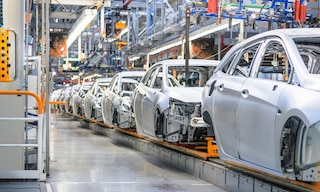
Automotive logistics: Key challenges and how to tackle them
Automotive logistics is a constantly evolving world — a complex machine that keeps car manufacturers moving. Driven by technological innovation, this sector demands extremely efficient, accurate, and fast processes to keep pace with an ever-changing, high-pressure industry.
In this post, we explore what automotive logistics is, the processes behind every vehicle, and the pivotal role of warehousing in maximizing competitiveness.
What is automotive logistics?
Automotive logistics involves planning, managing, and executing material flows from suppliers to production plants and transporting finished vehicles to dealerships or end customers.
Every car is the result of a tightly managed, carefully choreographed logistics process. From the smallest components to the finished product, automotive logistics ensures every part reaches the right place at the right time, like clockwork. Without precise coordination, vehicle production would simply grind to a halt.
Automotive logistics challenges
The automotive industry runs on tight timelines and high efficiency. In a globalized landscape shaped by digital transformation and the shift to cleaner energy, companies need to be more agile than ever to navigate complex, fast-changing environments.
Some of the main hurdles in automotive logistics include:
- Global operations. Coordinating with international suppliers and manufacturers introduces risks such as delays and resource planning issues.
- Component shortages. Missing parts (e.g., microchips or batteries) can disrupt production, stall assembly lines, and cause significant delays.
- Just-in-time manufacturing. Every component needs to arrive at the production lines at exactly the right moment. Even a minor disruption can lead to costly downtime.
- Adoption of new technologies. Automation, predictive analytics, and AI are becoming vital tools for boosting efficiency, reducing errors, and anticipating disruptions.
- Lack of visibility. A single car can contain more than 30,000 parts. Without real-time visibility, it’s nearly impossible to prevent issues, respond quickly to setbacks, or guarantee full traceability.
- Transition to electric vehicles. The move toward EVs brings new logistical challenges, particularly in transporting, storing, and safely handling batteries and other components.
- Sustainability and emissions reduction. With stricter environmental regulations and growing public concern, automakers are under pressure to optimize their logistics processes to lower their carbon footprint.
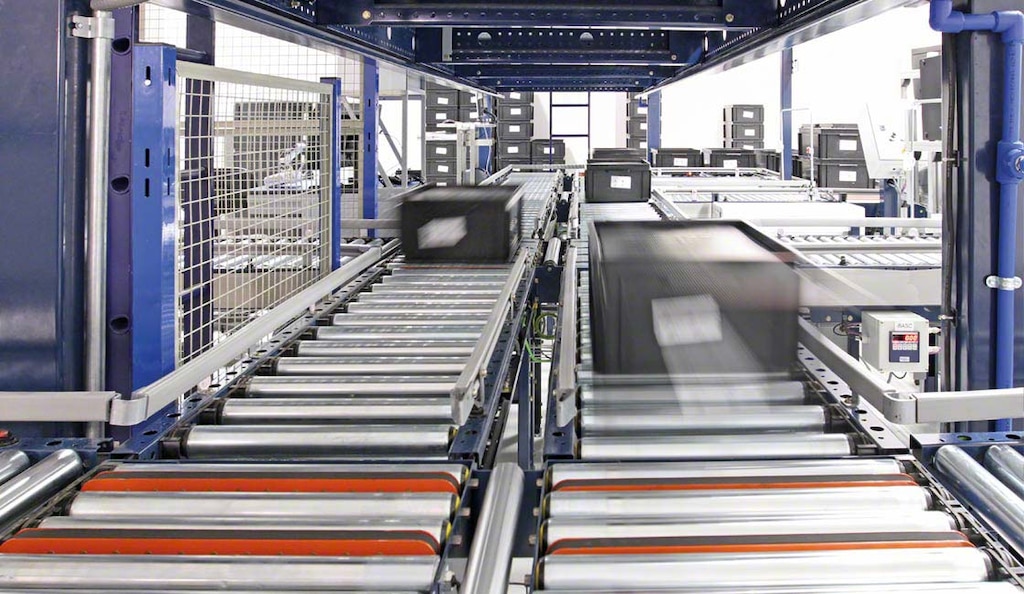
How does automotive logistics work?
