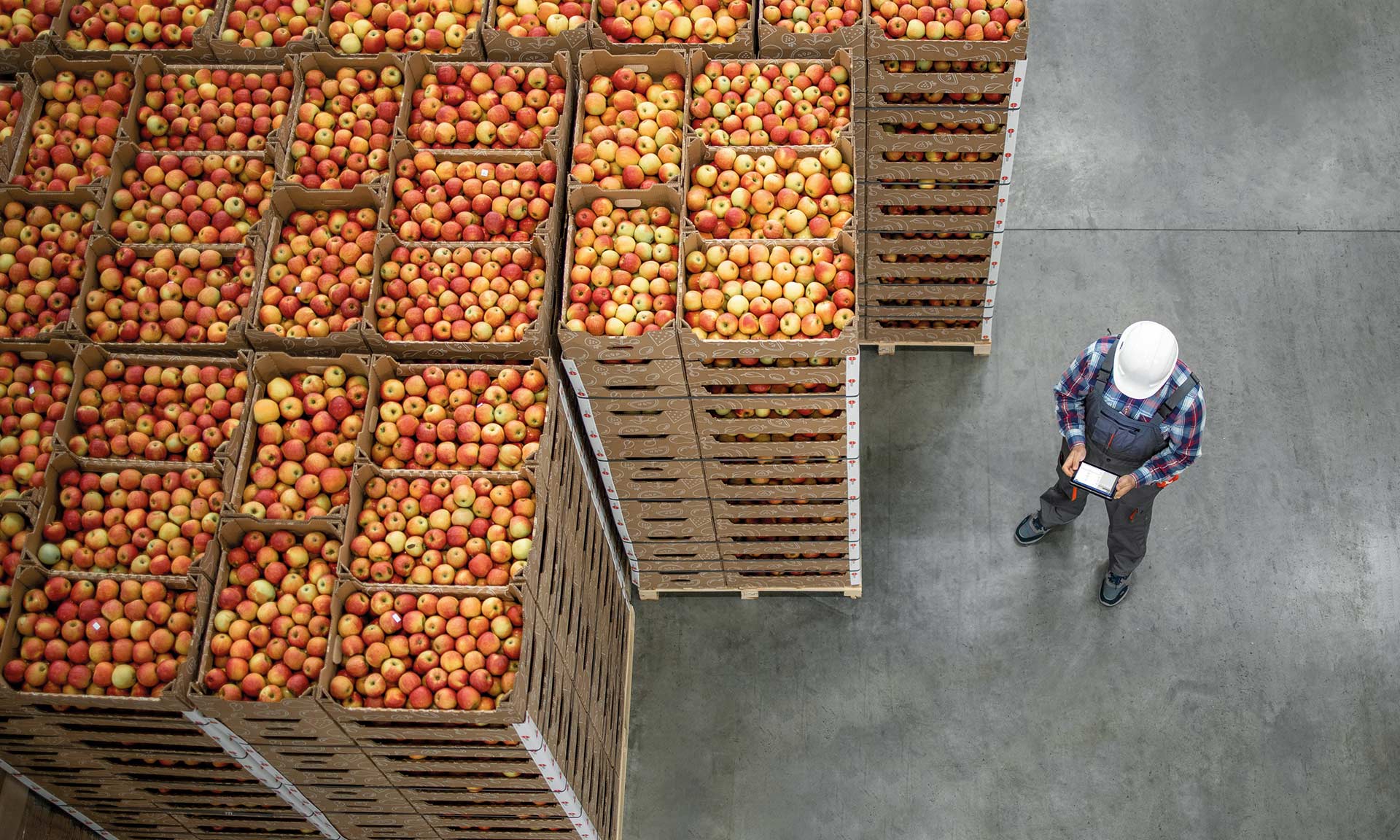
Megafin (3PL) digitalizes one of Colombia’s largest warehouses with Easy WMS
3PL provider Megafin digitalizes its logistics center in Colombia with Mecalux’s Easy WMS warehouse management software.
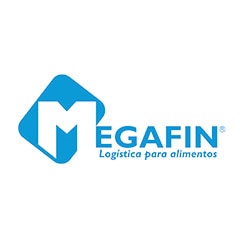
3PL provider Megafin has digitalized its logistics center in Colombia with Mecalux’s Easy WMS warehouse management software. Easy WMS organizes goods taking into account the food type, expiration date, and ideal storage temperature.
Megafin: logistics for food companies
Megafin is a third-party logistics (3PL) provider that manages products for Agrofrut, a leading Colombian manufacturer of tropical and exotic fruit, and for other food-industry companies. Megafin’s logistics center in La Estrella is one of Colombia’s largest, with a surface area of over 1.2 acres. The facility houses goods at three different temperatures: frozen (9,000-plus tons), refrigerated (550-plus tons), and ambient (330-plus tons). The Megafin center also has 12 freezer warehouses, 3 freezing tunnels, and 13 loading docks.
