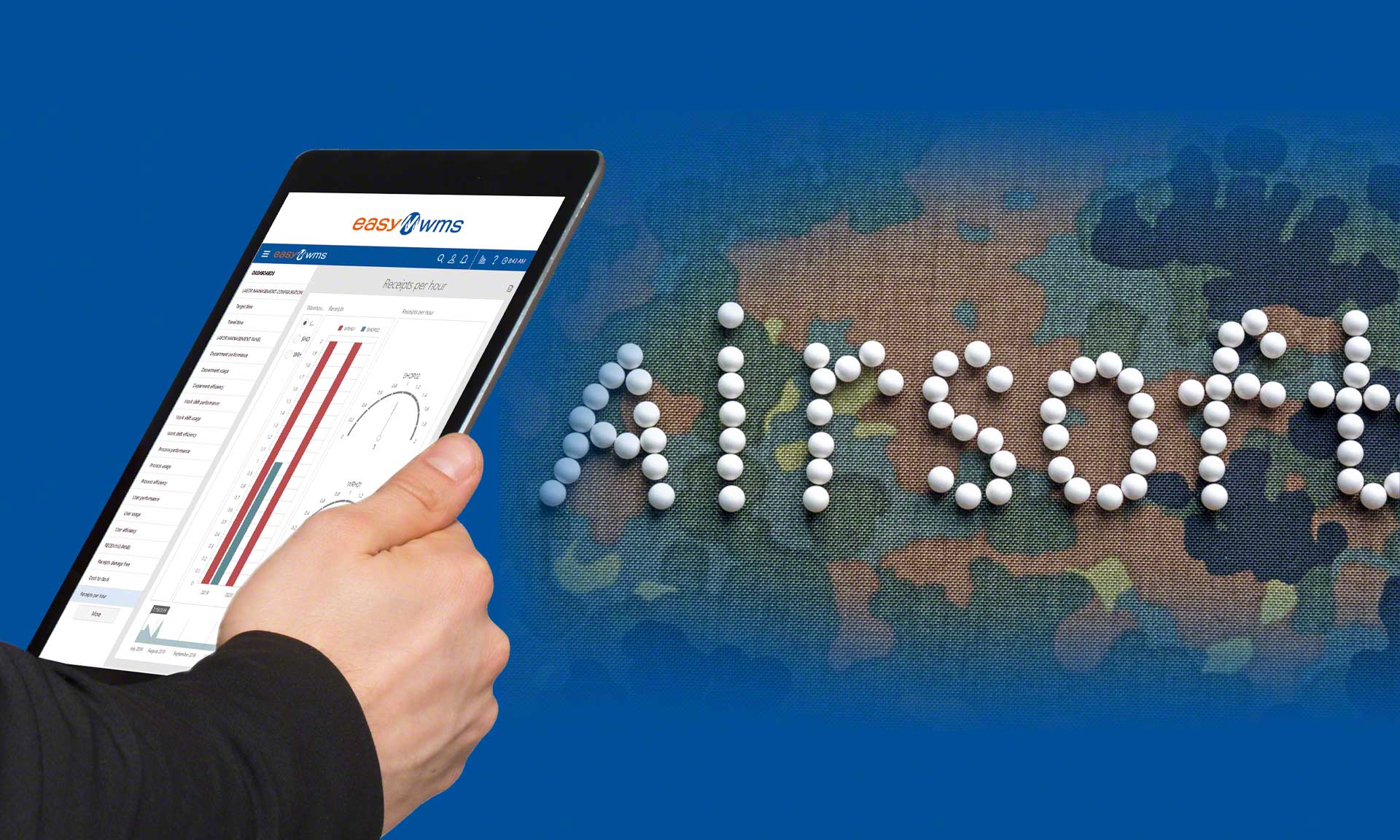
The airsoft e-commerce retailer installs Easy WMS in its warehouse in France
Destockage Games has implemented Easy WMS software in its facility in Avignon, France, to speed up the dispatch of 300 online orders a day.
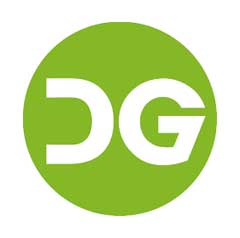
Destockage Games, an online store for airsoft (airgun games) products, has implemented Easy WMS from Mecalux in its warehouse in Avignon, France. With this technology, the company monitors its 7,000 SKUs in real time and has streamlined the preparation and distribution of 300 orders a day.
Destockage Games: the paradise of games
Headquartered in Avignon, France, Destockage Games — also known as DG — is a renowned online airsoft (airgun games) store and a leading company in the entertainment industry.
- Founded in: 2010
- Location: Avignon, France
- Products: compressed air items
- No. of SKUs: 7,000
CHALLENGES
|
SOLUTIONS
|
BENEFITS
|
---|
Destockage Games, a company specializing in airsoft items, has transformed its logistics operations to boost the expansion of its business. “We want to optimize our supply chain in order to anticipate market changes. Our priority is to satisfy our customers’ demands effectively,” says Margot Laurens, Project Manager at Destockage Games.
