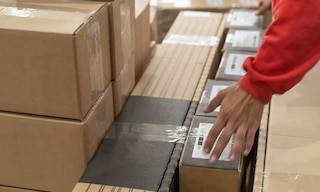
Double handling: example of waste in Lean logistics
Double handling relates to the excessive movement of goods, a practice that reduces productivity in logistics facilities. Inefficiency in material handling and order picking leads to cost overruns, stock losses, late deliveries, and thus poor service for end customers.
The good news is that modern logistics technologies can mitigate double handling: warehouse management systems (WMSs) guide operators in carrying out their tasks. They automate decision-making, ensure that orders are filled as quickly as possible, and maximize productivity. Automated solutions such as conveyors, mobile robots, and automatic handling equipment also avoid excessive goods handling. They eliminate unnecessary movements and guarantee that facilities operate at full capacity.
What is double handling in warehousing?
Double handling occurs when inefficiencies arise in operations such as product replenishment and order picking. Consequently, operators spend too much time or perform too many movements when transporting goods internally. One of the reasons behind this inefficient practice is the lack of route optimization in a logistics facility, which wastes time and increases the risk of damaging merchandise or storage systems during transfers.
In a warehouse, superfluous processes and actions lengthen order fulfillment lead times, and this affects end-customer service. The academic paper An efficient approach to investigate the tradeoff between double handling and needed capacity in automated distribution centers illustrates an example of double handling in a pallet storage system: “Double handling occurs when the daily demand is less than the pallet size, and the decision is made to take only some of the carton cases from the pallet (using depalletizers), and keep the rest in the unit-load warehouse until the rest of cases are needed.” Minimizing double handling can help companies improve their logistics service, deliver orders on time, and hence gain a larger market share.
Double handling, 'muda', and the Lean method
Double handling of products and unnecessary operator movements are examples of waste in Lean. The Lean logistics methodology consists of identifying and eliminating activities and processes that don’t add value and could decrease operational effectiveness. For instance, poor planning of paths in the warehouse can lead to wasted trips and, therefore, inefficient order picking tasks.
Lean logistics uses the Japanese term muda to describe any process that generates some type of waste or that fails to add real value to a product or service. Double handling of goods drives up costs and makes companies’ logistics operations less productive. But excessive movements aren’t the only kind of muda that can occur in a warehouse. The accumulation of stock without rhyme or reason and subpar inventory management in general can also lead to a loss of space or the obsolescence of the products stored.
What causes double handling?
When a facility receives materials, those goods should follow a preset path that prevents their needless movement or handling. These tend to be the main causes of double handling:
- Lack of a putaway and replenishment plan. Suboptimal inventory planning can cause stock to be stored in the wrong locations. Besides occupying space meant for other goods, this merchandise has to be moved to another area in the warehouse.
- Communication errors between the logistics facility and other company departments, such as manufacturing. Inadequate communication can lead to bottlenecks and stockouts on the production lines.
- Insufficient storage space or poor distribution of products. Mistakes in logistics planning and warehouse layout design can give rise to useless movements of workers and goods.
- Misuse of machinery, assistance devices, or material handling equipment. In manually run facilities, for example, employing the wrong forklifts could slow down operations.
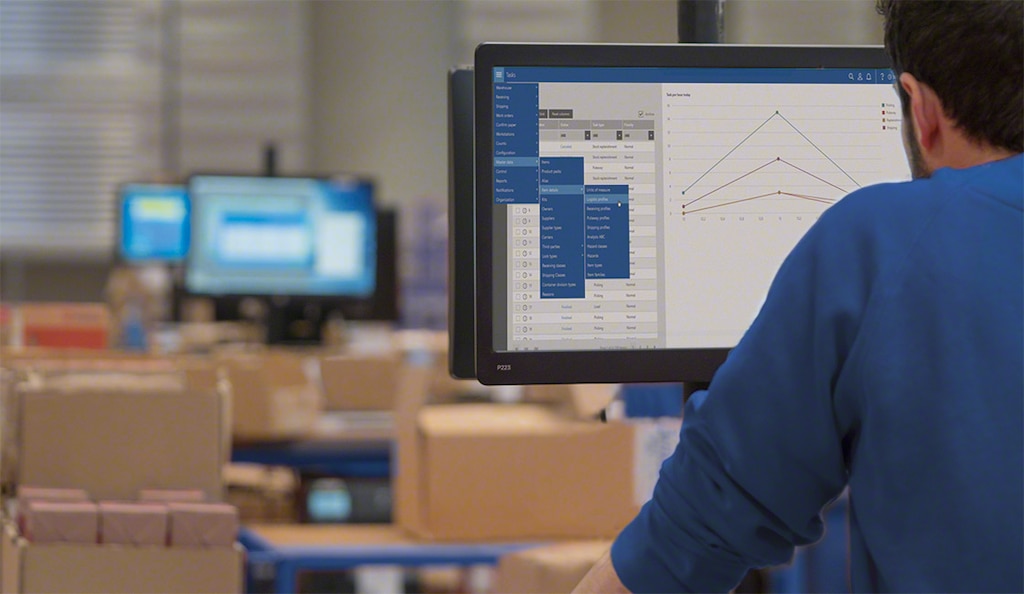
How to prevent double handling
To avoid double handling and other superfluous movements, it’s advisable to replace manual management of goods with a digital solution like a warehouse management system (WMS). This logistics software coordinates everything occurring in a facility, including the assignment of storage locations. Based on a set of rules and criteria set in advance by the logistics manager, the software determines the ideal location for each product. This limits the risk of inefficiencies — e.g., errors and double handling — in replenishment tasks.
