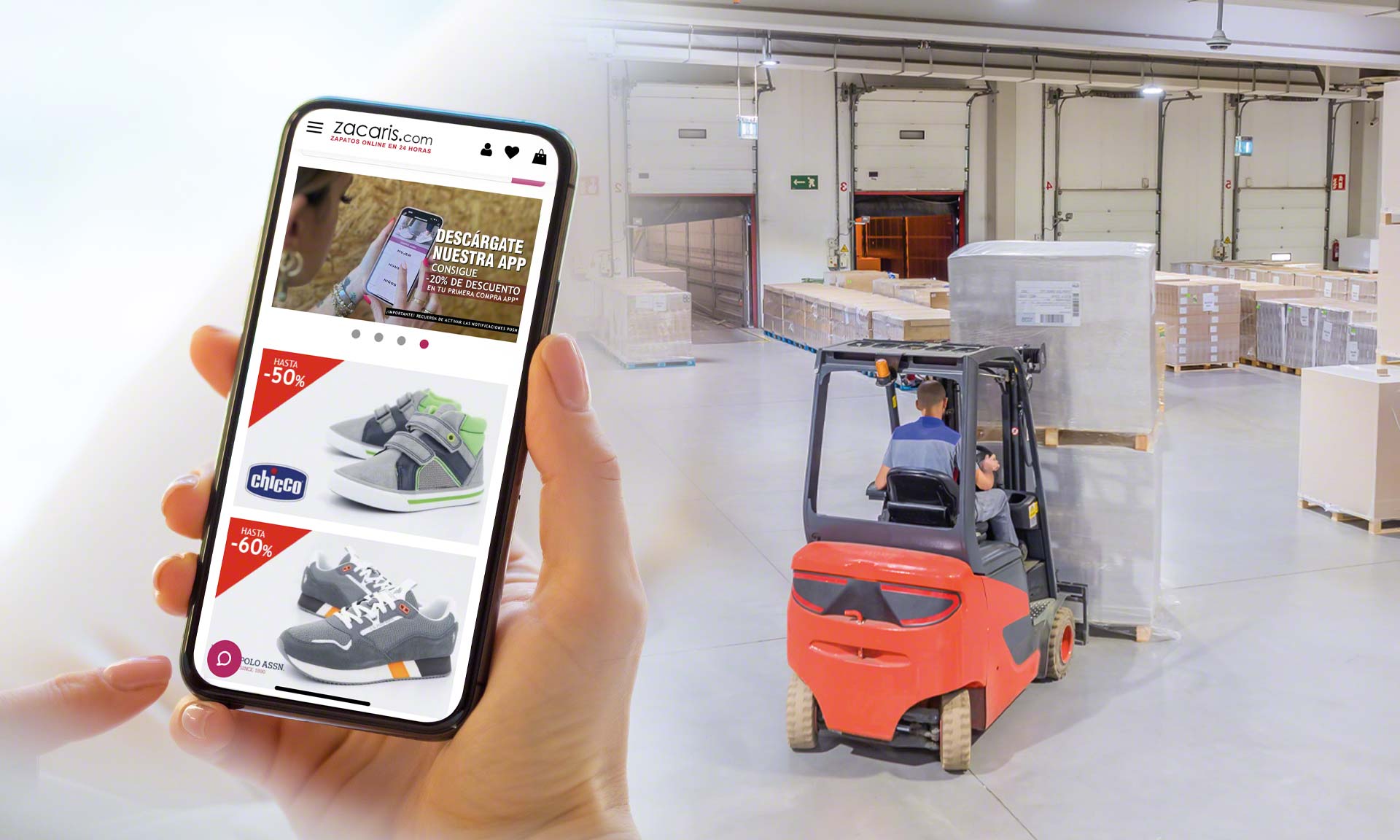
Zacaris optimizes its footwear warehouse with digitalization
Footwear e-commerce company Zacaris uses Easy WMS to prepare and ship 3,000 orders a day to its customers.
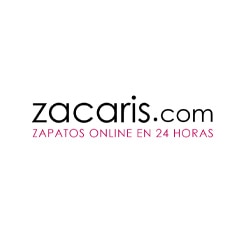
Online footwear store Zacaris has moved to a new warehouse equipped with Mecalux’s Easy WMS to facilitate the expansion of its e-commerce business. The software tracks 300,000 SKUs in real time and sends instructions to operators to prepare and ship 3,000 orders a day.