The automotive supply chain starts with raw material suppliers and ends with handing the keys to the customer. It involves:
- Raw material procurement
- Parts and component manufacturing
- Assembly
- Storage of finished vehicles
- Automobile distribution
- Delivery to dealerships
Everything begins with tier-three suppliers, which provide basic materials like steel and aluminum to tier-two suppliers. These companies turn those materials into items such as sensors and connectors, which then feed tier-one suppliers making major systems (engines, transmitters, or advanced electronics).
Once complete, these components arrive at the automaker’s plants for vehicle assembly. To keep production moving, most manufacturers implement a just-in-time logistics model: materials appear in the right quantity at the right moment, avoiding excess inventory and costly bottlenecks.
Automotive logistics doesn’t stop at the end of the assembly line. It also covers replacement-part distribution to repair shops and service centers that keep vehicles on the road.
Finished cars are transported to dealerships and eventually sold to customers. When a vehicle reaches the end of its service life, logistics takes on one final task: collecting, dismantling, and recycling materials to support the industry’s ambitious circular economy goals.
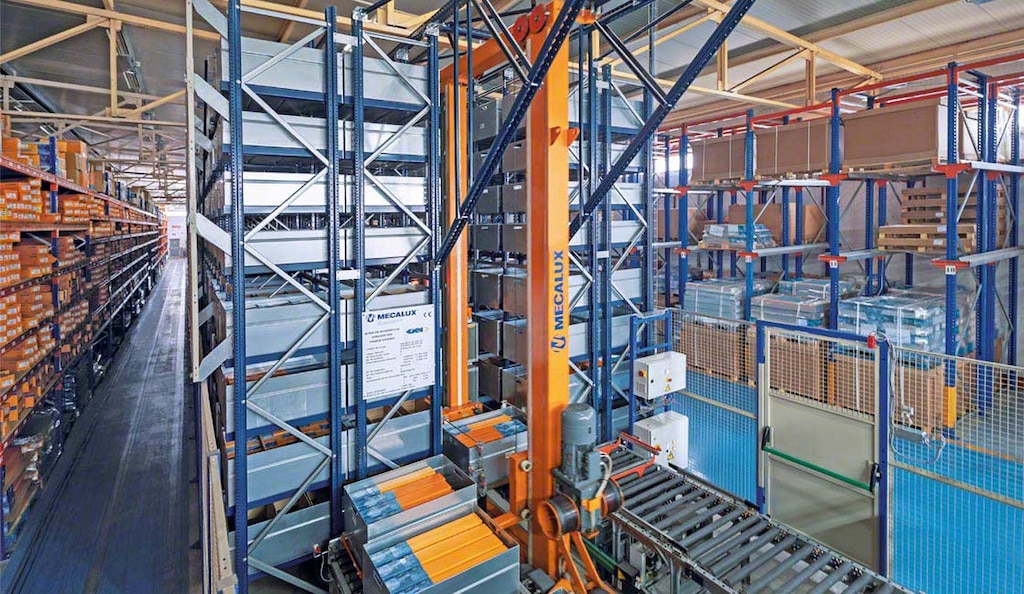
The role of warehousing in automotive logistics
Within automotive logistics, the warehouse acts as the nerve center for organizing and distributing components — for both vehicle production and aftermarket support.
Sound warehouse management ensures parts reach the line in the right sequence when required, especially in just-in-time environments. To hit those targets, many businesses invest in advanced automation and warehouse management solutions like those offered by Interlake Mecalux. They streamline material flow, improve traceability, and cut response times.
These key warehouse operations make sure components are available when and where they’re needed:
Goods receipt and sorting
Incoming parts from suppliers are inspected, logged, and strategically positioned for swift retrieval.
A case in point is the automated storage and retrieval system (AS/RS) in Schaeffler Iberia’s warehouse in Elgoibar, Spain. The needle roller bearings used in engine production pass under a scanner that identifies each unit and feeds the data into the logistics software. The AS/RS is purpose-built for KLT totes, the standard container across Schaeffler’s plants, with every rack, conveyor, and stacker crane tailored to that format.
Inventory management and traceability
Monitoring inventory levels, avoiding stockouts, and ensuring traceability of every component are critical in any automotive warehouse. Many companies rely on digital tools for real-time visibility.
