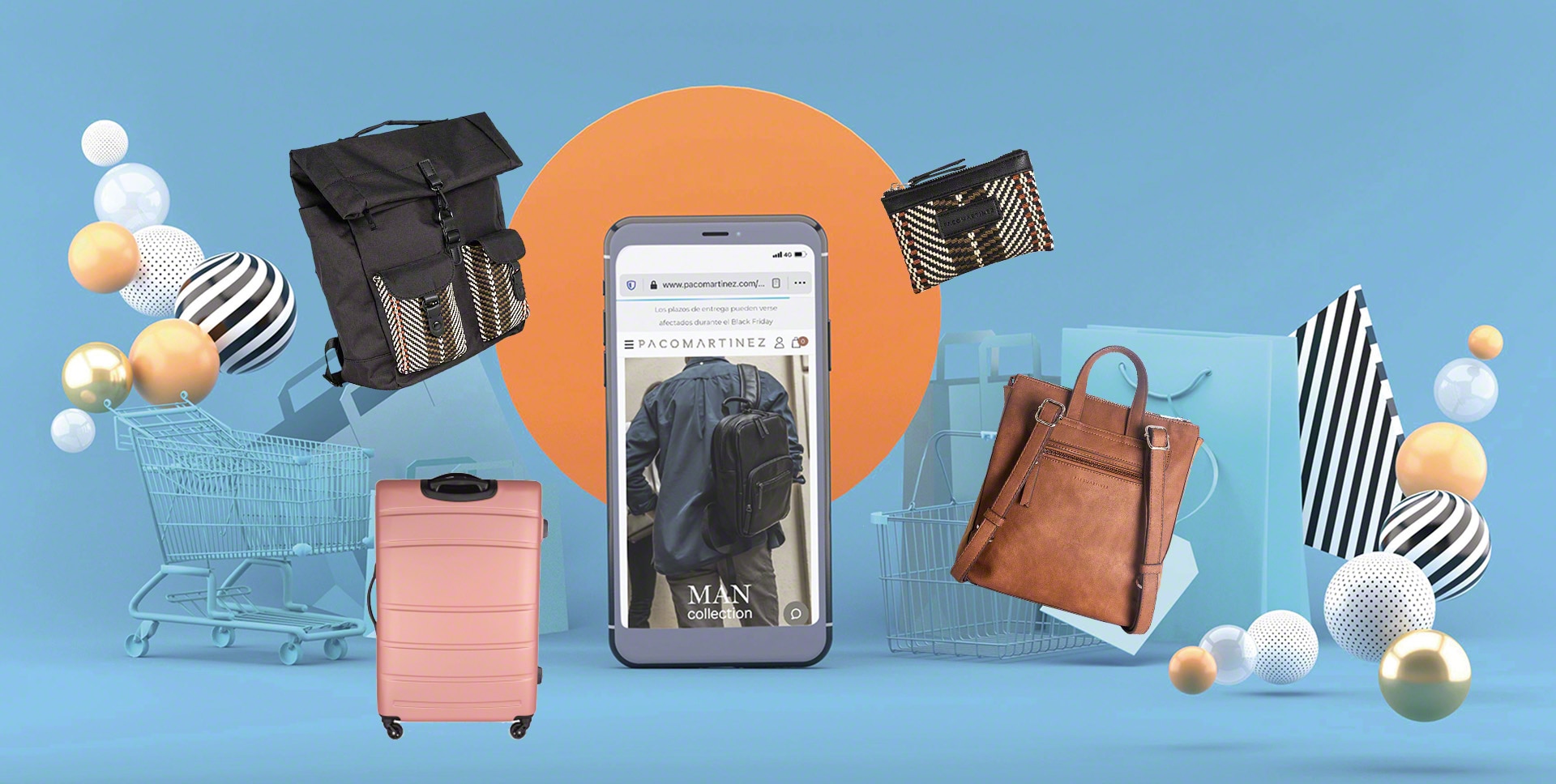
Pumped-up logistics for a leading retailer
Pacomartinez has streamlined picking for its shops throughout Spain
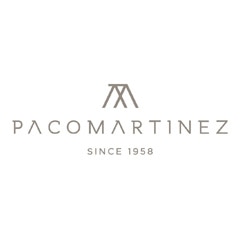
Pacomartinez, a distributor of luggage and travel accessories, has centralized all its logistics systems with the opening of a new warehouse in Valencia, Spain. Interlake Mecalux has provided it with a complete solution that includes pallet racking and Easy WMS, the warehouse management system. The digitization of operations has helped Pacomartinez to improve its customer service and bolster its future growth prospects. As a result, all its processes are now faster and safer.
A major retailer specializing in travel items
Pacomartinez is a Spanish distributor of handbags, suitcases, backpacks and fashion accessories. Commitment, cooperation, continuous improvement, innovation, transparency and loyalty are the distinguishing features of this firm, which boasts more than 100 physical shops all over Spain and Portugal.
Since it opened in 1958, it has grown steadily to become one of the leading accessories chains in the Spanish market. Every day, many customers visit Pacomartinez establishments in search of goods from the brand’s wide, unique and distinctive product range.