CHALLENGES
|
SOLUTIONS
|
BENEFITS
|
---|
The logistics operations of 3PL provider Megafin are complex as well as demanding. In its day-to-day, the business manages a wide range of products — mainly poultry, pork, ice cream, vegetables, and pulps — for more than 30 clients. Its main challenge consists of storing each item at the correct temperature and distributing it at the right time.
In response to the rising demand in recent years, the company sought to overhaul its entire supply chain. “Our number one priority is to provide our clients with the best possible service. To do so, we turned to technology. Innovation is part of our DNA; it’s the only way we can continually strive for excellence,” says Rogelio Betancourth, Logistics Manager at Megafin.
When it opened the logistics center in La Estrella, Colombia, in 2010, Megafin knew it had to digitalize all its processes. “We wanted a WMS that would ensure effective traceability of food. In our sector, monitoring perishable products in real time is a must for storing goods at proper temperatures and maintaining the cold chain,” says Betancourth.
Thus, the company installed Easy WMS, the warehouse management software from Mecalux. The system controls food items from the time they are recorded in the receiving area until they are sent to production or distributed to end customers. “Our operators are faster, as they receive instructions from Easy WMS via their RF scanners. With this working method, we’ve also eliminated errors,” says Betancourth.
Functionalities for logistics expansion
The food industry requires safe, effective operations that guarantee that products are in good condition when they reach the hands of end customers. By digitalizing its logistics processes, Megafin now handles its stock efficiently and without errors. Nevertheless, as the business grew and logistics operations became more challenging, the 3PL provider needed more flexibility. “When our client portfolio started to expand and we began filling more orders, we decided to upgrade our software and add features that would allow us to meet our clientele’s changing needs,” says Betancourth.
Recently, Megafin updated its logistics center with the latest version of Easy WMS. “The system was installed without interfering at any time in the operation of the warehouse. No shipments were delayed during the go-live days,” says Betancourth.
The Mecalux technical team first defined all the functionalities the software should include. With this information, the system was configured and developed at the Mecalux offices. Then, the software was installed in a test environment so that the Megafin team could familiarize itself with the new system and to verify that everything was working correctly. Finally, it was deployed.
The new version of Easy WMS stands out for its flexibility, adaptability, and scalability. The software’s functionalities can be expanded to adjust to changes in the environment, such as fluctuations in demand and new customer requirements. Megafin is now prepared to boost its business as a 3PL provider specializing in food products. The company can serve its clients more effectively and ramp up the productivity of its logistics operations.
Megafin has installed three additional extensions of Mecalux’s Easy WMS:
- 3PL Portal. Megafin’s clients have direct remote access to Easy WMS to consult the status of their inventory whenever needed. “We have a clear commitment to service, and we make every effort to maintain the utmost quality of the food we store for consumers’ well-being. Our partners can inform themselves of the status of their products whenever they wish,” says Betancourth. They can also interact with Megafin, for example, to request that specific orders be processed and distributed.
- 3PL Automated Billing. This software records the logistics processes that have been performed in the center, linking each activity to a price and the stock owner in question. With this information, Megafin can generate a billing report specifying the services provided to each client.
- Labor Management System. This program measures the performance of the various activities taking place in the logistics center to detect improvement opportunities. “Our ultimate goal is to raise our warehouse productivity. By monitoring operational throughput, we can plan our workforce and organize processes more effectively,” says Betancourth.
3PL logistics operations
Every day, the Megafin warehouse receives multiple pallets containing a wide variety of food products sent by its clients. Megafin’s ERP system notifies Easy WMS in advance of the merchandise scheduled to arrive. This way, the Mecalux software can check that no mistakes have been made in the goods delivered.
Operators read the barcode on each pallet with their RF scanners, and Easy WMS records the merchandise in the database. With this digital system, Megafin maintains tight control of all pallets received, with information on the batch and expiration date of each one.
Before storing them, all the food products must undergo strict quality controls to guarantee that they are in good condition. Moreover, each pallet’s weight is captured to verify available food quantities in the facility.
Next, most materials are sent directly to the storage rooms. Easy WMS determines the most suitable area for each product: the freezer, refrigerated, or ambient-temperature warehouse. Megafin has three rapid freezing tunnels. Each has the capacity to freeze 7.7 to 13.2 tons of food at -22 °F within a range of 12 to 36 hours depending on the product’s diameter and physical-chemical composition.
“One of the major advantages of digitalizing our logistics processes is the proper organization of the goods. Easy WMS assigns each pallet a location taking into account factors such as food type and required temperature. Some pallets can’t be stored together: we have to respect the regulations and specifications of each product to ensure the implementation of our food safety programs, HACCP system, and allergen control,” says Betancourth.
In the logistics center’s different warehouses, pallets are organized according to the FEFO (first expired, first out) principle: items with the closest expiration date are the first to be distributed, ensuring flawless turnover.
When performing picking, Easy WMS shows operators which box they need to fill each order. Based on the SKUs and the size of the food products, the system determines which box to use. “By following instructions from Easy WMS, our operators are quicker. Plus, they don’t make mistakes. All operations are appropriately planned to make us more efficient,” says Betancourth.