An advanced WMS software also plans pick paths and handling equipment routes with a twofold objective: efficiency and safety in the movements of both operators and goods. The program takes into account the number of orders to prepare and the distribution of products in the facility to determine the optimal pick path for each operator, thus maximizing throughput.
Automated solutions ― such as conveyors, stacker cranes, and mobile robots ― minimize the risk of double handling and move goods optimally. In warehouses with this type of equipment, the WMS software acts as the mastermind, coordinating the movements of the robots and goods. These automated solutions facilitate the goods-to-person strategy, where products are moved to operators in a completely autonomous way. Automation reduces the number of movements and handling maneuvers to maximize the performance of warehouse operations.
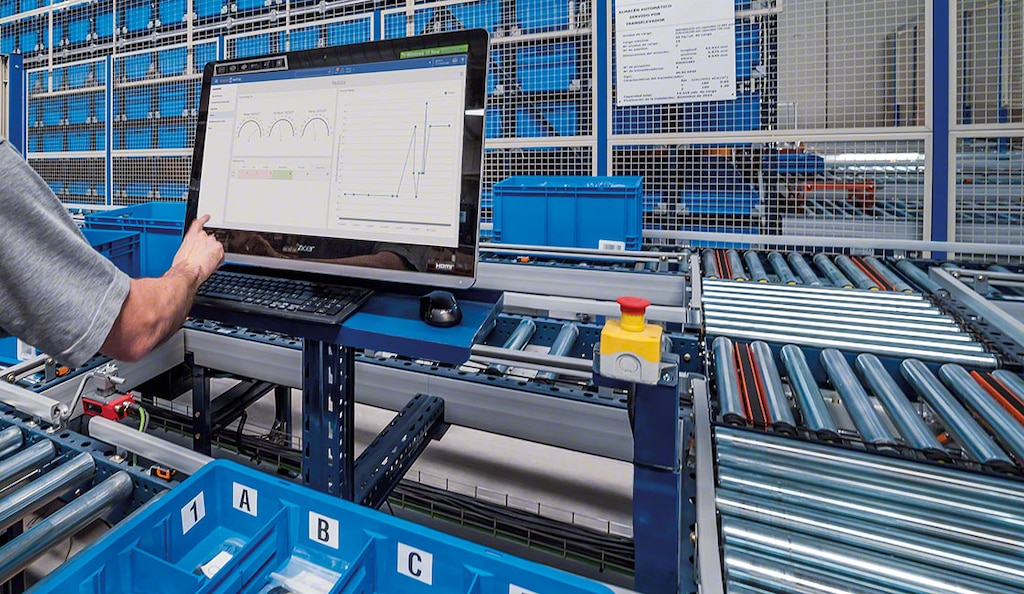
Advanced solutions to avoid warehouse inefficiency
In a logistics facility, a lack of streamlined movements is a clear indicator of waste in Lean and, therefore, logistics inefficiency. New technologies considerably scale down the risk of errors resulting from double handling. In manual facilities, warehouse management software such as Easy WMS coordinates the actions of the goods and operators, avoiding unproductive processes.
Likewise, investing in robotic solutions like stacker cranes, conveyors, and mobile robots automates product movements, boosting warehouse throughput. Interlake Mecalux has extensive experience in designing storage solutions and software for all kinds of businesses. Be sure to get in touch. One of our expert consultants will advise you on the best solution for your facility.