Low level order picking is performed above ground level. To fall under this category, the units must be positioned at a height that enables them to be accessed by an operator on foot or, at most, riding on the highest part of the body of a self-propelled pallet truck.
Systems for low-level picking
Orders can be picked at low level by taking individual pieces or packages stored as unit loads, or stored in the spaces in racking units enabled for this (through shelves, for example).
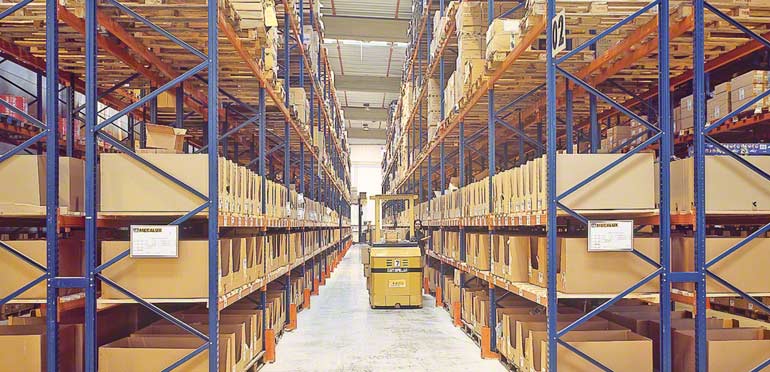
Operator working on a lower level of pallet racking.
As we have already seen, picking at ground level invariably involves taking parts of a unit load. At low level, this does not necessarily have to be the case. Rather, orders can be prepared by taking loose pieces or parts that have first been separated and placed in the spaces on a racking unit configured for manual picking.
When to use low-level picking
The choice of the most appropriate system is directly related to the number of orders that have to be prepared each day. Therefore, the factors that influence this decision are the time and space available.
In terms of space, when the number of SKUs to be included in the average order exceeds the capacity of the space allocated for order preparation, orders cannot be prepared at ground level. To solve this problem a system of racking units can be installed with two or more load levels in this preparation area. The choice of the number of load levels and their size will be determined by the volume of the
unit loads or individual parts to be handled.
As regards time, if an excessively large number of orders has to be prepared each day, the classic preparation sequence (in which a unit load is taken and placed in the order) may prove too slow. In this case, it would be helpful to use a low-level manual picking racking unit system.
When using this type of structure, there is a radical change in the way of working and orders are prepared in two phases. In the first phase, racking units are loaded with units, loose pieces, or parts, which are supplied either from the reserve area or from another preparations area at ground level. The second phase is to prepare the orders, taking pieces from the spaces in these racking units. For this system to operate smoothly, different shifts should be set up for each phase so that the working day is divided into two, four, or more parts. Depending on the number of orders to be prepared and the size of the racking units, the duration of each shift can be as long as a full working day.
Equipment for low-level picking
The appropriate equipment for picking at low levels is low-level pickers or order pickers, as discussed in the section on "Handling Equipment".
Position on manual picking racking units
When picking products stored on racking units, the quickest man-to-goods system is that which is carried out in the most manual way possible.
This circumstance arises when the operator, either on foot or mounted on a pallet truck or self-propelled trolley, can pick pieces or parts for orders without needing a machine to reach higher levels and without having to climb down from a machine to do so.
However, when there is a large number of SKUs stored in a facility, picking at height must be used and, therefore, machines are required to access the goods.
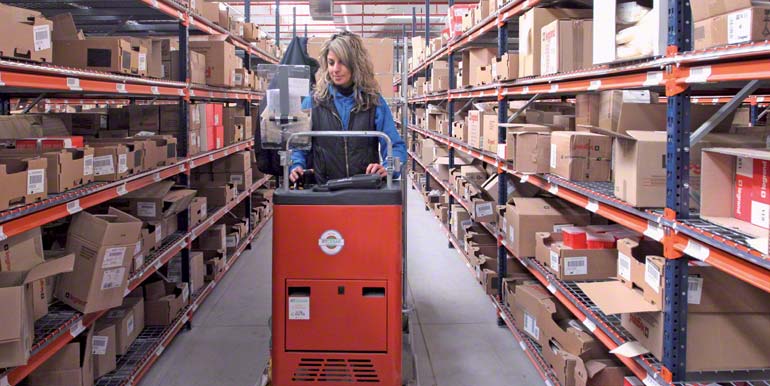
Operator carrying out picking tasks with an order picker machine.
