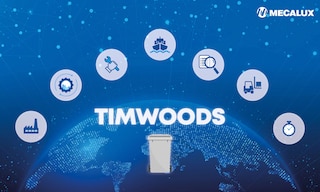
TIMWOODS and its importance for logistics
TIMWOODS is a tool used in business environments to avoid common errors such as non-value-adding steps, overproduction, unnecessary movements, and underutilization of employee talent. Collectively, these inefficiencies are known as the 8 wastes of lean.
What is TIMWOODS, and how is it related to lean?
TIMWOODS is a mnemonic acronym that helps businesses identify and remember the eight wastes or inefficiencies that, according to the lean method, can occur in factories, warehouses, distribution centers, and even offices when workflows aren’t well organized. By adopting lean practices and integrating them into their production plans, companies can add value to their final products or services and implement improvements across the board.
What does TIMWOODS mean? Each letter in TIMWOODS represents a specific type of waste: transportation, inventory, motion, waiting, overproduction, overprocessing, defects, and skills. They’re the areas businesses should focus on to boost their productivity.
TIMWOODS is part of the broader lean methodology, which is inspired by the Japanese philosophy of kaizen (continuous improvement). The goal is to cut costs and streamline supply chains by eliminating redundant processes. Lean principles can be applied across manufacturing, business management, and logistics processes.
What are lean wastes?
Lean wastes, or muda (Japanese for wastefulness), are non-value adding activities. They stem from poor production or management that could have been prevented through better organization. These inefficiencies can hinder productivity and drive up costs, so pinpointing and addressing them is crucial for running a profitable business.
The
Japanese engineer Taiichi Ohno first identified and categorized the wastes of TIMWOODS to eradicate them from work processes. Originally, his model included the seven most common wastes present in companies, with an eighth added later.
Examples of lean manufacturing in business
Several Mecalux Group clients have successfully incorporated lean manufacturing strategies into their workflows. Austrian company ALPLA, a packaging solutions specialist, applies the lean methodology at its Golborne plant in the UK. At this site, conveyors and automatic elevators streamline the movement of 2,500 pallets daily.
Another case is Motocard, a chain store specializing in gear and accessories for motorcyclists. The company equips its warehouse workstations with only the essentials — a computer, a printer, tape, scissors, and a cutter — enabling associates to fulfill as many orders as possible efficiently.
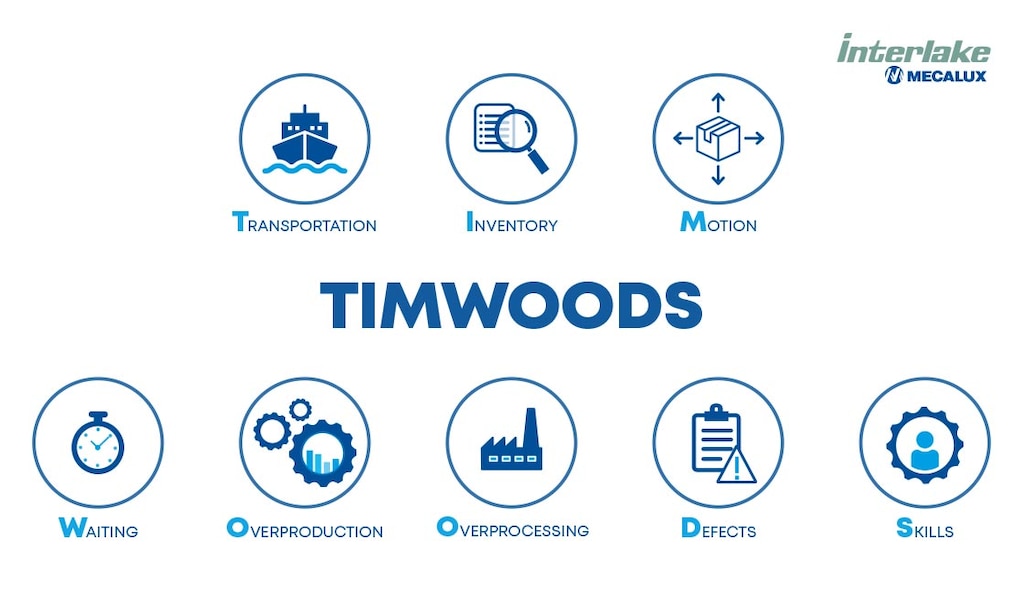
TIMWOODS: The 8 wastes of lean
The TIMWOODS (or TIM WOODS) list serves as a road map for combating inefficiencies:
- Transportation. Moving products from one point in a warehouse to another needlessly or without a clear purpose wastes both time and resources. Plus, excessive material handling can lead to damage or breakage, ultimately increasing inventory shrinkage.
- Inventory. Excess raw materials, partially finished products, and finished goods that are not immediately required affect profitability; they take up space that could otherwise accommodate other assets.
- Motion. Products, warehouse associates, and material handling equipment like forklifts can suffer unnecessary wear and fatigue from wasted movements. Warehouse automation helps minimize this issue.
- Waiting. Inordinately long shipping times can tarnish a company’s image. Likewise, idle time — when products or raw materials sit waiting to be moved or processed — results in losses and lowers productivity.
- Overproduction. Manufacturing too many products can lead to overstock. The best way to prevent this is through accurate demand forecasting, streamlined workflows, appropriate storage systems, and robust warehouse management software.
- Overprocessing. This involves performing tasks that complicate the workflow and fail to add value to the final product or service. Examples include superfluous paperwork, unclear separation of responsibilities, and duplicate record-keeping.
- Defects. Manufacturing defective products negatively impacts customer satisfaction. Moreover, it triggers additional costs, such as those linked to reverse logistics, refunds, and replacements.
- Skills. Wondering what the eighth waste added to Ohno's list is? It focuses on human capital within the company. Underutilizing employees’ knowledge, creativity, and skills is indeed a waste. That’s why it’s important to involve staff at all levels, encouraging them to share improvement ideas and contribute insights to help solve problems.
TIMWOOD waste examples
TIMWOODS waste can crop up in several areas of a warehouse. For instance, overly complex processes and poorly designed production lines or layouts result in transportation (T) waste. Flawed demand forecasting and the absence of warehouse management software can complicate inventory (I) control. Meanwhile, suboptimal storage systems or those poorly connected to production lines can cause delays and waiting (W). Furthermore, lifting heavy items due to a lack of equipment (e.g., forklifts) or having to travel to deliver documents wastes employees’ energy, contributing to motion-related waste (M).
Rooting out TIMWOODS from lean manufacturing
Maintaining perpetual inventory automates stock inflow and outflow tracking, preventing obsolescence. Businesses with logistics operations can monitor and optimize all processes and resources in their facilities — whether manual or automated — with the Easy WMS warehouse management system. Designed for medium-sized and large facilities, this solution ensures comprehensive, real-time inventory traceability, drastically reduces errors, and increases productivity, delivering a fast return on investment. Be sure to contact us for expert advice on this and other logistics and storage solutions.