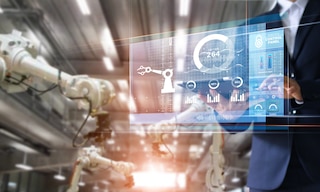
Process control in the supply chain
Operational accuracy is essential for achieving an optimized supply chain. For this reason, logistics and production managers turn to process control to ensure that their operations are efficient, error-free, and compliant with current safety standards.
Process control employs industrial control systems, a blanket term for the set of tools — i.e., sensors, controllers, and regulators — used to monitor the status of the processes taking place in a warehouse or production center.
What is process control?
Process control is an analysis method commonly adopted in logistics and manufacturing. Its main purpose is to run and supervise one or more industrial processes to identify anomalies and errors and thus eliminate inefficiencies.
Employing equipment and sensors in the work center, process control systems oversee the status of operations and analyze the data produced in processes such as goods movements and mass production. Companies install sensors and other automatic devices to avoid errors due to manual management.
One type of control system typically seen in warehouses is a programmable logic controller (PLC). PLCs are processors that direct the movements of the automatic equipment, following orders from a higher-level program (i.e., warehouse management software).
As defined in the research article Standards-based integration of advanced process control and optimization, published in the Journal of Industrial Information Integration, “APC [advanced process control] refers to techniques and technologies implemented in applications across process industry such as oil and gas, petrochemicals, water and wastewater, chemicals, power, paper and pulps, pharmaceuticals, food and beverages, and others. These industries are characterized by continuous processes. Process control systems may be a distributed control system (DCS), a programmable logic controller (PLC), and/or a supervisory control computer.”
The article also highlights the benefits of APC: “The broad range of technologies and techniques that APC solutions possess enables manufacturers to improve production capacity, monitor process parameters, and operate with greater flexibility and safety.”
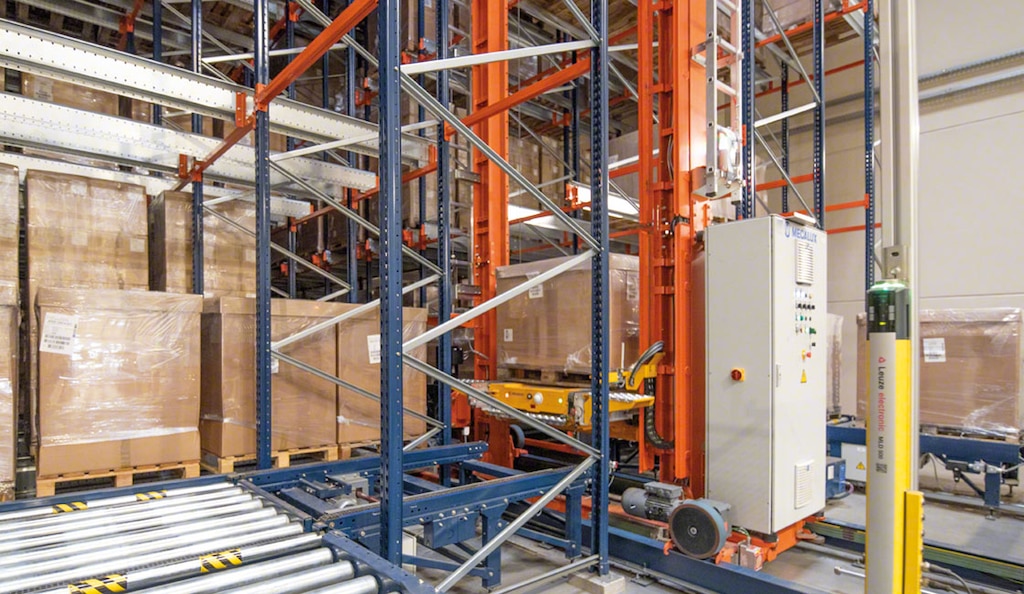
Why is process control so important?
Process control systems are normally applied in automated production lines, where items are manufactured without interruption. And more and more companies are employing process control methods to ensure the utmost quality of their products.
In smart factories, sensors are installed in different areas to control processes and measure product manufacturing and storage conditions: acidity, density, tension, temperature, weight, oxygen level, and many other properties that can be evaluated.
The reason for this? The use of sensors and other devices configured to track the status of processes is vital for preventing errors and enhancing safety in the facility. Process control systems enable businesses to:
- Optimize energy costs.
- Increase safety in their centers.
- Ensure quality standards.
- Reduce production costs.
How does a process control system work?