Pacomartinez’s expansion has been made possible thanks to the company’s commitment to innovation and continuous improvement. Along these lines, it has recently embarked on an unprecedented logistics transformation process aimed at providing more agile and efficient service.
This change consisted of consolidating all its logistics operations in a single 43,000 ft2 installation in Albuixech (Valencia, Spain). Regarding the objective of this project, David Valero, Partner and Continuous Improvement Technician at Pacomartinez, says, “Before, we had four warehouses in the Valencian town of Pedreguer: two main facilities and two auxiliary installations. This wasn’t effective for our business, as we were forced to transfer goods numerous times between the various buildings to prepare and dispatch the orders. This required more staff, took too much time and entailed a high risk of errors.”
The move to a new installation (where the company’s head offices have also been relocated) has been a huge improvement for Pacomartinez. In the words of David Valero, “Now, all our goods are under one roof, so we’ve optimized the surface area dedicated to storage as well as the work of the operators. I should note that the warehouse is located in a major communication hub, which facilitates distribution of the products to all our shops.”
To equip this facility, the company decided to contact Interlake Mecalux once again “because of our previous experience working with the firm on our old installations,” points out David Valero. Interlake Mecalux installed not only racking in its other facilities, but also the Easy WMS warehouse management system to monitor the goods more accurately. “In comparing various proposals, Mecalux’s was the most solid, offering more guarantees and faster delivery times,” he adds.
The installation is made up of pallet racking and drive-in racks with a total storage capacity of 4,968 pallets. “We chose these two storage systems because we’d used them at our other facilities. So the employees already knew how to work with them, and we were familiar with their particular features and advantages,” indicates David Valero.
Competitiveness in the supply chain
Initially — long before moving to the new facility in Albuixech — Pacomartinez used its own ICG Software ERP in conjunction with Easy WMS from Interlake Mecalux to organize operations in all its installations. However, as the business grew and the number of orders rose, the company realized it needed to overhaul its logistics management.
After analyzing various WMSs on the market in detail, it opted to install the new version of Easy WMS in its current warehouse. This is because this system is capable of managing and optimizing all processes, including goods receipt, product slotting, order prep and loading of the distribution truck. “We were sure we wanted to use Easy WMS because it’s a very intuitive WMS. You don’t need to install any programs on your computer; to consult the status of our installation, all we have to do is log in,” affirms the Partner and Continuous Improvement Technician.
Easy WMS carries out strict monitoring of Pacomartinez’s 2,000 SKUs, from the time they arrive at the warehouse up to their dispatch, providing detailed information about everything occurring in the installation. First, it assigns a location to each product according to its size and demand level. To do so, it incorporates parameterizable rules and algorithms that enable it to make decisions that contribute towards increasing throughput. Secondly, it oversees the operators at all times and tells them what to do, minimizing any possibility of error.
To fully leverage the potential of the warehouse, Easy WMS is integrated with Pacomartinez’s ICG ERP. This is essential for always having the necessary goods on hand and avoiding stockouts.
“By commissioning this installation, we set out to meet a new requirement: we wanted Easy WMS to be integrated with the various packaging agencies which with we work. This would streamline the exchange of information between the warehouse and the carriers,” explains David Valero. Interlake Mecalux’s technical team knew right away that the Multi Carrier Shipping Software module would achieve this goal.
This extension of Easy WMS informs the transportation agencies of the number of packages and their weight and volume before the carriers go to pick them up at the warehouse. The agencies, meanwhile, send data to the WMS to generate the labels and tracking numbers.
Effective organization for efficient operations
The warehouse is divided into five zones (one for online orders and four for the shops). This facilitates the work of the operators in carrying out storage and picking tasks with products from different categories: handbags and men’s accessories, leather goods and accessories, luggage sets and carry-on suitcases.
The goods in each of these areas are organized based on several criteria. According to David Valero, “In the space for luggage sets and carry-on suitcases, since these are products we sell a lot, we prioritize turnover. In the other areas, we arrange the merchandise by collection.”
Operators use radiofrequency terminals to individually identify items as they arrive at the warehouse. All products are labeled with a barcode that they merely need to read with the terminals in order for the WMS to intelligently decide where to deposit them. The WMS makes this decision according to the type of item in question, its collection and its turnover.
Order preparation method
Every day, between 100 and 150 orders (up to 200 on peak days) are prepared, dispatched and sent to bricks-and-mortar shops (100 throughout Spain and Portugal). This figure is expected to exceed 300 as the company’s growth prospects come to fruition. Each order is usually made up of a very variable number of lines, as these fluctuate based on the type of product (50 lines minimum, 1,000 lines maximum).
Orders are prepared by area. Hence, operators work only in the zone assigned to them, preparing up to four orders at once. David Valero describes the operation: “The employees move around one area of the warehouse using a pallet truck with four boxes; each box corresponds to an order or a shop. The WMS tells them exactly which location to go, which products to remove and how many of them to pick.” This control has made the process more agile and minimized potential errors.