When planning the position of racks for the preparation of orders on low levels, there are two options. The first is to prepare the orders on the general storage racking units. The second is to install racking units exclusively for manual picking, i.e. without the worker having to be lifted on a machine or climb down from it.
When the designer chooses the second option, it is important to remember that these racking units must have specific characteristics. These units must be capable of being loaded manually, with the height of the top load level no higher than the average shoulder height of the employee preparing the order. The maximum weight of packages positioned there must not exceed 55 lb.
These characteristics lead to a very specific racking unit design. Given that it will have to be loaded manually, the compartments or spaces do not have to be large and only need to be able to contain the average number of pieces to be picked in each picking shift (plus a percentage stipulated as the margin to ensure that there is no shortage of stock).
Given that the height of the racking units is limited, if the number of SKUs is very large and the available surface area is relatively small, orders must be prepared on two or more levels, for which mezzanines are used, connected using staircases.
Since packages must weigh no more than 55 lb, the racking units used are light or medium-duty. It is also advisable to store the heaviest pieces or packages on the intermediate levels and the lighter ones on the rest. The distribution of the units according to weight is illustrated in the image below. This will result in more efficient order preparation.
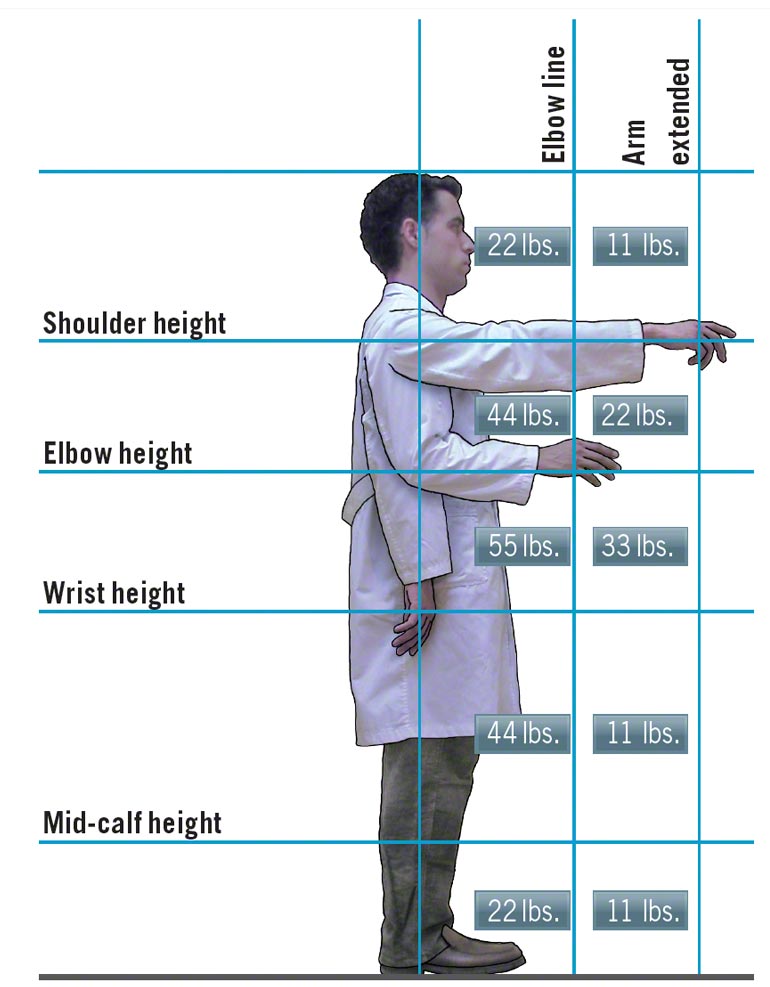
Having an ergonomic position is crucial during picking.