
Automated guided vehicles warehouse: the need for speed
Automated guided vehicles are a common solution for automating movements of goods between different zones in the warehouse. These driverless machines make use of different systems to know which routes they need to follow. In the logistics sector, these vehicles often replace manual handling equipment, streamlining goods flows with continuous, repetitive movements.
Since their invention in 1953 by engineer Arthur Barret, their configuration has evolved: from the “Guide-O-Matic” ― the first driverless vehicle ― to the popular wire-guided forklifts.
What are automated guided vehicles?
Automated guided vehicles (AGVs) are automated robots that transport goods between two points in a warehouse ― or between two connected systems ― without the need for a driver. These vehicles speed up the flow of heavy materials by moving along a pre-designed circuit.
These transportation solutions are increasingly present in industrial environments: they ensure that automated storage and retrieval systems (AS/RS) are agile and safe while reducing load movement times. This is illustrated by a study from consulting company Grand View Research, which indicates that the automated guided vehicle market size reached $3.39 billion in 2020.
The report also says that this market is slated to grow at an annual rate of 13.8% up to 2028. The reason? These machines are an agile solution for, among other things, replacing traditional forklifts to load and unload trucks, connecting the storage zone with the production lines, and even moving products between the different picking areas.
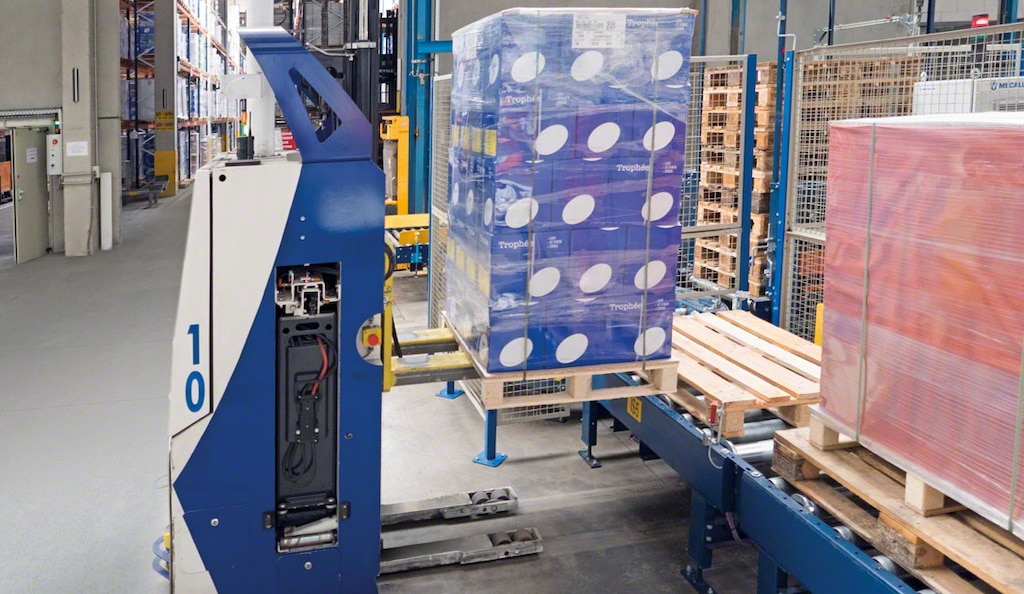
Automated guided vehicle navigation systems
Automated guided vehicles can be classified according to the guidance system that facilitates the movement of the equipment:
- Wire-guided: the equipment moves by means of a guide wire embedded in the warehouse floor. This method is only efficient when flows of goods are continuous and repetitive, as any change would require construction work to move the guide wire.
- Machine vision: the vehicle uses artificial intelligence (AI) to decide on the ideal route. This is done with the help of machine vision cameras with 360° imaging that can identify all elements in the vehicle’s environment.
- Collision avoidance with optical sensors: the vehicles move via a reflector strip placed along the route to be followed by the equipment. The vehicles are equipped with a retroreflector, i.e., a component that detects light and allows the vehicle to identify the path and follow the preset route. As opposed to wire-guided systems, this requires no prior construction work.
- Laser target navigation: the equipment is outfitted with a laser device that, by means of scanning, determines its exact position in the warehouse according to the map stored in its memory. With this navigation system, it isn’t necessary to install wires.