To that end, Destockage Games has implemented the Easy WMS warehouse management system from Mecalux in its 10,764 ft² distribution center (DC) in Avignon (France). This software monitors operations in real time and knows the exact location of the 7,000 SKUs in stock.
“With Easy WMS, our logistics processes have taken a huge step forward,” says Laurens. Now, the business can track its goods much more accurately and in much greater detail. The software not only records product entries and exits, but also assigns each item a location and thus knows where it is in real time.
In the past, Destockage Games organized its warehouse operations manually, aided by an enterprise resource management (ERP) system. “As the number of SKUs and orders in our facility started to grow, we realized we needed a more sophisticated, specialized system for our logistics processes. It was then that we considered installing warehouse management software,” says Laurens.
Easy WMS and the ERP system used by Destockage Games complement each other. Both programs are integrated in order to share essential information for the proper operation of the facility. For example, the ERP system informs Easy WMS of the items ordered by customers for order fulfillment to be organized immediately.
To work with Easy WMS in the warehouse, the operators use RF scanners. These devices display the messages sent by the WMS, e.g., which items to get, their exact location, and how many to pick. After completing a task, the operators merely have to confirm the action on their RF scanners to receive new instructions.
“With the RF scanners, we’ve cut down on the use of paper. Before, operators would use a printed list specifying the items needed to fill the orders. With such a large number of orders and SKUs, working with paper was inefficient — it entailed a high risk of errors,” says Laurens.
Destockage Games has implemented Easy WMS in the SaaS (software as a service) model. The system features high-performance servers in the cloud to ensure the correct behavior of Easy WMS and adapt to the volume of warehouse operations. “To access the program’s functionalities, all we have to do is connect via any browser or device with an internet connection,” says Laurens.
Efficient, controlled operations
By sending precise instructions to the operators, Easy WMS has optimized all processes in Destockage Games’ DC. “Our operations are much faster, and we’ve minimized mistakes,” says Laurens.
Easy WMS intervenes the moment goods arrive at the warehouse. Every day, it receives a multitude of pallets and boxes sent by suppliers. To enter these items in the system, the operators merely need to read the barcodes of each one with their RF scanners. Easy WMS can then verify that the products reported by the ERP system were received. Simultaneously, it assigns each item a location taking into account the SKU and demand level.
Immediately afterwards, the operators move the pallets and boxes to the locations indicated by Easy WMS. The software designs pick paths through the facility to ensure that operators travel the shortest possible distances.
“The main operation in the warehouse is order picking. We dispatch around 300 orders a day that are distributed to customers in France and other parts of Europe,” says Laurens. To manage this workload, Easy WMS sends instructions to operators on how to complete all the orders quickly.
In the Destockage Games facility, orders are prepared by grouping: on a single warehouse run, operators pick the items needed to complete several orders at once. The advantage of this working method is reduced operator travel.
Optimized dispatch
Once the orders are finished, the operators move the goods to the consolidation and dispatch area, where they are sorted and organized by order. These two processes are of high priority for Destockage Games, which needs to assure its items are properly distributed to satisfy customer demand.
To ensure maximum efficiency in dispatch operations, the company has implemented the Multi Carrier Shipping Software module. This extension of Easy WMS is specifically dedicated to organizing the order packing, labeling, and shipping processes. “With such a high number of daily shipments, we wanted to be able to control dispatches meticulously to avoid errors and wasted time,” says Laurens.
In the packing process, Multi Carrier Shipping Software guides the operators at all times, showing them which items to pack and whether to do this as a single unit load or multiple ones. With the constant supervision of the software, the operators prepare packages more swiftly and, at the same time, verify that no mistakes have been made in picking tasks.
Multi Carrier Shipping Software also knows which delivery agency will deliver each order and generates and prints a label for each one. The labels include the tracking number, which customers use to monitor their orders in real time.
The software is integrated Destockage Games’ delivery agencies — Chronopost, Colissimo, Frequenceo, GLS, and TNT — to send them all the information they need to distribute the goods (e.g., number of parcels per shipment, weight, and volume). “When the carriers arrive at the warehouse, all the information is already in their system automatically. They just have to pick up the prepared orders and begin delivering them,” says Laurens.
The optimal organization of the dispatch process has minimized errors and made product distribution faster.
Operational excellence
By digitizing its logistics operations, Destockage Games now accurately monitors its 7,000 SKUs. Moreover, it has streamlined key processes for customer satisfaction, namely order fulfillment and dispatch.
By integrating with Destockage Games’ ERP system, the Mecalux warehouse management software organizes order picking immediately. The minute a customer purchases an item through the company’s website — from high-pressure air guns to video games — operators begin preparing that order in the DC. This ensures that the goods are distributed as quickly as possible and without delay.
Destockage Games knows how important logistics processes are for its business. With a scalable software program such as Easy WMS, the company can adapt its processes to future changes, e.g., an increase in SKUs or daily orders.
Easy WMS is a very intuitive software program that enables our operators carry out their tasks more speedily and more accurately. The software has helped us to meet our objectives: to dispatch all orders the same day, before 4:00 p.m., and without making mistakes.
Ask an expert