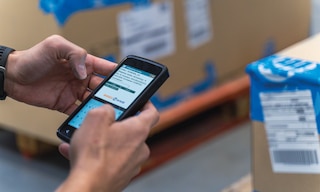
Traceability types in logistics with examples
There are four different types of traceability, depending on the stage of the supply chain in which products are located.
In logistics, traceability consists of tracking an item’s journey, from manufacturing to customer delivery. The objective is to ensure quality, safety, and compliance with regulations.
In industries such as food, pharmaceuticals, and chemicals, traceability is essential for maintaining product integrity and safety.
What are the various traceability types?
Companies’ supply chains encompass many operations, including receiving, order fulfillment, and shipping. By identifying and recording the location of products in each process, businesses can track the merchandise’s origin, processing status, and distribution.
These are the four types of traceability:
Upstream traceability (backward)
Upstream traceability tracks the origin and journey of a product from its source. This traceability type provides companies with a complete historical record of their goods, such as materials needed for production, suppliers involved, and manufacturing processes applied.
When receiving an item, several data are recorded, e.g., product quantity, arrival and expiration dates, supplier, batch number, and health and hygiene controls performed (if applicable).
Upstream traceability offers multiple benefits:
- Safety and quality. It helps identify the source of issues, facilitates the recall of defective products, and enables the correction of failures at any point in the supply chain.
- Regulatory compliance. It’s effective for meeting regulations that require detailed documentation on the origin of materials and components, ensuring that specific standards are followed.
- Transparency and trust. It provides consumers and business partners with clear information about the source of products, increasing confidence in the brand and manufacturing processes.
- Operational efficiency. It makes supply chain management more efficient, improving planning, inventory control, and responsiveness to any issues that may arise.
Upstream traceability is vital in numerous sectors, especially where product safety and quality are critical. For example, it’s a must for managing allergens in the food industry. Manufacturers can track each ingredient to guarantee goods comply with food safety and labeling regulations. If an undeclared allergen is detected, the company can quickly identify and recall affected batches, minimizing consumer risks and protecting the brand’s reputation.
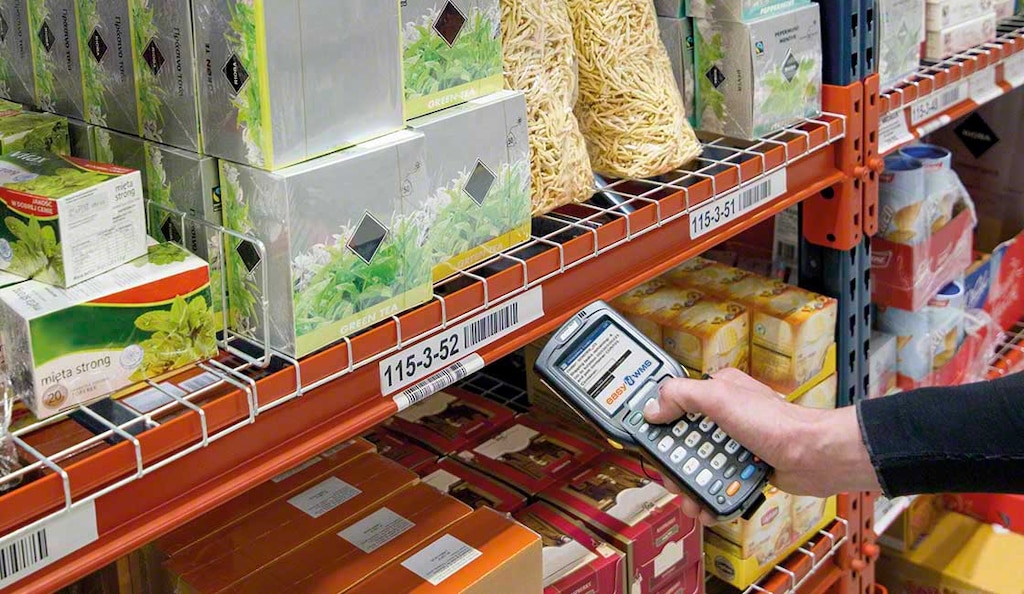
Downstream traceability (forward)
This focuses on tracking goods from the time they leave the production facility until they reach end customers. The process involves monitoring transportation, particularly identifying carriers, routes, shipping conditions, and delivery dates.
Downstream traceability records product recipient data, specifying each customer, item, sold batch, expiration date, warehouse from which the order was distributed, and shipping date.
