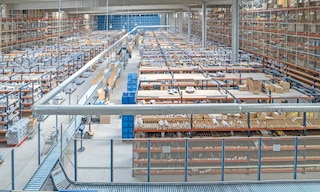
The power of the 5S: Transforming warehouse organization
Implementing the 5S methodology is essential for optimizing space management, improving productivity, and ensuring worker safety. A warehouse organized using this approach operates more efficiently, minimizing errors and reducing downtime.
What does the 5S stand for?
Developed in Japan, the 5S (five S) method aims to improve organization, cleanliness, and efficiency in the workplace. Its name comes from five Japanese words beginning with the letter “S”: seiri, seiton, seiso, seiketsu, and shitsuke. These terms represent key principles for maintaining safe, productive work environments. They serve as the foundation for other continuous improvement methods, such as lean manufacturing and kaizen.
- Seiri (Sort). Separate what is necessary from what is not by identifying and removing items that are unused or fail to add value to processes.
- Seiton (Set in order). Arrange materials so they are easy to find, use, and return to their proper place.
- Seiso (Shine). Keep the work area clean and orderly. This also involves preventive maintenance of equipment, where cleaning becomes an opportunity to spot anomalies or wear that could lead to breakdowns.
- Seiketsu (Standardize). Establish standards to maintain cleanliness and order consistently. Create clear procedures to ensure the long-term application of the first three “S” principles.
- Shitsuke (Sustain). Promote discipline to follow established standards and encourage a culture of continuous improvement.
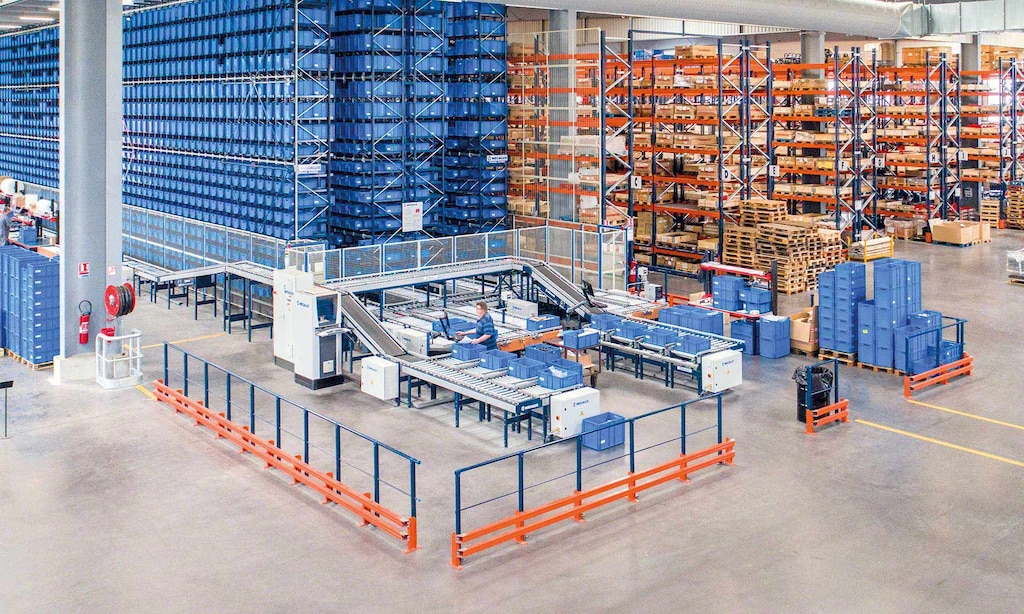
What are the advantages of the 5S method?
The 5S technique offers numerous benefits for both companies and employees by focusing on improving the work environment, efficiency, and quality. These are its main advantages:
- Greater productivity. Knowing how to organize and standardize the workspace prevents time wasted searching for tools or materials. Everything is within reach and in its place, streamlining processes.
- Enhanced efficiency. A tidy, organized environment helps identify problems before they become failures. Systematizing operational processes also reduces variable outcomes.
- Improved workplace safety. Eliminating unnecessary objects and maintaining cleanliness avoids the risk of trips, falls, or other accidents.
- Optimized space. Getting rid of nonessential items frees up usable space in the workplace.
- Cost savings. Reducing excess materials and minimizing errors significantly lowers operating costs. Additionally, keeping equipment in good condition and maintaining an organized environment extends the life of resources.
- Increased employee engagement and motivation. Workers develop constructive habits by following clear, well-defined rules.
- Stronger corporate image. A clean, organized workspace conveys professionalism to clients, suppliers, and visitors.
- Competitive edge. Adopting methodologies like the 5S positions companies as innovative and committed to excellence.
Implementing the 5Ss in the workplace is an investment in continuous improvement that can become a strategic advantage, bolstering internal processes and overall performance.
How to apply 5S in the warehouse
Adopting the 5S method requires a systematic approach to improve organization, efficiency, and safety. These are the key steps to follow when introducing each of the 5Ss in a warehouse environment:
Seiri (Sort)
To separate what’s necessary from what’s not, eliminate items that don’t add value to storage or other intralogistics operations. Measures include:
- Identify products, materials, or equipment that are obsolete, damaged, or rarely used.
