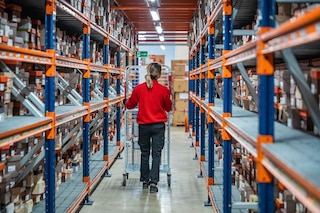
When wave picking applies
Wave picking is one way of organizing in-house pick tasks. Broadly speaking, it consists of:
1. Grouping orders according to logistical criteria like delivery routes or shipping priority.
2. Assigning each wave to an operator who will pick up all these products in the same route in a given period (each wave usually lasts between 1 and 4 hours, but this will depend a lot on the flows handled in each warehouse).
3. Finish preparing orders in a dedicated zone where they are packaged, consolidated and sorted for dispatch.
Time slots can also be reserved within the wave picking organization to replenish your picking shelves.
How does wave picking work?
Wave picking is one of the most efficient picking methods if it is executed with the help of a warehouse management software (WMS). On the one hand, wave picking is usually a combination of the following methodologies and their core principles:
- Batch picking: groups of orders are collated according to the shipping priority, the transport route and/or the customer, the number of orders, their composition and the workload of each operator.
- Picking by zones: groups of orders are distributed by location, to optimize routes and avoid congestion or excessive traffic in the warehouse aisles.
Depending on the in-house handling equipment, you can choose to operate:
- Hand carts, roll containers or order picking machines, where the products are initially set. Later, they are moved to another area where they are organized.
- Hand carts divided into slots where products are classified on the spot, reducing post-picking consolidation.
After a wave is done, the grouped products are taken to an order processing area where they are sorted (unless this was already done in the cart) and packed. The following diagram shows a graphical breakdown between order groups and wave picking zones:
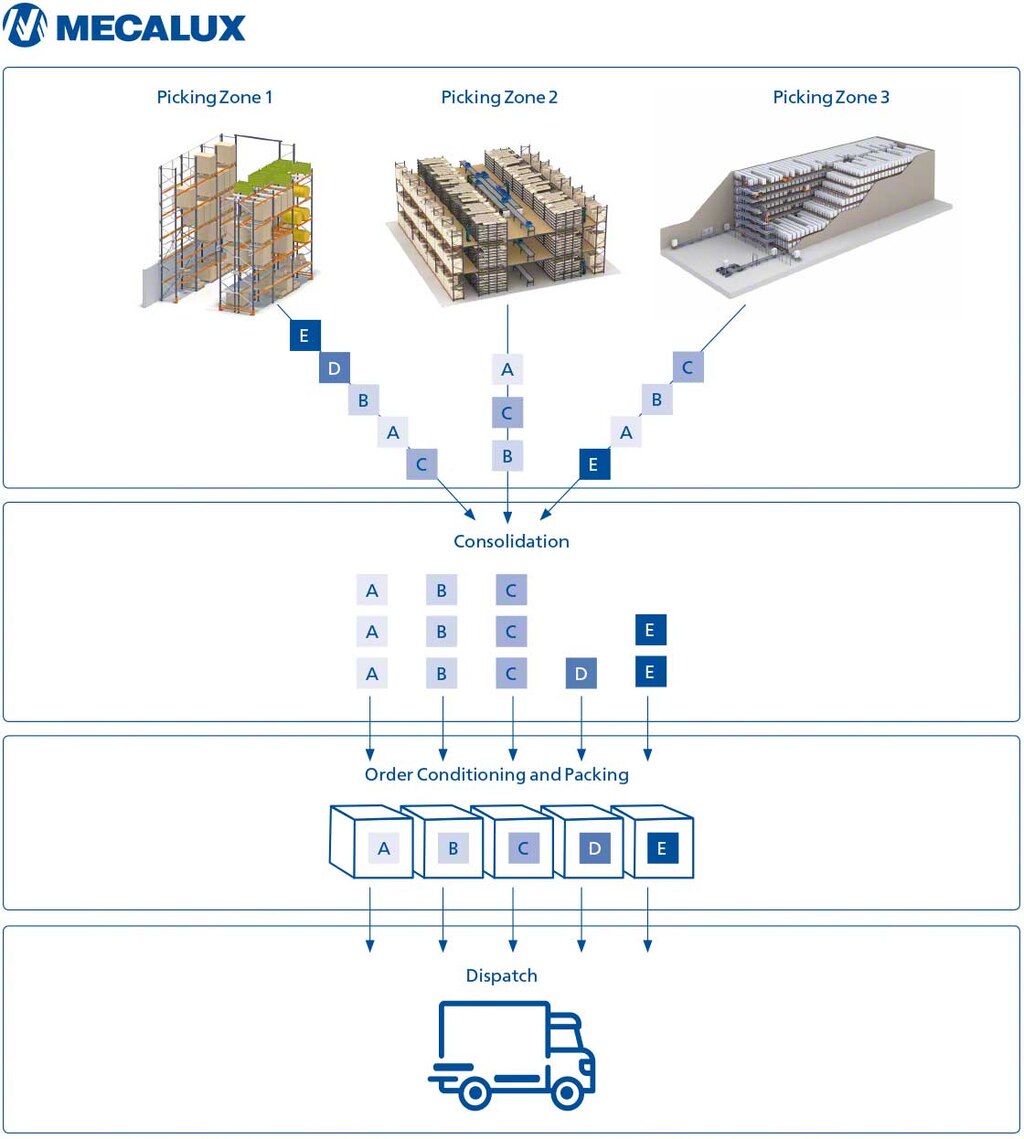
On the other hand, when using a WMS, each wave lasts a planned amount of time set by the system automatically. The system calculates the time ranges it takes to perform each task and reserves time for other operations like kit or pallet assembly, goods packaging, restocking of shelves... Don't forget that the warehouse management system has a digital snapshot of the warehouse layout, which it works from.
