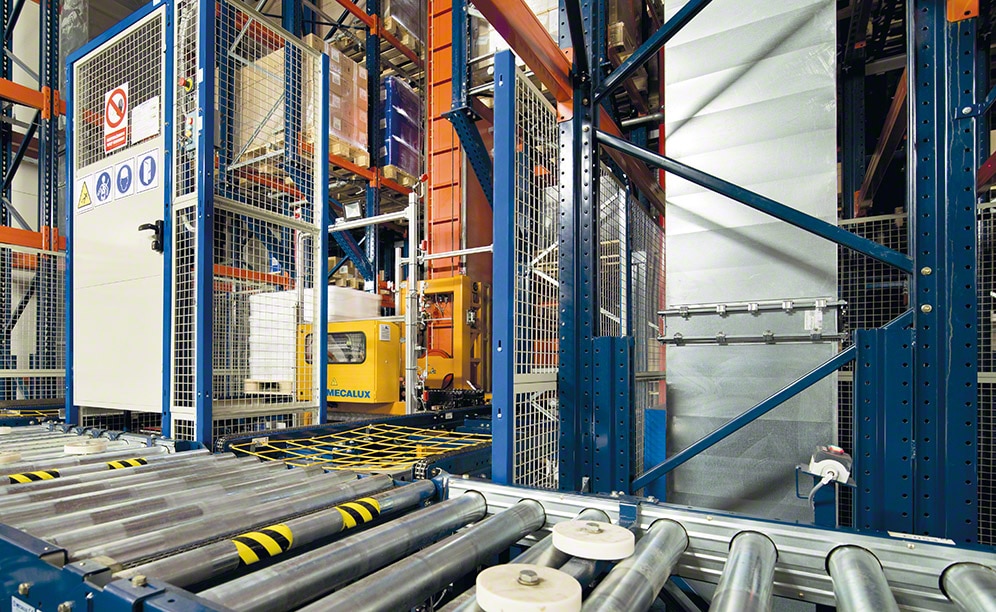
Novartis automates its supply chain in Poland
The supply chain of a pharmaceutical business stands out for its strict product control
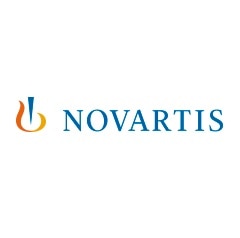
In the pharmaceutical industry, exhaustive control and stock security help preserve the qualities of medicines and eliminate any sort of error in all the processes this involves. With Interlake Mecalux’s help, the multinational Novartis just opened a new clad-rack warehouse in Poland with a 14,304-pallet capacity and fully-automated operations.
Health care leader
With its headquarters in the city of Basel (Switzerland), Novartis is a pharmaceuticals and biotech multinational company. This company opened in 1996, the result of the merger of three major companies: Geigy, which sells dyes and chemical products; Ciba, a dye-maker; and Sandoz, a chemicals company.
If there is something these three companies have in common, and which still survives today in Novartis, it is the passion for advances in science and leveraging this knowledge. All of this is done to develop products that contribute to human progress and a better quality of life for people.
Novartis produces and sells a huge variety of medication and treatments such as generic medicine, vaccines, and cancer-fighting drugs. Over the last few years, it has expanded its presence in emerging markets like Asia, Africa and Latin America, since there is a growing demand for access to health care and quality medication.
Challenges in storing medication
The health care sector has immersed itself in an unprecedented transformation to adapt to economic adjustment policies and new market trends. Consequently, companies like Novartis are faced with the challenge of increasing efficiency and optimizing costs, while also maintaining the quality of their drugs and responding to their customers’ needs.
Novartis is known for continuously investing in the betterment of all its processes, as well as revamping its manufacturing and logistics centers to ensure that its medicines stay fully effective.
The company needed an ample storage capacity for its center allocated to blister-packing medications in Stryków (Poland) to reinforce “the evolution of Novartis in this country, increase sales and respond to growing market demand for bubble-packed medication,” explained Tomasz Marchewa, Supply Chain Manager at Novartis.
In his own words, “the new warehouse must form an integral part of the modern packing center of Novartis in Stryków.” All finished product blister-packing takes place in this center, ready to be distributed. On this basis, “The decision to build the warehouse was also motivated by the desire to maximize productivity in the packaging process,” pointed out Tomasz Marchewa.
The location of the warehouse has a direct effect on the supply chain of the whole company. However, in the case of pharmaceutical companies, it also has repercussions on the health of human beings. It is essential that medicine distribution be as fast as possible, so that customers can get their medications exactly when they need them. In this vein, Novartis plays with a home-field advantage and the location of its warehouse in Poland is unparalleled; it is set up in the city of Stryków, in Central Poland, “very close to main highways, something that represents a clear added benefit,” mentions Tomasz Marchewa.
That said, storing and distributing pharmaceutical products is no easy matter because they must be housed in perfect conditions to maintain their qualities and make sure they stay sufficiently effective. For example, each medication is stored at a different temperature that, as a general rule, rarely exceeds 77 ˚F.
Fully automatic operations
Interlake Mecalux has constructed a new automated clad-rack warehouse that is 21,312 ft² and 89' high right next to the manufacturing center. For that matter, the two buildings are optimally connected together through a tunnel. On one side, the warehouse sends any required semi-finished products to manufacturing and, on the other, it receives the finished products.