- Classify materials by usage frequency: often, occasionally, or hardly ever.
- Remove unneeded items from the warehouse and assign them for recycling, disposal, or resale.
- Reduce excess inventory to free up space.
Seiton (Set in order)
Efficient organization means that every item has its place, is accessible, and is clearly identified. To maintain order, follow these steps:
- Define specific storage zones based on product category, size, weight, or turnover rate (ABC analysis). Interlake Mecalux’s Easy WMS warehouse management system, for instance, features Slotting for WMS. This module optimizes item classification by automating location management according to factors such as demand trends.
- Implement clear signage, with labels and coding systems (e.g., barcodes).
- Use appropriate racking systems and unit loads to maximize vertical space. Examples include drive-in pallet racking and the Pallet Shuttle system.
- Apply inventory management methods such as FIFO (first in, first out) or LIFO (last in, first out) to organize product shipments by age.
- Keep aisles clear and safe for handling equipment to move freely.
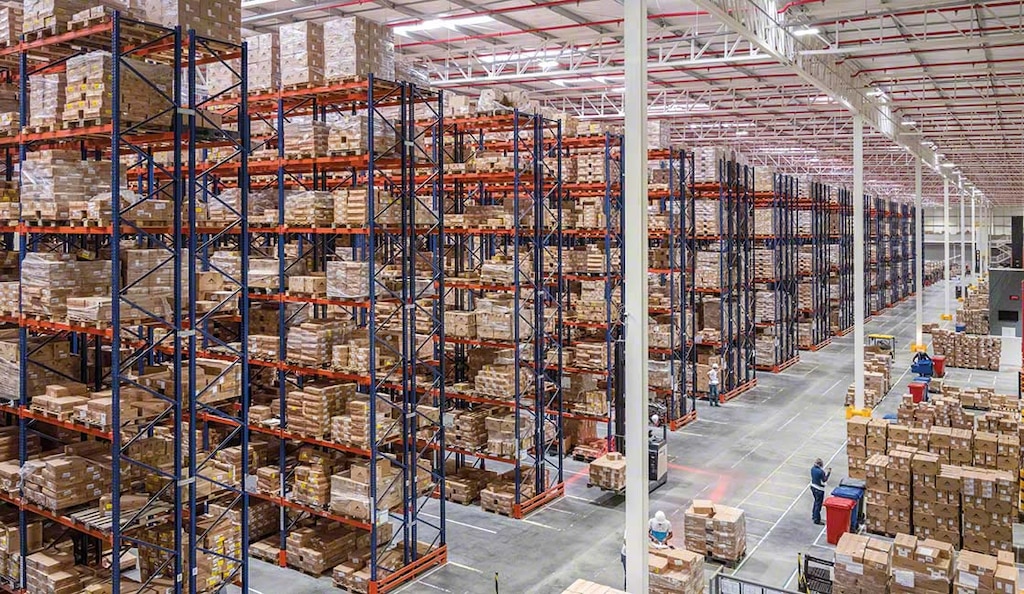
Seiso (Shine)
The examples below are aimed at keeping the warehouse spotless, preventing dirt buildup, ensuring safety, and extending equipment lifespan:
- Define daily cleaning routines for racks, aisles, workstations, and machinery.
- Identify and eliminate sources of dirt such as spills, dust, or packaging waste.
- Use checklists for visual cleaning inspections.
- Make sure tools and materials are clean before storing them.
- Carry out annual racking inspections by qualified technicians to assess storage system conditions.
Seiketsu (Standardize)
To make sure improvements stick, it’s crucial to create clear standards through procedures such as the following:
- Document best practices for storage, organization, and cleanliness.
- Design diagrams and visual guides that show how each area of the warehouse should be maintained.
- Train employees to follow established rules and use equipment, machines, and support systems correctly. Interlake Mecalux offers staff training programs on storage system operation and maintenance in addition to safe material handling to keep operations running smoothly.
Shitsuke (Sustain)
Companies need to create an environment that promotes a lasting 5S culture. Here are a few tips to make it happen:
- Motivate employees to take an active role in maintaining the 5Ss.
- Assign supervisors to oversee specific warehouse areas.
- Conduct regular audits to check compliance and reward outstanding teams.
- Encourage continuous improvement through meetings where participants discuss new ideas or issues.
The 5S: The path to flawless logistics operations
Implementing the 5Ss in the warehouse not only optimizes the physical space — it drives efficiency, safety, and operational quality. For logistics managers, it’s a powerful tool to overcome day-to-day challenges and strive for excellence.
Adopting the 5Ss isn’t just about operational improvement; it’s a strategic investment in your business’s productivity and competitiveness. If you're looking to take your warehouse performance to the next level, we're here to help. Contact us, and one of our expert consultants will guide you through tailored solutions to create a clean, efficient, well-organized warehouse.