combined as soon as possible in the consolidation area. Easy WMS shows the operators how to prepare each order, indicating which location to go to, which items to pick, and how many to extract.
- Consolidation. In the consolidation area, operators group goods from the different warehouse zones and pack orders before shipping them to end customers. By following commands from Easy WMS, operators sort the items, verifying that no mistakes have been made during order picking.
- Dispatch. Every month, more than 2,000 orders are distributed to Medis-M customers throughout Slovenia. In the dispatch area, orders are organized by delivery address. To ensure error-free deliveries, operators first scan the barcodes on the orders. Then, following instructions from Easy WMS, they merely place the products on the corresponding delivery truck.
Agility and traceability
Easy WMS is a software program with a multitude of functionalities that provide Medis-M with advanced logistics operations capable of adapting to business changes. Among the most notable improvements the company has seen is its product traceability. Monitoring stock more stringently limits the risk of mistakes in the different operations. Moreover, it makes it possible to track any movement the goods make until orders are delivered to customers.
The Mecalux software is designed to scale up business productivity and streamline fundamental operations such as order processing. “Easy WMS designs the most efficient pick paths through the facility to ensure operators travel the shortest distances,” says Krsnik.
An integrated supply chain is the key to Medis-M’s success. Digitization has enabled the company to manage and distribute its pharmaceuticals and medical supplies in compliance with safety protocols. All warehouse operations are coordinated and synced with one objective: to deliver goods to customers quickly and with zero errors.
One of the features we like most about Easy WMS is its ability to supervise all warehouse processes to minimize any possibility of error. With this software, our warehouse productivity has gone up by 36%. The program is extremely intuitive and user-friendly. New workers joining the company learn how to work with Easy WMS in no time.
Gallery
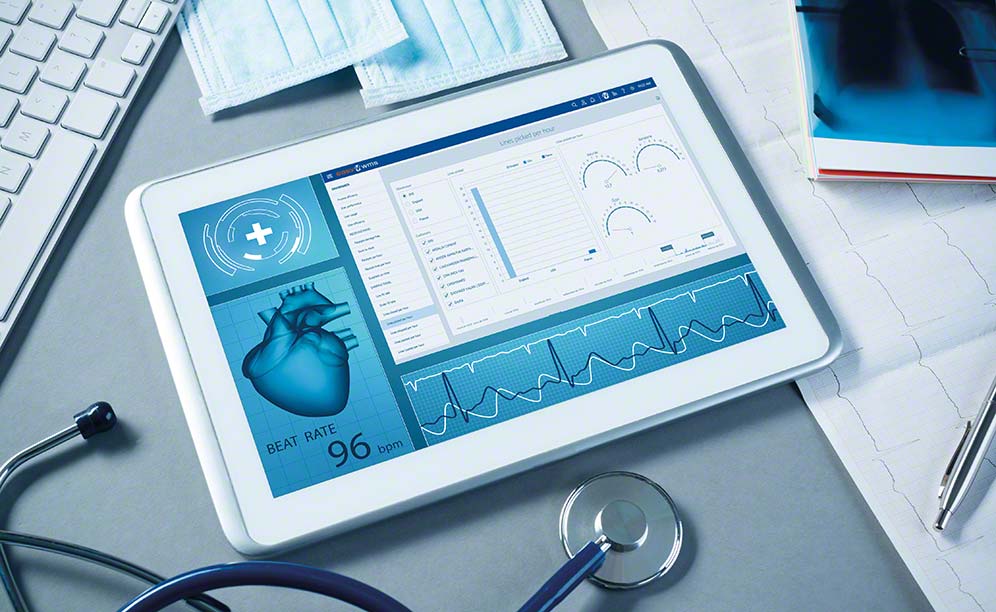
Digitization in healthcare logistics at Medis-M in Slovenia
Ask an expert