Each working area has its own particular characteristics when it comes to preparing orders. In the accessories zone, for example, smaller boxes are used because, evidently, these items are smaller. “Plus, they weigh no more than 26 lb to facilitate the work of the shop employees that eventually have to handle these boxes,” adds Valero.
Multi Carrier Shipping Software: dispatches under control
Once the orders are finished, the operators bring them directly to the dispatch area. At this point, Multi Carrier Shipping Software — the Easy WMS module specifically designed to control dispatches — comes into play.
This WMS extension knows in advance which transportation agency will distribute each package and prints a personalized label for each one. This label includes the destination and the tracking number, which customers and shops use to know the exact location of their orders.
Likewise, Multi Carrier Shipping Software generates all the documentation the carriers need (commercial invoice, transportation insurance, number of boxes to collect, destination, etc.). “Guaranteeing automated information flows between the warehouse and the transportation agencies was a huge step forward for us. With Multi Carrier Shipping Software, we can specify the times for the carriers to come and pick up the orders. Moreover, before they arrive, they already have all the necessary information to be able to make the delivery successfully,” enthuses David Valero.
Orders are prepared a day in advance. In the afternoon, the orders are grouped in the dispatch area, where operators verify that no mistakes have been made. Next, Multi Carrier Shipping Software creates a list of orders and notifies the transportation agency. The following day, the carrier simply has to collect the items and start off on the delivery route.
By incorporating a single module, the Pacomartinez warehouse has been integrated with the five transportation agencies that deliver the orders: SEUR, DHL, Dascher, DB Schenker and the firm’s own delivery truck.
Logistics out of a suitcase
Pacomartinez has centralized all its logistics processes in a new 43,000 ft2 installation in Albuixech, (Valencia). From there, it supplies its 100 shops in Spain and Portugal.
The retailer has implemented Interlake Mecalux’s Easy WMS warehouse management system, charged with precisely monitoring all processes taking place in the facility, from goods receipt through to dispatches.
Aided by the Multi Carrier Shipping Software module in particular, the firm has ramped up its shipments while lowering costs and gaining full control over stock and dispatches.
We’re really pleased with Easy WMS from Mecalux because it’s an extremely intuitive warehouse management system. And thanks to the Multi Carrier Shipping Software module, we now communicate automatically with the various transportation agencies that deliver our orders. This allows us to specify the times the carriers will come to pick up the orders. Moreover, before they arrive, they already have all the information they need to make the delivery successfully. As a result, our dispatches are now faster, safer and more accurate.
Advantages for Pacomartinez
- Management all under one roof: Pacomartinez has concentrated all its logistics operations in a single installation. From there, the firm supplies its shops and franchises in Spain and Portugal.
- Organized and effective picking: Easy WMS sends clear, detailed instructions to the operators so that they can prepare 100-150 orders a day more quickly.
- Automatic communication with carriers: Multi Carrier Shipping Software oversees dispatches and communicates automatically with the transportation agencies.
Gallery
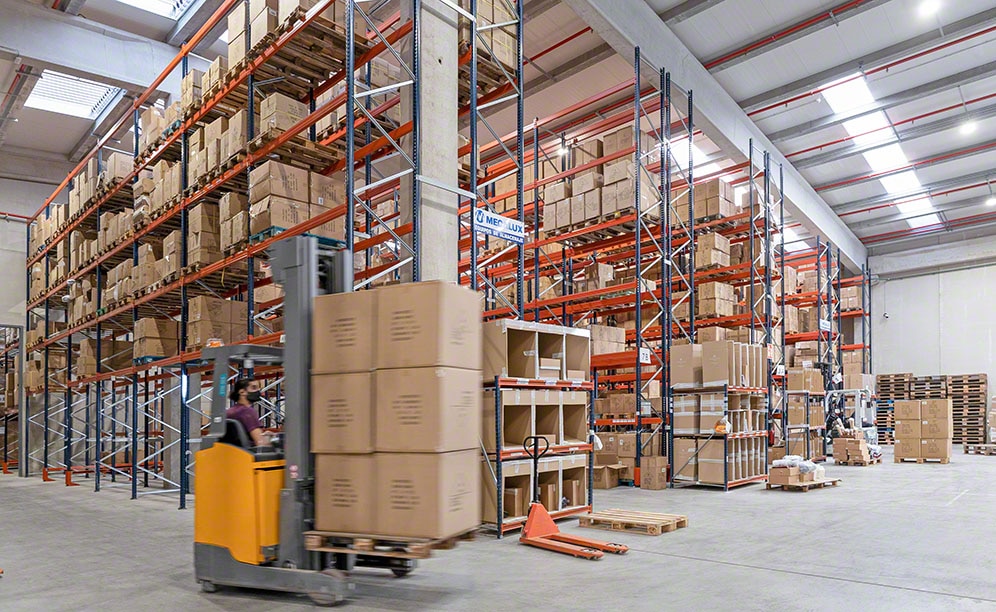
The Pacomartinez warehouse in Albuixech (Valencia, Spain)
Ask an expert