A process control system is activated when measuring tools are installed as part of a manufacturing process. The aim of this system is to collect information on the status of the production process and to take measures when the levels surpass the limits preset by the manager.
In an industrial control system, the set point is the exact level marked by a parameter to indicate that the operation is being executed correctly. Additionally, certain predetermined fluctuations have to be accepted for each property to be analyzed, facilitating the measurement and control of the process.
This production process control method includes three types of components for each of the variables to be monitored:
- Measurement device: this constantly tracks a specific property in the manufacturing process - e.g., temperature, oxygen level, or degree of acidity - to make sure it’s within the pre-established parameters.
- Controller: this component compares the values regularly recorded by the measurement device with the preset values. If they don’t match, the controller executes a pre-configured action for the production status to return to its established levels. For example, when the flow rate of a liquid drops below the established volume, the system commands the valves or injection pump to open so that the amount of product or raw material is increased.
- Regulator: this element depends on the controller and adapts to each manufacturing process. The regulator coordinates the throughput of the process by executing the controller’s commands when the production process fails to meet the standards stipulated in advance by the manager or manufacturer.
Example of a process control system
In an industrial environment, process control systems are tasked with monitoring and automatically adjusting a production processes to maintain quality and productivity standards. In a manufacturing context, an example of process control would consists of establishing mechanisms for maintaining a constant air temperature of 5 °F on the production lines to properly preserve a specific product.
To make sure the air remains at that temperature, a control system with a temperature sensor and a controller would be implemented. The temperature sensor would send information to the controller on an ongoing basis, indicating the facility’s temperature. The controller, which is in charge of verifying that the environment has a particular temperature (with certain acceptable fluctuations), sends instructions to the regulator - which could be an industrial air conditioning system - to adjust the temperature when it goes too far up or down.
Although this example shows how a process controller would work on a rather simple production line, process control systems tend to be installed in more complex industrial environments, e.g., on a chemical manufacturing line with a bill of materials containing multiple liquids to create a single product. In this case, the control system automates the management of the valves, using sensors that indicate the amount of product available. The controller calculates how much of the remaining materials are required based on the sensor’s measurement. It then indicates to the valves the levels of resources needed for the manufacturing process to continue as planned.
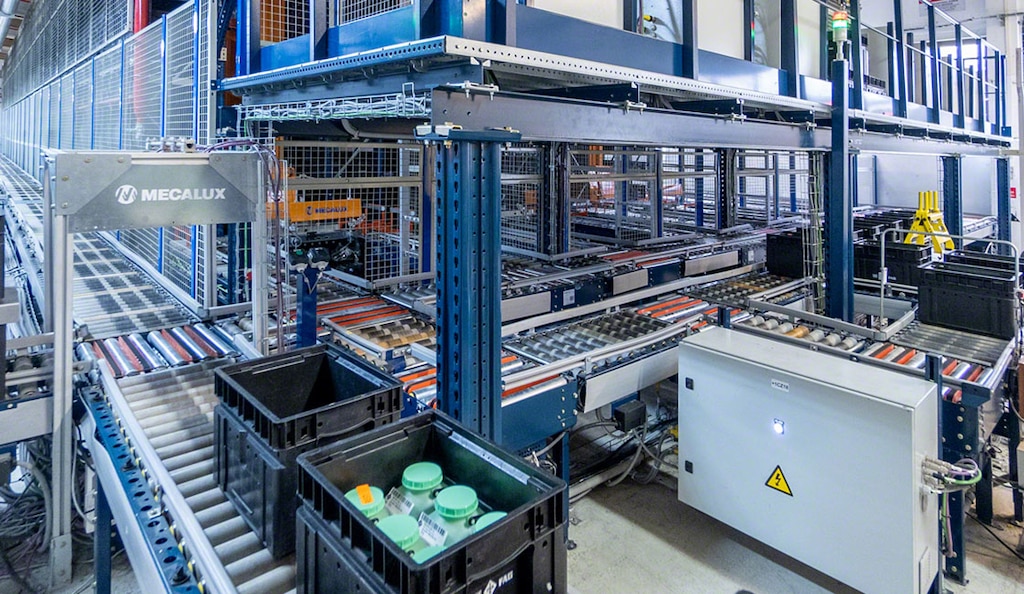
Process control for efficient management
An increasing number of companies are employing automatic controllers to run and oversee the performance of their processes. Why? An automated process control system eliminates errors from production lines.
The implementation of tools such as sensors and processors enables companies to maintain their quality standards as well as minimize costs in production, which are key in Logistics and Manufacturing 4.0.