The warehouse comprises four, 230' long aisles with double-deep racking on each side that provide a capacity for 14,304 pallets. Pallets hold finished products, semi-finished products, blister-packs and packaging. The warehouse management system (WMS) of Interlake Mecalux, the Easy WMS, was installed to distribute this variety of merchandise correctly. The software is responsible for assigning a location to each product as per their characteristics.
The stacker cranes run inputs and outputs of the goods from the items’ corresponding locations, according to the WMS’s instructions. They operate at a travel speed of 524 ft/min and 150 ft/min when in a lifted position. Each one of these machines can produce 24 combined cycles (24 pallets in and 24 pallets out), which “promotes better work efficiency and guarantees continuity in the processes carried out in the manufacturing center,” reflects Tomasz Marchewa.
Automating all processes has brought about significant gains for Novartis. The supply chain manager of Novartis highlights, above all, “the increased security, the cuts in maintenance costs, the control over all movements, the expanded storage capacity compared to other traditional storage systems and the reductions in personnel costs.” Furthermore, by automating all movements, it is unnecessary for the operators to deal directly with the goods, which translates into better hygiene and safety for both the workers and the products (an invaluable part of processing medicines).
According to Tomasz Marchewa, “the warehouse is very modern and gives us the storage capacity we needed.” Meanwhile, in a multinational the size of Novartis, it is imperative to always be looking ahead at future growth prospects. As such, it has reserved a space to expand when the moment presents itself.
Warehouse linked to manufacturing
The warehouse has two levels with distinct functions and operations:
Bottom floor
Products are received here, and then stored. These might be products supplied by providers or those flowing from other Novartis plants.
Additionally, dispatches and distribution of finished products are carried out here, all ready to be sold in more than 60 countries worldwide.
Upper floor
Here is where the warehouse connects to the manufacturing center. Automatically guided vehicles (AGVs) are used to transport the merchandise between the two installations. The reason for including these machines, mentions Tomasz Marchewa, is because “automating was a priority for Novartis, including the in-warehouse transportation.”
These forklifts carry out the functions that, in an unautomated warehouse, would be done by operators via traditional forklifts. In addition to the speed and safety afforded during movements, “the use of these forklifts lets us completely free up space and gangways,” he adds.
Product box packaging is done on this level. The AGVs move the goods to an automatic stretch wrapping machine that ensures the load’s stability. Onsite they also print labels and stick these on the pallets so they can be identified.
Tomasz Marchewa - Supply Chain Manager of Novartis
“Choosing Interlake Mecalux to build the automated rack-supported warehouse
was driven by factors such as the international experience this company
has in a multitude of diverse projects —both nationally and abroad—, its very efficient local service, the enticing price and that component manufacturing takes place in Poland, something that is highly appreciated.”
Advantages for Novartis
- A modern packaging centre: for Novartis, it was a top priority to set up a zone to blister pack finished products coming from the manufacturing center and one that would be backed by automated storage solutions.
- Top productivity: all warehouse operations are fully automatic. In doing so, it ensures the inflows and outflows that Novartis needs to supply its customers.
- Increased security: automation means operators are not required to handle the goods, which prevents errors and guarantees a high level of security.
Automated rack-supported warehouse in Poland | |
---|---|
Storage capacity: | 14,304 pallets |
Pallet size: | 32" x 48" |
Max. pallet weight: | 1,543 lb |
Racking height: | 89' |
Racking length: | 230' |
No. of stacker cranes: | 3 |
Gallery
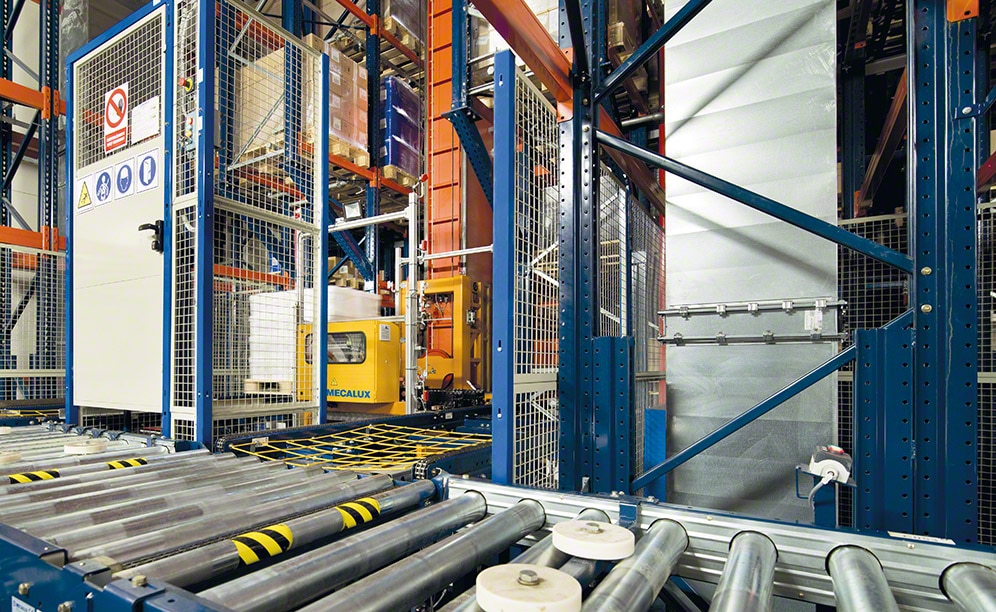
The automated clad-rack warehouse of Novartis in Poland
Ask an expert