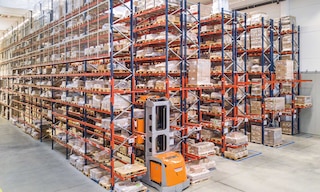
VNA pallet racking: uses and applications in warehousing
VNA pallet racking is a solution recommended for businesses that need to make the most of available space and maximize capacity. Additionally, to achieve continuous, error-free operations, this storage system can be automated by incorporating AS/RS trilateral stacker cranes.
What is VNA in warehousing?
The concept of VNA (very narrow aisle) racking refers to selective pallet rack units that are positioned closer to each other in a warehouse.
In facilities that use counterbalance forklifts, for example, aisles can measure between 10' and 14.5' wide. On the other hand, very narrow aisles are typically 5' to 6' wide. This type of pallet racking enables you to leverage the available floor space in your warehouse to expand capacity and accommodate a larger number of goods.
VNA pallet racking combines the characteristics of both conventional and high-density systems. It achieves significant space savings while ensuring direct access to products stored.
Employing this storage solution requires special forklifts such as trilateral or bilateral turret trucks. You can also automate operations by implementing AS/RS trilateral stacker cranes.
Handling equipment for VNA pallet racking
Companies with moderate warehouse flows generally rely on narrow aisle forklifts to insert and remove items from their locations:
- Trilateral. These VNA trucks have a rotating head that supports their forks, enabling them to handle goods on either side of the aisle as well as frontally. They are capable of depositing pallets directly onto the floor.
- Bilateral. These trucks have a cradle that houses their telescopic forks. While they can’t place pallets on the floor or position them frontally, they can operate in even narrower aisles.
These machines primarily operate within the aisles, only switching from one to another when necessary. If your flow of incoming and outgoing goods is high, you can use other types of handling equipment to bring products closer to or remove them from the ends of the aisles. Options include counterbalance forklifts and reach trucks, autonomous mobile robots, automated guided vehicles, and pallet conveyors. You can also install pick and deposit (P&D) stations to facilitate the exchange of pallets.
When operating in such narrow aisles, trilateral and bilateral forklifts need to be guided to enable their safe movement. In warehouses, two guidance systems are generally used:
- Mechanical. Metal profiles are anchored to the floor on both sides of the aisle. Profiles are L- or C-shaped.
- Wire-guided. A wire buried in the floor produces a magnetic field. The machine detects it and follows it as a guide.
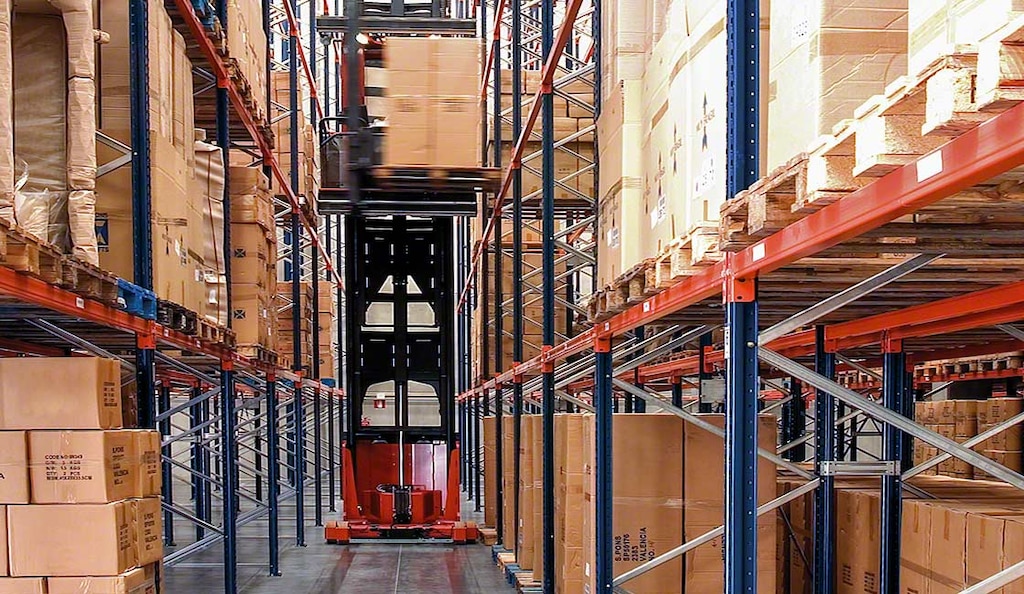
Automation of VNA pallet racking
Warehouses with narrow-aisle racking can be automated relatively easily by incorporating AS/RS trilateral stacker cranes. This automated storage and retrieval solution (AS/RS) is designed to perform these tasks with complete autonomy. Thanks to their rotating head, these machines can pick up and place pallets in the racking in three positions: one frontal and two lateral.
They have the advantage of being compatible with manual warehouses already run with operator-driven trilateral or bilateral forklifts. With only four points of support on the ground, AS/RS trilateral stacker cranes don’t have an upper guide rail, so they can adapt to warehouses that use forklifts.