These are key features of downstream traceability:
- Product identification. Each item or batch must be uniquely identified, usually through barcodes, batch numbers, or RFID systems.
- Information recording. This maintains a record of merchandise distribution (including how much was sold and to whom) and any movements made within the supply chain.
- Batch and series tracking. If a product needs to be recalled, downstream traceability makes it possible to identify specific affected batches and contact distributors or end customers.
If allergen contamination is detected in food, downstream traceability pinpoints the stores that received the affected batch for quick product recall and minimal consumer health risks.
Internal traceability
In logistics, this traceability type deals with tracking and controlling an organization’s internal processes. It monitors product movements, storage, and management within a facility.
It’s crucial to know when and how raw materials are mixed, in what quantities, the outcome of the processing, and the resulting final product. An internal traceability system allows companies to monitor every stage of the production process, from raw material receipt to the manufacture and distribution of finished goods.
Internal traceability also includes detailed control of product movements within a warehouse. This involves tracking how and when items are stored as well as any transfers or movements. This tracking is fundamental in logistics. It enables efficient inventory management, guarantees products are available when needed, and reduces inventory shrinkage. By accurately monitoring the location and status of each product in their facilities, businesses can significantly improve their supply chain efficiency and streamline finished goods distribution.
Rigorously tracking every step in manufacturing processes enhances operational efficiency and quality control within internal processes. The main goal is to optimize the workflow so that each stage of the process is effective and meets established quality standards.
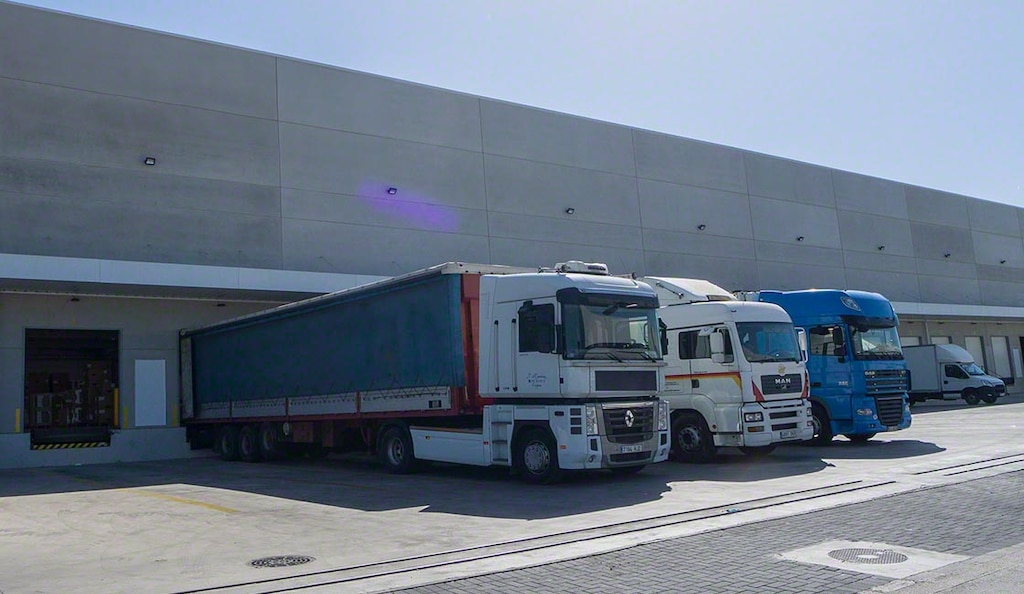
External traceability
This type traces a product across its journey outside the company, from the time it is shipped from the facility until it reaches the end customer. It deals with the information handled by couriers such as the number of packages and delivery dates.
External traceability is central to ensuring product safety and quality. Businesses can quickly detect and manage issues (e.g., product recalls or identifying defective items) as they arise.
Technology for logistics traceability
Through product traceability, companies offer consumers the highest quality assurance while identifying potential areas for improvement.
To ensure traceability, businesses leverage various technological resources and solutions to record and access product data at every stage of the supply chain. Examples include barcodes, RFID tags, and warehouse management software, which help optimize and control inventory.
Are you looking to manage product traceability effectively? Interlake Mecalux has the answer. With our Easy WMS warehouse management system, you can track every move your goods make. The system knows what stock you have in your warehouse in addition to what processes each item has gone through and when. Contact us, and we’ll advise you on how to monitor your end-to-end product history across the supply chain.