Waves tend to be “static” in wave picking (i.e. no changes are allowed once the wave has started, and marking the big difference with waveless picking). Waves are also ordered at the beginning of the day or shift. For example, if looking at some simple wave picking, it would look like this:
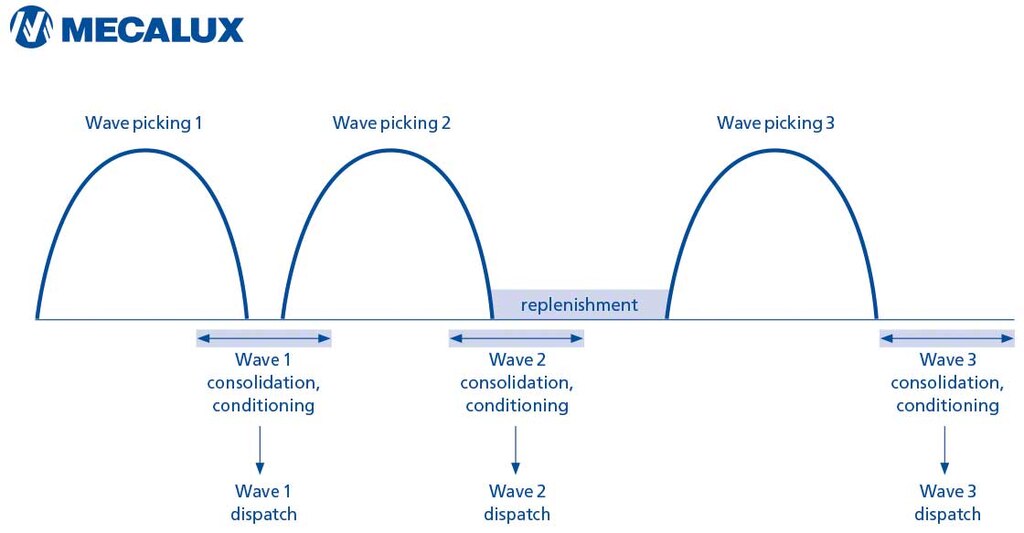
When to surf the pick wave…
Apply wave picking when:
- Your warehouse has a WMS or warehouse management system. Sorting requested lines and distributing them among operators is a highly complex process. Doing so manually would be almost impossible. And, you would definitely have your work cut out for you. The WMS ensures that no errors are made either in task organization or when executing each pick phase.
- The picking method is man to product, your warehouse is huge and the products are easily accessible.
- Your warehouse contains many SKUs and, above all, if these are lightweight; obviously, this is where overall improved productivity takes place.
- For some warehouses, this method may not cut it in terms of keeping pace (i.e. operations). So, before taking the plunge, study the nature of the demand. See if the wave formula can respond effectively or if you should opt for more flexible alternatives such as waveless picking.
Advantages of wave picking + a WMS:
A warehouse management system handles these wave picking tasks:
- It sorts each order line optimally (i.e. sets of orders to prepare during a wave) considering an enormous variety of logistic criteria.
- It allocates waves in a balanced way among your operators to make sure tasks are completed on time (taking individual workloads into account).
- It improves your response capability: the WMS monitors all processes and detects complications, keeping the warehouse manager informed so they can make quick decisions and easily reassign work.
- It monitors the progress of all your operations in real time to make sure the day’s schedule is being met.
As this is a very fluid method of preparing orders, it is important to adjust the WMS to the times, equipment and logistical variables of each specific warehouse. Software personalization is vital to smooth sailing during this process. If you want to know how our warehouse management system Easy WMS works, contact us and we'll explain its functionalities in detail.