Their implementation is easy because the racking structure doesn’t need to be modified. Another feature is their quick return on investment.
Advantages and disadvantages of VNA pallet racking
VNA racking systems provide the following benefits:
- Space optimization. They require less width between aisles, resulting in a larger storage area.
- Versatile system. They can accommodate various items, including pallets of different sizes and small boxes.
- Higher productivity. The racks offer direct access to products, speeding up operations such as product putaway and order picking.
- Easy automation. AS/RS trilateral stacker cranes can be used to automate storage tasks, thus ensuring a higher flow of pallets in and out.
One disadvantage of this solution is that it calls for specialized handling equipment to maneuver in such narrow aisles. Additionally, both bilateral and trilateral forklifts need to recharge their batteries and follow a guide to travel along the aisles. However, you can replace them with AS/RS trilateral stacker cranes, which optimize and accelerate movements in the warehouse.
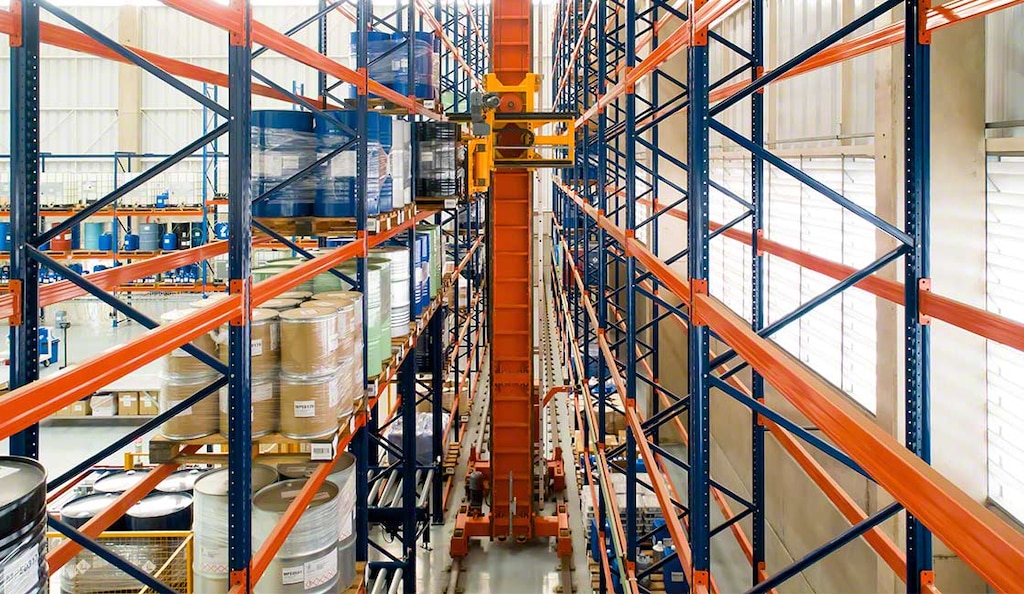
Applications of VNA pallet racking in warehousing
VNA pallet racking is ideal for businesses with limited storage space in their logistics facilities and that need to make the most of every available inch to achieve the highest storage capacity. Generally, VNA systems comprise high-bay pallet racking, which allows you to house more items.
This is the case with home decor company Côté Table. In France, the retailer equipped its warehouse with eight aisles of VNA pallet racking from Mecalux with a storage capacity of 19,600 pallets. It uses high-bay order pickers to perform picking. Operators stand in a cabin that is lifted with the load. From that height, they retrieve the items that make up each order directly from the racks.
This solution is also common in the warehouses of organizations that manage high-turnover items and that seek to expedite the goods-in/goods-out process. The direct access facilitates the work of the operators performing storage and picking tasks.
Elektro3, for instance, has installed a VNA pallet racking system in its warehouse in Spain. It aimed to “optimize all the space and house the largest possible number of products,” says Eduard Bordàs, Logistics Manager at Electro3, a retailer of products for hardware, DIY, household appliance, and gardening stores. The company chose this option to accelerate order processing: “They’re specifically designed to boost the most important operation in this center: order picking,” says Bordàs. Every day, the warehouse fills around 1,000 orders, which are distributed to a portion of its 22,500 customers in over 20 countries.
Businesses that manage different SKUs in their warehouses also often choose VNA pallet racking. Its slots can hold pallets as well as small boxes. Schneider Electric, a multinational specializing in technologies and power management solutions, equipped its warehouse in Spain with VNA pallet racking. It uses the system to store a wide variety of products, from small components to bulky industrial instruments. To facilitate the work of picking operators, the business employs high-bay order pickers.
High storage capacity and versatility
Companies from all sectors equip their warehouses with VNA pallet racking. It leverages available floor space and provides greater storage capacity. This racking can be used with forklifts that are safely guided inside the aisles. Alternatively, you can employ AS/RS trilateral stacker cranes to streamline the inbound and outbound flow of goods.
At Interlake Mecalux, we have extensive experience in manufacturing and installing this type of storage solution. Planning on optimizing your warehouse? Our VNA pallet racking is an effective, versatile choice. Contact us for more information on how to enhance your warehouse.