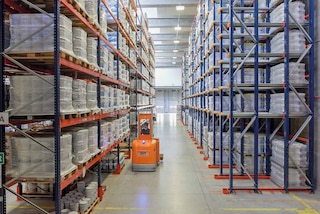
Chemical warehousing: challenges and success stories
Many companies rely on a variety of chemicals to carry out their business activity. Whether they contain raw materials, semi-finished goods or finished merchandise, installations dedicated to warehousing chemicals have to comply with strict safety requirements, as, in many cases, these goods are hazardous.
In our article, we’ll go over the main considerations to keep in mind when designing and equipping a warehouse for chemicals. In addition, we’ll provide you with real examples of solutions adopted in various projects.
Risks of warehousing chemicals on an industrial scale
Many of the risks present in warehouses derive from the characteristics of the goods they store. In the case of chemical warehousing, the hazard level depends on the following:
- Volume and category of chemicals stored.
- Organization and distribution of the chemicals in the storage installation.
- Storage conditions, in relation to both environment (temperature, humidity, etc.) and equipment (handling gear, containers, pallets, etc.).
- Employee working methods, linked to occupational risk prevention training.
Safety first
Chemical warehousing is regulated by specific safety regulations in each state. However, they are based on common regulations approved at the federal level. Let’s take a look at the main aspects to take into account for this type of storage:
1. Determine the chemical hazard level
Chemicals are shipped with Safety Data Sheets (SDS) that outline the product and required safety protocols, proper storage conditions, etc.
This information makes it possible to determine the chemicals’ hazard level. Subsequently, it’s necessary to count the volume of each type of chemical stored.
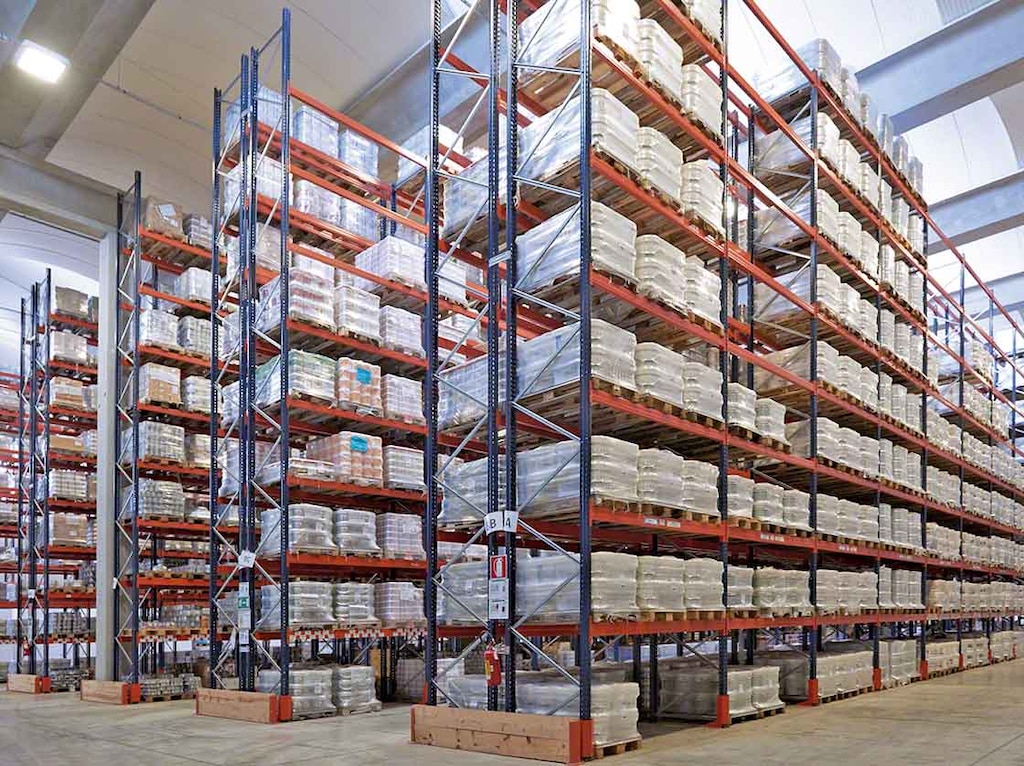
2. Ensure proper warehousing conditions
Optimal storage conditions are related to the kinds of chemicals to be stored. Chemicals should always be segregated and stored according to their incompatible chemical and physical characteristics. Basic hazard groups include: acids, bases, flammables, oxidizers, toxics, peroxide forming chemicals, pyrophoric forming substances, water reactive chemicals, and explosives.
With the chemicals classified and identified as belonging to the various groups, we now can examine
some guidelines on the safety conditions to be met by warehouses in the following areas:
- Design and structure of the installation: these set the safe distances required between chemicals, compatibility, storage location (whether indoor or outdoor, or on industrial racking, in bays, or in lockers), recommended handling equipment, and stacking standards, among other factors.