Zacaris: leader in online shoe sales
Zacaris is an online footwear store that sells a wide range of shoes from brands such as Converse, Skechers, Geox, Clarks, Tommy Hilfiger, and Camper, among many others. The company’s priority is to meet its users’ needs with competitive prices and fast, error-free delivery. The e-commerce business is constantly expanding its catalog with new brands, models, and styles of fashionable footwear.
- Founded in: 2010
- No. of brands: 200+
- International presence: Germany, Spain, France, Italy, Portugal and the UK
CHALLENGES
|
SOLUTION
|
BENEFITS
|
---|
Online footwear store Zacaris has experienced considerable growth in the last few years. The Badias brothers, who already owned three shoe stores at the time, founded Zacaris in 2010 with the aim of taking advantage of the possibilities of digital commerce and reaching a wider audience. For the e-commerce company, the internet was the catalyst for the internationalization of its business, which today sells products to thousands of customers in Germany, Spain, France, Italy, Portugal, and the UK.
Zacaris’s success is based on two pillars: an extensive catalog of products including the latest footwear trends and an efficient supply chain that offers next-day delivery for orders purchased before 4 p.m. In addition, Zacaris has a flexible returns policy, offering users a period of 12 months from the date of purchase to make an exchange or return.
The Zacaris supply chain stands out for being highly demanding, which is a hallmark of e-commerce logistics. To cope with the expansion of the business, the company is following a strategy of optimizing and renewing processes to speed up order picking and shipping. Under this premise, the e-tailer has centralized its logistics operations in a new facility equipped with Mecalux’s Easy WMS warehouse management software to keep a thorough control of 300,000 SKUs in real time.
Digitalization of the warehouse
In Lleida (Spain), Zacaris had a central logistics facility where it managed its goods and distributed orders received from its online customers. All operations were performed manually, from receiving to inventory control. “To perform the goods receipt process, we would consult the ERP system for the items that were scheduled to arrive in the warehouse and print out the labels. Afterwards, we had to locate the products among the pallets received and place the corresponding label on them,” says Oscar Herranz, CTO of Zacaris.
Once the items were recorded, the operators placed them on the racks, organized by brand, code, and size. “With such a large number of products in stock, arranging the goods in order was a very laborious task. If there was no space to store a product, we had to make room by moving hundreds of boxes,” Herranz adds.
It was clear to Zacaris that it needed to improve its warehouse operations to successfully implement its e-commerce strategy: “We wanted to stop organizing goods manually, streamline the receiving process, and optimize picking to minimize any chance of mistakes,” says Herranz. The e-commerce company was looking for a digital solution that would speed up its logistics processes and guarantee the highest quality.
After comparing several options, Zacaris chose Easy WMS, the warehouse management software from Mecalux. One of the special features of this program is that it can adapt its functionalities to the needs of each facility. The system is designed to help the e-tailer cope with changes in the business, such as a rise in the number of orders or the management of a growing number of SKUs.
Logistics centralization in a new warehouse
As online sales increased, the Zacaris facility was no longer big enough and had started to become overwhelmed by so much logistics activity. The company was finding it more and more difficult to accommodate the products, so it decided to move to a new, larger logistics center. “We also wanted the warehouse to be equipped with Easy WMS to be able to track the 300,000 SKUs in real time,” says Herranz.
Zacaris’s priority was to continue to serve customers without interruption over the course of the site relocation. During the time that the process lasted, Easy WMS was operational at both sites simultaneously. “Change is always complex. Coordinating operations at both logistics centers was a major challenge,” says Herranz.
In addition to providing uninterrupted service during the relocation, there was another constraint: all receipts of products had to take place at the new logistics facility. The old center no longer received goods for storage, but only dispatched merchandise that was in stock.
“Easy WMS has always been by our side, helping us to prepare all our orders for customers without any delays. Our greatest desire is to maintain our commitment to our users and to ensure 24-hour delivery. The warehouse move has shown us that Easy WMS is scalable software — capable of adapting to changes in our business — and that it will always drive our supply chain forward,” says Herranz.
Digital e-commerce warehouse
As in the previous Zacaris facility, “Easy WMS controls, manages, and optimizes all operations: from incoming goods to outgoing goods,” says Herranz. To do this, the system distributes the work among the operators and sends personalized instructions to each of them.
In the warehouse, workers use RF scanners to communicate instantly with the software. “When we installed Easy WMS, we needed some time to adapt to the software instructions, but now we’ve mastered the system. No operator would want to work without this technology,” says Herranz. The WMS generates routes for operators to travel the shortest possible distances for both storage and order picking.