For example, Distrimotos and Integrando, Colombian distributors of spare parts for auto repair shops, gas stations, and the automotive industry, use our company’s Easy WMS warehouse management system to identify each item. Associates read goods with RF scanners, capturing exact locations and maintaining strict inventory control throughout all logistics operations.
Order picking
After storage, parts are picked and staged to match production requirements. As speed and accuracy are paramount, more and more businesses are adopting WMS technology to minimize errors and meet tight deadlines.
Carglass, a leader in vehicle window repair, replacement, and recalibration, leverages Easy WMS to prevent picking mistakes. Its facility in Celje, Slovenia, manages windshields sent to repair shops. They look almost identical, so the system provides associates with step-by-step RF instructions, slashing errors, returns, and delays.
Production line supply
Once ready, components move to assembly. Many plants automate this flow with autonomous mobile robots (AMRs), conveyor systems, or automated guided vehicles (AGVs) to guarantee uninterrupted material supply and faster turnaround.
For instance, Renault’s plant in Seville, Spain, uses AGVs to feed transmission assembly lines with gears. Easy WMS synchronizes the warehouse with production processes, preventing mishaps that could halt the line and drive up costs.
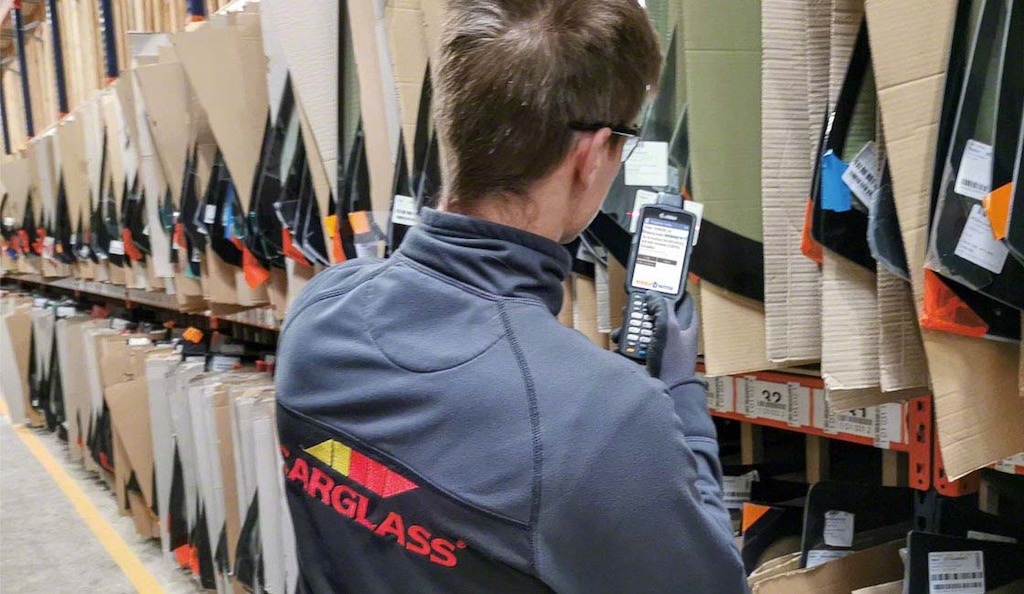
Automotive logistics: Automation brings reliability
Automotive logistics leaves zero room for error. Every link in the chain must run perfectly in sync. The warehouse is at the center, organizing inventory so the industry never misses a beat.
Automation and advanced management software solutions optimize material flow while tackling industry obstacles head-on, from component shortages to the transition toward greener mobility.
Automotive logistics in 5 questions
What is automotive logistics?
Automotive logistics coordinates the flow of materials, parts, and vehicles along the entire supply chain, from suppliers to dealerships. It’s the behind-the-scenes process that puts every car on the road.
What are the biggest challenges in automotive logistics?
Global supply chains, component shortages, just-in-time manufacturing, the shift to electric mobility, and tougher sustainability demands top the list.
What role does warehousing play?
The warehouse is the hub for organizing, sorting, and distributing parts for car manufacturing and aftermarket service. Smart management keeps production lines and repair centers fully stocked.
Which technologies are used in automotive logistics?
Internal-transport automation and warehouse management systems boost traceability, reduce errors, and raise operational efficiency.
Why is digitalization crucial in automotive logistics?
Real-time data drives better decisions, guarantees traceability, and flags issues before they snowball. With tools such as warehouse management systems, companies streamline processes, minimize errors, and stay agile in a rapidly changing industry.