- Containers and receptacles storing chemical products: IBCs (intermediate bulk containers) are normally used for bulk goods. Generally, containers for chemicals are made of steel or stainless steel (advantages of which include their low maintenance and high durability and resistance) and high-density polyethylene (HDPE, a light, flexible, low-temperature-resistant material).
- Systems for monitoring storage conditions (temperature, humidity) and protection systems (fire prevention) needed in the installation as part of its warehouse safety and risk prevention policy.
- Periodic inspection requirements: once operational, the installation storing chemicals must undergo regular inspections to ensure that these safe conditions are maintained.
3. Study chemical compatibility to ensure safe storage
When designing the layout of your warehouse, it’s crucial to assess chemical compatibility:
- Storing chemicals without the required safety measures in place could expose the installation to a high risk of accidents, since the substances could mix and react with dire consequences.
- In the event of an explosion, fire, or the generation of toxic gases, the presence of incompatible chemicals can accelerate combustion and create additional difficulties in resolving the problem.
As a general rule, only chemicals in the same hazard category should be stored together.
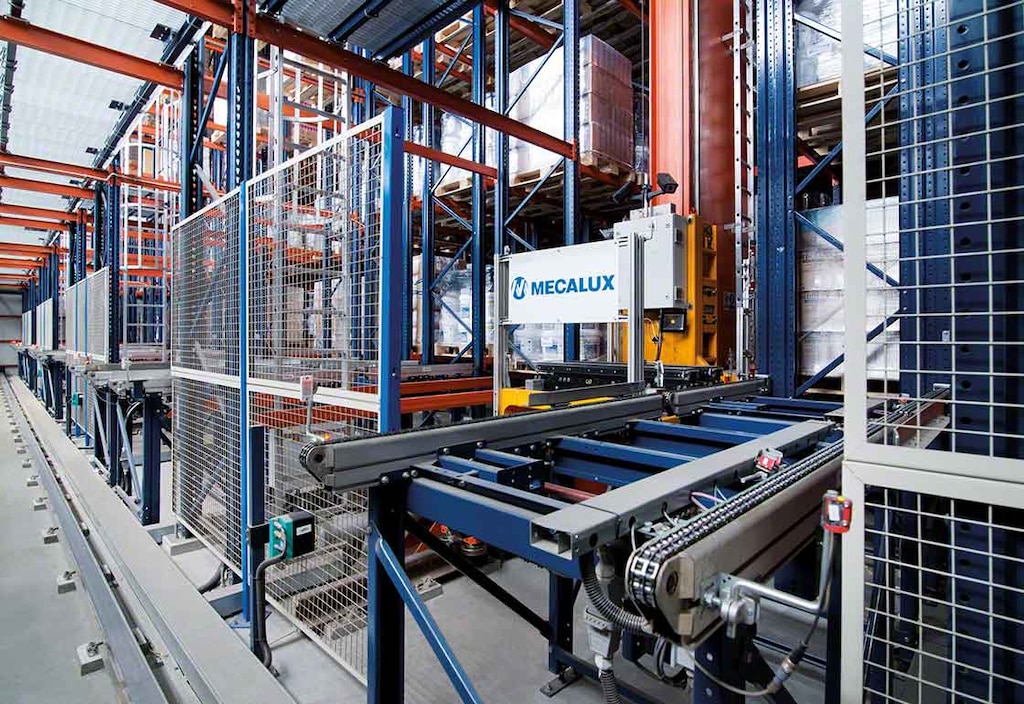
4. Guarantee safe handling of chemicals
Companies have to ensure that chemicals in storage installations are moved with the utmost control and safety. In this vein, two factors should be emphasized:
- Adequate occupational risk prevention training for employees: operators must know the properties of the chemicals stored, which PPE (personal protective equipment ) they need to use, the danger posed by improper handling of the chemicals, and how to respond to potential incidents.
- Clear load-handling procedures: handling equipment is employed in all operations involving the loading, unloading, storage, and transportation of chemicals. Therefore, working procedures have to take into consideration the dangerousness of the products and adjust the safety measures to take in each case.
5. Develop a chemical warehousing emergency plan
Each storage installation must have a self-protection and emergency plan to implement in the event of an accident (fire, spill or leakage of chemicals, etc.). This plan is included in the warehouse design phase and contains instructions on how emergency services and installation employees should proceed.
How do you limit risks when storing chemicals? Strategies and success stories
In warehousing logistics, part of the solutions for mitigating risks in these types of installations are centered on three aspects:
1. Zoned layout for chemical warehouses
Due to chemical compatibility requirements, installations that store these substances have clearly delineated areas, each of which functions independently for safety as well as operational reasons.