- Vision guidance: automated guided vehicles that navigate via vision guidance don’t require the installation of any elements other than the handling equipment. The vehicle incorporates a set of sensors (cameras, ultrasound, or other technology) to create a virtual 3D map of the warehouse and, thus, travel safely.
Types of automated guided vehicles
Automated guided vehicles come in many varieties. These are the most relevant:
- Unit load AGV: automated transportation system designed to carry a single load per journey (pallets, reels, boxes, containers, or other individual units).
- Automated guided forklift: self-driving forklift capable of moving one or several pallets. The forks of these automatic machines are equipped with sensors to ensure the safe loading and unloading of goods.
- Tugger AGV (tow tractor): vehicle charged with moving other non-motorized systems, e.g., the carts of a tugger train. This solution is configured with lift platforms, motorized rollers, or a trailer system to facilitate the loading and unloading of product from the tug.
How does an automated guided vehicle work?
Automated guided vehicles are able to move around the facility via the combination of a sensor-guided system and software, which can be integrated in a warehouse management system (WMS).
The automation process ensures that the transportation system always moves along a predetermined route at a controlled speed. Nevertheless, these machines are normally outfitted with additional components to guarantee the integrity of the operators, of the goods, and of the vehicles themselves. These parts can include bumpers, scanners, and smart sensors to detect nearby movements, among others.
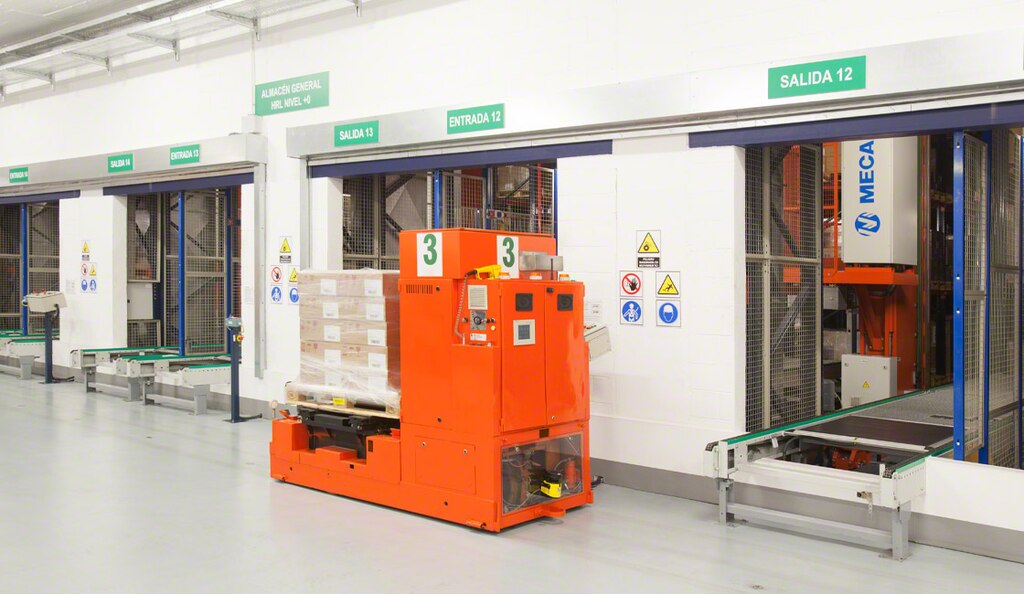
Automated guided vehicles: pros (and cons)
Automated guided vehicles bring a number of benefits to warehouses, enabling the following:
- Guarantee uniform flows of goods: these vehicles have a prefixed route that ensures the continuous movement of loads between two areas in a logistics facility.
- Allow 24-hour work cycles: this transportation solution automates the flow of goods, so operators can dedicate their time to higher value work.
- Limit the risk of accidents: automated guided vehicles incorporate safety systems to optimally navigate the warehouse, avoiding interaction with operators.
Automated guided vehicles do, however, have their disadvantages:
- Highly inflexible solution: except for those guided by AI, most automated guided vehicles still move by means of rigid systems — laser- or wire-guided — requiring uniform flows of goods.
- Insufficient system for high-density warehouses: automated guided vehicles are a unit load transportation system, making them unsuitable when dealing with high order density scenarios. In this case, alternatives include automated storage and transportation solutions such as pallet conveyor systems or miniload systems (AS/RS for boxes).
Automation solutions: when to use automated guided vehicles (and when not to)
Automated guided vehicles are often implemented in industrial settings, especially with production centers employing work methods such as lean manufacturing or just-in-time. This is because this transportation solution covers the distance between the warehouse and the production center, supplying raw materials to the production lines.