Every day, the e-commerce warehouse receives pallets from suppliers with a multitude of different SKUs and products. Operators simply scan the barcode on each item and enter it into the system so that Easy WMS can assign it a location. Working with tags and RF scanners has been a breakthrough for Zacaris’s logistics operations. Each item is identified with its own barcode, making it easier to locate and track the 300,000 SKUs in real time.
To assign a location to the goods, Easy WMS uses advanced algorithms that take into account variables such as the SKU, the brand, and the level of demand for each box of shoes. Zacaris uses a chaotic slotting strategy, meaning each SKU has a free and random location.
Despite this paradoxical name, the warehouse follows a very strict order: the software knows at all times what products are in stock and where they are located. “With this chaotic organization of the goods, our facility is much more efficient than it was before,” says the CTO.
One of the key and most demanding operations in the Zacaris e-commerce warehouse is picking. Every day, 3,000 orders are picked and distributed to customers in less than 24 hours. A special feature of online stores is the preparation of a multitude of orders, each consisting of only a few items. In the case of Zacaris, 80% of the orders usually include only one order line (for example, a single model of shoes). In order to create so many single-unit orders, a grouping strategy is used in the facility: operators pick the items belonging to several orders on the same run.
Then, in the consolidation area, the products are packed, labeled, and grouped by transportation route. The Zacaris e-commerce warehouse distributes 4,000 parcels a day to customers. To manage such a large number of shipments, the company has reorganized the shipping area with Mecalux software to avoid mistakes and ensure deliveries within 24 hours.
Logistics in transformation and expansion
Zacaris’s e-commerce logistics operations are continuously evolving and growing. Proof of this is the move to a new, larger center to cope with the real-time management of 300,000 SKUs and the preparation of 3,000 orders per day.
The company has implemented Mecalux’s Easy WMS software in its new warehouse to provide better service to customers. With digitalization, Zacaris has now simplified its operations to guarantee 24-hour order deliveries. The digital transformation of the facility has brought numerous advantages to Zacaris, including tighter stock control, better use of storage space, and great agility and security in operations as complex as picking.
Easy WMS has helped Zacaris to boost its logistics performance. With very promising future prospects, the e-commerce warehouse will continue to operate at full capacity to ship an ever-increasing number of orders.
Easy WMS has completely transformed our logistics operations. The warehouse is much more efficient than before because we have tighter control of all processes and stock. The organization of the goods has led to greater agility in storage and order picking tasks.
Gallery
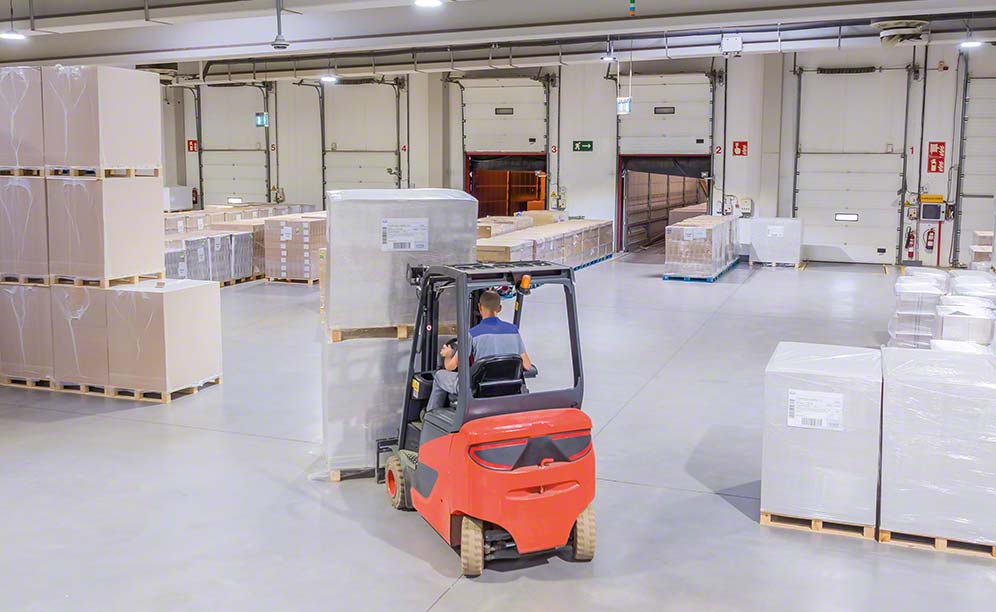
Zacaris’s operators prepare 3,000 online orders a day
Ask an expert