This type of zoned layout can be seen in the facilities of Italian company Cromology, which we equipped with standard and drive-in pallet racking. Notable emphasis was placed on safety, with the installation of:
- Signage for internal traffic: rails were placed in the storage aisles to minimize the risk of impact between the forklifts and the racks.
- Transverse emergency underpasses: these run crosswise through the lines of racking. They help to decongest internal traffic and serve as emergency exits. In addition, the bays at the top of this aisle are lined with mesh to protect the passageway from the potential fall of goods.
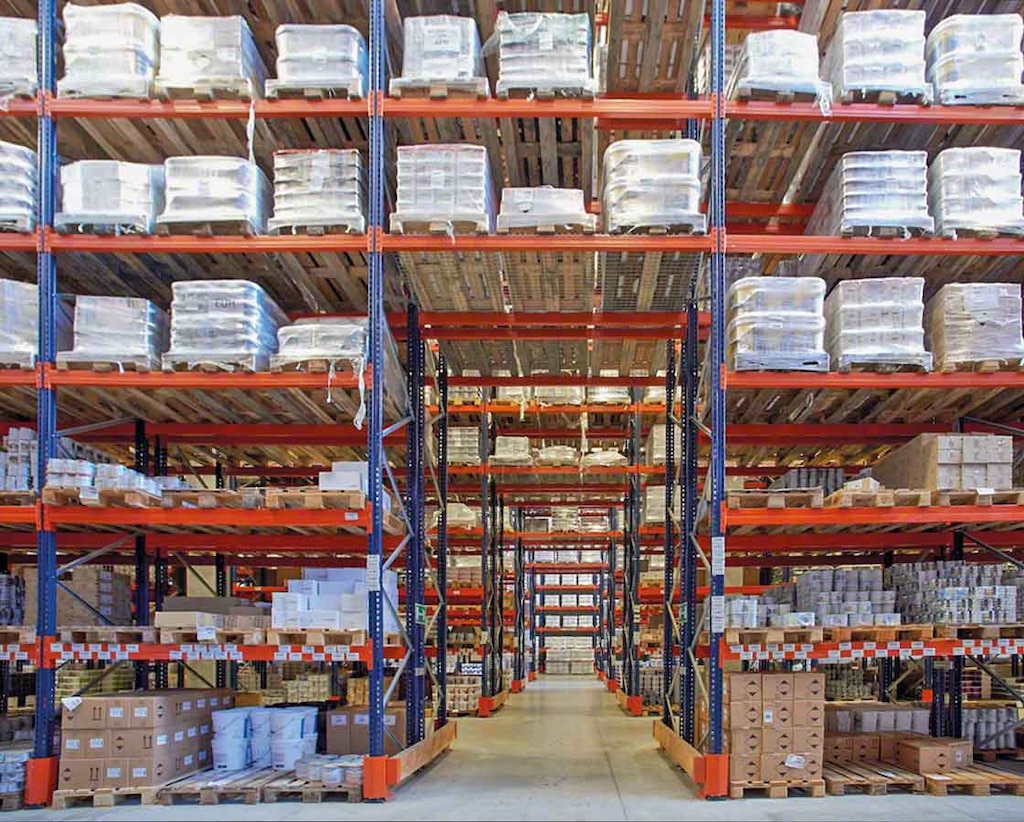
2. Automated handling of chemicals in warehouses
In many chemical installations, operations have been automated to make goods handling safer and more accurate. Chemical multinational BASF entrusted us with designing and outfitting its new warehouse in Brazil.
There, we built a fully automated installation with stacker cranes and conveyors for pallets, in addition to incorporating automatic picking robots. The rack-supported structure provides the installation with maximum stability. The automatic elements, governed by Galileo control software and the Easy WMS warehouse management system, contribute towards eliminating human error from the movement of chemicals.
3. Thorough control of stock status and characteristics with the WMS
As described above, information on each type of chemical stored is essential for controlling the distribution of these products and complying with the compatibility rules established by the regulations. In automated installations, like the one we set up for Lakma in Poland, Easy WMS warehouse management software plays a fundamental role:
- It provides real-time inventory data in terms of both stock levels and characteristics. Examples include information on receipt/dispatch date, goods traceability, staff who handled the product, hazard level, and production batch, among other logistics parameters.
- It manages the selection of locations intelligently by establishing rules that control entries and exits of products to and from the appropriate warehouse area according to certain logistics criteria. As handling is automated, Easy WMS transmits these orders to the control software that executes them.
Solutions for the industrial warehousing of chemicals
At Interlake Mecalux, we’ve worked with chemical warehouses of companies all over the world, helping them to meet the challenge of storing and handling these kinds of goods safely. Would you like us to walk you through the process of designing, remodeling, or equipping your installation? Feel free to get in touch. One of our expert consultants will analyze your case in depth to come up with the best solution.