Each operator is assigned a specific zone in the logistics center for picking. Orders are prepared in waves: as operators retrieve goods from their locations, they sort them into the boxes that will eventually be used to ship them. Once the task is finished, operators simply have to move the products to the shipping area for distribution.
Advanced food logistics management
Megafin’s supply chain involves moving, storing, and shipping goods that, due to their characteristics and composition, are susceptible to deterioration. To distribute its products effectively, the 3PL provider constantly overhauls its processes. Through digitalization, the company operates at full capacity, without any incidents, while maintaining strict control of its stock. All food is stored in ideal conditions, and order picking is much speedier and more accurate thanks to instructions from Easy WMS.
Megafin has also optimized management with its partners. “We’re a benchmark logistics provider in Colombia. Many food companies in the country rely on our services and professionalism. Thanks to digitalization, we can successfully meet our clients’ needs, and that’s truly satisfying,” says Betancourth.
Digitalizing our logistics center with Easy WMS has provided us with a multitude of benefits. I’d highlight real-time inventory control, optimized picking, and operational analysis to detect improvement opportunities. We’re prepared to effectively meet our clients’ needs.
Gallery
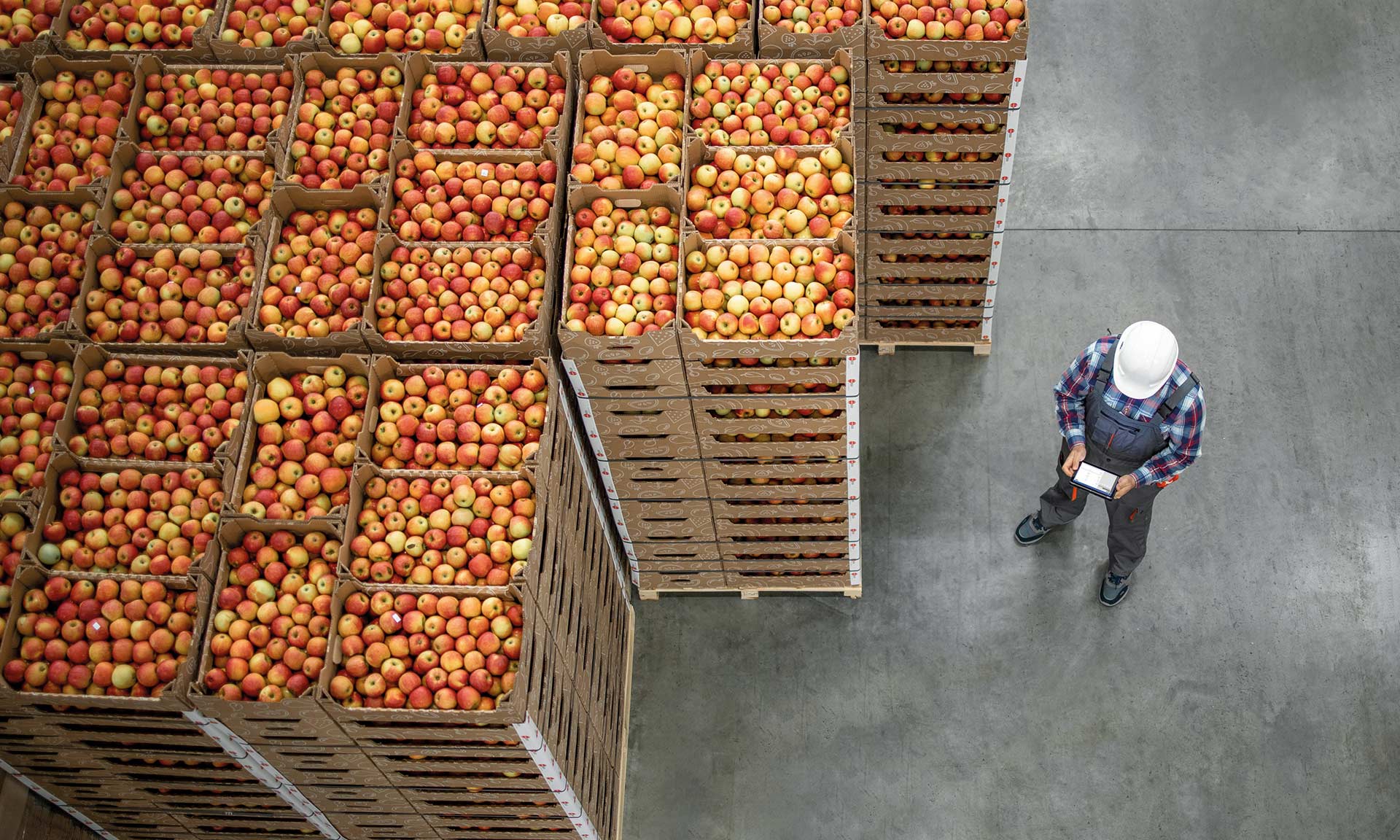
Logistics center of 3PL Megafin in Colombia with Easy WMS
Ask an expert