Nonetheless, in facilities with a larger number of orders, automated guided vehicles might not meet the logistics needs of the warehouse, since these machines have a limited load capacity. Meanwhile, other automated solutions, such as pallet conveyor systems, are capable of maintaining continuous flows of goods between two points in warehouses with high load volumes.
Automated guided vehicles usually complement automated storage and transportation systems, performing specific functions, for example: moving heavier products between two points in the facility, loading and unloading product at the entrance to an AS/RS, or connecting the warehouse with the production buffer outside the building.
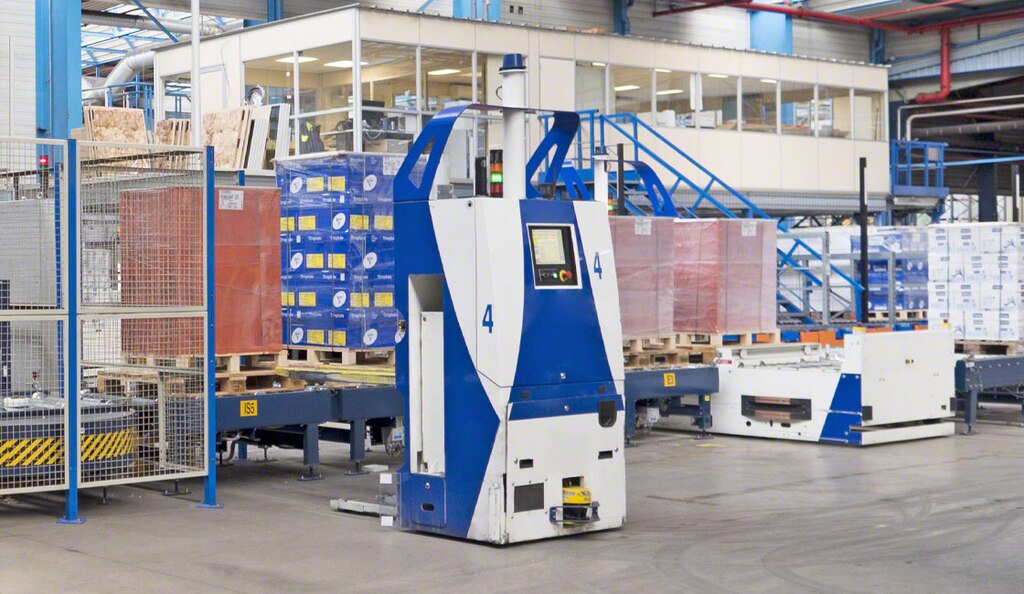
Automated guided vehicle warehouse examples
Automated guided vehicles constitute a goods transportation solution that streamlines load flows. For instance, French paper manufacturer Clairefontaine implemented these vehicles to transport loads internally in its warehouse, enhancing safety in the aisles. The logistics center, coordinated by Easy WMS, the WMS from Interlake Mecalux, consists of three storage systems with fully automated operations.
Automated guided vehicles serve a similar purpose in the Kern Pharma facility in Terrassa, Spain: the equipment picks up pallets from the production lines and deposits them on the conveyors feeding into the rack-supported warehouse built by Mecalux. In this case, the vehicles are laser-guided.
Swiss pharmaceutical company Novartis also needed to streamline its logistics operations and flows of goods in Poland. To do so, the Mecalux Group built a new 89' tall automated clad-rack warehouse near the production center. A set of automated guided vehicles transports goods between the two facilities: “Automating was a priority for Novartis, including the in-warehouse transportation,” says Tomasz Marchewa, Supply Chain Manager at Novartis.
These vehicles also automate the connection between the logistics facility and the production center at Renault. Coordinated by the warehouse management software from the Mecalux Group, the operators deposit the raw materials for each production order on the warehouse racks. The automated guided handling equipment then moves them to the production center.
Automated guided vehicles: agility in moving loads in the warehouse
Automated guided vehicles could be the first step towards automation: they take the place of conventional forklifts in carrying out repetitive movements, allowing operators to focus on tasks that add more value. But these machines should complement other transportation and storage solutions, performing tasks geared more towards flows of heavy goods or to loading and unloading products.
Interested in automating part or all of your warehouse? Don’t hesitate to get in touch. One of our expert consultants will analyze your needs and advise you on the best solution for your company.